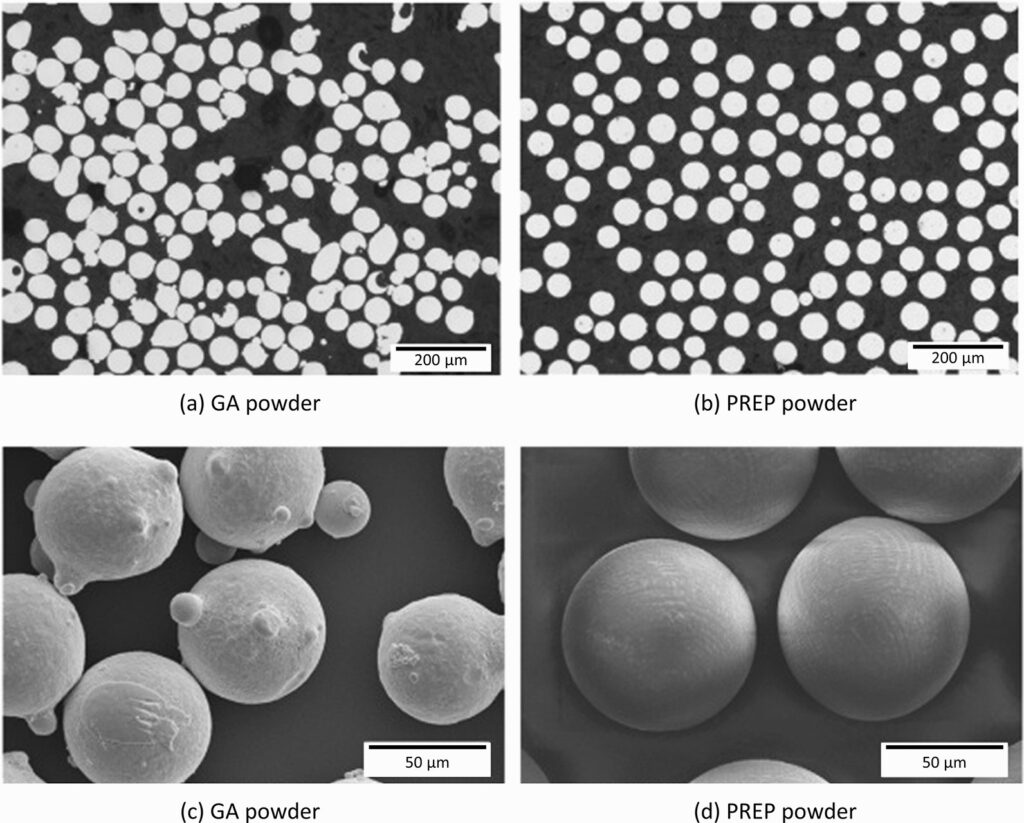
Haynes 75 Powder: Superior Composition and Versatile Applications
Low MOQ
Provide low minimum order quantity to meet different needs.
OEM & ODM
Provide customized products and design services to meet unique customer needs.
Adequate Stock
Ensure fast order processing and provide reliable and efficient service.
Customer Satisfaction
Provide high quality products with customer satisfaction at the core.
share this article
Table of Contents
When it comes to high-performance alloys, few materials stand out quite like Haynes 75 powder. This nickel-chromium alloy is renowned for its exceptional resistance to oxidation and high temperatures, making it a go-to material in industries such as aerospace, power generation, and chemical processing. Whether you need a material that can withstand extreme heat or resist corrosion, Haynes 75 powder offers unparalleled performance.
In this comprehensive guide, we will dive deep into everything you need to know about Haynes 75 powder—its composition, properties, applications, and much more. By the end of this article, you’ll have a clear understanding of why Haynes 75 is a top choice for many critical industrial applications.
Overview
Haynes 75 powder is a nickel-based superalloy that is designed primarily for use in high-temperature environments. Its excellent combination of oxidation resistance and mechanical strength makes it perfect for applications where both corrosion resistance and thermal stability are essential.
Some of the key features of Haynes 75 powder include:
- Outstanding oxidation resistance at high operating temperatures.
- Excellent mechanical properties, including creep resistance and tensile strength.
- Versatility in manufacturing processes, including additive manufacturing and thermal spray coatings.
- Good weldability, which makes it suitable for complex fabrication and repair applications.
Haynes 75 powder is used primarily in applications like gas turbine engines, industrial furnaces, and chemical reactors, where materials are routinely exposed to high levels of heat and corrosive environments.
Composition and Properties of Haynes 75 Powder
The performance of Haynes 75 powder can be attributed to its precise chemical composition. This alloy is primarily a nickel-chromium formulation, with additional elements that enhance its oxidation resistance, durability, and mechanical strength. Understanding this composition is crucial for determining how Haynes 75 powder can meet the needs of specific applications.
