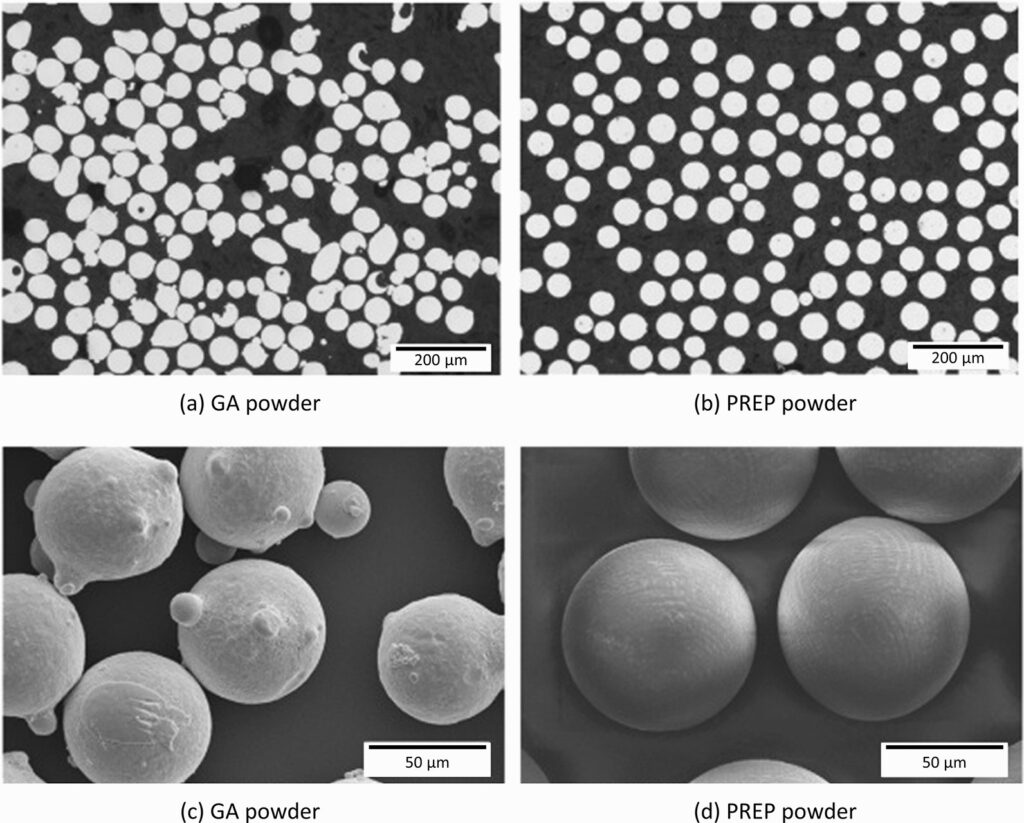
Ni55 Powder: The Alloy Leading the Way in Advanced Manufacturing
Low MOQ
Provide low minimum order quantity to meet different needs.
OEM & ODM
Provide customized products and design services to meet unique customer needs.
Adequate Stock
Ensure fast order processing and provide reliable and efficient service.
Customer Satisfaction
Provide high quality products with customer satisfaction at the core.
share this article
Table of Contents
When it comes to selecting the right material for high-performance applications, Ni55 powder is a name that stands out in the world of nickel-based alloys. Whether you’re involved in aerospace, automotive, oil and gas, or additive manufacturing, Ni55 powder offers a remarkable combination of strength, thermal stability, and corrosion resistance.
In this comprehensive guide, we’ll break down everything you need to know about Ni55 powder. From its composition to its applications and pricing, this article will give you a clear understanding of how this material can be the solution you’ve been looking for. We’ll even compare Ni55 to other alloys to help you make the best decision for your project.
