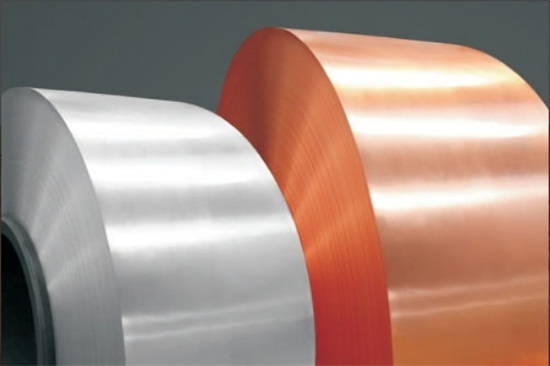
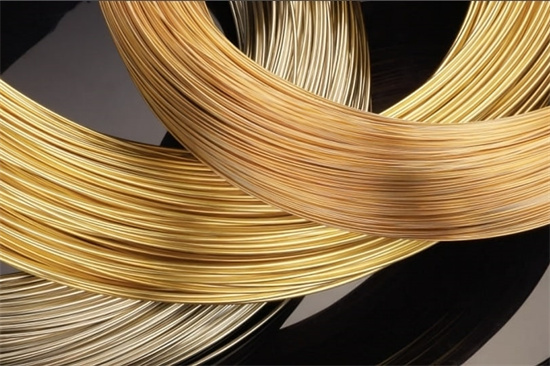
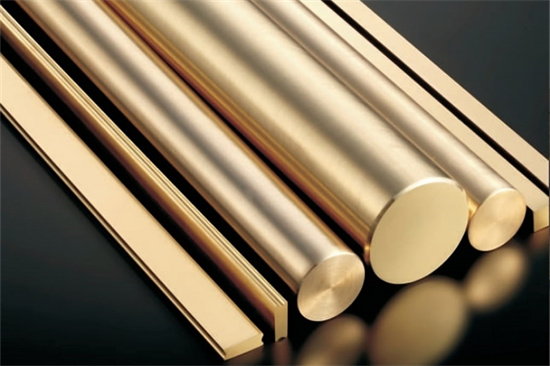
High-Strength Elastic Alloys: Pushing the Limits of Strength and Flexibility
Low MOQ
Provide low minimum order quantity to meet different needs.
OEM & ODM
Provide customized products and design services to meet unique customer needs.
Adequate Stock
Ensure fast order processing and provide reliable and efficient service.
Customer Satisfaction
Provide high quality products with customer satisfaction at the core.
share this article
Table of Contents
If you’ve ever wondered what materials make suspension springs, aerospace components, or precision instruments resilient and durable, the answer often lies in high-strength elastic alloys. These specialized materials combine the ability to withstand high loads with exceptional elasticity, making them essential in a wide range of industries. In this article, we’re going to explore everything you need to know about high-strength elastic alloys, including their composition, properties, applications, pricing, and much more.
Overview of High-Strength Elastic Alloys
High-strength elastic alloys are materials designed to endure extreme stress while retaining their ability to return to their original shape. This combination of high strength and elasticity makes them vital in applications where both flexibility and durability are required. These alloys are often used in industries like aerospace, automotive, electronics, and medical devices, where precision and reliability are non-negotiable.
So, what exactly makes these alloys so special? It’s all about balance. They strike a unique equilibrium between strength and elasticity, allowing them to perform under conditions that would cause other materials to fail. Think of them as the superheroes of the materials world—strong but flexible, tough yet adaptable.
Composition and Properties of High-Strength Elastic Alloys
High-strength elastic alloys are typically composed of a mix of metals that enhance both their strength and elasticity. Commonly used base metals include nickel, titanium, copper, and cobalt, often combined with other elements like chromium, molybdenum, and iron to fine-tune their properties.
