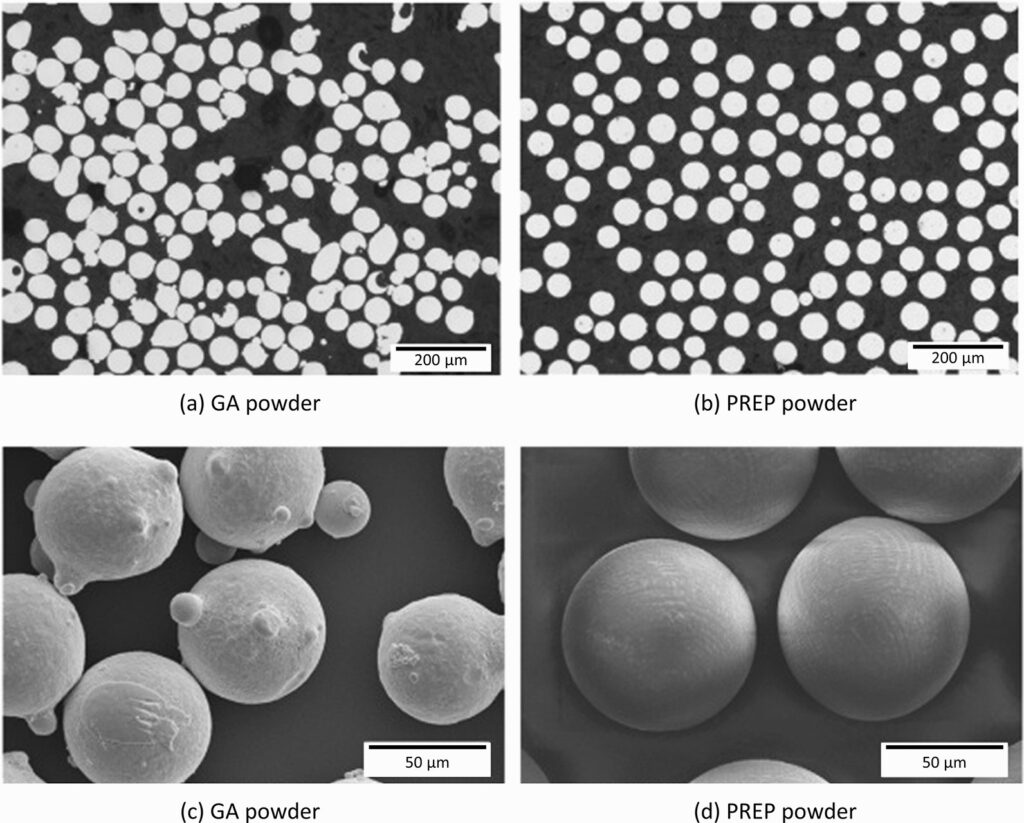
Ni65 Powder: Why It’s the Best Choice for Harsh Conditions
Low MOQ
Provide low minimum order quantity to meet different needs.
OEM & ODM
Provide customized products and design services to meet unique customer needs.
Adequate Stock
Ensure fast order processing and provide reliable and efficient service.
Customer Satisfaction
Provide high quality products with customer satisfaction at the core.
share this article
Table of Contents
Are you on the hunt for an alloy that offers outstanding wear resistance, high-temperature performance, and excellent corrosion protection? Look no further than Ni65 powder. This nickel-based alloy is quickly becoming the go-to material for industries that demand durability, strength, and resilience.
In this comprehensive guide, we’ll uncover everything you need to know about Ni65 powder. We’ll dive into its composition, properties, and uses across various industries. Whether you’re a materials engineer, an industrial buyer, or just someone curious about cutting-edge alloys, this guide has got you covered. Let’s get into the details!
Overview of Ni65 Powder
Ni65 powder, as the name suggests, is a nickel-based alloy with 65% nickel content. This alloy is prized for its excellent mechanical strength, oxidation resistance, and its ability to perform at high temperatures. It is commonly used in industries like aerospace, automotive, thermal spraying, and powder metallurgy for coating, welding, and additive manufacturing.
One of the standout features of Ni65 powder is its self-fluxing behavior, which enables it to form dense, durable coatings when applied to surfaces. This makes it perfect for hard-facing applications, where components need to resist abrasion and corrosion in harsh environments.
Key Features :
- High Nickel Content: Ensures oxidation resistance and thermal stability in extreme conditions.
- Wear Resistance: Excellent for applications that demand abrasion resistance and durability.
- High Hardness: Achieves superior hardness after heat treatment, extending component life.
- Self-Fluxing: Forms a strong, protective layer when applied, ideal for thermal spraying and coating.
- Corrosion Resistance: Performs well in corrosive environments, making it reliable for chemical processing and oil & gas applications.
Composition and Properties of Ni65 Powder
The chemical composition of Ni65 powder is what makes it an exceptional material. The combination of nickel, chromium, silicon, boron, and other elements gives it its mechanical strength, wear resistance, and oxidation stability.