Overview of Ni55 Powder
Ni55 powder is a nickel alloy that contains approximately 55% nickel, with the remaining percentage made up of elements like chromium, iron, manganese, and silicon. The combination of these elements gives Ni55 powder an impressive set of properties, including high-temperature stability, corrosion resistance, and excellent mechanical strength.
Because of these properties, Ni55 powder is used across a variety of industries where durability and resistance to harsh conditions are required. It’s used in high-stress environments such as gas turbines, automotive components, and chemical processing equipment.
Key Features :
- High Nickel Content: Provides excellent corrosion resistance and thermal stability.
- Versatile Applications: Suitable for industries like aerospace, automotive, chemical processing, and additive manufacturing.
- High-Temperature Strength: Performs well in extreme heat and oxidizing environments.
- Corrosion Resistance: Ideal for use in chloride-rich, acidic, and oxidizing atmospheres.
- Wear Resistance: Can withstand abrasion and creep in high-stress environments.
Composition and Properties of Ni55 Powder
The specific chemical composition of Ni55 powder is what makes it such a high-performing material. By combining nickel with other elements like chromium, manganese, and iron, this alloy can resist corrosion and oxidation while maintaining mechanical strength at high temperatures.
Chemical Composition
Element | Weight Percentage (%) | Primary Function |
---|---|---|
Nickel (Ni) | 54.00 – 55.00 | Provides the base, ensuring oxidation resistance and thermal performance. |
Chromium (Cr) | 15.00 – 18.00 | Adds corrosion resistance, especially in oxidizing environments. |
Iron (Fe) | 6.00 – 9.00 | Enhances mechanical strength and provides additional ductility. |
Manganese (Mn) | 0.50 – 2.00 | Improves impact resistance and helps in deoxidation during alloy production. |
Silicon (Si) | 0.50 – 1.50 | Increases oxidation resistance and improves hot-forming properties. |
Carbon (C) | 0.08 max | Improves hardness and wear resistance, but excessive amounts can negatively impact ductility. |
This blend of elements ensures that Ni55 powder can withstand high temperatures and corrosive environments, making it the perfect choice for industries that demand materials with long-lasting performance.
Mechanical and Thermal Properties
The mechanical and thermal properties of Ni55 powder are what make it such a sought-after material in high-stress applications. Here’s a breakdown of its most important properties:
Property | Value |
---|---|
Density | 8.4 g/cm³ |
Melting Point | 1350°C – 1400°C |
Ultimate Tensile Strength | 800-950 MPa |
Yield Strength (0.2% Offset) | 450-600 MPa |
Elongation at Break | 25-35% |
Thermal Conductivity | 12.0 W/m·K |
Oxidation Resistance | Effective up to 1100°C in oxidizing atmospheres. |
Corrosion Resistance | Excellent in acidic, oxidizing, and chloride-rich environments. |
Why These Properties Matter
These properties mean that Ni55 powder can handle extreme heat, pressure, and corrosive atmospheres without losing its mechanical integrity. Whether it’s being used in jet engines, automotive components, or chemical reactors, Ni55 powder’s thermal stability and strength make it a versatile and reliable material for demanding applications.
Applications of Ni55 Powder
Because of its high nickel content, corrosion resistance, and thermal stability, Ni55 powder is used in a wide range of industries. From aerospace to chemical processing to additive manufacturing, this alloy is favored for its ability to perform in harsh environments.
Common Applications
Industry | Application |
---|---|
Aerospace | Used in turbine blades, combustion chambers, and exhaust systems for high-temperature stability. |
Automotive | Ideal for turbochargers, exhaust manifolds, and valve seats that endure high heat and corrosive gases. |
Chemical Processing | Applied in reactors, heat exchangers, and piping systems that handle corrosive chemicals and high pressures. |
Power Generation | Suitable for components in gas turbines, boilers, and high-temperature furnace parts. |
Oil & Gas | Utilized in downhole drilling tools, valves, and pipes for corrosion resistance in harsh environments. |
Additive Manufacturing | Used to 3D print high-performance parts for aerospace, automotive, and industrial equipment. |
Thermal Spray Coatings | Applied as a protective coating on boilers, turbines, and chemical processing equipment for enhanced wear and corrosion resistance. |
Ni55 Powder in Aerospace Applications
In the aerospace industry, materials need to be able to withstand extreme temperatures while maintaining their mechanical strength. Ni55 powder is often used in turbine blades, combustion chambers, and exhaust systems because of its ability to resist oxidation and maintain its properties in high-heat environments.
