Molybdenum Titanium Powders
Table of Contents
Overview of molybdenum titanium powders
molybdenum titanium powders refer to fine metallic particles of each element produced through atomization processes. They display high strength, hardness and heat resistance.
The powders are used individually or as blends for manufacturing high performance alloys. Their controlled particle size distribution allows complex near-net shape components to be built up from layers during metal 3D printing.
Some key characteristics of molybdenum and titanium powders:
Molybdenum Powder
- Excellent creep resistance and stability at high temperatures
- Low thermal expansion coefficient
- High hardness and wear resistance
- Used as alloying addition to strengthen steels and superalloys
Titanium Powder
- Extremely strong yet lightweight as a structural metal
- Excellent corrosion resistance
- Biocompatible for medical implants
- Reactive and requires controlled processing
Blended/Alloyed Powders
- Combine beneficial properties of each element
- Allows customized material performance
- Requires optimized 3D printing parameters
By manipulating compositions through AM, innovative alloys with superior properties suited for extreme environments can be created.
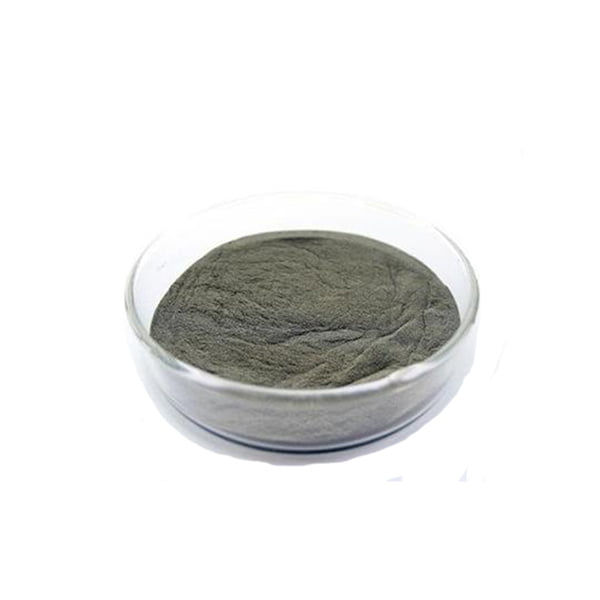
Types of Molybdenum and Titanium Powders
Molybdenum and titanium powders are commercially available in various types for metal additive manufacturing:
Powder Variant | Characteristics | Typical Uses |
---|---|---|
Molybdenum | Pure and alloyed grades | AM of moly alloys, catalysts |
Titanium Ti-6Al-4V | Aerospace alloy | Load-bearing aerostructures |
Titanium Ti-6Al-7Nb | Biocompatible alpha-beta alloy | Medical implants, prosthetics |
Mo-Ti elemental blends | Custom alloy compositions | Advanced engineering applications |
Mo-Ti master alloys | Pre-alloyed blends | Simplified AM processing |
In their elemental form, molybdenum provides high temperature hardness while titanium contributes strength and corrosion resistance. By combining both through AM, innovative alloys can be created with enhanced overall performance.
Composition/Alloying
Molybdenum and titanium powders have the following nominal compositions:
Molybdenum Powder
Element | Composition Range |
---|---|
Molybdenum (Mo) | 99% and above |
Oxygen (O) | 0.01% max |
Carbon (C) | 0.01% max |
Iron (Fe) | 0.01% max |
Other metals | 0.01% max |
High purity is required for reproducibility during AM and downstream processing. Contamination can adversely affect material properties.
Titanium Ti-6Al-4V
Element | Weight % |
---|---|
Titanium (Ti) | Balance |
Aluminum (Al) | 5.5-6.75 |
Vanadium (V) | 3.5-4.5 |
Iron (Fe) | < 0.3 |
Oxygen (O) | <0.2 |
Other metals | <0.1 |
Small amounts of alloying additions of aluminum and vanadium significantly enhance titanium’s strength for load-bearing lightweight structures.
For blended Mo-Ti powders, the relative ratios can be varied from 100% Mo to 100% Ti to create customized alloys. Using both elemental and pre-alloyed blended powders, the unlimited freedom of compositions allows hitherto unexplored alloys to be developed through AM.
