Vacuum Inert Gas Atomisation
Table of Contents
Overview
In the world of advanced manufacturing, the quest for perfection in materials has led to the development of numerous sophisticated techniques. One such revolutionary method is Vacuum Inert Gas Atomisation (VIGA). This process plays a critical role in producing high-quality metal powders, essential for various applications such as additive manufacturing, powder metallurgy, and specialized coatings. In this article, we delve into the intricacies of VIGA, exploring its processes, benefits, limitations, and applications.
Overview of Vacuum Inert Gas Atomisation
Vacuum Inert Gas Atomisation (VIGA) is a state-of-the-art method used to produce fine, spherical metal powders. This process involves melting a metal under a vacuum and then introducing an inert gas to atomize the molten metal into tiny droplets, which solidify into fine powders. VIGA is renowned for its ability to produce high-purity powders with controlled particle sizes, making it indispensable in high-precision industries.
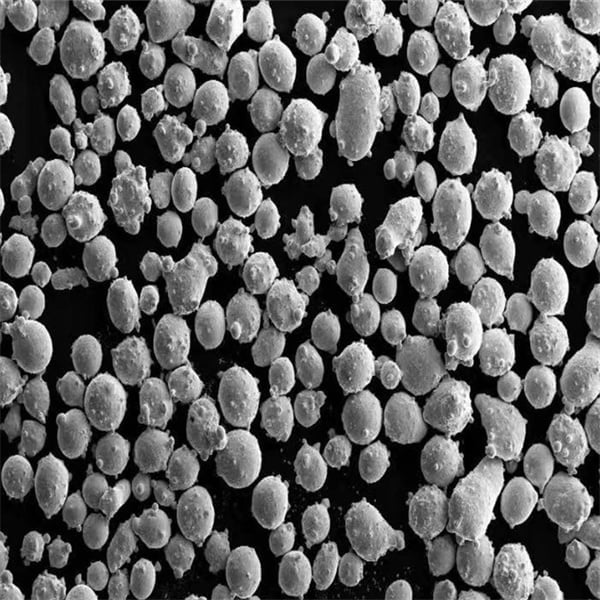
How Vacuum Inert Gas Atomisation Works
VIGA operates under a controlled environment to ensure the production of superior quality metal powders. Here’s a step-by-step breakdown of the process:
- Melting: Metal or alloy is melted in a vacuum induction furnace.
- Atomisation: The molten metal is poured through a nozzle into a chamber where it is atomized by a high-pressure stream of inert gas (such as argon or nitrogen).
- Solidification: The tiny metal droplets rapidly cool and solidify into fine, spherical powders.
- Collection: The powders are collected in a chamber, separated from the inert gas, and sieved to achieve the desired particle size distribution.
Key Metal Powder Models Produced by VIGA
The VIGA process can produce a wide range of metal powders, each with unique properties tailored for specific applications. Here are some notable models:
Metal Powder Model | Composition | Properties | Applications |
---|---|---|---|
316L Stainless Steel | Fe-16.5Cr-10Ni-2Mo | High corrosion resistance, good weldability | Medical implants, aerospace components |
Ti-6Al-4V | Ti-6Al-4V | High strength-to-weight ratio, biocompatible | Aerospace parts, biomedical devices |
AlSi10Mg | Al-10Si-0.4Mg | Lightweight, good thermal conductivity | Automotive parts, heat exchangers |
Inconel 718 | Ni-52Cr-19Fe-5Nb-3Mo-1Ti | High temperature resistance, corrosion resistance | Turbine blades, nuclear reactors |
Copper | Pure Cu | Excellent electrical and thermal conductivity | Electrical components, heat sinks |
Maraging Steel (18Ni300) | Fe-18Ni-9Co-5Mo-1.5Ti | High strength, good toughness | Tooling, high-performance parts |
Cobalt-Chromium (CoCrMo) | Co-28Cr-6Mo | High wear resistance, biocompatible | Dental implants, orthopedic devices |
Nickel-Based Superalloys (Hastelloy X) | Ni-22Cr-18Fe-9Mo | Exceptional oxidation and corrosion resistance | Aerospace, chemical processing |
Aluminum Alloy 7075 | Al-5.6Zn-2.5Mg-1.6Cu | High strength, good fatigue resistance | Aerospace frames, sporting goods |
Stellite 21 | Co-28Cr-4Mo | Wear resistance, high temperature stability | Cutting tools, engine components |
Applications of Vacuum Inert Gas Atomisation
The versatility of VIGA-produced powders opens up numerous applications across various industries. Here are some of the most significant uses:
Industry | Applications |
---|---|
Aerospace | Turbine blades, structural components, fasteners |
Medical | Orthopedic implants, dental prosthetics |
Automotive | Engine parts, lightweight structural components |
Electronics | Conductive inks, soldering materials |
Energy | Nuclear reactors, fuel cells |
Tooling | Cutting tools, molds, dies |
Additive Manufacturing | 3D printing, prototyping |
Coatings | Thermal barrier coatings, wear-resistant coatings |
Advantages of Vacuum Inert Gas Atomisation
VIGA offers several advantages that make it a preferred choice for metal powder production:
- High Purity: The vacuum environment minimizes contamination, ensuring high-purity powders.