Chemical Composition
Element | Weight Percentage (%) | Primary Function |
---|---|---|
Nickel (Ni) | 63.00 – 67.00 | Provides the base, ensuring thermal stability and oxidation resistance. |
Chromium (Cr) | 13.00 – 16.00 | Enhances wear resistance and oxidation protection. |
Silicon (Si) | 3.00 – 5.00 | Improves oxidation resistance and contributes to the alloy’s self-fluxing ability. |
Boron (B) | 2.00 – 4.00 | Lowers the melting point, aiding in the formation of a dense, smooth coating. |
Carbon (C) | 0.50 – 1.00 | Adds hardness and resistance to wear. |
Iron (Fe) | 3.00 max | Provides additional strength while maintaining ductility. |
The high nickel and chromium content gives Ni65 powder its excellent corrosion resistance, while silicon and boron ensure the alloy has self-fluxing properties, making it perfect for thermal spraying and fusion welding.
Mechanical and Thermal Properties
Property | Value |
---|---|
Density | 8.3 g/cm³ |
Melting Point | 950°C – 1050°C |
Hardness (as sprayed) | 45-65 HRC |
Ultimate Tensile Strength | 700-900 MPa |
Thermal Conductivity | 12.5 W/m·K |
Oxidation Resistance | Effective up to 850°C in oxidizing atmospheres. |
Wear Resistance | Excellent in abrasive environments, especially at high temperatures. |
Why These Properties Matter
The combination of high hardness, thermal stability, and abrasion resistance makes Ni65 powder ideal for applications where materials must maintain their mechanical integrity under extreme conditions. Whether used for thermal spray coatings or welding consumables, Ni65 powder’s ability to resist wear, corrosion, and oxidation ensures a long service life for critical components.
Applications of Ni65 Powder
Ni65 powder is used in a wide range of industries due to its outstanding properties. From aerospace to oil & gas, it offers wear resistance, corrosion protection, and thermal stability in demanding environments.
Key Applications
Industry | Application |
---|---|
Aerospace | Used in thermal spraying for engine components, exhaust systems, and high-stress parts. |
Automotive | Ideal for hard-facing parts like valve seats, camshafts, and bearings. |
Oil & Gas | Applied to drill bits, valves, and tubing to resist corrosion and wear. |
Power Generation | Used in boilers, turbines, and furnace parts to withstand high heat and abrasion. |
Additive Manufacturing | Utilized for 3D printing high-performance components with wear and heat resistance. |
Thermal Spray Coatings | Applied to protect surfaces exposed to high wear, oxidation, and thermal stress. |
Ni65 Powder in Aerospace Applications
In the aerospace industry, components like engine parts and exhaust systems must handle high temperatures and abrasion. Ni65 powder is often used in thermal spraying to coat these parts, ensuring their performance and longevity in extreme environments.
Ni65 Powder in Automotive Applications
For the automotive industry, Ni65 powder plays a vital role in hard-facing components such as valve seats, camshafts, and gears. These parts experience significant wear, and Ni65’s high hardness and wear resistance extend their operational lifespan, reducing the need for frequent replacements.
Specifications, Sizes, and Standards for Ni65 Powder
When choosing Ni65 powder for an application, it’s important to be aware of the specifications, sizes, and standards that apply. These factors ensure the material is used optimally for your specific needs, whether for thermal spraying, welding, or additive manufacturing.
Specifications and Standards
Specification/Standard | Details |
---|---|
UNS Number | N06650 |
ASTM Standards | ASTM B50 (Nickel-Chromium Alloy Wires), ASTM F3055 (Additive Manufacturing) |
AMS Standards | AMS 4777 (Nickel Alloy Welding Rods) |
ISO Standards | ISO 15156-3 (Materials for sour gas environments) |
Powder Particle Size | Typically ranges from 15 to 45 microns, depending on the application (e.g., thermal spraying or 3D printing). |
Density | 8.3 g/cm³ |
Melting Range | 950°C – 1050°C |
By adhering to these standards and choosing the appropriate specifications, you can ensure that Ni65 powder will perform effectively in your applications. For example, selecting the correct particle size is critical for achieving the desired results in thermal spray coatings or additive manufacturing.
Available Forms and Sizes
Form | Available Sizes |
---|---|
Powder | Particle sizes typically range from 15 to 45 microns, ideal for additive manufacturing and thermal spraying. |
Welding Rods/Wires | Diameters from 1 mm to 3 mm, used for welding and hard-facing. |
Selecting the correct form and size of Ni65 powder is essential to ensure optimal performance. For instance, choosing the right particle size for 3D printing ensures proper layer bonding and material consistency in additive manufacturing applications.
Suppliers and Pricing of Ni65 Powder
When sourcing Ni65 powder, it’s important to consider quality, availability, and price. The cost of Ni65 powder can vary based on particle size, order volume, and supplier location.