Composition Breakdown
Let’s take a closer look at the typical composition of popular high-strength elastic alloys:
Alloy Type | Base Metals | Additional Elements |
---|---|---|
Nickel-Titanium Alloy | Nickel (55-60%), Titanium (40-45%) | Small amounts of copper, chromium |
Cobalt-Chromium Alloy | Cobalt (50-60%), Chromium (20-30%) | Molybdenum, Nickel |
Beryllium Copper Alloy | Copper (94-98%), Beryllium (2%) | Cobalt, Nickel, Iron |
Titanium Alloy (Ti-6Al-4V) | Titanium (90%), Aluminum (6%), Vanadium (4%) | Trace amounts of iron and oxygen |
Each alloy’s unique composition is designed to enhance specific properties, such as corrosion resistance, fatigue endurance, or thermal stability. For example, Nickel-Titanium (Nitinol) is widely known for its shape-memory properties, making it an ideal choice for medical devices that need to return to their original form after deformation.
Key Properties of High-Strength Elastic Alloys
Property | Value |
---|---|
Tensile Strength | 600-1200 MPa |
Elastic Modulus | 100-200 GPa |
Fatigue Strength | High fatigue resistance, often exceeding 10^7 cycles |
Corrosion Resistance | Excellent, especially in marine and chemical environments |
Thermal Stability | Can withstand extreme temperatures, ranging from -200°C to 600°C |
Magnetic Properties | Can be magnetic or non-magnetic, depending on composition |
Density | Varies by alloy, typically between 6.5 and 8.5 g/cm³ |
These alloys are specifically engineered to retain their shape under stress, making them invaluable for applications where high cyclic loads are common, such as springs in automotive suspensions or stents in medical applications.
Applications of High-Strength Elastic Alloys
High-strength elastic alloys have a wide range of applications across various industries. Their ability to withstand extreme mechanical stresses while retaining their shape makes them indispensable in sectors that require both durability and precision.
Common Uses of High-Strength Elastic Alloys
Application Area | Details |
---|---|
Aerospace Components | Used in jet engine parts, landing gear, and other critical aerospace equipment due to their lightweight and high-strength properties. |
Medical Devices | Commonly found in surgical instruments, stents, and orthodontic wires due to their biocompatibility and shape-memory properties. |
Automotive Industry | Utilized in suspension springs, valve springs, and other high-stress components in vehicles. |
Electronics | Used in precision components like connectors, switches, and relays where high fatigue resistance is needed. |
Oil & Gas Industry | Employed in downhole tools and valves where high wear resistance and strength are required. |
Marine Applications | Ideal for propeller shafts, fasteners, and springs that operate in corrosive seawater environments. |
Sports Equipment | Found in high-performance products like golf clubs, tennis rackets, and bicycles for their strength and flexibility. |
These alloys are often used in niche applications where the combination of strength, elasticity, and corrosion resistance is crucial. For instance, in the medical field, Nickel-Titanium (Nitinol) is a go-to material for stents because of its ability to expand and return to its original shape once inside the body.
Specifications, Sizes, and Standards for High-Strength Elastic Alloys
When selecting the right high-strength elastic alloy for a project, it’s essential to consider the available specifications, sizes, and industry standards. Ensuring the material meets the required standards guarantees optimal performance in its intended application.
Specifications and Sizes of High-Strength Elastic Alloys
Alloy Type | Available Forms | Size Range |
---|---|---|
Nickel-Titanium (Nitinol) | Wire, Rod, Strip, Tube | Wire: 0.1 mm to 10 mm, Rod: 5 mm to 50 mm |
Cobalt-Chromium Alloy | Bar, Plate, Wire | Bar: 10 mm to 200 mm, Plate: 1 mm to 20 mm |
Beryllium Copper Alloy | Sheet, Plate, Rod, Wire | Sheet: 0.5 mm to 5 mm, Rod: 2 mm to 100 mm |
Titanium Alloy (Ti-6Al-4V) | Sheet, Bar, Wire, Tubing | Bar: 10 mm to 150 mm, Wire: 0.5 mm to 10 mm |
Standards for High-Strength Elastic Alloys
Standard | Description |
---|---|
ASTM F2063 | Standard for Nickel-Titanium Shape Memory Alloys |
ASTM B194 | Standard for Beryllium Copper Alloy |
ASTM F1537 | Standard for Wrought Cobalt-Chromium-Molybdenum Alloys |
AMS 4928 | Standard for Titanium Alloy Plates and Sheets |
These standards ensure that the materials meet the necessary mechanical properties, chemical composition, and manufacturing quality required for high-performance applications.