Chemical Composition
Element | Weight Percentage (%) | Role in the Alloy |
---|---|---|
Nickel (Ni) | 75.0 | Forms the base of the alloy, providing high-temperature strength and corrosion resistance. |
Chromium (Cr) | 18.5 | Enhances oxidation resistance at high temperatures. |
Iron (Fe) | 5.0 | Adds strength and toughness, but in controlled amounts to maintain corrosion resistance. |
Manganese (Mn) | 1.0 | Improves the alloy’s workability and toughness. |
Silicon (Si) | 0.5 | Helps in oxidation resistance and reduces the risk of carburization. |
Carbon (C) | 0.08 | Adds to the alloy’s creep resistance at high temperatures. |
Titanium (Ti) | 0.2 | Improves creep strength and helps stabilize the alloy during extended exposure to elevated temperatures. |
The high nickel content in Haynes 75 powder provides the material with its excellent corrosion resistance, while the addition of chromium boosts its ability to withstand oxidizing environments at elevated temperatures.
Mechanical and Thermal Properties
The mechanical and thermal properties of Haynes 75 powder are what make it a standout choice in high-stress, high-temperature environments. Below, we break down the key properties that make this alloy so versatile.
Property | Value/Description |
---|---|
Density | 8.30 g/cm³ |
Melting Point | 1350°C – 1400°C (2462°F – 2552°F) |
Ultimate Tensile Strength | 760 MPa (110 ksi) |
Yield Strength | 275 MPa (40 ksi) |
Elongation at Break | 45% |
Hardness | 75-85 HRB (Rockwell B) |
Thermal Conductivity | 11.2 W/m·K |
Creep Resistance | Excellent, particularly at temperatures above 800°C (1472°F). |
Oxidation Resistance | Outstanding, up to temperatures of 1000°C (1832°F). |
These properties make Haynes 75 powder a top choice in high-temperature, high-stress applications, where maintaining mechanical integrity and resisting oxidation are both critical.
Applications of Haynes 75 Powder
The versatility of Haynes 75 powder makes it suitable for a wide range of industrial applications. It’s especially valuable in environments where materials are exposed to extreme heat and oxidizing atmospheres. Below, we explore some of the most common uses of Haynes 75 powder across various industries.
Common Applications by Industry
Industry | Application |
---|---|
Aerospace | Used in gas turbine engines, exhaust systems, and combustion chambers due to its high-temperature stability. |
Power Generation | Employed in industrial gas turbines, boilers, and heat exchangers where oxidation resistance is critical. |
Chemical Processing | Ideal for equipment exposed to corrosive chemicals at high temperatures, such as reactors, valves, and piping. |
Automotive | Applied in turbochargers and exhaust components that require heat resistance and longevity. |
Furnace Manufacturing | Used in industrial furnaces, burners, and retorts that operate at elevated temperatures. |
Why Haynes 75 Powder is Ideal for These Applications
The reason Haynes 75 powder is so widely used across these industries is that it provides a unique combination of oxidation resistance and mechanical strength at high temperatures. In aerospace, for example, the material’s ability to maintain integrity in gas turbine engines means fewer repairs and longer service life. Similarly, in chemical processing, the alloy’s resistance to both heat and corrosive chemicals ensures equipment reliability and reduces downtime.
Specifications, Sizes, and Standards for Haynes 75 Powder
When selecting Haynes 75 powder, it’s crucial to ensure that the material meets the necessary industry standards and fits the specific size and form required for your application. Below, we outline the most common specifications and available sizes for Haynes 75 powder.
Specifications and Standards
Specification/Standard | Details |
---|---|
UNS Number | N06075 |
AMS Standards | AMS 5597, covering sheet, strip, and plate for high-temperature applications. |
ASTM Standards | ASTM B564, ASTM B619, for forged fittings and seamless pipes. |
ISO Standards | ISO 15156, for materials used in sour gas environments. |
Powder Particle Size | 15 to 45 microns, ideal for additive manufacturing and thermal spray coatings. |
Density | 8.30 g/cm³ |
Melting Range | 1350°C – 1400°C (2462°F – 2552°F) |
Available Sizes and Forms
Haynes 75 powder can be purchased in a variety of sizes depending on the intended manufacturing process or application. Below are the most commonly available sizes and forms:
Form | Available Sizes |
---|---|
Powder | Particle sizes typically range from 15 to 45 microns, used for additive manufacturing and metal injection molding. |
Rod/Bar | Available in diameters ranging from 0.5 to 6 inches, used for valves, piping, and large components. |
Sheets and Plates | Available in thicknesses ranging from 2 mm to 50 mm, used for furnace components, heat exchangers, and more. |
Suppliers and Pricing of Haynes 75 Powder
Finding reliable suppliers for Haynes 75 powder is crucial to ensure you get high-quality material that meets all industry standards. Below is a list of some trusted suppliers and the estimated pricing for Haynes 75 powder.