Properties of molybdenum titanium powders
Molybdenum Powder
Physical Properties | |
---|---|
Density | 10.22 g/cm3 |
Melting Point | 2610°C |
Thermal Conductivity | 138 W/mK |
Electrical Resistivity | 5.5 μΩ-cm |
Coefficient of Thermal Expansion | 5.3 μm/m-°C |
Mechanical Properties | |
---|---|
Hardness | ~300 HV |
Ultimate Tensile Strength | 600-800 MPa |
Yield Strength (0.2% offset) | 500+ MPa |
Elongation | 30-50% |
Modulus of Elasticity | 325 GPa |
Molybdenum powder enables extremely hard and heat resistant alloys to be fabricated using AM techniques. Parts maintain high strength in oxidizing, corrosive and frictional wear conditions at elevated temperatures exceeding 1000°C.
Titanium Ti-6Al-4V Powder
Physical Properties | Values |
---|---|
Density | 4.43 g/cm3 |
Melting Point | 1604-1660°C |
Thermal Conductivity | 7.2 W/mK |
Electrical Resistivity | 170 μΩ-cm |
Coeff. of Thermal Expansion | 8.6 μm/m-°C |
Mechanical Properties | As Built | Annealed |
---|---|---|
Tensile Strength | 1050 MPa | 950 MPa |
Yield Strength (0.2% offset) | 900 MPa | 850 MPa |
Elongation | ~15% | ~20% |
Hardness | ~350 HV | ~300 HV |
The fine balance of high strength along with decent ductility makes this an extremely popular aerospace alloy for critical printed parts in rocket engines, airframes and turbines.
By blending molybdenum and titanium powders in different ratios, a combination of their properties can be realized in customized alloys.
Applications of Molybdenum Titanium Powders
Application Area | Properties Leveraged | Examples |
---|---|---|
Aerospace & Defense | High strength-to-weight ratio, excellent heat resistance | – Aircraft engine components (disks, blades) <br> – Missile casings – Heat shields |
Biomedical | Biocompatible, good corrosion resistance, high strength | – Orthopedic implants (hip replacements, knee joints) – Dental implants – Surgical instruments |
Chemical Processing | Corrosion resistance, good machinability | – Chemical reactors and vessels – Heat exchangers – Agitator shafts |
Electronics & Electrical | High electrical conductivity, good thermal stability | – Electrical contacts and connectors – High-power resistors – Electrodes for electrical discharge machining (EDM) |
Additive Manufacturing | Tailorable properties, complex geometries possible | – Lightweight, high-performance components for aerospace and automotive – Biocompatible implants with customized structures – Complex heat exchangers for efficient thermal management |
Specifications of molybdenum titanium powders
Molybdenum and titanium powders must meet exact chemistry requirements and stringent quality specifications for additive manufacturing use per industry accepted standards:
Chemical Purity Standards
Powder Grade | Standard |
---|---|
Molybdenum | ASTM B393 |
Titanium Ti-6Al-4V | ASTM F2924 |
Titanium Ti-6Al-7Nb | ASTM F3001 |
Typical Powder Characteristics
Attribute | Requirements | Test Methods |
---|---|---|
Particle shape | Predominantly spherical | SEM imaging per ASTM B822 |
Apparent density | 2 to 5 g/cc | MPIF 04 or ASTM B212 |
Flow rate | >30 sec for Hall flow test | ASTM B213 |
Particle size distribution | D10, D50, D90 optimized for AM process | ASTM B822 |
Loss on ignition (LOI) | Low oxygen/nitrogen | Inert gas fusion analysis |
Microstructure | Defect-free, no satellites | SEM at high magnifications |
The requirements aim to ensure uniform melting behavior, defect-free builds and reproducible end part properties.
