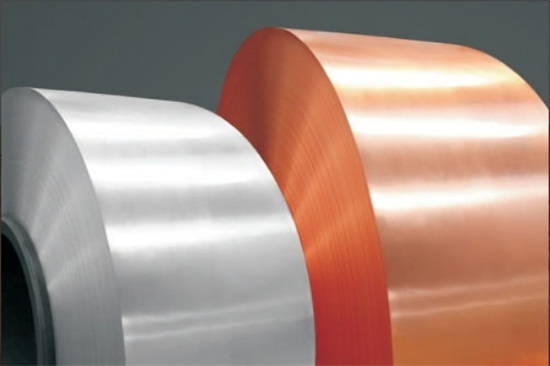
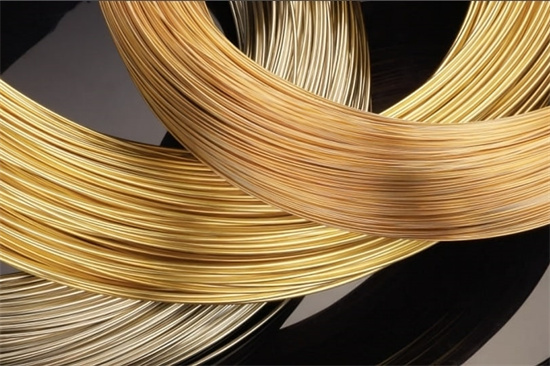
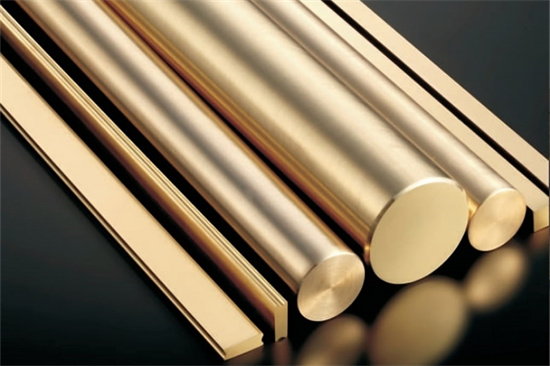
Efficient Energy Saving Alloy: The Future of Sustainable Materials
Low MOQ
Provide low minimum order quantity to meet different needs.
OEM & ODM
Provide customized products and design services to meet unique customer needs.
Adequate Stock
Ensure fast order processing and provide reliable and efficient service.
Customer Satisfaction
Provide high quality products with customer satisfaction at the core.
share this article
Table of Contents
In today’s world, where the demand for energy-efficient technologies is growing steadily, one aspect that often gets overlooked is the role of materials. Enter the game-changing concept of the Efficient Energy Saving Alloy—a material specifically engineered to reduce energy consumption in various applications. These alloys are designed not only to perform better but to do so in a way that conserves energy, reduces waste, and contributes to a more sustainable future.
But what exactly is an Efficient Energy Saving Alloy? How does it work, and why is it so important in industries ranging from automotive to electronics? In this comprehensive guide, we’ll break down everything you need to know about these innovative materials, including their types, properties, applications, and much more.
Overview: What is an Efficient Energy Saving Alloy?
At its core, an Efficient Energy Saving Alloy is a material composed of a blend of metals that, when combined, exhibit properties that enable them to use less energy during their manufacturing, operation, or lifespan. These alloys are increasingly being used to address global environmental concerns such as carbon emissions, energy consumption, and resource depletion.
These alloys are engineered to have high thermal stability, low electrical resistivity, and excellent mechanical properties, all while requiring less energy to process, maintain, or operate. Whether you’re looking at lightweight automotive components, high-conductivity electrical wiring, or durable aerospace parts, these alloys offer solutions that are both economical and environmentally friendly.
Types, Composition, and Properties of Efficient Energy Saving Alloys
Different industries require different types of energy-saving alloys, each tailored to meet specific performance and energy efficiency requirements. From high-strength steels to aluminum alloys and other smart materials, the composition and properties of these alloys are diverse.
Below is a breakdown of some common types of Efficient Energy Saving Alloys, along with their composition, properties, and key characteristics.
