Disadvantages of EBM process
Table of Contents
Electron Beam Melting (EBM) has revolutionized additive manufacturing (AM), enabling the creation of complex, high-performance metal parts. But like any technology, EBM comes with its own set of challenges. Let’s delve into the limitations of EBM, exploring its impact on material selection, surface quality, and overall process efficiency.
The Equipment Cost of EBM Process is High
Imagine a high-tech machine that hums with the power of an electron beam, meticulously melting metal powder layer by layer. That’s the essence of EBM. However, this sophisticated technology comes with a hefty price tag. EBM machines are significantly more expensive compared to other AM techniques like Fused Deposition Modeling (FDM) or Selective Laser Melting (SLM). This upfront investment can be a major hurdle for companies considering EBM integration.
Consider this analogy: Think of buying a top-of-the-line sports car versus a reliable family sedan. EBM is the high-performance machine, offering exceptional capabilities but demanding a premium price. While FDM and SLM might be more affordable options, they might not deliver the same level of precision and material properties.
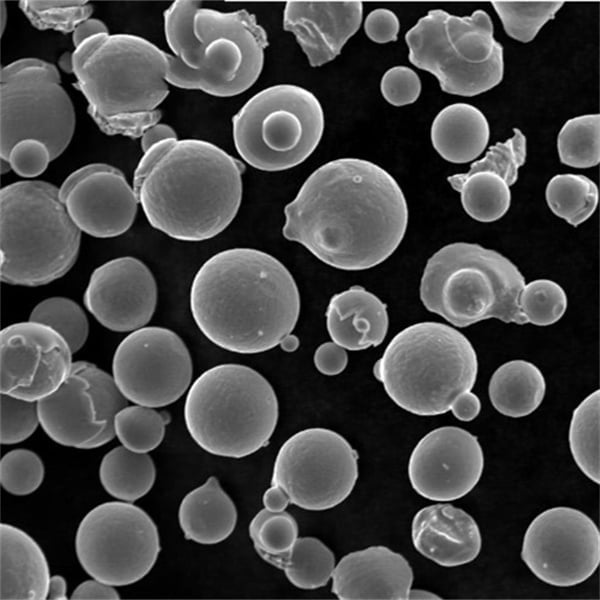
Limited Material Selection for EBM Process
EBM thrives on its ability to handle highly reactive metals. However, the process itself imposes limitations on the types of materials it can work with. Here’s a breakdown of some commonly used metal powders in EBM, along with their properties:
Metal Powders for EBM
Metal Powder | Description | Properties | Applications |
---|---|---|---|
Titanium Grade 2 (Ti-6Al-4V) | The workhorse of EBM, known for its excellent strength-to-weight ratio and biocompatibility. | High strength, good corrosion resistance, lightweight | Aerospace components, biomedical implants, dental prosthetics |
Titanium Grade 5 (Ti-6Al-4Eli) | A variant of Ti-6Al-4V with improved strength but slightly lower ductility. | High strength, moderate ductility, good corrosion resistance | Aerospace components, demanding industrial applications |
Cobalt Chrome (CoCr) | A biocompatible alloy widely used in medical implants. | Excellent wear resistance, biocompatibility | Hip and knee replacements, dental implants |
Inconel 625 (IN625) | A high-performance nickel-chromium superalloy known for its exceptional resistance to heat and corrosion. | High strength, excellent oxidation resistance, good weldability | Gas turbine components, aerospace applications, chemical processing equipment |
Stainless Steel 316L (SS316L) | A versatile stainless steel grade offering good corrosion resistance and biocompatibility. | Moderate strength, good corrosion resistance, biocompatible | Medical devices, chemical processing equipment, food and beverage applications |
Copper (Cu) | A pure copper powder used for its high thermal and electrical conductivity. | Excellent conductivity, good machinability | Heat sinks, electrical components, thermal management applications |
Molybdenum (Mo) | A refractory metal known for its high melting point and strength at elevated temperatures. | High melting point, good strength at high temperatures | Crucible liners, high-temperature furnace components |
Tungsten (W) | Another refractory metal with exceptional strength and heat resistance. | Very high melting point, excellent strength at high temperatures | Electrodes, welding applications, armor components |
Nickel (Ni) | A pure nickel powder used for its good corrosion resistance and electrical conductivity. | Moderate strength, good corrosion resistance, good conductivity | Electrical components, chemical processing equipment |
Iron (Fe) | A pure iron powder with limited applications in EBM due to its tendency to oxidize. | Good mechanical properties, low cost (compared to other EBM powders) | Research and development purposes, prototyping |
The Takeaway: While EBM can handle these and some other specialized metal powders, its compatibility is not as extensive as other AM techniques like SLM, which can work with a wider range of materials, including plastics and polymers.