Global Suppliers
Many established manufacturers provide molybdenum and titanium powders for AM applications:
Molybdenum Powder
Company | Brand Names | Production Method |
---|---|---|
H.C. Starck | Mo | Electrolytic |
Molymet | PureMo | Hydrogen reduction |
Plansee | MolyPowder | Calcium reduction |
Midwest Tungsten | TeroMoly | Calcium reduction |
Titanium Powder
Company | Grades Offered | Production Methods |
---|---|---|
AP&C | Ti-6Al-4V, Other Ti Alloys | Plasma atomization |
Carpenter Additive | Ti-6Al-4V | Plasma atomization |
Sandvik | Ti6Al4V ELI, Ti6Al4V ELI-0406 | Plasma atomization |
Tekna | Ti-6Al-4V, Ti 6Al-7Nb | Plasma atomization |
TLS Technik | Ti6Al4V, Ti6Al4V ELI, Ti Grade 23 | Gas, plasma atomization |
Both established metal powder producers as well as specialized AM powder manufacturers provide these materials to demanding industry specifications.
Pricing of molybdenum titanium powders
As widely used materials in metal AM, published pricing indicators for molybdenum and titanium powders are available:
Molybdenum Powder
Particle Size | Price Range |
---|---|
10-45 μm | $40 – $60 per kg |
15-53 μm | $50 – $70 per kg |
Custom sizes | > $100 per kg |
Titanium Ti-6Al-4V Powder
Particle Size | Price Range |
---|---|
15-45 μm | $150 – $450 per kg |
45-100 μm | $100 – $350 per kg |
Custom sizes | > $500 per kg |
Prices depend on quality grade, lot size, distribution range, plasma vs gas atomization and purchase volume. Large quantity and contract pricing is usually negotiated directly with suppliers.
Pros and Cons of Molybdenum and Titanium Alloys from AM
Feature | Molybdenum Alloys (AM) | Titanium Alloys (AM) |
---|---|---|
Strength | Very high strength and creep resistance at elevated temperatures. Ideal for high-performance applications in aerospace and energy sectors. | Excellent strength-to-weight ratio. Lighter than steel but offers comparable strength, making them valuable in aerospace, automotive, and biomedical fields. |
Weight | Relatively dense compared to titanium, but still lighter than many other high-performance metals. | Significantly lighter than steel, offering substantial weight reduction benefits in applications where weight is critical. |
Corrosion Resistance | Generally good corrosion resistance, particularly in reducing environments. However, can be susceptible to oxidation at high temperatures. | Outstanding corrosion resistance in various environments, including seawater and human body fluids. A preferred material for marine applications and biomedical implants. |
Biocompatibility | Limited biocompatibility due to potential release of molybdenum ions in the body. Not ideal for most medical implants. | Excellent biocompatibility, making them well-suited for implants and prosthetics. |
High-Temperature Performance | Maintains strength and creep resistance at high temperatures, enabling use in hot sections of jet engines and other extreme environments. | Can maintain good mechanical properties at elevated temperatures, but not to the same extent as molybdenum alloys. |
Thermal Conductivity | Very good thermal conductivity, allowing for efficient heat dissipation in high-temperature applications. | Moderate thermal conductivity, lower than molybdenum but sufficient for many applications. |
Additive Manufacturing (AM) Printability | Molybdenum powder can be challenging to process due to its high melting point and reactivity. Requires specialized AM techniques like Electron Beam Melting (EBM). | More readily printable using various AM techniques like Selective Laser Melting (SLM) and Electron Beam Melting (EBM). Powder characteristics and printability can vary depending on the specific titanium alloy. |
Cost | Molybdenum is a relatively abundant element, but the AM process can be expensive due to specialized equipment and handling requirements. | Titanium itself is a more expensive element than molybdenum. However, advancements in AM technology are bringing down the cost of titanium parts. |
Surface Finish | AM-produced molybdenum parts can have a rough surface finish, requiring additional post-processing steps. | AM titanium parts can achieve a good surface finish depending on the specific AM process and parameters used. |
Applications | – High-temperature components in jet engines and rocket engines – Heat exchangers – Molybdenum crucibles for high-temperature melting processes | – Aerospace components (aircraft parts, landing gear) – Biomedical implants (knee replacements, hip joints) – Automotive parts (connecting rods, suspension components) – Sporting goods (golf clubs, bicycle frames) |
How are Molybdenum and Titanium Powders Made?
