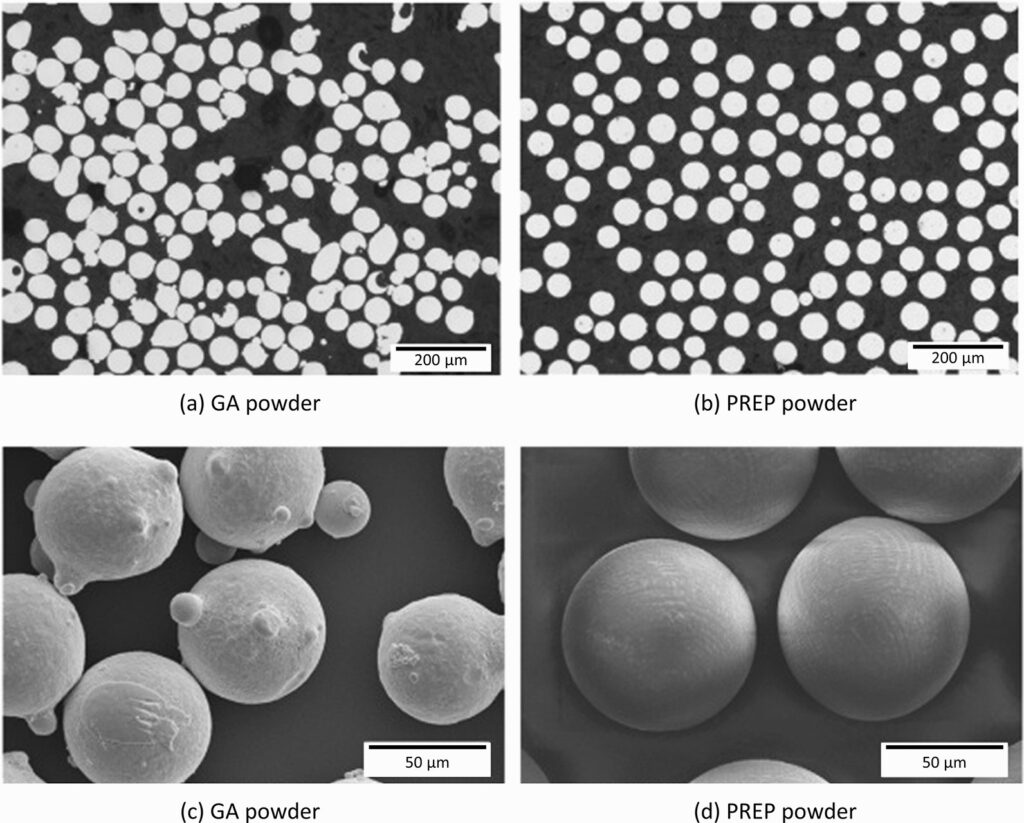
CoCrFeMnNi Powder: The Ultimate Guide for 2025
Low MOQ
Provide low minimum order quantity to meet different needs.
OEM & ODM
Provide customized products and design services to meet unique customer needs.
Adequate Stock
Ensure fast order processing and provide reliable and efficient service.
Customer Satisfaction
Provide high quality products with customer satisfaction at the core.
share this article
Table of Contents
Overview
CoCrFeMnNi powder, commonly referred to as a High-Entropy Alloy (HEA), is a specialized metal powder known for its exceptional mechanical strength, wear resistance, and corrosion resistance. This alloy is widely used in aerospace, biomedical, energy, and high-performance industrial applications due to its unique combination of five major elements—Cobalt (Co), Chromium (Cr), Iron (Fe), Manganese (Mn), and Nickel (Ni) in nearly equal proportions.
Key Properties
✔ Exceptional strength and ductility, making it ideal for high-stress applications
✔ Superior corrosion and oxidation resistance, ensuring long-term performance in harsh environments
✔ High-temperature stability, improving reliability in extreme thermal conditions
✔ Optimized for additive manufacturing (AM), including Laser Powder Bed Fusion (LPBF) and Electron Beam Melting (EBM)
This guide will cover:
- Best CoCrFeMnNi powder for 3D printing
- How to choose the right CoCrFeMnNi powder
- Top suppliers of CoCrFeMnNi powder
- Properties and industrial applications
- Production methods and cost analysis
- Comparison of gas-atomized vs. plasma-atomized CoCrFeMnNi powder
Best CoCrFeMnNi Powder for 3D Printing in 2025
Why CoCrFeMnNi Powder is Ideal for Additive Manufacturing?