Common Types and Composition of Efficient Energy Saving Alloys
Alloy Type | Composition | Key Properties |
---|---|---|
Aluminum Alloys | Aluminum (90-95%), Magnesium (2-5%), Silicon (1-3%) | Lightweight, high strength-to-weight ratio, good thermal conductivity. |
High-Strength Steel (HSS) | Iron (Fe), Carbon (C), Manganese (Mn), Nickel (Ni) | High tensile strength, lightweight, exceptional durability. |
Copper Alloys | Copper (Cu) with trace amounts of Tin (Sn) or Zinc (Zn) | Excellent electrical conductivity, corrosion resistance. |
Nickel-Based Alloys | Nickel (Ni), Chromium (Cr), Molybdenum (Mo) | High heat resistance, corrosion resistance, long-lasting durability. |
Titanium Alloys | Titanium (Ti), Aluminum (Al), Vanadium (V) | Lightweight, excellent corrosion resistance, high strength. |
Magnesium Alloys | Magnesium (90-95%), Aluminum (3-6%), Zinc (Zn) | Extremely lightweight, good machinability, moderate strength. |
Key Properties of Efficient Energy Saving Alloys
Property | Description |
---|---|
Low Density | Many energy-saving alloys, such as aluminum and magnesium, are lightweight, leading to energy savings in transportation and manufacturing applications. |
High Electrical Conductivity | Alloys like copper and aluminum have high conductivity, reducing energy losses in electrical systems. |
Thermal Stability | Nickel-based and titanium alloys retain strength and integrity at high temperatures, which is critical for energy efficiency in high-heat environments like aerospace and power plants. |
Corrosion Resistance | Many efficient alloys resist corrosion, requiring less maintenance and prolonging the lifespan of components, reducing energy costs over time. |
Recyclability | Most energy-saving alloys are highly recyclable, reducing the energy required for producing new materials. |
These properties make Efficient Energy Saving Alloys ideal for applications where energy conservation is critical, whether it’s through lightweighting, improving electrical efficiency, or enhancing durability.
Applications of Efficient Energy Saving Alloys
So, where exactly do we see these energy-saving alloys in action? The uses are vast and span multiple industries. From transportation and construction to consumer electronics and renewable energy systems, Efficient Energy Saving Alloys are revolutionizing the way we think about material performance and sustainability.
Common Applications of Efficient Energy Saving Alloys
Industry | Application |
---|---|
Automotive | Lightweight components for electric vehicles (EVs), improving fuel efficiency. |
Aerospace | High-temperature alloys for engines, reducing energy consumption in flight. |
Electronics | Conductive materials for wiring and circuit boards, reducing energy loss in devices. |
Renewable Energy | Turbine blades and solar panel frames, improving energy efficiency in power generation. |
Construction | Reinforced steel with better strength-to-weight ratios for energy-efficient buildings. |
Expanded Application Insights
- Automotive: In the push for fuel efficiency and electric vehicle (EV) advancements, lightweighting is critical. Aluminum and magnesium alloys are increasingly being used in vehicle frames, reducing overall weight and thus improving fuel consumption and battery performance in EVs.
- Aerospace: High-strength, low-weight alloys such as titanium and nickel-based superalloys are used in aerospace applications due to their ability to perform at high temperatures without compromising structural integrity. These materials help lower fuel consumption by making aircraft lighter and more efficient.
- Electronics: Copper and aluminum alloys have long been used in electronics due to their excellent electrical conductivity. These materials reduce energy losses in electrical systems, improving the efficiency of devices ranging from smartphones to industrial machinery.
- Renewable Energy: In the world of wind turbines and solar panels, aluminum and steel alloys play a major role. These materials are used to create lightweight yet strong structures that can withstand the elements while optimizing energy production.
- Construction: The construction industry is increasingly looking toward energy-efficient materials to build green buildings. High-strength steel and aluminum alloys, for example, are used for reinforcement to reduce the amount of material needed, cutting down on both energy consumption and costs.
Specifications, Sizes, and Standards for Efficient Energy Saving Alloys
When selecting an Efficient Energy Saving Alloy, it’s essential to adhere to established specifications and standards that ensure performance and reliability. Different alloys come in a variety of sizes and grades, each tailored to specific applications.