Suppliers and Pricing of High-Strength Elastic Alloys
Given their specialized nature, high-strength elastic alloys are typically sourced from suppliers that focus on advanced materials. Pricing can vary significantly based on the alloy type, form, and market conditions. Below is a breakdown of suppliers and estimated pricing for these alloys.
Suppliers and Pricing Estimates
Supplier | Location | Price per kg | Minimum Order Quantity |
---|---|---|---|
ABC Specialty Alloys | USA | $80 – $120 | 50 kg |
Global Metals Ltd. | Europe | $90 – $150 | 100 kg |
Advanced Alloys Co. | Asia | $85 – $130 | 200 kg |
Precision Metals Supplier | Global | $100 – $160 | 500 kg |
Pricing is influenced by factors like alloy composition, form (wire, sheet, rod), and order quantity. For example, Nickel-Titanium (Nitinol) tends to be more expensive due to its shape-memory properties, while Beryllium Copper is typically more affordable.
Advantages and Disadvantages of High-Strength Elastic Alloys
No material is perfect, and high-strength elastic alloys are no exception. While they offer numerous benefits, there are also some limitations to consider. Let’s take a close look at the pros and cons.
Advantages and Limitations
Advantages | Disadvantages |
---|---|
High strength and elasticity – ideal for high-stress applications | Cost – more expensive than standard alloys |
Corrosion-resistant – excellent for harsh environments | Difficult to machine – requires specialized equipment |
Thermal stability – can operate in extreme temperatures | Limited availability – not as widely available as other metals |
Shape memory effect (in Nitinol) – returns to original form | Fatigue resistance can vary based on alloy type and composition |
Non-magnetic options – useful in specialized applications | Work hardening – can become difficult to work with over time |
FAQs About High-Strength Elastic Alloys
Question | Answer |
---|---|
What are high-strength elastic alloys used for? | They’re used in aerospace, medical devices, automotive, and electronics due to their strength, elasticity, and durability. |
What is the most popular high-strength elastic alloy? | Nickel-Titanium (Nitinol) is highly popular for its shape-memory properties, especially in medical devices. |
Are high-strength elastic alloys expensive? | Yes, they tend to be more expensive than traditional alloys due to their specialized properties and limited availability. |
Can high-strength elastic alloys be welded? | Some can, but others, like certain titanium alloys, require specific welding techniques to avoid cracking. |
How do high-strength elastic alloys compare to stainless steel? | These alloys are often stronger and more elastic, but they can be more expensive and harder to machine. |
Do high-strength elastic alloys corrode easily? | No, most are highly corrosion-resistant, making them suitable for marine and chemical environments. |
Conclusion
High-strength elastic alloys are critical to modern engineering and manufacturing, thanks to their unique combination of durability and flexibility. These alloys are essential in high-stress environments, from aerospace parts to medical devices, providing the strength and elasticity needed to perform under extreme conditions.
Whether you’re designing a suspension system for a car or a stent for a medical procedure, understanding the properties, applications, and limitations of high-strength elastic alloys will help you choose the right material for the job. What’s more, while these materials can be more expensive and harder to work with than standard alloys, their performance benefits often outweigh the costs.
By diving into the details of high-strength elastic alloys, you’ve armed yourself with the knowledge to make informed decisions in your next project.
Maybe you want to know more about our products, please contact us
Get Latest Price
About Met3DP
Product Category
HOT SALE
CONTACT US
Any questions? Send us message now! We’ll serve your request with a whole team after receiving your message.