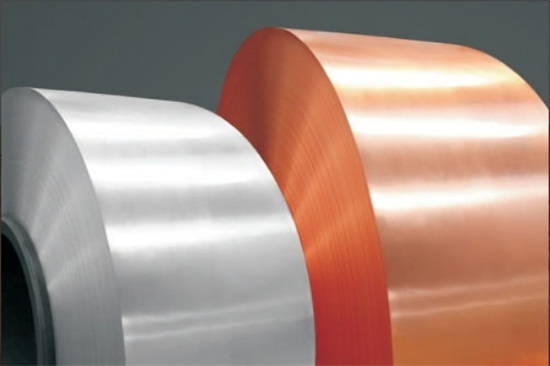
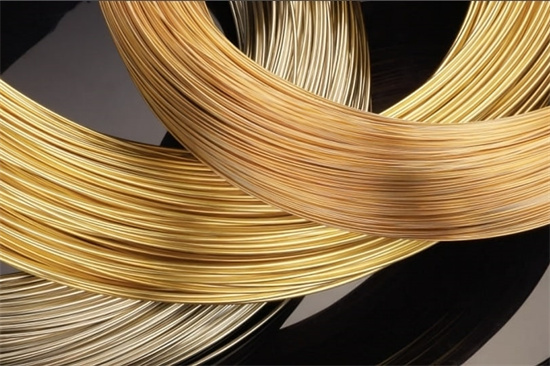
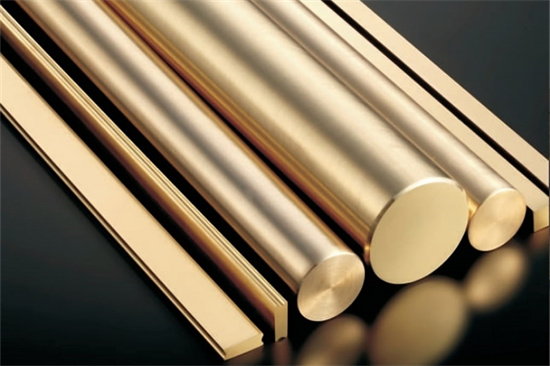
CuNiP: Discover the Superior Copper-Nickel-Phosphorus Alloy
Low MOQ
Provide low minimum order quantity to meet different needs.
OEM & ODM
Provide customized products and design services to meet unique customer needs.
Adequate Stock
Ensure fast order processing and provide reliable and efficient service.
Customer Satisfaction
Provide high quality products with customer satisfaction at the core.
share this article
Table of Contents
In the world of advanced materials, CuNiP (Copper-Nickel-Phosphorus) stands out as a highly specialized alloy known for its strength, corrosion resistance, and superior conductivity. This alloy is a popular choice in industries ranging from electronics to automotive and marine engineering, where precision, performance, and reliability are non-negotiable.
But what exactly makes CuNiP so special? How does this alloy compare to others, and where should you consider using it? In this comprehensive guide, we’ll dive deep into everything you need to know about CuNiP, including its composition, applications, mechanical properties, and even the cost you can expect when sourcing this material.
Overview
CuNiP, or Copper-Nickel-Phosphorus, is an alloy that offers an impressive blend of mechanical strength, thermal and electrical conductivity, and resistance to wear and corrosion. What sets this alloy apart is its ability to maintain these properties even in harsh environments, making it a top choice for demanding applications.
Key Features :
- High Conductivity: Ideal for electrical applications where both strength and conductivity are crucial.
- Corrosion Resistance: Performs exceptionally well in marine and industrial environments.
- Wear Resistance: Thanks to the addition of phosphorus, CuNiP offers enhanced durability under mechanical stress.
- Thermal Stability: Can withstand elevated temperatures without losing its structural integrity.
Composition and Properties
The unique performance characteristics of CuNiP are derived from its chemical composition. The combination of nickel and phosphorus with copper creates an alloy that balances conductivity with mechanical strength and corrosion resistance.