Advanced gas atomization processes manufacture the fine metallic powders with precise control over critical characteristics like particle shape, size range and chemical purity.
Gas Atomization
High purity ingots are induction melted in an inert atmosphere and the liquid metal stream poured into specialized atomization vessels. Powerful argon or nitrogen gas jets atomize the metal into fine droplets which rapidly solidify into powder.
By optimizing gas flow parameters and cooling rates, spherical particles with the desired particle size distribution are obtained. The powder is then sieved into different size classifications required for various AM processes.
Additional Processing
Further steps may be taken to enhance powder properties – degassing to lower oxygen levels, annealing to reduce internal stresses from rapid solidification, and blending with other powder fractions to obtain specific size ranges.
The powders are finally packaged under inert atmospheres to prevent oxidation before shipping to customers. Handling and storage protocols prevent moisture absorption or contamination during downstream metal AM processing.
Binder Jetting vs. Powder Bed Fusion of Molybdenum and Titanium
Molybdenum and titanium alloys can be printed using both binder jetting and powder bed fusion categories:
Aspect | Binder Jetting | Powder Bed Fusion |
---|---|---|
Build Method | Liquid binding agents | Laser/e-beam melting |
Resolution | ~100 μm | ~50 μm |
Porosity | Higher, requires infiltration | Lower, 99%+ density |
Surface Finish | Rough, needs machining | Moderate, may need finishing |
Mechanical Properties | Low, varies through part | Higher, more uniform |
Dimensional Accuracy | ±0.3% with shrinkage | ±0.1% or better |
Post-Processing | Debinding, sintering, HIP | Support removal, heat treatment |
Build Size | Industrial scale | Smaller chambers |
Time Requirements | Days | Hours up to 1-2 days |
Economics | Lower part cost, higher volume | Lower volume, expensive hardware |
Binder jetting is suitable for design concept models due to speed and low cost. Powder bed fusion creates high fidelity end use parts with superior properties.
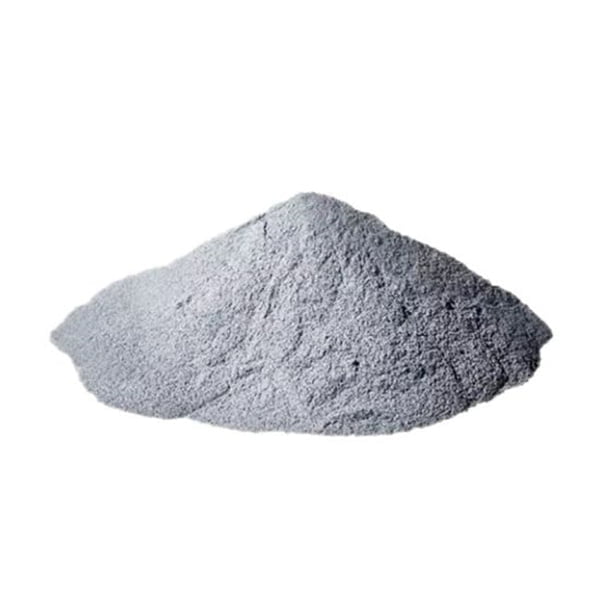
Molybdenum Titanium Alloys – Prospects
Feature | Description | Advantages | Potential Challenges |
---|---|---|---|
Superior Mechanical Properties | Molybdenum (Mo) strengthens titanium (Ti), creating alloys with exceptional strength-to-weight ratio, high creep resistance (resistance to deformation under stress at high temperatures), and good fatigue strength (resistance to failure under cyclic loading). | – Ideal for applications requiring lightweight yet robust components, particularly at elevated temperatures. – Enables efficient designs due to less material needed for the same level of strength compared to heavier alternatives. | – Molybdenum addition can reduce the alloy’s ductility (ability to deform plastically), potentially limiting its formability for complex shapes. – The processing of these alloys can be complex and require specialized techniques, potentially impacting cost-effectiveness. |
Enhanced High-Temperature Performance | Molybdenum’s high melting point elevates the maximum service temperature of Ti-Mo alloys compared to unalloyed titanium. | – Enables their use in environments with extreme heat, such as jet engines, rocket components, and high-performance furnaces. – Provides extended component lifespan in demanding thermal applications. | – Oxidation resistance, the ability to resist reacting with oxygen at high temperatures, can be a concern for some Ti-Mo alloys. Research is ongoing to improve their oxidation behavior through alloying additions or surface treatments. |
Electrical Conductivity Applications | Certain Ti-Mo alloys, particularly those with a higher Mo content, exhibit good electrical conductivity. | – Useful for applications requiring electrical current transmission, such as electrodes, electrical contacts, and high-power resistors. – Offers a potential material alternative to traditional conductors like copper in specific scenarios. | – The electrical conductivity of Ti-Mo alloys might not always match that of pure copper, requiring careful material selection based on the specific application’s needs. – Brittle behavior at low temperatures can limit their use in cryogenic applications. |