- High strength and toughness, making it perfect for aerospace and energy industries
- Excellent printability, reducing defects in LPBF and EBM processes
- Outstanding oxidation and corrosion resistance, making it suitable for marine and chemical applications
- Superior fatigue resistance, ensuring durability in high-stress applications
Key Factors for Selecting CoCrFeMnNi Powder for 3D Printing
- Spherical morphology for optimal powder flowability
- Controlled particle size distribution enhances printability and layer adhesion
- Low oxygen & impurity levels prevent powder degradation
- Consistent mechanical properties post-processing
Comparison for Different 3D Printing Technologies
3D Printing Technology | Recommended CoCrFeMnNi Powder | Advantages | Challenges |
---|---|---|---|
Laser Powder Bed Fusion (LPBF) | Gas-atomized spherical powder (15-45µm) | High precision, fine details | Requires optimized laser parameters |
Electron Beam Melting (EBM) | Plasma-atomized powder (45-105µm) | Low residual stress | Limited material availability |
Direct Energy Deposition (DED) | Gas-atomized powder (50-150µm) | Large-scale part production | Requires post-processing |
Binder Jetting | Irregular or spherical powder (30-80µm) | High-speed production | Requires sintering & infiltration |
For high-performance 3D printing applications, Met3DP’s gas-atomized CoCrFeMnNi powder is the best choice. Learn more about Met3DP’s high-quality metal powders.
Related Products
How to Choose the Right CoCrFeMnNi Powder
Selecting the best CoCrFeMnNi powder depends on several factors, including particle size distribution, atomization process, and application-specific requirements.
1. Particle Size Distribution (PSD)
- Fine powders (15-45µm) → Best for LPBF (Laser Powder Bed Fusion)
- Medium powders (45-105µm) → Suitable for EBM & Binder Jetting
- Coarse powders (50-150µm) → Used in DED (Direct Energy Deposition)
2. Powder Morphology
- Spherical Powder → Best for 3D printing and powder bed fusion technologies
- Irregular Powder → Suitable for Binder Jetting & Sintering
3. Atomization Process
- Gas-Atomized Powder → High purity, excellent flowability, best for 3D printing
- Plasma-Atomized Powder → Ultra-high purity, best for aerospace and biomedical applications
For high-precision 3D printing, Met3DP’s gas-atomized CoCrFeMnNi powder is the best choice. Contact Met3DP for more details.
Production Methods
The manufacturing method of CoCrFeMnNi powder plays a crucial role in determining its particle morphology, purity, and mechanical properties, which directly impact its performance in additive manufacturing, aerospace, and biomedical applications.
Comparison of Production Methods
Production Method | Particle Shape | Purity | Best Applications | Cost |
---|---|---|---|---|
Gas Atomization (GA) | Spherical | High | 3D Printing, Aerospace, Biomedical | Medium |
Plasma Atomization (PA) | Highly Spherical | Ultra High | High-End AM, Aerospace, Biomedical Implants | High |
Vacuum Induction Melting + Gas Atomization (VIGA) | Spherical | Ultra-High | Aerospace Components, High-Precision AM | Very High |
PREP (Plasma Rotating Electrode Process) | Highly Spherical | Ultra-Pure | Biomedical, High-Performance Structural Components | Very High |
1. Gas Atomization (GA)
Process:
- Molten CoCrFeMnNi alloy is atomized into fine droplets using high-pressure inert gas (argon or nitrogen), which rapidly solidifies into spherical powder particles.
Advantages:
✔ Highly spherical morphology, improving flowability and printability
✔ Low oxygen content, reducing oxidation defects
✔ Excellent particle size distribution, ensuring consistent layer deposition in additive manufacturing
Best for: Laser Powder Bed Fusion (LPBF), Electron Beam Melting (EBM), and Direct Energy Deposition (DED)
2. Plasma Atomization (PA)
Process:
- CoCrFeMnNi wire is fed into a high-energy plasma torch, melting it into fine droplets that form highly spherical powder particles.