Chemical Composition Breakdown
Element | Percentage (%) |
---|---|
Copper (Cu) | 92 – 95 |
Nickel (Ni) | 1.0 – 2.5 |
Phosphorus (P) | 0.03 – 0.35 |
Other Elements | Trace amounts |
- Copper (Cu): The primary element, responsible for the alloy’s electrical conductivity and thermal properties.
- Nickel (Ni): Enhances mechanical strength and corrosion resistance, particularly in marine environments.
- Phosphorus (P): Improves wear resistance and adds strength to the alloy without compromising its conductivity.
Mechanical and Physical Properties
Property | Typical Value |
---|---|
Tensile Strength | 400 – 600 MPa |
Yield Strength | 250 – 400 MPa |
Elongation | 10 – 20% |
Hardness | 100 – 150 HV |
Electrical Conductivity | 40 – 60% IACS |
Density | 8.9 g/cm³ |
Thermal Conductivity | 180 – 220 W/mK |
Corrosion Resistance | Excellent, especially in marine and chemical environments |
Why the Composition Matters:
- Nickel and phosphorus improve the alloy’s wear resistance and corrosion resistance, making CuNiP suitable for demanding environments.
- Copper ensures the alloy retains a high level of thermal and electrical conductivity, crucial for electronic and mechanical components.
Applications: Where It Excels
Thanks to its unique combination of strength, corrosion resistance, and conductivity,it is used in a variety of industries. Let’s take a closer look at where this alloy truly shines.
Common Applications
Industry | Applications |
---|---|
Electronics | Connectors, terminals, switches, relays |
Automotive | Sensors, electrical contacts, connectors |
Marine | Corrosion-resistant components, valves, fittings |
Telecommunications | RF connectors, signal contacts, antennas |
Aerospace | High-strength fasteners, connectors, springs |
Energy | Power distribution components, bushings |
Why CuNiP Is an Ideal Material for These Applications:
- Electronics: It is frequently used in connectors and switches where electrical performance and reliability are key. It offers an excellent combination of strength and conductivity.
- Automotive: CuNiP’s wear resistance and ability to withstand mechanical stress make it ideal for use in sensors and contacts within vehicles, where high performance is required over long lifespans.
- Marine: Its outstanding corrosion resistance makes it the go-to material for marine components, such as valves and fittings, that are constantly exposed to saltwater environments.
Specifications, Sizes, and Grades
When selecting it for a specific application, it’s important to understand the available sizes, grades, and standards associated with this alloy to ensure it meets your project’s exact requirements.
Specifications and Sizes
Specification | Details |
---|---|
Form | Strip, sheet, wire, rod, foil |
Thickness Range | 0.03 mm to 4 mm |
Width Range | 1 mm to 300 mm |
Temper | Annealed, half-hard, full-hard |
Standards | ASTM B422, EN 1652, JIS H3270 |
Typical Grades | CuNiP1, CuNiP2, CuNiP3 (varying Ni and P contents for specific applications) |
Grades
Grade | Key Characteristics |
---|---|
CuNiP1 | General-purpose grade, balanced properties |
CuNiP2 | Higher nickel content for enhanced corrosion resistance |
CuNiP3 | Optimized for applications requiring superior conductivity |
Why Standards Matter:
Adhering to industry standards ensures that the CuNiP you purchase is of high quality and suitable for specific applications. Always check the relevant standards and grades when selecting your material to avoid costly mistakes.
Suppliers and Pricing
The cost of CuNiP can vary significantly depending on factors such as grade, form, and quantity. Knowing where to source it and understanding the pricing structure can help you get the best deal without compromising on quality.
Suppliers and Pricing Details
Supplier | Location | Price Range (per kg) | Delivery Time |
---|---|---|---|
Global Alloy Metals | USA | $30 – $50 | 2-3 weeks |
EuroCopper Solutions | Europe | $28 – $45 | 1-2 weeks |
AsiaMet Alloy Corp. | China | $25 – $40 | 3-4 weeks |
CopperTech International | India | $27 – $43 | 2-4 weeks |
Superior Alloys Ltd. | UK | $32 – $49 | 1-2 weeks |
Factors Influencing CuNiP Pricing:
- Grade: Higher nickel content grades like CuNiP2 tend to cost more due to enhanced corrosion resistance and mechanical properties.
