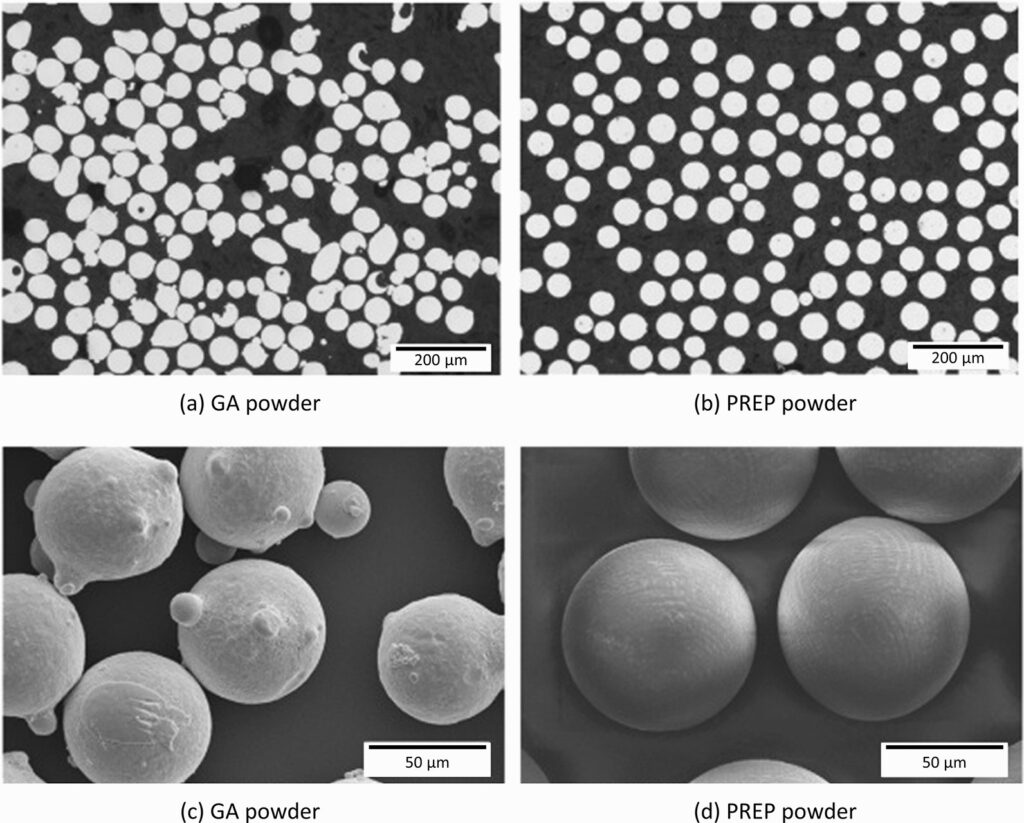
93Co7Ni Powder: The Best Choice for Extreme Heat and Corrosion Defense
Low MOQ
Provide low minimum order quantity to meet different needs.
OEM & ODM
Provide customized products and design services to meet unique customer needs.
Adequate Stock
Ensure fast order processing and provide reliable and efficient service.
Customer Satisfaction
Provide high quality products with customer satisfaction at the core.
share this article
Table of Contents
Are you looking for a material that can handle extreme environments, deliver superior performance, and offer reliable durability in various applications? 93Co7Ni powder might just be the answer. This cobalt-based alloy, enhanced with nickel, is a powerhouse in industries that require high wear resistance, thermal stability, and corrosion protection.
In this comprehensive guide, we’ll break down everything you need to know about 93Co7Ni powder—from its composition and properties to its applications, specifications, and pricing. Whether you’re in aerospace, automotive, or medical sectors, you’ll discover why this powder is highly valued in critical applications.
Overview: What Is 93Co7Ni Powder?
93Co7Ni powder is a specialized cobalt-nickel alloy powder consisting of 93% cobalt and 7% nickel. This specific combination creates a material that boasts high temperature resistance, wear resistance, and oxidation stability. It’s primarily used in thermal spraying, additive manufacturing, and powder metallurgy to produce coatings or parts that must endure extreme conditions.
This powder is frequently used in industries like aerospace, automotive, and medical implants, where reliability and performance are paramount. So, if your project demands a material that can withstand stress, heat, and corrosion, 93Co7Ni powder is a strong contender.
Chemical Composition and Properties of 93Co7Ni Powder
The strength and performance of 93Co7Ni powder are rooted in its precise chemical composition. Each element contributes to the powder’s specific properties, which make it ideal for high-performance applications.
