Classify 3D printed metal powders by material
Table of Contents
The world of 3D printing has exploded in recent years, revolutionizing how we design and manufacture everything from toys to prosthetics. But have you ever stopped to wonder what the magic ingredient is that allows us to build complex metal objects layer by layer? The answer lies in the heart of the process: 3D printed metal powders.
These fine, metallic grains are the unsung heroes of metal additive manufacturing. Imagine a giant bag filled with millions of tiny, shimmering particles, each one holding the potential to be transformed into a intricate gear, a lightweight aerospace component, or even a life-saving medical implant. But with so many different types of metal powders available, choosing the right one for your project can feel like navigating a metallic labyrinth.
This comprehensive guide will equip you with the knowledge to confidently select the perfect 3D printed metal powder for your needs. We’ll delve into the various classifications of these powders, explore their properties, and unveil the specific applications where each one shines. Buckle up and get ready to explore the fascinating world of metal alchemy in a digital age!
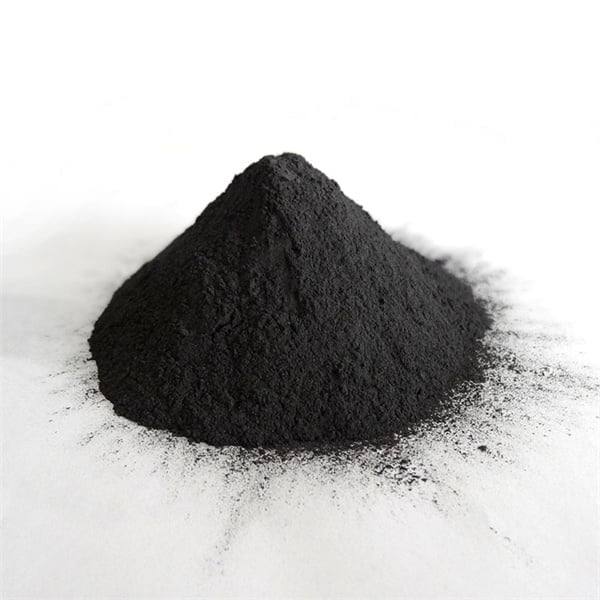
Common 3D Printed Metal Powder Types
Just like a baker wouldn’t use the same flour for a delicate cake and a hearty loaf of bread, the choice of metal powder in 3D printing hinges on the desired outcome. Here’s a breakdown of some of the most commonly used metal powder categories, along with their key characteristics:
Material Category | Composition | Properties | Characteristics |
---|---|---|---|
Stainless Steel | Primarily iron, chromium, and nickel, with possible additions like molybdenum and nitrogen | Excellent corrosion resistance, good strength and ductility | Widely used due to versatility; various grades offer tailored properties |
Tool Steel | Primarily iron, with high carbon content and alloying elements like chromium, vanadium, tungsten | High wear resistance, good hardness | Ideal for creating molds, dies, and cutting tools |
Titanium Alloys | Primarily titanium, often with aluminum and vanadium | High strength-to-weight ratio, excellent biocompatibility | Popular in aerospace, medical implants, and high-performance applications |
Aluminum Alloys | Primarily aluminum, with elements like copper, magnesium, and silicon | Lightweight, good corrosion resistance, varying strength depending on alloy | Used in applications requiring a balance of weight and strength, like automotive and aerospace parts |
Nickel-Based Alloys | Primarily nickel, often with chromium, cobalt, and molybdenum | High-temperature resistance, excellent corrosion resistance | Used in demanding environments like jet engines and chemical processing equipment |
Cobalt-Chromium Alloys | Primarily cobalt and chromium, with possible additions like molybdenum and tungsten | High wear resistance, good biocompatibility | Primarily for medical implants and wear-resistant components |
This table provides a starting point, but within each category lies a rich tapestry of specific metal powder models. Let’s delve deeper and explore some popular examples:
1. 17-4 PH Stainless Steel: This versatile powder offers a good balance of strength, corrosion resistance, and weldability. It’s a popular choice for applications ranging from aerospace components to medical devices.