Ni55 Powder in Automotive Applications
In the automotive industry, Ni55 powder is used in turbochargers, exhaust manifolds, and engine components that are subjected to high temperatures and corrosive gases. The alloy’s ability to resist oxidation and thermal cycling makes it ideal for components that need to perform reliably over long periods of time.
Specifications, Sizes, and Standards for Ni55 Powder
When choosing Ni55 powder for your application, it’s important to understand the specifications, sizes, and standards that are available. This ensures that you’re selecting the right form of the alloy for your specific needs, whether you’re using it for additive manufacturing, thermal spraying, or high-strength components.
Specifications and Standards
Specification/Standard | Details |
---|---|
UNS Number | N05500 |
ASTM Standards | ASTM B127 (Nickel Alloy Sheet), ASTM B163 (Seamless Nickel Alloy Tubes), ASTM F3055 (Additive Manufacturing) |
AMS Standards | AMS 4676 (Nickel Alloy Bars, Forgings, and Rings) |
ISO Standards | ISO 15156-3 (Materials for sour gas environments) |
Powder Particle Size | Typically ranges from 15 to 45 microns, depending on the application (e.g., 3D printing, thermal spray). |
Density | 8.4 g/cm³ |
Melting Range | 1350°C – 1400°C |
By selecting the correct specifications and standards, you can ensure that Ni55 powder will perform optimally in your specific application. Whether you’re using it for additive manufacturing, thermal spray coatings, or high-performance industrial components, adhering to these standards is essential.
Available Sizes and Forms
Form | Available Sizes |
---|---|
Powder | Particle sizes typically range from 15 to 45 microns, ideal for additive manufacturing, thermal spraying, and powder metallurgy. |
Bars/Rods | Diameters from 0.5 inches to 3 inches, used for structural components and fasteners. |
Sheets/Plates | Thicknesses from 1 mm to 50 mm, commonly used in reactor parts and piping systems. |
Choosing the right form and size of Ni55 powder is critical for ensuring that the material performs as expected in your application. For example, powder particle size is particularly important when using Ni55 in 3D printing or thermal spray coatings.
Suppliers and Pricing of Ni55 Powder
Finding the right supplier for Ni55 powder can make a significant impact on both the quality and cost of your project. Pricing can vary based on factors like particle size, order volume, and supplier location.
Suppliers and Pricing
Supplier | Price Range (per kg) | Notes |
---|---|---|
Höganäs AB | $200 – $320 | Specializes in metal powders for additive manufacturing, thermal spray, and powder metallurgy. |
Sandvik Materials | $210 – $330 | Offers high-quality powders for aerospace and industrial applications. |
Oerlikon Metco | $220 – $340 | Known for premium powders used in thermal spraying and laser cladding. |
Carpenter Technology | $215 – $325 | Supplies nickel alloys for aerospace, automotive, and oil & gas industries. |
The cost of Ni55 powder typically ranges from $200 to $340 per kilogram, depending on the supplier, particle size, and order volume. It’s important to consider both quality and price when selecting a supplier to ensure that the material is up to the standards required for your specific application.
Advantages and Limitations of Ni55 Powder
Like any material, Ni55 powder has both advantages and limitations. Understanding these can help you decide whether this alloy is suitable for your specific needs.
