PREP-ared Powders
Table of Contents
The world of materials science is brimming with fascinating innovations, and PREP-prepared powders are a prime example. But what exactly are they, and why are they causing a stir in various industries? Buckle up, because we’re about to embark on a comprehensive exploration of these metallic marvels, unraveling their secrets and diving into their diverse applications.
What are PREP-ared Powders?
PREP stands for Plasticized, Reduced, Electrolyzed, and Pasticized. It’s a multi-stage process that transforms metals into finely-ground powders with unique characteristics. Imagine taking a lump of iron and turning it into a dust-like substance with specific properties – that’s the magic of PREP.
Here’s a breakdown of the PREP process:
- Plasticization: The metal undergoes a treatment that enhances its ductility and malleability, making it easier to manipulate in the next stage.
- Reduction: The softened metal is crushed and milled into a coarse powder.
- Electrolysis: This stage refines the metal powder further, removing impurities and ensuring a consistent particle size distribution.
- Passivation: A final treatment is applied to coat the powder particles with a protective layer, preventing them from oxidation and ensuring better flowability.
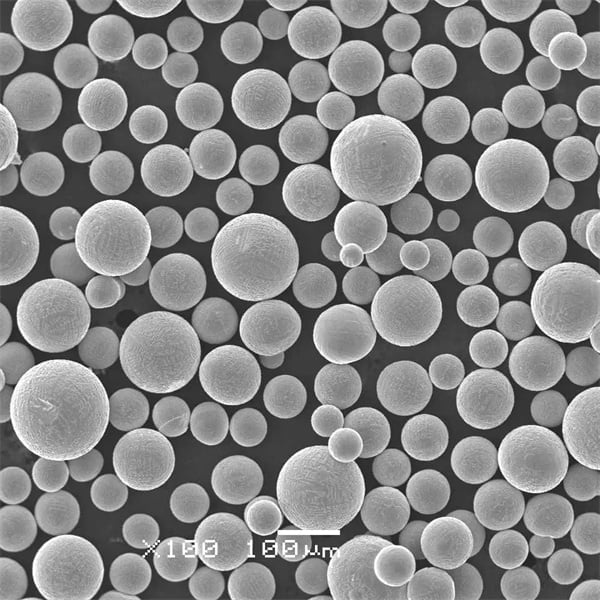
Exploring PREP Powder Options
The beauty of PREP lies in its versatility. It can be applied to a wide range of metals, each offering distinct properties and applications. Here’s a glimpse into some of the most popular PREP powder models:
Metal | Description |
---|---|
Aluminum (Al) | Lightweight and highly conductive, making it ideal for applications in aerospace, electronics, and heat dissipation. PREP aluminum powders boast excellent flowability and packing density. |
Copper (Cu) | Renowned for its superior electrical conductivity and thermal conductivity, PREP copper powders find use in electrical components, heat sinks, and brazing alloys. They offer tight particle size distribution and good sinterability. |
Nickel (Ni) | Known for its strength, corrosion resistance, and magnetic properties, PREP nickel powders are employed in catalysts, battery electrodes, and additive manufacturing. They exhibit good shaping characteristics and high surface area. |
Iron (Fe) | The workhorse of the metal world, PREP iron powders are valued for their magnetic properties and affordability. They are widely used in soft magnetic components, powder metallurgy parts, and iron enrichment applications. |
Stainless Steel (SS) | Offering a combination of strength, corrosion resistance, and aesthetics, PREP stainless steel powders cater to the needs of biomedical implants, chemical processing equipment, and high-performance components. |
Titanium (Ti) | A lightweight metal with exceptional strength-to-weight ratio and biocompatibility, PREP titanium powders are utilized in aerospace components, medical implants, and sporting goods. |
Cobalt (Co) | Valued for its high-temperature strength and magnetic properties, PREP cobalt powders are employed in cutting tools, jet engine components, and permanent magnets. They offer good hardness and wear resistance. |
Tungsten (W) Renowned for its extreme hardness and high melting point, PREP tungsten powders are utilized in tungsten carbide cutting tools, armor-piercing ammunition, and heat filaments. | |
Molybdenum (Mo) | Highly resistant to corrosion and high temperatures, PREP molybdenum powders are employed in filaments, crucibles, and electrical contacts. They offer good thermal stability and machinability. |
Niobium (Nb) | Appreciated for its superconductivity at relatively high temperatures, PREP niobium powders are used in superconducting magnets, nuclear reactors, and jet engines. |
Properties and Applications of PREP Powder
PREP powders boast a unique set of properties that set them apart from traditional metal forms:
- High Surface Area: The fine particle size of PREP powders translates to a vast surface area, which can be beneficial for applications like catalysis and powder metallurgy.
