Inconel 600 Powder
Inconel 600 Powder is a nickel-chromium-iron alloy with excellent corrosion and heat resistance. It is used extensively in high temperature applications. Inconel 600 powder is the powder metallurgy form of Inconel 600, which offers several advantages over conventional Inconel 600 such as better mechanical properties.
Low MOQ
Provide low minimum order quantity to meet different needs.
OEM & ODM
Provide customized products and design services to meet unique customer needs.
Adequate Stock
Ensure fast order processing and provide reliable and efficient service.
Customer Satisfaction
Provide high quality products with customer satisfaction at the core.
share this product
Table of Contents
Overview
Inconel 600 Powder is a nickel-chromium-iron alloy with excellent corrosion and heat resistance. It is used extensively in high temperature applications. Inconel 600 powder is the powder metallurgy form of Inconel 600, which offers several advantages over conventional Inconel 600 such as better mechanical properties.
Some key details about Inconel 600 powder:
- Composition: Nickel 72%, Chromium 14-17%, Iron 6-10% plus minor amounts of carbon, manganese, silicon, sulfur and copper
- High temperature strength from cryogenic to 1093°C (2000°F)
- Excellent resistance to corrosion and oxidation
- Good mechanical properties at both low and high temperatures
- Versatile material used in a wide range of industries
- Powder metallurgy processing results in fine grains and improved properties
- Available in various size ranges suitable for different applications
Table 1: Composition of Inconel 600 Powder
Element | Composition % |
---|---|
Nickel | 72 |
Chromium | 14 – 17 |
Iron | 6 – 10 |
Carbon | 0.15 max |
Manganese | 1.0 max |
Silicon | 0.5 max |
Sulfur | 0.015 max |
Copper | 0.5 max |
Types and Grades
Several variants of Inconel 600 powder are commercially available:
Table 2: Variants of Inconel 600 Powder
Type | Description |
---|---|
Inconel 617 | Modified chemistry for improved creep strength |
Inconel 601 | Higher aluminum plus titanium addition improves oxidation resistance |
Inconel 690 | Higher chromium content gives better corrosion resistance |
Inconel 600 SG | Atomized spherical powder gives excellent flowability |
Inconel 600 powder also comes in different size ranges for various applications:
Table 3: Size Grades of Inconel 600 Powder
Size Range | Typical Applications |
---|---|
>150 microns | Hot extrusion, hot isostatic pressing |
45-150 microns | Metal injection molding, cold isostatic pressing |
5-45 microns | Additive manufacturing, spray coatings |
<5 microns | Production of oxide dispersion strengthened alloys |
Properties and Characteristics
Inconel 600 has outstanding high temperature properties combined with good resistance to corrosive environments. Some of the key properties include:
Table 4: Properties of Inconel 600 Powder
Property | Value |
---|---|
Density | 8.47 g/cc |
Melting Point | 1355-1390°C (2475-2535°F) |
Thermal Conductivity | 9.8 W/m-K |
Electrical Resistivity | 92 to 112 μΩ-cm |
Modulus of Elasticity | 205 GPa |
Poisson’s Ratio | 0.29-0.30 |
Coefficient of Thermal Expansion | 13.3 x 10<sup>-6</sup> /°C |
Elongation | 45% |
The microstructure of Inconel 600 consists of an austenitic face centered cubic matrix with small additions of niobium and titanium carbides. The grain size is very fine in the powder product compared to conventional Inconel 600.
Micrograph showing the fine grained microstructure of gas atomized Inconel 600 powder. Image credit PMReview
Applications and Uses
The combination of strength across a wide temperature range, corrosion resistance and ease of fabrication makes Inconel 600 suitable for numerous high performance applications:
Table 5: Applications of Inconel 600 Powder
Industry | Typical Applications |
---|---|
Aerospace | Turbine blades, combustor cans and liners, exhaust cones |
Automotive | Turbocharger turbine wheels and housings |
Chemical | Heat treating baskets and fixtures, process piping |
Petroleum Refining | Reformer and cracker tubes exposed to high temperatures |
Power Generation | Boiler tubes, coal gasification, heat recovery systems |
Biomedical | Orthopedic and dental implants |
In powder form, Inconel 600 is ideal for part manufacture using powder bed fusion or directed energy deposition. This gives greater design freedom compared to conventional techniques for making components with complex shapes.
