Fewer Satellite Particles Powder
Table of Contents
Imagine building intricate objects layer by layer, with each layer a precise deposit of metal powder. This is the magic of Additive Manufacturing (AM), also known as 3D printing. But what if these tiny metal particles, instead of forming a smooth surface, clump together, creating imperfections? This is where the concept of “satellite particles” comes in, and achieving a powder with fewer satellite particles becomes crucial for a flawless finish.
What are Satellite Particles?
Think of a perfect metal sphere, ideal for AM. Now, imagine smaller, irregularly shaped particles clinging to its surface. These are satellite particles, acting like unwelcome hitchhikers on the journey to a smooth, high-quality final product. Their presence can lead to several issues:
- Surface Roughness: Satellite particles disrupt the even deposition of powder, resulting in a rough and uneven surface finish on the printed object.
- Weak Interlayer Bonding: When these satellite particles come between the main powder layers, they can hinder the proper fusion between them, leading to weak interlayer bonding and potentially compromising the object’s strength.
- Porosity: Satellite particles can trap air pockets within the printed object, creating unwanted porosity that affects its mechanical properties and aesthetics.
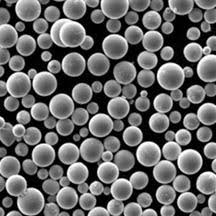
The Quest for Flawless Metal Powders
Several metal powder types are used in AM, each with its own characteristics and susceptibility to satellite particles. Here’s a closer look at ten popular choices:
Metal Powder Model | Description |
---|---|
Gas-Atomized Stainless Steel 316L (SS316L): A versatile and widely used powder, offering excellent corrosion resistance. | Moderately Prone |
Electron Beam-Melted (EBM) Titanium (Ti-6Al-4V): High-strength titanium alloy known for its biocompatibility. | Less Prone |
Nickel-based Superalloy Inconel 625: Renowned for its high-temperature strength. | Moderately Prone |
Aluminum Alloy AlSi10Mg: A popular choice for lightweight applications with good weldability. | Highly Prone |
Copper (Cu): Offers excellent thermal and electrical conductivity. | Moderately Prone |
Cobalt Chrome (CoCr): Biocompatible material used for medical implants. | Less Prone |
Tool Steel (H13): A wear-resistant steel for tooling applications. | Moderately Prone |
Inconel 718: A high-strength, high-temperature nickel-chromium alloy. | Moderately Prone |
Maraging Steel: High-strength steel with excellent toughness. | Moderately Prone |
Tungsten (W): Offers exceptional high-temperature properties. | Highly Prone |
As you can see, the susceptibility to satellite particles varies depending on the metal and the manufacturing process. Gas-atomized powders, due to their rapid solidification, tend to be more prone to forming satellite particles compared to EBM powders. Particle size and distribution also play a role, with finer powders having a higher chance of clumping.
Benefits of Fewer Satellite Particles Powder
Here’s why achieving a powder with fewer satellite particles is crucial for successful AM:
- Superior Surface Finish: Reduced surface roughness translates to a visually appealing and high-quality final product.
- Enhanced Mechanical Properties: Stronger interlayer bonding leads to a more robust object with improved mechanical strength and fatigue resistance.
- Reduced Post-Processing: Minimized surface imperfections require less post-processing steps like grinding or polishing, saving time and resources.
- Improved Design Freedom: Flawless finishes enable the creation of intricate geometries with finer details.
Challenges and Solutions:
Manufacturing metal powders with minimal satellite particles requires a delicate balance. Here are some strategies employed by manufacturers:
- Process Optimization: Fine-tuning parameters like atomization gas pressure and flow rate can minimize the formation of satellite particles during the powder production process.
- Sphericalization: Post-processing techniques like plasma atomization can be used to transform irregular particles into near-perfect spheres, reducing the chances of clumping.
- Powder Sieving: Sifting the powder removes larger particles and agglomerates, promoting a more consistent particle size distribution.
The Future of Fewer Satellite Particles Powder
As AM continues to evolve, the demand for high-quality metal powders with minimal satellite particles will only increase. Research is ongoing in developing new manufacturing techniques and post-processing methods to achieve even greater levels of powder perfection. Imagine a future where AM produces objects with near-mirror finishes and unparalleled strength, all thanks to the relentless pursuit of fewer satellite particles.
Applications of Fewer Satellite Particles Powder
The benefits of fewer satellite particles powders extend to various AM applications, demanding both aesthetics and functionality:
- Aerospace: Flawless finishes are crucial for components in airplanes and spacecraft, where even minor surface imperfections can affect aerodynamics and performance. Fewer satellite particles ensure a smooth airflow, reducing drag and improving fuel efficiency.
- Medical Implants: In the world of medical implants, biocompatibility and strength reign supreme. Powders with minimal satellite particles produce implants with a smooth surface, reducing the risk of infection and promoting better tissue integration. Additionally, strong interlayer bonding ensures the implant can withstand the stresses and strains of daily life.