- Controlled Particle Size: Precise control over atomization parameters results in uniform particle sizes.
- Spherical Particles: The process produces spherical powders, enhancing flowability and packing density.
- Versatility: Capable of processing a wide range of metals and alloys.
- Reduced Oxidation: The inert gas environment reduces oxidation, preserving the powder’s properties.
Disadvantages of Vacuum Inert Gas Atomisation
Despite its many benefits, VIGA has some limitations:
- High Cost: The equipment and operation costs are relatively high compared to other atomization methods.
- Complexity: The process requires sophisticated control systems and skilled operators.
- Limited Production Scale: Typically, VIGA is more suited for small to medium-scale production.
Comparison of VIGA with Other Atomisation Methods
When choosing an atomization method, it’s crucial to compare VIGA with other techniques like Water Atomisation and Gas Atomisation. Here’s how they stack up:
Method | Particle Shape | Purity | Cost | Production Scale | Applications |
---|---|---|---|---|---|
VIGA | Spherical | High | High | Medium | High-precision industries, aerospace |
Water Atomisation | Irregular | Moderate | Low | High | Powder metallurgy, steel powders |
Gas Atomisation | Spherical | High | Moderate | Medium | Additive manufacturing, special alloys |
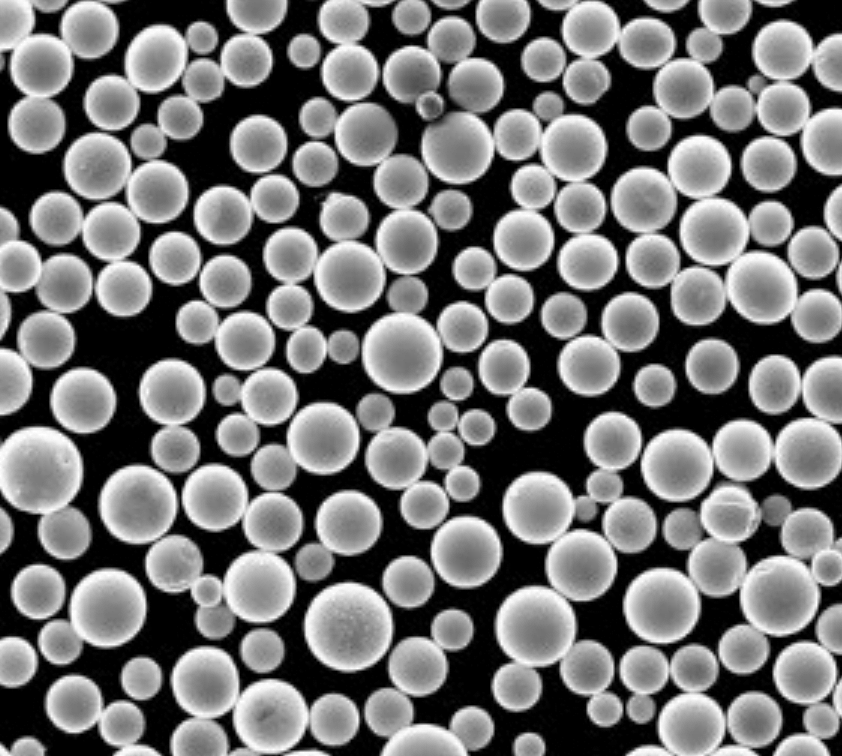
Specifications, Sizes, and Standards
To ensure consistency and quality, metal powders produced via VIGA adhere to specific standards and specifications:
Metal Powder | Particle Size Range (µm) | Standards |
---|---|---|
316L Stainless Steel | 15-45, 45-150 | ASTM A276, ISO 5832-1 |
Ti-6Al-4V | 15-53, 53-150 | ASTM F2924, ISO 5832-3 |
AlSi10Mg | 20-63, 63-125 | ASTM B928, ISO 209-1 |
Inconel 718 | 15-45, 45-150 | ASTM B637, ISO 6208 |
Copper | 10-75, 75-150 | ASTM B216, ISO 3497 |
Maraging Steel (18Ni300) | 15-45, 45-150 | ASTM A646, ISO 4955 |
Cobalt-Chromium (CoCrMo) | 20-53, 53-150 | ASTM F1537, ISO 5832-4 |
Nickel-Based Superalloys (Hastelloy X) | 15-53, 53-150 | ASTM B435, ISO 6208 |
Aluminum Alloy 7075 | 20-63, 63-125 | ASTM B209, ISO 6362-2 |
Stellite 21 | 20-63, 63-150 | ASTM F75, ISO 5832-4 |
Suppliers and Pricing Details
Finding reliable suppliers and understanding pricing details is essential for procurement. Here’s a snapshot of some prominent suppliers and their pricing:
Supplier | Metal Powders Offered | Price Range (per kg) | Location |
---|---|---|---|
Sandvik Osprey | Stainless Steel, Titanium | $150 – $300 | Sweden |
Carpenter Technology | Nickel Alloys, Cobalt Alloys | $200 – $500 | USA |