- Enhanced Flowability: The passivation process ensures smooth-flowing powders, making them ideal for automated processes and precise dispensing.
- Tailored Properties: The PREP process can be adjusted to control the particle size distribution and morphology of the powders, allowing for customization to specific applications.
These properties pave the way for a diverse range of applications:
- Additive Manufacturing (AM): PREP powders are a perfect feedstock for 3D printing techniques like Selective Laser Melting (SLM) and Electron Beam Melting (EBM). Their flowability and precise particle size distribution enable the creation of complex geometries with high accuracy. Imagine printing a lightweight and strong aircraft component using titanium PREP powder – that’s the power of AM with these advanced powders.
- Metal Injection Molding (MIM): This process utilizes PREP powders mixed with a binder to create a feedstock that can be injection molded into intricate shapes. Once molded, the binder is removed, and the metal powder particles are sintered together to form the final part. Think about creating tiny gears or intricate medical implants with high precision and complex details – that’s the advantage of MIM with PREP powders.
- Brazing and Soldering: PREP powders can be used as filler metals for joining dissimilar materials. Their fine particle size allows for excellent capillary action, ensuring strong and consistent bonds. Imagine repairing a cracked heat exchanger or joining electrical components with a reliable and precise brazing technique – that’s where PREP powders come into play.
- Catalysts: The high surface area of PREP powders makes them ideal candidates for catalysts in various chemical reactions. The increased surface area provides more active sites for the reaction to occur, leading to improved efficiency and performance. Think about creating a more efficient catalytic converter in your car to reduce emissions – that’s a potential application of PREP powders.
- Battery Electrodes: Certain PREP powders, like nickel and cobalt, can be used to manufacture high-performance battery electrodes. Their tailored properties can enhance battery capacity, lifespan, and charging efficiency. Imagine extending the range of your electric vehicle with next-generation battery technology that utilizes PREP powders – that’s a glimpse into the future.
-
Ti45Nb Powder for Additive Manufacturing
-
Stainless Steel 316L Powder for Metal 3D Printing
-
TiNb Alloy Powder
-
TiNbZrSn Alloy Powder
-
Ti6Al4V Powder Titanium Based Metal Powder for Additive Manufacturing
-
CoCrMoW Powder
-
CPTi Powder
-
TC18 Powder : Unlocking the Power of Titanium Carbide
-
TC11 Powder : A Comprehensive Guide
Choosing the Right PREP
When selecting a PREP powder, several factors need to be considered:
- Metal Type: As discussed earlier, different metals offer unique properties. Choose the metal that best suits the desired application’s needs – corrosion resistance for marine components or high electrical conductivity for electronics.
- Particle Size Distribution: The size and distribution of the powder particles significantly impact flowability, packing density, and final part properties. Finer powders offer better surface area but may be less flowable, while coarser powders might be easier to handle but have lower surface area.
- Sinterability: This refers to the powder’s ability to bond together during the sintering process. Good sinterability ensures a strong and dense final part.
- Purity: The level of impurities in the powder can affect its performance. High purity powders are often preferred for critical applications.
Here’s a table summarizing some key specifications to consider when choosing PREP powders:
Specification | Description |
---|---|
Metal Type | Aluminum (Al), Copper (Cu), Nickel (Ni), Iron (Fe), Stainless Steel (SS), Titanium (Ti), Cobalt (Co), Tungsten (W), Molybdenum (Mo), Niobium (Nb), etc. |
Particle Size Distribution | Typically measured in microns (µm) |
Sphericity | The degree to which particles resemble perfect spheres |
Apparent Density | The weight of powder per unit volume |
Flowability | The ease with which the powder flows |
Purity | The percentage of the desired metal in the powder |
Suppliers and Pricing
PREP powders are becoming increasingly available from a variety of suppliers. Here are some factors to consider when choosing a supplier:
- Reputation: Look for a reputable supplier with a proven track record of quality and consistency.
- Product Range: Ensure the supplier offers the specific PREP powder you require.
- Technical Expertise: A supplier with in-house technical expertise can provide valuable guidance and support.
- Pricing: PREP powders can vary in price depending on the metal type, particle size, and purity.