- Consumer Goods: From customized jewelry to high-end consumer electronics, AM is making its mark on everyday products. Powders with minimal satellite particles enable the creation of aesthetically pleasing objects with intricate details and a luxurious feel. Imagine a phone case with a flawless metallic finish, or a pair of custom-made sunglasses with a smooth, reflective surface – all thanks to superior powder quality.
- Automotive: The automotive industry is increasingly embracing AM for lightweight components and intricate designs. Fewer satellite particles powders ensure a smooth surface finish for parts like pistons and engine components, reducing friction and wear. Additionally, the improved mechanical properties can lead to lighter yet stronger components, contributing to better fuel efficiency.
Considerations and Trade-offs:
While the pursuit of fewer satellite particles is laudable, it’s important to acknowledge some potential trade-offs:
- Cost: Manufacturing powders with minimal satellite particles can be a complex and resource-intensive process, potentially leading to higher powder costs.
- Availability: Not all metal powders are readily available with minimal satellite particles. Depending on the specific material and desired particle size, there might be limitations in availability.
Finding the Right Balance:
The decision of whether to prioritize minimal satellite particles depends on the specific application. For critical components in aerospace or medical implants, where flawless finishes and exceptional strength are paramount, the extra cost and potential limitations in availability might be justifiable. However, for less demanding applications like certain consumer goods, a balance might be struck between cost and the level of surface finish achievable.
Advantages and Limitations of Fewer Satellite Particles Powder
Feature | Advantages | Limitations |
---|---|---|
Surface Finish | Superior, smooth, visually appealing | May increase powder cost |
Mechanical Properties | Stronger interlayer bonding, improved strength, fatigue resistance | Not always readily available for all materials |
Post-Processing | Reduced need for grinding/polishing, saves time and resources | May require specialized manufacturing techniques |
Design Freedom | Enables intricate geometries and finer details | Might not be cost-effective for all applications |
Specifying Fewer Satellite Particles Powder:
When working with AM service providers, it’s crucial to clearly specify your requirements regarding satellite particles. Here are some key points to consider:
- Application: Communicate the intended use of the printed object. This helps the service provider recommend the appropriate powder type with the desired level of minimal satellite particles.
- Surface Finish Expectations: Clearly define the desired surface finish requirements. Are you aiming for a flawless, mirror-like finish, or is a moderately smooth surface acceptable?
- Budgetary Constraints: Discuss your budget limitations. The service provider can then suggest powder options that balance minimal satellite particles with cost-effectiveness.
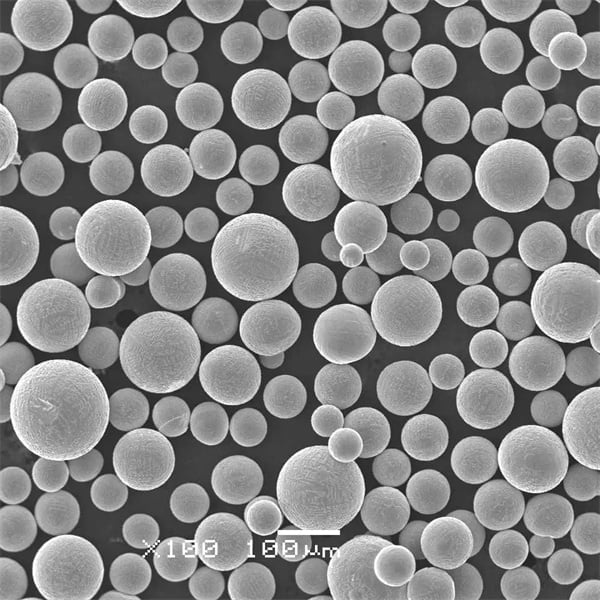
FAQs
Q: How can I tell if a metal powder has a lot of satellite particles?
A: Visual inspection under a microscope can reveal the presence of satellite particles. Reputable AM service providers typically provide detailed information on the powder characteristics, including the level of satellite particles.
Q: Are there any alternative methods to achieve a smooth surface finish with powders containing satellite particles?
A: Yes, post-processing techniques like grinding, polishing, or chemical etching can be used to improve the surface finish of a printed object. However, these add to the overall processing time and cost.
Q: What are the environmental implications of manufacturing powders with minimal satellite particles?
A: Some powder manufacturing techniques can be energy-intensive. However, ongoing research is focused on developing more sustainable and eco-friendly methods for producing high-quality metal powders.
Share On
MET3DP Technology Co., LTD is a leading provider of additive manufacturing solutions headquartered in Qingdao, China. Our company specializes in 3D printing equipment and high-performance metal powders for industrial applications.
Inquiry to get best price and customized Solution for your business!
Related Articles
About Met3DP
Recent Update
Our Product
CONTACT US
Any questions? Send us message now! We’ll serve your request with a whole team after receiving your message.
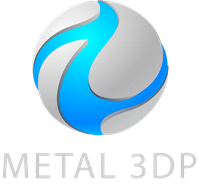
Metal Powders for 3D Printing and Additive Manufacturing
COMPANY
PRODUCT
cONTACT INFO
- Qingdao City, Shandong, China
- [email protected]
- [email protected]
- +86 19116340731