Specifications
Inconel 600 powder is covered by various national and international specifications:
Table 6: Specifications for Inconel 600 Powder
Standard | Designation | Title |
---|---|---|
ASTM | B171 | Standard Specification for Inconel Alloy 600 Tube |
ASME | SB 171 | Inconel Alloy 600 Seamless Tube |
ISO | 13380:1997 | Unalloyed titanium – Powder metallurgy products |
AMS | 5837 | Sheet, strip, plate, bar, wire, forgings and rings |
NACE | – | Use for service in high temperature aqueous solutions |
Manufacturers and Pricing
There are several reputable global suppliers that manufacture Inconel 600 alloy powder:
Table 7: Suppliers of Inconel 600 Powder
Company | Product Designation | Price Per Kg |
---|---|---|
Sandvik | A 600 Atomized Powder | $18 – $28 |
Praxair | Inconel 617 Powder | $22 – $36 |
Hoganas | Shapal Hi-Flow 464 | $16 – $24 |
Carpenter Additive | Inconel 660 Pre-alloyed | $25 – $45 |
Pricing varies based on factors like order volume, size distribution and whether value-added processing is included. Small quantities for R&D purposes are more expensive.
Comparison
Table 8: Comparison of Inconel 600 with other alloys
Alloy | Strength | Wear Resistance | Oxidation Resistance | Cost |
---|---|---|---|---|
Inconel 600 | Medium | Medium | Excellent | Medium |
Inconel 625 | Higher | Excellent | Excellent | High |
SS 316L | Lower | Low | Medium | Low |
Inconel 718 | Highest | Good | Very Good | Highest |
So Inconel 600 provides an optimal balance between performance and cost for many applications requiring good environmental resistance and strength at extreme temperatures.
Pros and Cons
Table 9: Advantages and limitations of Inconel 600 powder
Pros | Cons |
---|---|
Outstanding high temperature strength | More expensive than carbon steel or stainless steel powders |
Resistance to oxidation and corrosion | Lower tensile strength compared to precipitation hardening grades |
Non-magnetic, unlike steel alloys | Requires hot isostatic pressing to achieve full density |
Readily fabricable across range of methods | Restricted weldability without proper PWHT |
Powder route gives better control of composition | Limited data available compared to Inconel wrought products |
In general, Inconel 600 powder provides valuable benefits in extreme environment service that justify the higher cost in many critical applications.
FAQs
What is the difference between Inconel and stainless steel?
Inconel alloys are nickel-based while stainless steels contain at least 10.5% chromium and more than 50% iron. Inconels offer substantially better tensile strength and corrosion resistance at high temperatures exceeding 540°C where steels rapidly lose strength.
What industries use Inconel 600?
Aerospace is the largest consumer of Inconel alloys but they find widespread use in power generation, chemical processing, pollution control equipment, nuclear reactors and even motorsports and Formula 1 exhaust systems.
What fabrication methods can be used with Inconel 600 powder?
Hot isostatic pressing (HIP) and powder bed technologies like selective laser melting (SLM) or electron beam melting (EBM) are popular. Other techniques like metal injection molding (MIM) and binder jetting can also utilize the powders.
Get Latest Price
About Met3DP
Product Category
HOT SALE
CONTACT US
Any questions? Send us message now! We’ll serve your request with a whole team after receiving your message.
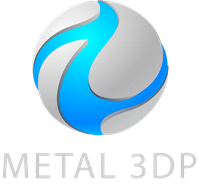
Metal Powders for 3D Printing and Additive Manufacturing