Suppliers and Pricing
Supplier | Price Range (per kg) | Notes |
---|---|---|
Höganäs AB | $900 – $1050 | Specializes in high-performance metal powders for additive manufacturing and thermal spray. |
Carpenter Technology | $950 – $1100 | Offers custom formulations for high-temperature applications. |
Oerlikon Metco | $920 – $1080 | Supplies Haynes 75 powder for thermal spray coatings and laser cladding. |
Sandvik | $880 – $1100 | Focuses on advanced materials for corrosive environments and high-temperature conditions. |
Prices generally range from $880 to $1100 per kilogram, depending on the supplier, particle size, and order volume. Pricing may also fluctuate based on market demand and material availability.
Comparing the Pros and Cons of Haynes 75 Powder
While Haynes 75 powder is an excellent material for high-temperature applications, like any material, it comes with both advantages and limitations. Below, we break down the pros and cons of Haynes 75 powder to help you determine if it’s the right choice for your specific needs.
Advantages
Advantage | Description |
---|---|
High-Temperature Stability: Maintain strength and structural integrity at temperatures up to 1000°C. | Perfect for use in gas turbines, heat exchangers, and industrial furnaces. |
Oxidation Resistance: Resists oxidation in high-temperature environments. | Provides long-lasting protection in combustion chambers, exhaust systems, and chemical reactors. |
Good Weldability: Can be easily welded without compromising mechanical properties. | Suitable for complex fabrication and repair work in demanding environments. |
Corrosion Resistance: Performs well in environments containing sulfur compounds and carbonization. | Ideal for chemical processing and power generation applications. |
Limitations
Limitation | Description |
---|---|
Cost: More expensive than standard stainless steels or other high-temperature alloys. | May not be suitable for budget-sensitive projects. |
Limited Availability: Some specialized forms or particle sizes may require custom orders. | Can lead to longer lead times and higher costs for specific applications. |
Oxidizing Environments: While resistant to oxidation, Haynes 75 may not perform as well in severely oxidizing atmospheres. | Consider other nickel-based alloys for extreme oxidation resistance. |
Work Hardening: Can harden during processing, which may affect machinability. | Requires special care during machining and forming operations. |
FAQs
To further clarify some of the most common questions about Haynes 75 powder, we’ve compiled a list of frequently asked questions. Whether you’re considering this alloy for your next project or just want to learn more, these answers should help.
Question | Answer |
---|---|
What is Haynes 75 powder used for? | It’s widely used in industries such as aerospace, power generation, and chemical processing for high-temperature, high-stress applications. |
How much does Haynes 75 powder cost? | Prices typically range from $880 to $1100 per kilogram, depending on the supplier and specifications. |
Can Haynes 75 powder be used in 3D printing? | Yes, Haynes 75 powder is commonly used in additive manufacturing for creating parts that require heat resistance and oxidation resistance. |
What industries use Haynes 75 powder? | Industries such as aerospace, chemical processing, power generation, and automotive utilize this alloy for its high-temperature performance. |
Is Haynes 75 powder weldable? | Yes, Haynes 75 powder has good weldability, making it suitable for fabrication and repair applications. |
How does Haynes 75 compare to Haynes 188? | While Haynes 75 is ideal for high-temperature oxidation resistance, Haynes 188 offers better thermal fatigue resistance in cyclic environments. |
Can Haynes 75 powder handle high temperatures? | Absolutely, Haynes 75 offers excellent mechanical strength and oxidation resistance at temperatures up to 1000°C (1832°F). |
What are the main advantages of Haynes 75 powder? | Its key advantages include high-temperature stability, oxidation resistance, and good mechanical properties in harsh environments. |
What are the limitations of Haynes 75 powder? | The main limitations include its higher cost and limited availability in certain sizes or forms. |
Conclusion: Why Haynes 75 Powder is the Ideal Choice for High-Temperature Applications
In industries where high-temperature strength and oxidation resistance are critical, Haynes 75 powder offers an exceptional balance of performance and durability. Its unique combination of mechanical properties and resistance to harsh environments makes it a top choice for applications like gas turbines, industrial furnaces, and chemical reactors.
While Haynes 75 powder may come at a higher cost compared to other alloys, its long-term benefits—including reduced maintenance, longer service life, and improved performance—make it a smart investment for industries that demand high-performance materials.
So, if you’re looking for a material that can withstand extreme heat, resist oxidation, and maintain its mechanical integrity in some of the harshest environments, Haynes 75 powder is definitely worth considering. Whether you’re in aerospace, power generation, or chemical processing, this alloy has the potential to significantly enhance the longevity and efficiency of your equipment.
Get Latest Price
About Met3DP
Product Category
HOT SALE
CONTACT US
Any questions? Send us message now! We’ll serve your request with a whole team after receiving your message.
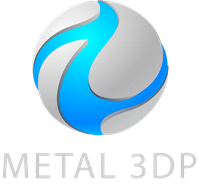
Metal Powders for 3D Printing and Additive Manufacturing