Why EBM Takes Its Time
You’re absolutely right, Electron Beam Melting (EBM) falls on the slower side of the spectrum compared to other additive manufacturing (AM) techniques. While EBM boasts incredible advantages like complex geometries and high-strength metal parts, patience is a key ingredient for success. Here’s a deeper dive into why EBM takes its time:
1. Meltic Meltdown: A Layer-by-Layer Ballet
EBM builds objects meticulously, one layer at a time. An electron beam scans across a thin layer of metal powder, melting it precisely according to the design. This controlled melting ensures intricate features and dense parts. However, compared to techniques that might deposit entire layers at once, this layer-by-layer approach inherently adds build time.
2. Precision Demands Precision Time
EBM excels at creating highly detailed and complex parts. These intricate features require a very focused electron beam and precise control over the melting process. Unfortunately, achieving this level of accuracy necessitates a slower build speed compared to processes that prioritize faster deposition over intricate details.
3. The Heat is On (But Not Too On)
EBM operates in a vacuum at elevated temperatures, typically around 650-700°C. This high temperature ensures proper melting and bonding of the metal particles. However, maintaining this temperature uniformly throughout the build chamber takes time. Additionally, rapid cooling can lead to warping or cracking in the final part. EBM employs a controlled cooldown process to prevent these issues, further adding to the overall build time.
So, is EBM Slow? Not Necessarily…Depends on Your Needs
While EBM might not be the speediest AM process, its strengths lie elsewhere. If your project prioritizes complex geometries, exceptional material properties, and high-strength metal parts, the wait time associated with EBM might be a worthwhile trade-off.
There are Other Drawbacks to the EBM Process
While the high cost, limited material selection, and slower build speed are major limitations, EBM has other challenges to consider:
- Surface Roughness: Due to the nature of the EBM process, the resulting parts can have a rough surface finish. This might necessitate additional post-processing steps like machining or polishing to achieve a desired surface quality, adding to the overall production time and cost.
- Support Structures: EBM requires intricate support structures to prevent warping and distortion during the melting process. Removing these supports can be a delicate task, and sometimes, they can leave behind marks on the finished part, requiring further finishing work.
- Vacuum Environment: EBM operates in a high-vacuum chamber, which adds complexity to the setup and maintenance of the equipment. This can also limit the size of parts that can be printed due to the limitations of the vacuum chamber size.
- Environmental Concerns: EBM involves the use of electron beams in a vacuum environment. This can generate X-rays, which require proper shielding to ensure operator safety. Additionally, the process might involve the use of hazardous materials like binders in the metal powders, requiring proper handling and disposal procedures.
- Limited Design Freedom: Compared to some other AM techniques, EBM might have limitations in terms of design freedom. The need for support structures and the potential for residual stresses can restrict the creation of highly intricate internal features.
Weighing the Pros and Cons: Is EBM Right for You?