2. 316L Stainless Steel: Renowned for its exceptional corrosion resistance, particularly in saltwater environments, 316L powder is ideal for marine components, chemical processing equipment, and even architectural elements.
3. H13 Tool Steel: This high-alloy steel powder boasts impressive wear resistance and hot hardness, making it the go-to choice for creating molds and dies used in metal forming and plastic injection molding.
4. A2 Tool Steel: Offering a balance between wear resistance and toughness, A2 tool steel powder is a cost-effective option for less demanding tooling applications like punches and cold forming dies.
5. Ti64 (Grade 23) This titanium alloy powder is a workhorse material in the aerospace industry. Its high strength-to-weight ratio and excellent fatigue resistance make it perfect for lightweight, high-performance components.
6. Aluminum 6061: This widely used aluminum alloy powder offers a good balance of strength, weight, and machinability. It’s a popular choice for prototyping, automotive parts, and general-purpose applications.
7. Inconel 625: Renowned for its exceptional resistance to high temperatures and harsh environments, Inconel 625 powder is a mainstay in jet engine components, chemical processing equipment, and applications requiring superior heat resistance.
8. MP1 CoCr: This biocompatible cobalt-chromium alloy powder is a leading choice for medical implants like hip replacements and knee joints. Its excellent wear resistance and biocompatibility ensure long-lasting performance within the human body.
Applications Tailored to Powder Properties
Choosing the right 3D printed metal powder isn’t just about the material itself; it’s about aligning the powder’s properties with the specific needs of your project. Here’s a breakdown of some common applications and how different powder types cater to them:
Application | Ideal Metal Powder | Why it Works |
---|---|---|
Aerospace Components | Titanium alloys (Ti64), Aluminum alloys (6061, 7075) | High strength-to-weight ratio for lightweight, high-performance parts. Excellent fatigue resistance for components experiencing repeated stress. |
Medical Implants | Cobalt-Chromium alloys (MP1 CoCr, CM247), Titanium alloys (Ti64) | Biocompatible materials minimize rejection risks within the body. High strength and wear resistance ensure long implant lifespans. |
Molds and Dies | Tool Steels (H13, A2) | Excellent wear resistance allows for extended tool life and high-quality part production. Hot hardness ensures tools maintain their shape under high temperatures. |
Chemical Processing Equipment | Stainless Steels (316L), Nickel-Based Alloys (Inconel 625) | Superior corrosion resistance protects against harsh chemicals, ensuring equipment longevity and safe operation. |
Marine Components | Stainless Steels (316L) | Exceptional resistance to saltwater corrosion keeps marine equipment functioning flawlessly in harsh environments. |
Prototyping | Stainless Steels (17-4 PH), Aluminum Alloys (6061) | Versatile materials allow for creating functional prototypes with good strength and machinability. Cost-effective option for initial design iterations. |
High-Performance Parts | Titanium Alloys (Ti64), Nickel-Based Alloys (Inconel 625) | Excellent strength-to-weight ratio and high-temperature resistance make them ideal for demanding applications like racing components and jet engine parts. |
This is just a glimpse into the vast array of applications that 3D printed metal powders enable. As technology advances, we can expect even more specialized powders to emerge, pushing the boundaries of what’s possible in metal additive manufacturing.
Powder Specifications and Standards
Just like snowflakes, no two metal powder particles are exactly alike. To ensure consistent performance and successful printing, manufacturers adhere to specific powder specifications and standards. Let’s explore some key parameters that define a metal powder:
- Particle Size and Distribution: The size and uniformity of the powder particles significantly impact the printability, surface finish, and mechanical properties of the final product.
- Sphericity: Ideally, metal powder particles should be as close to perfect spheres as possible. This ensures smooth flow during the printing process and minimizes voids within the printed part.
- Flowability: The powder’s ability to flow freely is crucial for even deposition during printing. Poor flowability can lead to inconsistencies and printing defects.