- Form: CuNiP in wire or foil form can be more expensive per kilogram compared to rod or sheet due to additional processing steps.
- Order Quantity: Bulk orders typically reduce the overall price per kilogram by offering volume discounts.
Advantages and Limitations
Like any alloy, it comes with its strengths and weaknesses. Below is a comprehensive look at the advantages and limitations of using it in various applications.
Advantages and Limitations
Advantages | Limitations |
---|---|
Excellent electrical conductivity | Slightly lower conductivity than pure copper |
High corrosion resistance, especially in marine environments | More expensive than standard copper alloys |
Superior wear resistance | Requires precise processing to maximize performance |
Maintains properties in high-temperature environments | Limited ductility in harder tempers |
Is CuNiP the Right Material for Your Project?
If you require an alloy that balances mechanical strength with conductivity and corrosion resistance, particularly in marine or industrial environments, it is an excellent choice. However, if cost or maximum conductivity is your top priority, you may want to consider other options such as pure copper or brass.
CuNiP Compared to Other Copper Alloys
Choosing the right alloy often comes down to comparing several options side-by-side. Here, we’ll compare CuNiP with other popular copper alloys like C11000 (pure copper) and CuNi2Si to help you make an informed decision.
CuNiP vs. C11000 and CuNi2Si
Property | CuNiP | C11000 (Pure Copper) | CuNi2Si |
---|---|---|---|
Tensile Strength | 400 – 600 MPa | 200 – 300 MPa | 550 – 800 MPa |
Yield Strength | 250 – 400 MPa | 70 – 100 MPa | 300 – 450 MPa |
Electrical Conductivity | 40 – 60% IACS | 100% IACS | 30 – 50% IACS |
Corrosion Resistance | Excellent | Moderate | Excellent |
Cost | Moderate | Low | Moderate |
Applications | Connectors, springs, contacts | Wiring, general use | High-stress components, connectors |
Key Takeaways:
- It offers a balance of strength and conductivity, making it ideal for electrical components that require durability.
- Pure copper (C11000) is the go-to for applications where maximum conductivity is needed, but it lacks the strength and wear resistance of CuNiP.
- CuNi2Si provides higher strength but slightly lower conductivity, making it better suited for mechanical components under high stress.
Frequently Asked Questions (FAQ)
To better understand CuNiP, here are some of the most frequently asked questions about this versatile alloy.
Question | Answer |
---|---|
What is CuNiP used for? | It is commonly used in industries like electronics, automotive, and marine for connectors, terminals, and springs. |
How does CuNiP compare to pure copper? | While it has slightly lower conductivity than pure copper, it offers superior strength and corrosion resistance. |
Is CuNiP suitable for high-temperature environments? | Yes, it can withstand moderate to high temperatures, making it suitable for thermal applications. |
What makes CuNiP corrosion-resistant? | The addition of nickel and phosphorus enhances CuNiP’s resistance to corrosion, especially in marine environments. |
How much does CuNiP cost? | It costs generally range from $25 to $50 per kg, depending on the supplier, grade, and form. |
What standards apply to CuNiP? | It is governed by standards such as ASTM B422, EN 1652, and JIS H3270, ensuring quality and performance. |
Conclusion
In conclusion, it is a high-performance alloy that offers an exceptional blend of strength, wear resistance, conductivity, and corrosion resistance. It is widely used in industries where reliability and durability are essential, such as electronics, automotive, marine, and aerospace.
If you need a material that can withstand mechanical stress, high temperatures, and corrosive environments while still delivering good electrical conductivity, it is an excellent choice. However, if cost or maximum conductivity is your primary concern, you might want to explore alternatives like pure copper or other copper alloys.
Get Latest Price
About Met3DP
Product Category
HOT SALE
CONTACT US
Any questions? Send us message now! We’ll serve your request with a whole team after receiving your message.
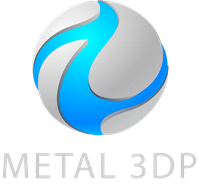
Metal Powders for 3D Printing and Additive Manufacturing