Höganäs AB | Steel Powders, Aluminum | $50 – $200 | Sweden |
LPW Technology | Various Alloys, Custom Powders | $100 – $400 | UK |
AP&C (GE Additive) | Titanium, Aluminum | $200 – $600 | Canada |
Pros and Cons Comparison
Understanding the advantages and limitations of VIGA is crucial for making informed decisions:
Pros | Cons |
---|---|
High purity and controlled composition | High cost of equipment and operation |
Spherical particles with good flowability | Requires skilled operators |
Versatility in metal and alloy types | Limited to small to medium-scale production |
Reduced oxidation due to inert gas | Complex process with stringent control |
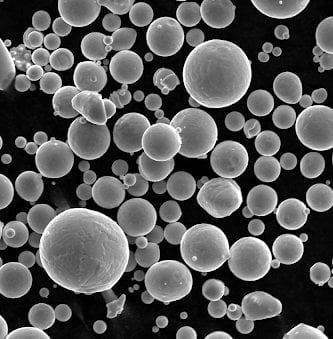
FAQ
Question | Answer |
---|---|
What is VIGA used for? | VIGA is used to produce high-quality metal powders for applications in aerospace, medical, and additive manufacturing. |
How does VIGA differ from gas atomization? | VIGA uses a vacuum and inert gas to minimize contamination and oxidation, resulting in higher purity powders. |
What metals can be processed using VIGA? | A wide range of metals and alloys including stainless steel, titanium, aluminum, and nickel-based superalloys. |
What are the particle size ranges achievable with VIGA? | Typically, VIGA can produce powders with particle sizes ranging from 10 µm to 150 µm. |
Is VIGA cost-effective? | While VIGA offers high quality and precision, it is generally more expensive than other atomization methods. |
In conclusion, Vacuum Inert Gas Atomisation stands out as a premier technique for producing high-quality metal powders, essential for various high-precision applications. Its ability to produce spherical, high-purity powders with controlled particle sizes makes it indispensable in fields ranging from aerospace to medical implants. While it comes with higher costs and complexity, the benefits often outweigh the drawbacks for applications demanding top-tier material performance. As industries continue to innovate, the role of advanced techniques like VIGA in shaping the future of manufacturing cannot be overstated.
Share On
MET3DP Technology Co., LTD is a leading provider of additive manufacturing solutions headquartered in Qingdao, China. Our company specializes in 3D printing equipment and high-performance metal powders for industrial applications.
Inquiry to get best price and customized Solution for your business!
Related Articles
About Met3DP
Recent Update
Our Product
CONTACT US
Any questions? Send us message now! We’ll serve your request with a whole team after receiving your message.
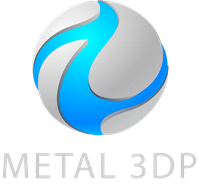
Metal Powders for 3D Printing and Additive Manufacturing