Advantages:
✔ Perfect spherical shape, ensuring superior flowability in powder bed fusion processes
✔ Ultra-high purity, making it ideal for biomedical and aerospace applications
✔ Minimal satellite particles, leading to superior print quality
Disadvantages:
✖ Higher production costs
✖ Limited scalability for large-scale production
Best for: High-performance biomedical implants and aerospace components
3. PREP (Plasma Rotating Electrode Process)
Process:
- A rotating CoCrFeMnNi electrode is melted by plasma, while centrifugal force atomizes the molten material into fine spherical particles.
Advantages:
✔ Ultra-high purity, with minimal contamination
✔ Highly spherical morphology, leading to excellent flowability
✔ Minimal porosity, making it ideal for biomedical and aerospace applications
Disadvantages:
✖ Very high cost
✖ Limited scalability
Best for: Biomedical implants, aerospace turbine blades, and high-performance structural components
For high-quality additive manufacturing, Met3DP’s gas-atomized CoCrFeMnNi powder is the best choice. Explore Met3DP’s powder production solutions.
Cost Analysis in 2025
The cost of CoCrFeMnNi powder is influenced by several factors, such as production method, particle morphology, purity level, and application-specific requirements.
Factors Affecting Cost
- Production Method – PREP and plasma-atomized powders are the most expensive, while gas-atomized powders offer a more balanced cost-performance ratio.
- Particle Shape – Spherical powders (for AM) are more expensive than irregular powders.
- Purity Level – Higher purity = Higher cost.
- Market Demand – Increased demand from biomedical, aerospace, and high-performance applications influences pricing.
Estimated Price Ranges
Powder Type | Price (USD/kg) | Best For |
---|---|---|
Gas-Atomized CoCrFeMnNi Powder | 500−500 – 500−900 | 3D Printing, Aerospace, Biomedical |
Plasma-Atomized CoCrFeMnNi Powder | 1,300−1,300 – 1,300−2,500 | Biomedical Implants, Aerospace Turbines |
PREP CoCrFeMnNi Powder | 3,000−3,000 – 3,000−5,000 | High-Purity Biomedical Components |
For cost-effective, high-quality CoCrFeMnNi powder, Met3DP provides precision-engineered solutions tailored to industrial needs. Contact Met3DP for pricing and availability.
FAQ
Q1: What is the best CoCrFeMnNi powder for 3D printing?
Gas-atomized spherical CoCrFeMnNi powder is optimal for LPBF, EBM, and DED due to its excellent flowability and low oxygen content.
Q2: How does CoCrFeMnNi compare to traditional stainless steel alloys?
CoCrFeMnNi offers superior high-temperature strength, corrosion resistance, and mechanical toughness, whereas stainless steels like 316L are more cost-effective but have lower mechanical properties.
Q3: Can CoCrFeMnNi powder be used for aerospace applications?
Yes, CoCrFeMnNi is widely used in aerospace for turbine blades, jet engines, and high-temperature structural components due to its high strength and oxidation resistance.
Q4: Where can I buy high-quality CoCrFeMnNi powder?
Met3DP is a leading supplier of gas-atomized CoCrFeMnNi powder, optimized for 3D printing and high-performance applications. Contact Met3DP today!
Conclusion
It is an exceptional high-performance High-Entropy Alloy (HEA) for aerospace, biomedical, additive manufacturing, and high-temperature industrial applications. Choosing the right powder type, production method, and supplier ensures optimal performance and reliability.
Why Choose Met3DP’s CoCrFeMnNi Powder?
✅ Industry-leading gas atomization technology
✅ High-purity spherical powders for additive manufacturing
✅ Reliable supply chain & global distribution
For high-performance CoCrFeMnNi powder, Met3DP provides state-of-the-art solutions tailored to industrial demands.
Want to learn more or get a quote? Contact Met3DP today!
Get Latest Price
About Met3DP
Product Category
HOT SALE
CONTACT US
Any questions? Send us message now! We’ll serve your request with a whole team after receiving your message.
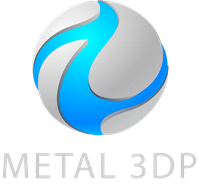
Metal Powders for 3D Printing and Additive Manufacturing