- Chemical Composition: Strict adherence to the desired chemical composition is essential for achieving the anticipated material properties in the final part.
- Oxygen Content: Excessive oxygen content can lead to porosity and brittleness in the printed metal.
Standards and Certifications: Several industry standards and certifications govern the production and quality of metal powders for 3D printing. These standards ensure consistency, safety, and printability of the powders. Some prominent examples include:
- ASTM International (ASTM): A global standards organization that publishes various specifications for metal powders used in additive manufacturing.
- American Society of Mechanical Engineers (ASME): Develops and maintains standards for metal powder materials used in pressure vessels and other critical applications.
- EOS GmbH: A leading manufacturer of 3D printing systems also offers material specifications for powders compatible with their machines.
- SLM Solutions: Similar to EOS, SLM Solutions provides material data sheets outlining the specifications of their metal powders for use in their 3D printing systems.
Understanding these specifications and adhering to relevant standards is crucial for achieving optimal results in your 3D printing projects.
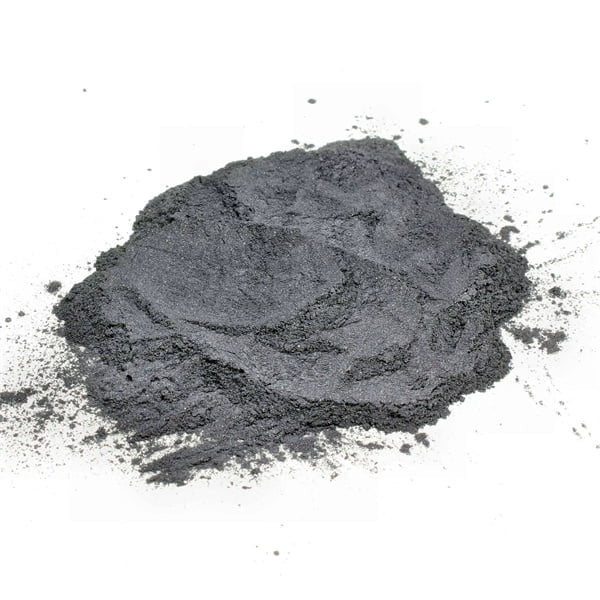
Weighing the Pros and Cons of Different Powders
The choice between different metal powders involves a careful evaluation of their advantages and limitations. Here’s a breakdown of some key considerations:
Powder Type | Advantages | Disadvantages |
---|---|---|
Stainless Steel | Versatile, good strength and corrosion resistance, readily available | May not be the strongest or lightest option for all applications. |
Tool Steel | Excellent wear resistance, ideal for tooling applications | Can be more challenging to print compared to some other powders. |
Titanium Alloys | High strength-to-weight ratio, excellent biocompatibility | Higher cost compared to some other options. |
Aluminum Alloys | Lightweight, good corrosion resistance, | May not be as strong as some other options at high temperatures. |
Nickel-Based Alloys | High-temperature resistance, excellent corrosion resistance | Expensive and can be difficult to print due to their high melting points. |
Cobalt-Chromium Alloys | High wear resistance, good biocompatibility | Relatively high cost. |
Additional Considerations:
- Printability: Different metal powders have varying printability characteristics. Some may require specialized printing equipment or parameters.
- Post-Processing: The level of post-processing required, such as heat treatment or support removal, can vary depending on the chosen powder.
- Environmental Impact: The production and use of certain metal powders may have environmental implications to consider.
By carefully weighing these pros and cons, you can make an informed decision about the most suitable metal powder for your specific project requirements.
Suppliers, Pricing, and Availability
Now that you’re armed with a wealth of knowledge about 3D printed metal powders, it’s time to explore where you can acquire them. Here’s a glimpse into the world of metal powder suppliers:
- Metal Powder Manufacturers: Leading manufacturers like Höganäs, Carpenter Additive, and AP Powder offer a wide range of metal powders specifically designed for 3D printing applications.