Chemical Composition of 93Co7Ni Powder
Element | Percentage (%) | Role in the Alloy |
---|---|---|
Cobalt (Co) | 93% | Provides excellent heat resistance, wear resistance, and high strength even at elevated temperatures. |
Nickel (Ni) | 7% | Enhances toughness, corrosion resistance, and increases the alloy’s ability to withstand high thermal stress. |
Key Properties of 93Co7Ni Powder
Property | Value/Description |
---|---|
Density | 8.60 g/cm³ |
Melting Point | 1,250°C – 1,400°C |
Hardness | 55-60 HRC |
Wear Resistance | High, particularly in abrasive and erosive environments. |
Corrosion Resistance | Excellent, particularly in oxidizing environments. |
Thermal Stability | Maintains mechanical properties up to 800°C. |
Tensile Strength | 900 MPa |
Oxidation Resistance | Superior, especially at elevated temperatures. |
Machinability | Moderate; due to hardness, specialized tools may be required for machining. |
Why Choose 93Co7Ni Powder for Your Applications?
You might be wondering, “Is 93Co7Ni powder the right material for my project?” Let’s dive into the specific benefits that make this powder a top choice for high-wear and high-temperature applications.
1. Outstanding Wear Resistance
If your application involves high friction or abrasion, 93Co7Ni powder is a fantastic option. The cobalt content, combined with nickel, enhances the powder’s ability to resist wear and tear, making it ideal for parts that endure constant use and friction, such as bearings, valve seats, and cutting tools.
2. High-Temperature Stability
In industries like aerospace and power generation, components are regularly exposed to extreme heat. 93Co7Ni powder excels in these conditions, maintaining its hardness and strength even at temperatures as high as 800°C. This makes it a reliable choice for turbine blades, engine components, and heat exchangers.
3. Superior Oxidation and Corrosion Resistance
One of the standout qualities of 93Co7Ni powder is its excellent oxidation resistance. The combination of cobalt and nickel forms a protective oxide layer, which shields the material from environmental attack, especially at high temperatures. This makes it suitable for marine and chemical processing applications, where exposure to corrosive environments is common.
4. Versatility in Manufacturing
As a powder, 93Co7Ni can be used in a variety of manufacturing processes, such as thermal spraying, laser cladding, and additive manufacturing. The powder’s flowability ensures uniform application, resulting in high-quality coatings or 3D-printed components with minimal defects.
Applications of 93Co7Ni Powder
Now that we’ve covered the properties, let’s look at where 93Co7Ni powder shines in real-world applications. This cobalt-nickel alloy is used across a range of industries, thanks to its durability, temperature stability, and corrosion resistance.
Common Applications of 93Co7Ni Powder
Industry | Application |
---|---|
Aerospace | Turbine blades, engine components, bearings, and seals that must withstand high temperatures and wear. |
Automotive | High-performance engine parts, turbochargers, and exhaust systems exposed to high temperatures and friction. |
Medical | Orthopedic implants, surgical tools, and other medical devices requiring biocompatibility and wear resistance. |
Power Generation | Steam turbine parts, heat exchangers, and other components exposed to high-temperature gas or steam. |
Oil & Gas | Drill bits, valve seats, and other components exposed to abrasive particles and corrosive fluids in harsh environments. |
Marine | Propellers, shafts, and fittings that must resist corrosion from saltwater exposure. |
Tooling | Cutting tools, dies, and molds that require high wear resistance and thermal stability. |
Specifications, Sizes, Grades, and Standards of 93Co7Ni Powder
When considering 93Co7Ni powder for your project, it’s essential to understand the available specifications, sizes, and grades. These factors can influence the performance and suitability of the material in different applications.
Specifications of 93Co7Ni Powder
Specification | Details |
---|---|
Particle Size | Typically ranges from 15 to 53 microns, depending on the intended application and manufacturing process. |
Powder Morphology | Spherical particles for optimal flowability and uniform deposition in thermal spray and additive manufacturing. |
ASTM Standards | ASTM F75 for cobalt-based alloys used in medical and industrial applications. |
ISO Standards | ISO 5832-12 for cobalt-chromium-molybdenum alloys used in medical implants and other high-performance components. |
Hardness Range | 55-60 HRC, depending on heat treatment and application requirements. |
UNS Number | UNS R30035 |
The specifications ensure that the powder meets the requirements for quality, consistency, and performance in your specific application.
Suppliers and Pricing of 93Co7Ni Powder
The cost of 93Co7Ni powder can vary based on the supplier, quantity, and specific requirements of your project. It’s crucial to source the material from reputable suppliers to ensure it meets the necessary quality standards.