Advantages
Advantage | Description |
---|---|
High-Temperature Strength: Retains mechanical strength at temperatures up to 1100°C. | Ideal for aerospace, automotive, and industrial applications. |
Corrosion Resistance: Performs exceptionally well in oxidizing and chloride-rich environments. | Perfect for use in chemical processing and oil & gas industries. |
Thermal Stability: Can withstand thermal cycling and high-heat environments. | Ensures long service life in demanding conditions. |
Versatility: Suitable for a wide range of industries, including additive manufacturing and thermal spraying. | Allows for customized components in 3D printing and coatings. |
Limitations
Limitation | Description |
---|---|
Cost: More expensive than many other nickel alloys and stainless steels. | May not be suitable for cost-sensitive projects. |
Density: Heavier than some other materials like aluminum or titanium. | Not ideal for applications where weight is a critical factor. |
Machinability: Can be challenging to machine due to its hardness and toughness. | Requires specialized machining techniques, which may increase manufacturing time and cost. |
Ni55 Powder vs. Other Nickel-Based Alloys
When selecting a material for your project, it’s often helpful to compare Ni55 powder to other commonly used nickel-based alloys. Below, we’ll compare Ni55 to several other high-performance alloys, highlighting their strengths and weaknesses.
Alloy | Strengths | Limitations |
---|---|---|
Ni55 Powder | Excellent oxidation resistance, high strength at elevated temperatures, superior corrosion resistance. | Higher cost, more challenging to machine. |
Inconel 625 | Outstanding corrosion resistance in aqueous and acidic environments. | Lower yield strength compared to Ni55 at elevated temperatures. |
Hastelloy C276 | Exceptional corrosion resistance in chloride and acidic environments. | Lower mechanical strength at high temperatures. |
Stainless Steel 316 | Lower cost, good general corrosion resistance. | Poor high-temperature performance compared to Ni55. |
Frequently Asked Questions (FAQs)
To help clear up any lingering questions you might have about Ni55 powder, here’s a detailed FAQ section to guide you further.
Question | Answer |
---|---|
What is Ni55 powder used for? | It is used in industries like aerospace, automotive, chemical processing, and power generation for high-temperature, corrosion-resistant components. |
How much does Ni55 powder cost? | Prices typically range from $200 to $340 per kilogram, depending on the supplier, particle size, and order volume. |
Can Ni55 powder be used in 3D printing? | Yes, it is suitable for additive manufacturing and is often used to 3D print high-strength, corrosion-resistant parts. |
What industries use Ni55 powder? | Industries such as aerospace, automotive, oil & gas, and chemical processing extensively use Ni55 powder for its thermal and corrosion resistance. |
Is Ni55 powder weldable? | Yes, it can be welded, but it requires specialized techniques due to its high melting point and hardness. |
How does Ni55 powder compare to Inconel 625? | Both are nickel-based alloys, but it offers superior thermal stability at elevated temperatures, while Inconel 625 is better in aqueous environments. |
Conclusion: Why Ni55 Powder is the Ideal Choice for High-Performance Applications
In conclusion, Ni55 powder is a top-tier material for industries that require high-temperature performance, corrosion resistance, and mechanical strength. Its unique combination of nickel, chromium, and manganese ensures that it can withstand the harshest of environments, making it a reliable choice for aerospace, automotive, chemical processing, and additive manufacturing applications.
While Ni55 powder may come at a higher cost compared to other nickel alloys, its durability, thermal stability, and corrosion resistance make it a cost-effective solution over the long term for critical applications. Whether you’re using it to print high-strength 3D components or applying it as a thermal spray coating, Ni55 powder is a material that delivers exceptional performance in the most demanding environments.
Get Latest Price
About Met3DP
Product Category
HOT SALE
CONTACT US
Any questions? Send us message now! We’ll serve your request with a whole team after receiving your message.
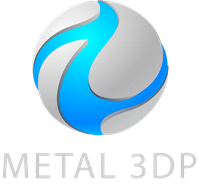
Metal Powders for 3D Printing and Additive Manufacturing