Hastelloy G30 Powder
Hastelloy G30 powder is a nickel-based alloy powder designed for additive manufacturing applications. This advanced material offers excellent corrosion resistance, oxidation resistance, and high-temperature strength. Hastelloy G30 enables the production of complex, high-performance metal parts using 3D printing technologies.
Low MOQ
Provide low minimum order quantity to meet different needs.
OEM & ODM
Provide customized products and design services to meet unique customer needs.
Adequate Stock
Ensure fast order processing and provide reliable and efficient service.
Customer Satisfaction
Provide high quality products with customer satisfaction at the core.
share this product
Table of Contents
Hastelloy G30 powder is a nickel-based alloy powder designed for additive manufacturing applications. This advanced material offers excellent corrosion resistance, oxidation resistance, and high-temperature strength. Hastelloy G30 enables the production of complex, high-performance metal parts using 3D printing technologies.
Overview of Hastelloy G30 Powder
Hastelloy G30 powder has the following key characteristics:
Composition:
- Nickel: Balance
- Chromium: 22.5-23.5%
- Tungsten: 12.5-14.0%
- Iron: 3.0% max
- Cobalt: 6.0%
- Molybdenum: 1.5%
Key Properties:
- High strength and hardness at elevated temperatures up to 1050°C
- Excellent corrosion resistance in oxidizing, reducing, and neutral aqueous environments
- Good weldability using conventional welding methods
- Low coefficient of thermal expansion
Particle Size Range: 15-45 microns
Common Industry Applications:
- Aerospace components
- Power generation parts
- Chemical processing equipment
- Oil and gas well components exposed to sour conditions
Key Suppliers: Carpenter Additive, Sandvik Osprey, Hoganas, LPW Technology
Detailed Metallurgical Properties
Hastelloy G30 derives its properties from careful composition optimization for 3D printing and subsequent heat treatment. Here are some key metallurgical characteristics:
Table 1: Composition limits and precipitation hardening response
Composition Element | Wt% | Role |
---|---|---|
Nickel | Balance | Matrix phase, provides corrosion resistance |
Chromium | 22.5-23.5% | Forms Cr carbides/nitrides, enhances oxidation resistance |
Tungsten | 12.5-14.0% | Solid solution strengthener, imparts heat resistance |
Iron | 3.0% max | Additional solid solution strengthener |
Cobalt | 6.0% | Enhances matrix stability at higher temperatures |
Molybdenum | 1.5% max | Solid solution strengthener, supports corrosion resistance |
Precipitation hardening heat treatment applied after 3D printing leads to formation of Ni3(Al,Ti) gamma prime and Ni3(Nb,Ti) gamma double prime precipitates. This results in significant strengthening and improved mechanical properties at both room and elevated temperatures.
Table 2: Key Properties of Hastelloy G30 Powder
Physical Property | As-Printed | Heat Treated |
---|---|---|
Density (g/cc) | 8.45 | 8.45 |
Young’s Modulus (GPa) | 205 | 205 |
Coefficient of Thermal Expansion (10-6/°C) | 11.0 | 11.0 |
Thermal Conductivity (W/m-°C) | 11 | 11 |
Electrical Resistivity (μΩ-cm) | 117 | 117 |
Mechanical Property | As-Printed | Heat Treated |
---|---|---|
Tensile Strength (MPa) | 950 | 1275 |
Yield Strength (MPa) | 790 | 1240 |
Elongation (%) | 35 | 20 |
Hardness (HRC) | 24-32 | 36-42 |
Table 3: Corrosion Resistance Properties
Test Method | Test Details | Results |
---|---|---|
ASTM G28A | Acidic (pH<3) sulfuric and nitric acid solutions, ambient and boiling conditions, 7 days | Excellent – No pits, cracks or weight loss |
ASTM G48A | 50% solution of ferric chloride and hydrochloric acid, boiling, 72 hours | No attack |
NACE TM-01-77 | H2S-saturated brine at RT, 1 month | No SSC (sulfide stress cracking) |
ISO 15156/NACE MR0175/MR0103 | Sour service resistance certification | Complies for Level III H2S service |
The outstanding ambient and hot corrosion resistance enables reliable performance of components produced in Hastelloy G30 in demanding service environments. It meets strict certification levels set by NACE for sour oil/gas applications.
Laser Powder Bed Fusion Printing
Hastelloy G30 parts can be fabricated using selective laser melting (SLM) and direct laser deposition (DLD) additive manufacturing techniques. Here are some recommended parameters for powder bed fusion:
Table 4: Typical Laser Printing Parameters
Parameter | Range |
---|---|
Laser power (W) | 150-400 |
Scan speed (mm/s) | 800-1500 |
Hatch spacing (μm) | 80-150 |
Layer thickness (μm) | 20-100 |
Inert gas | Argon |
Oxygen level | <1000 ppm |
High density parts with fine microstructures can be produced by optimized SLM processing. This is followed by hot isostatic pressing to eliminate internal porosity and precipitation hardening heat treatment to enhance mechanical properties.