Specifications and Sizes of Efficient Energy Saving Alloys
Alloy Type | Standard | Available Sizes |
---|---|---|
Aluminum Alloys | ASTM B209, EN 485 | Sheets: 0.1mm to 100mm thick, Rods: 10mm to 400mm diameter |
High-Strength Steel (HSS) | ASTM A1011, EN 10025 | Plates: 1mm to 50mm thickness, Bars: 10mm to 200mm diameter |
Copper Alloys | ASTM B152, EN 1652 | Sheets: 0.5mm to 50mm thick, Rods: 5mm to 300mm diameter |
Nickel-Based Alloys | ASTM B168, ISO 6208 | Sheets: 0.25mm to 50mm thick, Bars: 10mm to 350mm diameter |
Titanium Alloys | ASTM B348, AMS 4928 | Plates: 0.5mm to 100mm thick, Rods: 10mm to 250mm diameter |
Common Standards for Efficient Energy Saving Alloys
Standard Code | Description |
---|---|
ASTM B209 | Standard for Aluminum and Aluminum-Alloy Sheet and Plate. |
EN 485 | European standard for Aluminum and Aluminum-Alloy products. |
ASTM A1011 | Standard for Steel, including hot-rolled carbon and high-strength alloys. |
ISO 6208 | International standard for Nickel-Based Alloys. |
AMS 4928 | Aerospace Material Specification for Titanium Alloys. |
Suppliers and Pricing for Efficient Energy Saving Alloys
As with any material, the cost of Efficient Energy Saving Alloys can vary widely depending on factors such as composition, purity, and order size. Below is a breakdown of typical suppliers and pricing information to give you a better idea of what to expect when sourcing these materials.
Suppliers and Pricing for Efficient Energy Saving Alloys
Supplier | Location | Price Range (per kg) | Lead Time |
---|---|---|---|
Thyssenkrupp Materials | Global | $10.00 – $15.00 (Aluminum Alloy) | 3-5 weeks |
Kobe Steel | Japan | $12.00 – $18.00 (High-Strength Steel) | 4-6 weeks |
Wieland Group | Europe, USA | $9.00 – $14.00 (Copper Alloys) | 3-4 weeks |
ATI Metals | USA | $25.00 – $40.00 (Nickel-Based Alloys) | 6-8 weeks |
VSMPO-AVISMA | Russia | $30.00 – $50.00 (Titanium Alloys) | 5-6 weeks |
Price Insights
- Aluminum Alloys: Typically range from $10.00 to $15.00 per kg, making them one of the more affordable energy-saving alloys, especially when ordered in bulk.
- High-Strength Steels: Prices can range from $12.00 to $18.00 per kg, depending on the grade and specific alloy composition.
- Nickel-Based Alloys: These are among the more expensive options, generally ranging from $25.00 to $40.00 per kg, largely due to their superior heat resistance and corrosion resistance.
- Titanium Alloys: These alloys are premium materials with prices ranging from $30.00 to $50.00 per kg, but their lightweight and high-strength properties are worth the investment in aerospace and high-performance applications.
Advantages and Disadvantages of Efficient Energy Saving Alloys
While Efficient Energy Saving Alloys offer a multitude of benefits, they also come with their own set of challenges. Understanding the advantages and disadvantages will help you make informed decisions about their use in your projects.
Advantages and Limitations of Efficient Energy Saving Alloys
Advantages | Limitations |
---|---|
Lightweight (Aluminum, Titanium) | Higher initial costs for certain alloys (e.g., Titanium, Nickel-based alloys) |
Improved Energy Efficiency | Some alloys may require specialized processing techniques. |
Corrosion Resistance (Copper, Nickel) | Availability may be limited depending on geographic location. |
High Recyclability | Some alloys, like Nickel-based, require intensive recycling processes. |
Excellent Thermal and Electrical Conductivity | Not all alloys are suitable for extreme high-temperature environments. |
Key Advantages
- Energy Savings: The lightweight nature of materials like aluminum and magnesium alloys can significantly reduce fuel consumption in vehicles and energy usage in manufacturing processes.
- Corrosion Resistance: Alloys like nickel-based and copper alloys offer exceptional corrosion resistance, making them ideal for applications in harsh environments like marine or chemical processing industries.