EBM is a powerful AM technology, but it’s not a one-size-fits-all solution. Carefully consider these limitations alongside its strengths (exceptional material properties, high-density parts) to determine if EBM aligns with your specific needs. Here’s a table summarizing the pros and cons of EBM:
EBM Process: Advantages vs. Disadvantages
Advantages | Disadvantages |
---|---|
High-quality metal parts with excellent strength-to-weight ratio | High equipment cost |
Wide range of compatible metal powders (including highly reactive metals) | Limited material selection compared to other AM techniques |
Excellent dimensional accuracy and surface finish (after post-processing) | Slower build speed compared to some AM methods |
Complex geometries possible | Surface roughness can require additional finishing |
The Bottom Line: EBM is a valuable tool for creating high-performance metal parts in applications like aerospace, medicine, and demanding industrial settings. However, its limitations in terms of cost, speed, and post-processing requirements necessitate careful consideration before integrating it into your workflow.
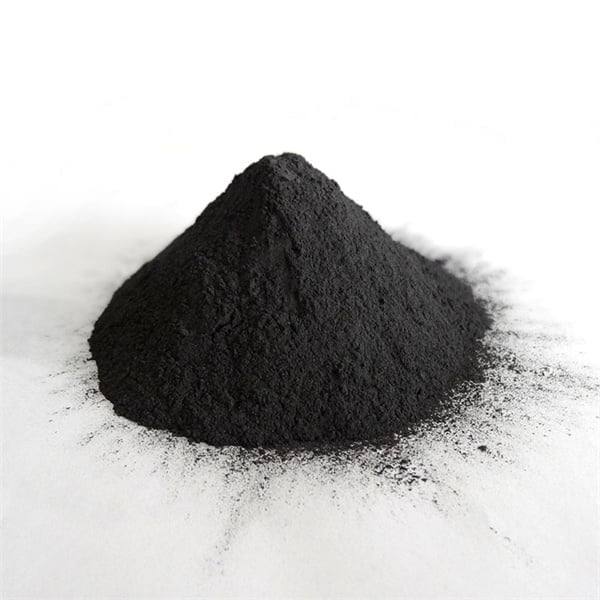
FAQ
Q: Is the high cost of EBM a dealbreaker?
A: Not necessarily. If your application prioritizes exceptional material properties and part strength, and the production volume is relatively low, the high cost of EBM might be justified. However, for high-volume applications or those where cost is a major concern, other AM techniques might be more suitable.
Q: Are there ways to mitigate the surface roughness in EBM?
A: Yes, several strategies can help. Using finer metal powders, optimizing beam parameters, and applying post-processing techniques like machining or polishing can improve surface finish. However, these steps add to the overall production time and cost.
Q: Can EBM be used for large parts?
A: The size of parts that can be printed using EBM is limited by the size of the vacuum chamber. While some machines can handle larger builds, EBM is generally better suited for smaller to medium-sized parts.
Q: What are the safety considerations for EBM?
A: EBM involves X-rays and potentially hazardous materials. Proper shielding and safety protocols are essential to protect operators. It’s crucial to consult the machine manufacturer’s guidelines and relevant safety regulations.
Q: Are there any advancements that might address the limitations of EBM?
A: Research and development in EBM are ongoing. Advancements in areas like faster build speeds, broader material compatibility, and improved surface quality hold promise for overcoming some of the current limitations.
By understanding the limitations of EBM, you can make informed decisions about whether it’s the right AM technology for your specific needs. EBM offers a unique combination of capabilities, but careful consideration of its drawbacks is crucial for successful implementation.
Share On
MET3DP Technology Co., LTD is a leading provider of additive manufacturing solutions headquartered in Qingdao, China. Our company specializes in 3D printing equipment and high-performance metal powders for industrial applications.
Inquiry to get best price and customized Solution for your business!
Related Articles
About Met3DP
Recent Update
Our Product
CONTACT US
Any questions? Send us message now! We’ll serve your request with a whole team after receiving your message.
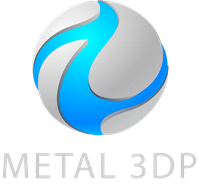
Metal Powders for 3D Printing and Additive Manufacturing