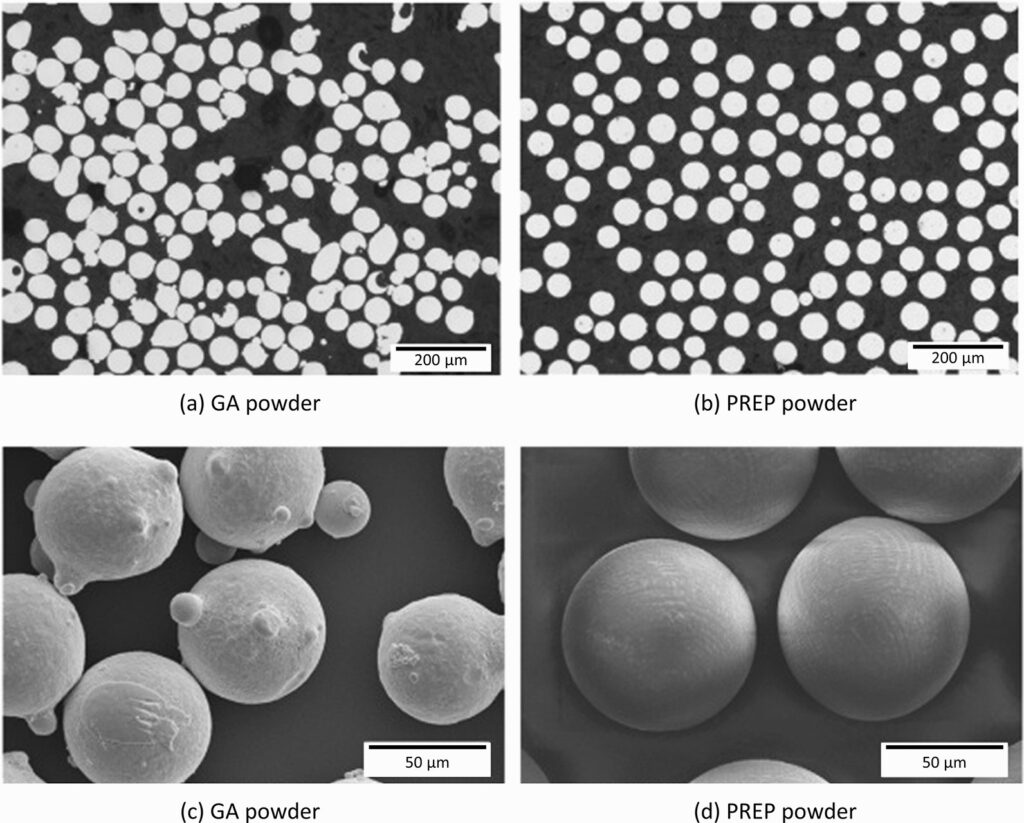
NiCrPSi Powder: The Durable, High-Performance Coating You Need
Low MOQ
Provide low minimum order quantity to meet different needs.
OEM & ODM
Provide customized products and design services to meet unique customer needs.
Adequate Stock
Ensure fast order processing and provide reliable and efficient service.
Customer Satisfaction
Provide high quality products with customer satisfaction at the core.
share this article
Table of Contents
In the world of industrial coatings and high-performance applications, NiCrPSi powder is a standout material. Known for its exceptional corrosion resistance, high-temperature stability, and wear resistance, this alloy powder plays a critical role in industries ranging from aerospace to power generation. But what exactly is NiCrPSi powder? How is it used, and why is it so essential in today’s demanding industrial environments?
In this extensive guide, we’ll take a deep dive into NiCrPSi powder, exploring its composition, properties, applications, and much more. Along the way, we’ll break down technical details into easy-to-understand explanations, answer common questions, and provide insights on where to buy NiCrPSi powder. Whether you’re an engineer, a materials scientist, or simply curious, this guide will give you all the information you need.
Overview
NiCrPSi powder is a type of nickel-based alloy containing chromium, phosphorus, and silicon. Each element contributes uniquely to the powder’s performance. Nickel provides the base and offers corrosion resistance, chromium adds oxidation resistance, phosphorus improves flowability during thermal spraying, and silicon helps with wetting and bonding.
One of the standout characteristics of NiCrPSi powder is its ability to form self-fluxing coatings. This means that when applied using thermal spray techniques such as plasma spraying or HVOF (High-Velocity Oxygen Fuel), the powder melts and creates a smooth, uniform coating that seals and protects the underlying material from wear and corrosion.
Key Benefits
- High corrosion and oxidation resistance: Ideal for harsh environments.
- Excellent wear resistance: Protects surfaces from friction-related damage.
- Self-fluxing properties: Creates strong, smooth coatings that don’t require additional flux.
- Versatile in various industries: Used widely in aerospace, oil & gas, and power generation.
Now, let’s break down the composition and properties in more detail.