- Recyclability: Most Efficient Energy Saving Alloys are highly recyclable, reducing the energy needed to create new materials and contributing to a circular economy.
Limitations
- Cost: Some of these alloys, particularly nickel-based and titanium alloys, come with a higher price tag. This can make them less accessible for some projects, particularly those with tight budgets.
- Specialized Processing: Many Efficient Energy Saving Alloys require precise processing techniques, which can further drive up costs and complicate manufacturing schedules.
Efficient Energy Saving Alloys vs. Traditional Alloys
Now that we’ve covered the benefits and limitations, how do Efficient Energy Saving Alloys stack up against traditional alloys?
Comparison Between Efficient Energy Saving Alloys and Traditional Alloys
Property | Efficient Energy Saving Alloys | Traditional Alloys |
---|---|---|
Energy Efficiency | High—designed to conserve energy during use and processing | Moderate—requires more energy to process and operate. |
Weight | Lightweight (Aluminum, Magnesium, Titanium) | Heavier (Standard Steel, Cast Iron) |
Corrosion Resistance | Excellent for many efficient alloys (Nickel, Copper-based) | Varies—often requires coatings or treatments. |
Cost | Higher upfront costs but more savings in the long run | Lower initial cost but higher maintenance and energy costs. |
Recyclability | Highly recyclable, reducing long-term energy costs | Varies—some traditional alloys are less recyclable. |
Key Comparisons
- Energy Efficiency: Efficient alloys are designed with energy conservation in mind, whereas traditional materials may require more energy to produce, process, and operate.
- Weight: Efficient alloys, particularly aluminum and magnesium, are lighter than traditional materials like steel or cast iron, which reduces energy consumption in transportation and manufacturing.
- Cost: While traditional alloys may have lower initial costs, Efficient Energy Saving Alloys often save money in the long run due to their enhanced durability, recyclability, and lower energy use.
Frequently Asked Questions (FAQ) About Efficient Energy Saving Alloys
Curious to learn more? Here are some of the most frequently asked questions about Efficient Energy Saving Alloys.
Question | Answer |
---|---|
What are Efficient Energy Saving Alloys? | Alloys specifically designed to reduce energy consumption in various applications. |
Which industries use these alloys the most? | Industries like automotive, aerospace, electronics, and renewable energy rely heavily on them. |
How do these alloys reduce energy consumption? | By being lightweight, thermally stable, and corrosion-resistant, which reduces energy use in production and operation. |
Are Efficient Energy Saving Alloys expensive? | Some, like titanium and nickel-based alloys, can be more expensive but offer long-term savings. |
Can these alloys be recycled? | Yes, most efficient energy-saving alloys are highly recyclable. |
What is the most common alloy used for energy efficiency? | Aluminum alloys are the most common due to their light weight and good conductivity. |
Conclusion: Why Efficient Energy Saving Alloys are Key to a Sustainable Future
In an era where sustainability is no longer a choice but a necessity, Efficient Energy Saving Alloys are playing a pivotal role in shaping the future of green technology. From automotive to aerospace and beyond, these alloys are helping industries reduce their carbon footprints, improve energy efficiency, and create products that are stronger, lighter, and more durable than ever before.
While some alloys, such as titanium and nickel-based alloys, may come with a higher price tag, the long-term savings in terms of energy costs, maintenance, and reduced environmental impact make them a worthwhile investment for any forward-thinking company.
As we look to the future, it’s clear that Efficient Energy Saving Alloys will continue to be at the forefront of innovation, offering solutions to some of the world’s most pressing environmental challenges. So, whether you’re designing the next generation of electric vehicles or crafting high-performance aerospace components, these alloys are the key to building a more sustainable, energy-efficient world.
Maybe you want to know more about our products, please contact us
Get Latest Price
About Met3DP
Product Category
HOT SALE
CONTACT US
Any questions? Send us message now! We’ll serve your request with a whole team after receiving your message.
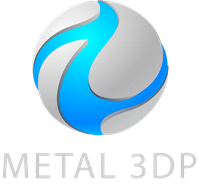
Metal Powders for 3D Printing and Additive Manufacturing