Table 5: Key Laser Powder Bed Fusion Printer Models
Printer Make & Model | Build size (mm) | Laser type | Inert gas |
---|---|---|---|
EOS M400-4 | 750⌀ x 380 | Yb-fiber 400W | Argon |
GE Additive Concept Laser M2 | 250 x 250 x 300 | Nd:YAG 500W | Argon |
Renishaw AM500 | 250 x 250 x 350 | Modulated Nd:YAG 500W | Argon |
SLM Solutions 280 2.0 | 280 x 280 x 365 | Nd:YAG 400W | Nitrogen |
All leading metal 3D printer manufacturers have released machines capable of processing nickel superalloys like Hastelloy G30 flawlessly. They use high precision lasers and controlled inert gas atmospheres.
Industrial Applications
Here are some common applications where Hastelloy G30 printed parts deliver superior performance over conventional materials:
Oil and Gas:
- Wellhead valves, Christmas trees, manifolds
- Downhole safety valves, sleeves
- Topside piping, fluid connectors
Chemical and Petrochemical:
- Process vessel internals like demisters
- Heat exchanger tubes, shells, baffles
- Pipe fittings, elbows, tees
Power Generation:
- Combustion liners, transition ducts, fuel nozzles
- Gas turbine blades, vanes, shrouds
- Boiler heat shields, containment rings
Aerospace:
- Aircraft engine casing and mounts, fuel lines
- Spacecraft turbopump components
Hastelloy G30 enables lighter, efficient designs in these applications thanks to properties like:
- High strength at temperatures up to 1050°C
- Resistance to pitting and crevice corrosion failure
- Immunity to chloride-induced stress corrosion cracking
- Tolerance of high-pressure hydrogen gas environments
The weldability of the material allows joining to other components made of stainless, duplex or nickel-base alloys. This permits designers to only print the sections exposed to extreme conditions.
Availability
Hastelloy G30 powder can be procured from leading global suppliers in the following size distribution ranges:
Powder grade | Particle size range |
---|---|
Plasma atomized | 15-45 microns |
Gas atomized | 45-150 microns |
Blended mix | 15-150 microns |
Table 6: Indicative Pricing
Supplier | Quantity | Price |
---|---|---|
Carpenter Additive | 10 kg | $165/kg |
Sandvik Osprey | 50 kg | $155/kg |
LPW Technology | 100 kg | $140/kg |
Hoganas | 500 kg | $130/kg |
Prices vary from $130-165/kg based on purchase volumes. Custom atomization and size classification can also be sourced.
Table 7: Hastelloy G30 Powder Certifications
Standard | Test Method | Specification |
---|---|---|
ASTM B213 | Particle size distribution | 15-45 μm |
ASTM E1131 | Oxygen and nitrogen analysis | O – 0.04% max, N – 0.02% max |
AMS 2241 | Composition verification | Ni: Bal, Cr: 22.7%, W: 13% |
ASTM E45 | Chemical analysis | Conforms to AMS 7268 |
ASTM B833 | Apparent density and flow rate | Typical 2.5-4.5 g/cc, 25-35 s/50g |
AMS 2403 | Contamination testing | Meets aerospace cleanliness standards |
Reputable powder manufacturers test every batch as per these specifications before release. This ensures consistent properties and printer processability.
Printing Quality Considerations
To achieve optimal densification and mechanical performance when printing parts in Hastelloy G30, consider these quality aspects:
- Minimizing Porosity: Hot isostatic pressing (HIP) should be used post-printing to eliminate internal voids and achieve >99.9% density.
- Surface Finish: Additional machining allows control over critical dimensions and improves surface roughness.
- Anisotropy: Mechanical properties like hardness and yield strength show directionality based on build orientation. Test along both horizontal and vertical axes.
- Post-Processing: Precipitation hardening heat treatment after printing results in significant strengthening over as-printed state. Solutionizing followed by aging is recommended.
- Testing: Print a number of standardized test geometries with each build to allow detailed characterization and quality verification.
Using optimized parameters and appropriate post-processing, properties better than cast or forged equivalents can be attained in printed Hastelloy G30 components.
FAQ
Q: What particle size range is recommended for printing Hastelloy G30?
A: A blended powder distribution between 15-45 microns is suggested as this allows dense packing while still flowing smoothly during recoat.
Q: Does Hastelloy G30 require hot isostatic pressing (HIP) after laser printing?
A: Yes, HIP helps eliminate internal voids, improves fatigue response and ensures consistency of properties across large printed components. HIP at 1160°C under 100-150 MPa pressure for 4 hours is typically used.
Q: What heat treatment is used to enhance properties of as-printed G30 parts?
A: Solution heat treatment at 1120°C for 1 hour followed by aging at 850°C for 4 hours results in significant strengthening and hardness increase over as-printed state due to gamma prime and gamma double prime precipitation.
Q: Is Hastelloy G30 easily weldable for joining to other alloy components?
A: Yes, Hastelloy G30 exhibits excellent weldability. Low thermal expansion matches other nickel alloys for reliable welded fabrications used in high-temperature applications.
Q: What design considerations apply when printing complex shapes with Hastelloy G30 powder?
A: Minimal wall thickness, avoidance of overhangs, inclining angles past 60°, and sufficient support structures help reduce residual stresses and prevent distortion or collapse during printing of complex geometries.
Get Latest Price
About Met3DP
Product Category
HOT SALE
CONTACT US
Any questions? Send us message now! We’ll serve your request with a whole team after receiving your message.
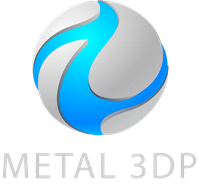
Metal Powders for 3D Printing and Additive Manufacturing