Here’s a table providing a general overview of suppliers and pricing for some common PREP powders (Note: Prices are indicative and may vary depending on supplier and market conditions):
Metal | Typical Suppliers | Price Range (USD/kg) |
---|---|---|
Aluminum (Al) | Atotech, Höganäs AB, Sandvik Hyperion | $10 – $50 |
Copper (Cu) | American Elements, Carpenter Powder Products, ERAMET | $20 – $70 |
Nickel (Ni) | Höganäs AB, OM Materials, Sumitomo Metal Industries | $30 – $100 |
Iron (Fe) | Höganäs AB, GKN Powder Metallurgy, AMETEK | $5 – $20 |
Stainless Steel (SS) | Carpenter Powder Products, AP Powder Company, Höganäs AB | $20 – $80 |
Titanium (Ti) | GE Additive, ATI Powder Metals, OSRAM | $50 – $200 |
Cobalt (Co) | Höganäs AB, Carpenter Powder Products, American Elements | $40 – $150 |
Tungsten (W) | HC Starck, Sandvik Hyperion, Kennametal | $100 – $300 |
Molybdenum (Mo) | Höganäs AB, Materion Performance Materials, China Molybdenum | $50 – $150 |
Niobium (Nb) | American Elements, CBMM, Treibacher Industrie AG | $100 – $400 |
Advantages and Limitations
PREP powders offer a compelling set of advantages, but it’s important to acknowledge their limitations as well.
Advantages of PREP Powders:
- High Purity and Consistency: The PREP process ensures a high degree of purity and consistent particle size distribution, leading to predictable and reliable performance in end-use applications.
- Enhanced Flowability: The surface treatment during the PREP process improves flowability, making these powders ideal for automated processes and precise dispensing in techniques like AM and MIM.
- Tailored Properties: The PREP process can be adjusted to control the particle size, morphology, and even surface chemistry of the powders, allowing for customization to specific needs.
- Versatility: PREP powders can be applied to a wide range of metals, each offering unique properties for diverse applications.
Limitations of PREP Powders:
- Cost: The PREP process can be more expensive than traditional metal production methods, which can translate to higher costs for the final powders.
- Storage Considerations: PREP powders can be susceptible to moisture and oxidation, requiring careful storage and handling to maintain their integrity.
- Process Optimization: For some applications, optimizing the use of PREP powders in techniques like AM and MIM may require adjustments to processing parameters to achieve the desired results.
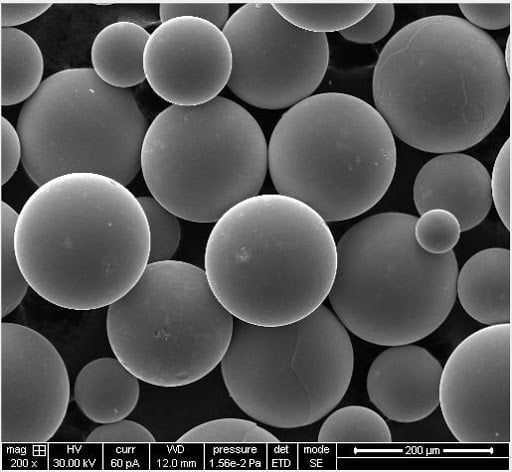
FAQs
Here are some frequently asked questions regarding PREP powders:
- Q: Are PREP powders environmentally friendly?
A: The environmental impact of PREP powders depends on the specific metal and the manufacturing process. However, the reduced waste and precise material usage associated with AM and MIM can offer some environmental advantages.
- Q: How will PREP powders affect traditional metalworking techniques?
A: PREP powders are not a complete replacement for traditional metalworking techniques like casting and forging. However, they offer new possibilities for creating complex shapes and components, potentially leading to a more complementary relationship between these technologies.
- Q: What are the future trends for PREP powders?
A: The future of PREP powders looks bright. Advancements in AM and MIM technologies are expected to drive increased demand for these powders. Additionally, research is ongoing to develop new PREP processes for a wider range of metals and alloys, further expanding their application potential.
Share On
MET3DP Technology Co., LTD is a leading provider of additive manufacturing solutions headquartered in Qingdao, China. Our company specializes in 3D printing equipment and high-performance metal powders for industrial applications.
Inquiry to get best price and customized Solution for your business!
Related Articles
About Met3DP
Recent Update
Our Product
CONTACT US
Any questions? Send us message now! We’ll serve your request with a whole team after receiving your message.
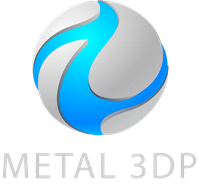
Metal Powders for 3D Printing and Additive Manufacturing
COMPANY
PRODUCT
cONTACT INFO
- Qingdao City, Shandong, China
- [email protected]
- [email protected]
- +86 19116340731