NiCrPSi Powder Composition and Properties
The composition of NiCrPSi powder plays a crucial role in its performance. Each element is selected to optimize the powder for specific applications, offering durability, resistance to extreme conditions, and ease of application.
Detailed Composition
Element | Weight Percentage (%) | Function |
---|---|---|
Nickel (Ni) | 75 – 80% | Base element providing corrosion resistance and high-temperature stability. |
Chromium (Cr) | 10 – 15% | Adds oxidation resistance and improves strength at elevated temperatures. |
Phosphorus (P) | 2 – 4% | Lowers the melting point and enhances flowability during thermal spraying. |
Silicon (Si) | 2 – 4% | Improves wetting properties and bonding strength of the coating. |
Key Properties
Property | Value/Description |
---|---|
Melting Point | 950°C – 1050°C |
Density | 7.9 g/cm³ |
Corrosion Resistance | Excellent in aqueous and oxidizing environments. |
Bond Strength | High bond strength, particularly on steel and cast iron. |
Hardness | 40-65 HRC (depending on the method of application and heat treatment). |
Wear Resistance | High resistance to abrasion and erosion. |
Thermal Expansion | Coefficient matches well with steel and nickel alloys, reducing stress during thermal cycling. |
Why NiCrPSi Powder Stands Out
NiCrPSi powder’s unique blend of nickel, chromium, phosphorus, and silicon allows it to offer a combination of high-temperature resistance, corrosion resistance, and wear protection that few other powders can match. The addition of phosphorus and silicon also ensures that the powder flows well during application, forming dense, defect-free coatings that protect equipment and components from the harshest conditions.
Applications
Thanks to its excellent corrosion resistance, wear protection, and self-fluxing properties, NiCrPSi powder is used in a wide array of industries. From protecting aircraft engine parts to extending the life of industrial machinery, this powder plays a crucial role in ensuring the longevity and performance of critical components.
Common Applications
Industry | Typical Applications |
---|---|
Aerospace | Coating of turbine blades, engine components, and exhaust systems. |
Oil & Gas | Protection of pipes, valves, and drilling equipment from corrosion and abrasion. |
Power Generation | Coating of boiler tubes, turbine blades, and heat exchangers. |
Automotive | Coating of exhaust manifolds, turbochargers, and cylinder liners. |
Mining | Wear-resistant coatings for mining equipment, crusher parts, and drill bits. |
Marine | Corrosion-resistant coatings for propellers, rudders, and marine hardware. |
Why NiCrPSi Powder Is Popular in Aerospace and Power Generation
In industries like aerospace and power generation, components are often exposed to high temperatures, oxidizing environments, and mechanical wear. NiCrPSi powder’s ability to form dense, wear-resistant coatings makes it an ideal choice for protecting critical parts like turbine blades and heat exchangers. These coatings extend the life of equipment, reduce downtime, and improve overall efficiency.
Specifications, Sizes, and Standards
To achieve optimal results in your thermal spray or brazing applications, it’s essential to choose the right specifications and grades of NiCrPSi powder. Below, we’ll outline the most common sizes and standards associated with this versatile material.
Specifications and Standards
Specification/Standard | Details |
---|---|
AWS A5.21 | Classified under thermal spraying materials. |
UNS Number | N07050 |
ISO Standards | ISO 14919:2015 for thermal spraying powders. |
Particle Size | Available in 15 to 45 microns (fine powders) and 45 to 150 microns (coarse powders). |
Density | 7.9 g/cm³ |
Hardness | 40-65 HRC (depending on application and heat treatment). |
Available Forms and Sizes
NiCrPSi powder is available in various forms to suit different thermal spray and brazing techniques. Here are the most common forms and sizes:
Form | Available Sizes |
---|---|
Powder | Particle sizes typically range from 15 to 150 microns, depending on the application. |
Wire | Available in wire form for use in arc spraying and flame spraying processes. |
Rod | Available for hard-facing and thermal spray applications. |
NiCrPSi Powder Price and Suppliers
Pricing for NiCrPSi powder can vary based on factors such as particle size, quantity, and supplier reputation. In this section, we’ll provide an overview of pricing trends and some of the top suppliers you can turn to for purchasing NiCrPSi powder.
Suppliers and Pricing
Supplier | Price Range (per kg) | Notes |
---|---|---|
Praxair | $250 – $400 | Known for high-quality thermal spray powders for aerospace and power generation industries. |
Oerlikon Metco | $300 – $450 | Offers a wide range of NiCrPSi powders for both thermal spraying and brazing applications. |
Höganäs AB | $290 – $420 | Specializes in metal powders for surface engineering and thermal spraying. |
Kennametal | $270 – $400 | Provides NiCrPSi powders for industrial applications such as oil & gas and mining. |
Wall Colmonoy | $260 – $410 | Supplies a variety of nickel-based alloy powders, including NiCrPSi for high-temperature coatings. |
Factors that Affect the Price
The price of NiCrPSi powder can vary based on several factors:
- Particle Size: Finer powders often cost more due to the additional processing required.