Suppliers and Pricing of 93Co7Ni Powder
Supplier | Price Range (per kg) | Notes |
---|---|---|
Kennametal | $400 – $550 | Known for high-quality cobalt-based powders, including 93Co7Ni for thermal spraying and additive manufacturing. |
Oerlikon Metco | $420 – $580 | Offers advanced materials for wear-resistant coatings; specializes in powders like 93Co7Ni. |
Höganäs AB | $410 – $540 | A leading supplier of metal powders, including cobalt-nickel alloys for industrial applications. |
Carpenter Technology | $430 – $570 | Supplies high-performance alloys, including 93Co7Ni, for aerospace, energy, and medical sectors. |
Powder Alloy Corporation | $400 – $530 | Provides top-quality cobalt-based powders for use in thermal spraying and laser cladding applications. |
While 93Co7Ni powder can be relatively expensive, typically ranging from $400 to $580 per kilogram, its performance and longevity often make it a cost-effective choice, especially in high-demand environments.
Comparing the Pros and Cons of 93Co7Ni Powder
Before making a final decision, it’s important to weigh the advantages and limitations of 93Co7Ni powder. This will help you determine whether it’s the right material for your specific application.
Advantages of 93Co7Ni Powder
Advantage | Why It’s Important |
---|---|
High Wear Resistance: Handles abrasion and erosion exceptionally well. | Ideal for applications like cutting tools, turbine blades, and bearings that experience high friction. |
Thermal Stability: Retains hardness and strength at high temperatures. | Perfect for engine components, heat exchangers, and other high-temperature applications. |
Corrosion Resistance: Performs well in environments exposed to chemicals and saltwater. | Suitable for marine, oil & gas, and chemical processing industries. |
Versatile Powder Form: Can be used in various manufacturing processes such as thermal spraying. | Ensures consistent, high-quality results in coatings and additive manufacturing. |
Long Service Life: Reduces the need for frequent replacements, lowering maintenance costs. | Particularly beneficial in industries where downtime is costly, like aerospace and power generation. |
Limitations of 93Co7Ni Powder
Limitation | Why It’s a Challenge |
---|---|
High Cost: More expensive than some other wear-resistant materials. | May not be feasible for low-budget applications or projects with less demanding material requirements. |
Moderate Toughness: Not ideal for applications with high impact or shock loads. | For impact-heavy applications, other materials may offer better performance. |
Difficult to Machine: Due to its hardness, machining can be challenging. | Requires specialized tools and techniques, which can increase production costs. |
Limited Availability: Not always readily available in all regions or in large quantities. | May result in longer lead times depending on supplier and demand. |
FAQs About 93Co7Ni Powder
Here are some frequently asked questions to help clarify any uncertainties you might have about 93Co7Ni powder.
Question | Answer |
---|---|
What is 93Co7Ni powder used for? | It’s widely used in industries such as aerospace, automotive, and medical, specifically for high-wear, high-temperature parts like turbines, engine components, and implants. |
How much does 93Co7Ni powder cost? | Pricing typically ranges from $400 to $580 per kilogram, depending on the supplier and specific application requirements. |
Can 93Co7Ni powder be used in additive manufacturing? | Yes, it’s commonly used in additive manufacturing processes like laser cladding and powder-bed fusion for creating durable, wear-resistant parts. |
What industries commonly use 93Co7Ni powder? | Aerospace, automotive, medical, oil & gas, and power generation industries frequently use it for components exposed to high wear and heat. |
What makes 93Co7Ni powder resistant to wear? | Its high cobalt content gives it exceptional wear resistance, particularly in abrasive and high-friction environments. |
Is 93Co7Ni powder magnetic? | No, it is generally non-magnetic, making it suitable for applications where non-magnetic properties are required. |
Can 93Co7Ni powder withstand high heat? | Yes, it maintains its hardness and durability at temperatures up to 800°C, making it perfect for high-temperature applications like turbines. |
How does 93Co7Ni compare to other cobalt alloys? | Compared to other cobalt-based alloys, it offers a good balance of wear resistance, thermal stability, and corrosion protection. |
What are the main advantages of using 93Co7Ni powder? | The primary advantages include its high wear resistance, thermal stability, and corrosion resistance, especially in demanding environments. |
Conclusion: Is 93Co7Ni Powder Right for Your Project?
It is a game-changer for industries that require high-performance materials capable of withstanding extreme conditions. Whether you’re in aerospace, automotive, or medical, this cobalt-nickel alloy provides the wear resistance, thermal stability, and corrosion protection needed for critical applications.
However, it’s essential to weigh the pros and cons, particularly when it comes to cost and machinability. While 93Co7Ni powder may come at a higher price, its durability and long service life often make it a cost-effective solution in the long run—especially in high-demand environments.
So, is 93Co7Ni powder the right choice for your next project? If you need a material that can handle extreme wear, heat, and corrosion, then the answer is likely yes!
Get Latest Price
About Met3DP
Product Category
HOT SALE
CONTACT US
Any questions? Send us message now! We’ll serve your request with a whole team after receiving your message.
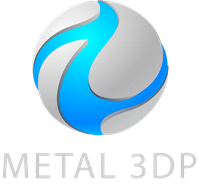
Metal Powders for 3D Printing and Additive Manufacturing