Suppliers and Pricing
Supplier | Price Range (per kg) | Notes |
---|---|---|
Höganäs AB | $190 – $320 | Known for high-performance powders used in thermal spray and additive manufacturing. |
Oerlikon Metco | $210 – $330 | Specializes in nickel alloys for thermal spraying and laser cladding. |
Kennametal Stellite | $200 – $310 | Offers premium powders for hard-facing and wear-resistant applications. |
Carpenter Technology | $205 – $315 | Supplies nickel alloys for aerospace, automotive, and industrial applications. |
The price of Ni65 powder typically ranges from $190 to $330 per kilogram, depending on the supplier and particle size. Bulk orders often come with discounts, and some suppliers may offer custom particle size distributions based on the specific needs of your application.
Advantages and Limitations of Ni65 Powder
No material is perfect. While Ni65 powder offers exceptional properties, it also has its limitations. Understanding these will help you make the right decision for your project.
Advantages
Advantage | Description |
---|---|
Wear Resistance: Outstanding wear resistance in abrasive environments. | Ideal for hard-facing and other high-wear applications. |
Corrosion Resistance: Performs well in oxidizing and corrosive environments. | Suitable for chemical processing and oil & gas applications. |
Thermal Stability: Can withstand high temperatures without losing strength or hardness. | Perfect for aerospace and power generation industries. |
Self-Fluxing: The alloy’s ability to form a dense, hard layer when applied makes it ideal for thermal spraying. | Ensures long-lasting coatings in abrasive environments. |
Limitations
Limitation | Description |
---|---|
Cost: More expensive than other nickel alloys and stainless steel. | Could be a limiting factor for cost-sensitive projects. |
Brittleness: Can become brittle if not heat-treated properly. | Requires careful handling during processing and application. |
Machinability: Difficult to machine due to its high hardness. | Specialized machining techniques and tools may be required, increasing overall production costs. |
Ni65 Powder vs. Other Nickel-Based Alloys
When selecting a nickel-based alloy, it’s essential to compare your options to find the best fit for your application. Let’s see how Ni65 powder stacks up against other popular nickel alloys.
Alloy | Strengths | Limitations |
---|---|---|
Ni65 Powder | Excellent wear resistance, high hardness, good oxidation resistance. | More expensive and harder to machine. |
Inconel 625 | Outstanding corrosion resistance in aqueous and acidic environments. | Lower hardness and wear resistance. |
Hastelloy C276 | Exceptional corrosion resistance in chloride and acidic environments. | Lower mechanical strength at high temperatures. |
Stellite 6 | Great for wear resistance and corrosion protection, especially in welding. | Higher cost and limited availability. |
As you can see, Ni65 powder is an excellent choice for applications that require wear resistance and thermal stability, while other alloys like Inconel 625 or Hastelloy C276 might be better suited for corrosive environments.
Frequently Asked Questions (FAQs)
Still curious about Ni65 powder? Here are some of the most frequently asked questions about this versatile material.
Question | Answer |
---|---|
What is Ni65 powder used for? | It is used in industries like aerospace, automotive, oil & gas, and power generation for applications requiring wear resistance and thermal stability. |
How much does Ni65 powder cost? | Prices usually range from $190 to $330 per kilogram, depending on supplier, particle size, and order volume. |
Can Ni65 powder be used in 3D printing? | Yes, it is suitable for additive manufacturing and is commonly used to 3D print components that require wear resistance and heat stability. |
What industries use Ni65 powder? | Industries like aerospace, automotive, oil & gas, and power generation extensively use Ni65 powder for its high wear resistance and oxidation stability. |
Is Ni65 powder weldable? | Yes, it is often used in welding applications, especially for hard-facing components that require high wear resistance. |
How does Ni65 powder compare to Inconel 625? | While both are nickel-based alloys, Ni65 offers superior hardness and wear resistance, making it ideal for abrasive environments, whereas Inconel 625 excels in corrosive, aqueous environments. |
Conclusion: Why Ni65 Powder is the Ultimate Choice for Wear-Resistant Applications
If you’re looking for a material that offers unmatched wear resistance, thermal stability, and oxidation resistance, it is your best bet. Its high hardness, self-fluxing properties, and corrosion resistance make it ideal for demanding applications across industries like aerospace, automotive, oil & gas, and power generation.
While it may be more expensive than other nickel-based alloys, the extended lifespan and durability of components made with Ni65 powder often justify the cost. Whether you’re looking to extend the life of wear-prone parts or create new components with superior performance, Ni65 powder delivers exceptional value and reliability.
So, why settle for less when you can have the best? Choose Ni65 powder for your next project and experience the difference in performance, durability, and quality.
Get Latest Price
About Met3DP
Product Category
HOT SALE
CONTACT US
Any questions? Send us message now! We’ll serve your request with a whole team after receiving your message.
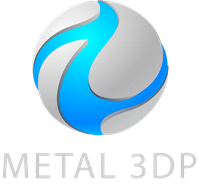
Metal Powders for 3D Printing and Additive Manufacturing