- 3D Printer Manufacturers: Many 3D printer manufacturers also sell metal powders compatible with their machines. This ensures optimal performance and compatibility.
- Metal Service Centers: These companies often stock various metal powders alongside other raw materials used in metalworking.
Pricing: The cost of metal powder can vary significantly depending on the material, particle size, and supplier. Generally, exotic materials like nickel-based alloys and titanium alloys command a higher price tag compared to common stainless steels. Here’s a ballpark range to provide perspective:
- Stainless Steel Powders: $10 – $50 per kilogram
- Tool Steel Powders: $20 – $70 per kilogram
- Titanium Alloy Powders: $50 – $200 per kilogram
- Nickel-Based Alloy Powders: $70 – $300 per kilogram
Availability: The availability of certain metal powders can vary depending on the material and its demand. Common powders like stainless steel are generally readily available, while more specialized powders may require longer lead times.
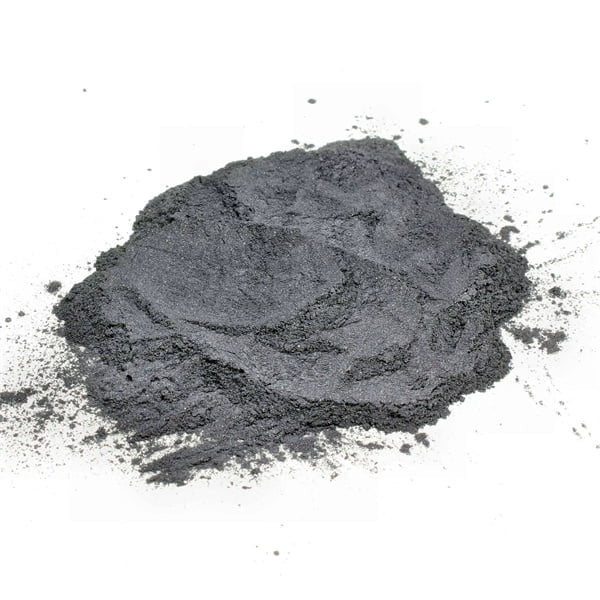
FAQ
Here are some of the most common questions people have about 3D printed metal powders, answered in a clear and concise format:
FAQ Table
Question | Answer |
---|---|
What are the benefits of using 3D printed metal powders? | 3D printed metal powders enable the creation of complex metal objects with high strength and design flexibility. They also offer reduced waste compared to traditional manufacturing methods. |
What factors should I consider when choosing a metal powder? | Consider the desired properties for your final part, such as strength, weight, corrosion resistance, and biocompatibility. Printability, post-processing requirements, and cost are also important factors. |
Where can I buy 3D printed metal powders? | Metal powder manufacturers, 3D printer manufacturers, and metal service centers are all potential suppliers. |
How much do metal powders cost? | The cost varies depending on the material, particle size, and supplier. Expect a range of $10 – $300 per kilogram for common powders. |
What safety precautions should I take when handling metal powders? | Metal powders can be flammable or explosive. Always follow the manufacturer’s safety data sheet (SDS) for handling and storage guidelines. |
By understanding the different types of 3D printed metal powders, their properties, applications, and the factors to consider when choosing one, you’re well on your way to unlocking the exciting world of metal additive manufacturing. With the right knowledge and resources, you can transform your designs into tangible metal objects, pushing the boundaries of innovation and creativity.
Share On
MET3DP Technology Co., LTD is a leading provider of additive manufacturing solutions headquartered in Qingdao, China. Our company specializes in 3D printing equipment and high-performance metal powders for industrial applications.
Inquiry to get best price and customized Solution for your business!
Related Articles
About Met3DP
Recent Update
Our Product
CONTACT US
Any questions? Send us message now! We’ll serve your request with a whole team after receiving your message.
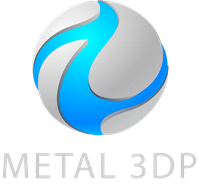
Metal Powders for 3D Printing and Additive Manufacturing