- Supplier Reputation: Established suppliers with strict quality controls may charge more.
- Quantity: Bulk purchases often come at a discounted rate.
On average, NiCrPSi powder costs between $250 and $450 per kilogram, depending on the form and supplier.
Advantages and Limitations
Like any material, NiCrPSi powder comes with its own set of advantages and limitations. Let’s break them down to understand why this powder excels in certain applications while being less suitable for others.
Advantages
Advantage | Description |
---|---|
High Wear Resistance: Protects equipment from abrasion and erosion. | Extends the life of components exposed to high-friction environments. |
Corrosion Resistance: Withstands oxidizing environments exceptionally well. | Ideal for industries like aerospace, oil & gas, and marine. |
Self-Fluxing: Creates dense, smooth coatings without the need for additional flux. | Reduces the risk of coating defects and ensures uniform protection. |
High Bond Strength: Forms strong bonds with a variety of base materials, including steel. | Ensures coatings remain intact even in high-stress environments. |
Versatile Application: Suitable for thermal spraying, brazing, and hard-facing. | Can be used across a wide range of industries and applications. |
Limitations
Limitation | Description |
---|---|
Cost: NiCrPSi powder tends to be more expensive than other nickel-based powders. | May not be the best choice for budget-sensitive projects. |
Requires Specialized Equipment: Application methods like plasma spraying and HVOF require specialized equipment. | Not ideal for small-scale or low-budget operations. |
Limited Strength at Extreme Temperatures: While it performs well in most conditions, it may not be the best choice for ultra-high-temperature applications. | Consider other alloys like Inconel for extreme environments. |
NiCrPSi Powder vs. Other Nickel-Based Powders
When selecting a nickel-based powder for your project, it’s essential to consider how NiCrPSi powder stacks up against other options. Let’s compare it to some other widely used nickel-based powders in terms of strength, flowability, corrosion resistance, and cost.
Comparing NiCrPSi Powder to Other Nickel-Based Powders
Alloy | Strengths | Limitations |
---|---|---|
NiCrBSi Powder | Higher bond strength and wear resistance. | Slightly higher melting point, may require hotter processes. |
Inconel 625 | Excellent for high-temperature applications. | Less suitable for corrosion resistance in aqueous environments than NiCrPSi. |
NiCrMo Powder | Superior performance in highly corrosive environments. | More expensive and less wear resistant than NiCrPSi. |
NiAl Powder | Best suited for oxidation resistance at high temperatures. | Lower wear resistance compared to NiCrPSi. |
NiCrPSi powder offers a balanced mix of corrosion resistance, wear protection, and flowability, making it an excellent choice for most thermal spray and brazing applications. However, if your project involves extreme temperatures or requires superior corrosion resistance in specialty environments, alternatives like Inconel or NiCrMo might be worth considering.
Frequently Asked Questions (FAQs)
Still have questions about NiCrPSi powder? Let’s answer some of the most commonly asked questions to help clear things up.
Question | Answer |
---|---|
What is NiCrPSi powder used for? | It is used for thermal spraying and brazing in industries like aerospace, oil & gas, and power generation. |
What is the melting point of NiCrPSi powder? | NiCrPSi powder has a melting point range of 950°C to 1050°C. |
How much does NiCrPSi powder cost? | Prices typically range from $250 to $450 per kilogram, depending on the supplier and particle size. |
Can NiCrPSi powder be used for thermal spray applications? | Yes, NiCrPSi powder is widely used in thermal spraying techniques like HVOF and plasma spray. |
What industries most commonly use NiCrPSi powder? | The aerospace, oil & gas, power generation, and marine industries are the biggest users of NiCrPSi powder. |
What are the key properties of NiCrPSi powder? | Corrosion resistance, wear resistance, self-fluxing properties, and high bond strength. |
Conclusion: Why NiCrPSi Powder is a Top Choice for High-Performance Applications
In summary, NiCrPSi powder is a versatile, high-performance material that offers exceptional corrosion resistance, wear protection, and self-fluxing properties. Its ability to form durable, smooth coatings makes it a top choice for industries like aerospace, oil & gas, and power generation, where equipment and components are exposed to harsh environments.
While it may come at a higher price point compared to other materials, the longevity and protection it provides make it well worth the investment for critical applications. Whether you’re looking to coat turbine blades, valve components, or thermal shields, NiCrPSi powder delivers the performance and reliability you need.
If you’re ready to take your coatings and brazing applications to the next level, NiCrPSi powder is an excellent choice to consider.
Get Latest Price
About Met3DP
Product Category
HOT SALE
CONTACT US
Any questions? Send us message now! We’ll serve your request with a whole team after receiving your message.
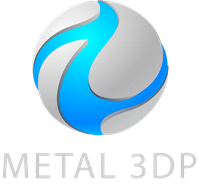
Metal Powders for 3D Printing and Additive Manufacturing