Emerging Additive Manufacturing Potential | The development of Ti-Mo alloy powders compatible with additive manufacturing techniques like 3D printing opens new possibilities for complex component design and lightweight structures. | – Enables creation of intricate geometries and lattice structures, potentially leading to weight reduction and improved performance. – Offers greater design freedom compared to traditional manufacturing methods. | – Powder production and printability optimization for Ti-Mo alloys are ongoing research areas. – Ensuring consistent material properties and quality control throughout the additive manufacturing process requires further development. |
Market Growth and Development | The global market for Ti-Mo alloys is projected to experience steady growth due to increasing demand in aerospace, biomedical, and energy sectors. | – Rising demand for lightweight and high-performance materials in these industries drives market expansion. – Technological advancements in processing and production methods can further improve cost-effectiveness and broaden application potential. | – Competition from established materials like aluminum and high-performance steels can limit market share in certain sectors. – Fluctuations in the prices of molybdenum and titanium can impact the overall cost of Ti-Mo alloys. |
FAQs
Q: What is molybdenum used for?
A: With excellent high temperature properties, molybdenum sees major use as an alloying addition to strengthen heat-resistant steels and superalloys used in aerospace, power generation, furnace construction, missile components among other demanding applications.
Q: Is molybdenum toxic?
A: Elemental molybdenum and its alloys generally have low toxicity levels and are safe for engineering use. However, some molybdenum compounds when inhaled over long durations may have potential carcinogenic effects warranting protective equipment use during handling and machining.
Q: Is titanium expensive?
A: Titanium alloys display a higher raw material cost compared to steels and aluminum alloys. However, with buy-to-fly ratios approaching 1 for AM manufacture, finished titanium part costs can be economical for industries like aerospace willing to adopt new technologies and designs.
Q: What makes titanium ideal for implants?
A: The biocompatibility of titanium alloys coupled with their high strength-to-weight ratio makes them ideal for replacing human bone. The modulus of elasticity can be reduced closer to that of bone by alloying with biocompatible beta stabilizers like Nb and Ta for improved life of load-bearing implants.
Q: Which 3D printing process is used for molybdenum and titanium?
A: For high-performance end-use parts, powder bed fusion techniques like selective laser melting (SLM) and electron beam melting (EBM) are predominantly used. The high temperature heat source achieves near full density builds with superior properties suited for engineering applications.
Q: Why blend molybdenum with titanium powder?
A: Molybdenum enhances high temperature hardness, creep resistance and tool steel-like properties while titanium contributes excellent corrosion resistance and low density attributes. Together, customized alloys made by directly blending their powders using AM provide the ideal combination for advanced applications.
Share On
MET3DP Technology Co., LTD is a leading provider of additive manufacturing solutions headquartered in Qingdao, China. Our company specializes in 3D printing equipment and high-performance metal powders for industrial applications.
Inquiry to get best price and customized Solution for your business!
Related Articles
About Met3DP
Recent Update
Our Product
CONTACT US
Any questions? Send us message now! We’ll serve your request with a whole team after receiving your message.
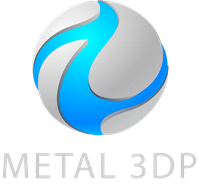
Metal Powders for 3D Printing and Additive Manufacturing