Inconel 625 Powder丨Nickel based superalloy in625 powder
In625 powder is a powdered form of the nickel-chromium alloy Inconel 625, which exhibits excellent corrosion resistance, high strength, and outstanding heat resistance. This superalloy is composed of nickel, chromium, molybdenum, and niobium, along with smaller amounts of other elements. Its unique composition imparts remarkable mechanical properties, making it a sought-after material in numerous industries.
Low MOQ
Provide low minimum order quantity to meet different needs.
OEM & ODM
Provide customized products and design services to meet unique customer needs.
Adequate Stock
Ensure fast order processing and provide reliable and efficient service.
Customer Satisfaction
Provide high quality products with customer satisfaction at the core.
share this product
Table of Contents
Overview of Inconel 625 Powder
Inconel 625 powder is a nickel-based superalloy that possesses high strength properties and resistance to elevated temperatures. Inconel 625 (Alloy 625, UNS N06625) is widely used for its high strength, excellent fabricability (including joining), and outstanding corrosion resistance. Its service temperatures range from cryogenic to 1800°F (982°C). High tensile, creep, and rupture strength, outstanding fatigue and thermal-fatigue strength, oxidation resistance and excellent weldability and brazeability are the properties of INCONEL alloy 625 that make it interesting to the aerospace field.
Inconel 625 powder is a high-performance nickel-based superalloy powder widely used in additive manufacturing (AM) and traditional metalworking processes. Known for its exceptional strength, corrosion resistance, and thermal stability, this material is a top choice in industries such as aerospace, energy, and marine engineering.
But what makes Inconel 625 powder stand out? Its unique composition, primarily consisting of nickel, chromium, and molybdenum, provides outstanding resistance against oxidation, pitting, and creep deformation. This makes it ideal for high-temperature and high-stress applications where ordinary materials would fail.
With the rise of metal 3D printing, the demand for high-quality Inconel 625 powder has skyrocketed. Companies like Met3DP are at the forefront, supplying industry-leading gas atomized and PREP-produced spherical powders optimized for Selective Laser Melting (SLM), Electron Beam Melting (EBM), Metal Injection Molding (MIM), and other advanced manufacturing techniques.
Now, let’s dive deeper into the top factors that make Inconel 625 powder an indispensable material in 2025.
Best Inconel 625 Powder for 3D Printing
Why Inconel 625 Powder Is Perfect for 3D Printing
3D printing, particularly metal additive manufacturing (AM), has revolutionized industrial production, and Inconel 625 powder is one of the most sought-after materials for this technology. The key benefits include:
- High temperature resistance – Withstands extreme heat without losing strength.
- Excellent corrosion resistance – Performs well in harsh environments, such as marine and chemical processing.
- Superior mechanical properties – High tensile strength, creep resistance, and fatigue performance.
- Good printability – Spherical powder particles ensure smooth flow and uniform layer deposition in powder bed fusion.
Inconel 625 Powder Specification
Norminal Composition(wt%) | ||||||
In625
|
Cr | Mo | Nb | Co | Fe | Al |
20-23 | 8-10 | 3.15-4.15 | ≤1 | ≤1 | ≤0.4 | |
Ti | C | Ni | O | N | ||
≤0.4 | ≤0.1 | Bal. | ≤500ppm | ≤100ppm |
Common Size:15-45um,15-53um,45-106um,45-150u,-200/-300/-400/-500/-600mesh etc,.
No | Name | Related Powder Composition(wt%) |
1 | 18Ni300 | Ni17-19,Mo4.5-5.2,Co8.5-9.5,Ti0.6-0.8,Al0.05-0.15,Fe(Bal.) |
2 | Hastelloy Alloy | Fe17-20,Cr20.5-23,Mo8-10,W0.2-1,Co0.5-2.5,C0.05-0.15,Ni(Bal.) |
3 | AlSi10Mg | Si9-11,Mg0.2-0.45,Al(Bal.) |
4 | CoCrW | Cr26.5-29,W7-9,Si1.2-1.9,Co(Bal.) |
5 | Co28Cr6Mo | Cr27-29,Mo5-7,Co(Bal.) |
6 | Spherical Ti Powder | Ti≥99.9 |
7 | TC4 | Al5.5-6.8,V3.5-4.5,Ti(Bal.) |
8 | TA15 | Al5.5-7.1,V0.8-2.5,Mo0.8-2,Zr1.5-2.5,Al(Bal.) |
9 | 316L | Cr16.00-18.00, Ni10.00-14.00,Mo2.00-3.00,Fe(Bal.) |
10 | S136 | Cr12.0-14.0,Si0.8-1.0,V0.15-0.4,C0.2-0.45,Fe(Bal.) |
11 | In625 | Cr20-23 , Mo8-10 , Nb 3.15-4.15 , Co≤1, Fe≤1 , Ni (bal.) |
12 | In718 | Cr17-21 , Mo2.8-3.3 , Nb 4.75-5.5 , Co≤1, Ni50-51 , Fe(Bal.) |
13 | Spherica WC | C3.7-4.2,W(Bal.) |
14 | Spherical Cr Powder | Cr≥99.9 |
15 | Spherica Mo Powder | Mo≥99.9 |
16 | Spherica Ta Powder | Ta≥99.9 |
17 | Spherica W Powder | W≥99.9 |
Choosing the Right Powder for Different 3D Printing Methods
Not all Inconel 625 powders are the same. The powder characteristics depend on production methods and particle size distribution, which influence their suitability for different 3D printing techniques.
Printing Method | Ideal Powder Size (µm) | Recommended Powder Type | Advantages |
---|---|---|---|
Selective Laser Melting (SLM) | 15-45 | Gas Atomized | High precision, fine details |
Electron Beam Melting (EBM) | 45-106 | Plasma Rotating Electrode Process (PREP) | Better for large, strong parts |
Binder Jetting | 20-50 | Water Atomized | Cost-effective, high throughput |
Direct Energy Deposition (DED) | 50-150 | Gas Atomized | Good for repair and large-scale printing |
Met3DP’s Advanced Powder Solutions
At Met3DP, we provide high-purity, spherical Inconel 625 powders specifically tailored for SLM, EBM, and other metal 3D printing methods. Our powders are manufactured using Vacuum Induction Gas Atomization (VIGA) and PREP technologies, ensuring optimal flowability, packing density, and printability.
Properties of Inconel 625 Powder
Understanding the chemical and physical properties of Inconel 625 powder is crucial for selecting the right material for your application.
Chemical Composition of Inconel 625 Powder
The unique chemical composition gives Inconel 625 its outstanding corrosion resistance and high-temperature strength.
Element | Percentage (%) |
---|---|
Nickel (Ni) | 58.0 min |
Chromium (Cr) | 20.0-23.0 |
Molybdenum (Mo) | 8.0-10.0 |
Iron (Fe) | 5.0 max |
Niobium (Nb) & Tantalum (Ta) | 3.15-4.15 |
Cobalt (Co) | 1.0 max |
Manganese (Mn) | 0.50 max |
Silicon (Si) | 0.50 max |
Carbon (C) | 0.10 max |
Sulfur (S) | 0.015 max |
Physical and Mechanical Properties
Inconel 625 powder exhibits exceptional mechanical properties, making it ideal for high-stress and high-temperature applications.
Property | Value |
---|---|
Density | 8.44 g/cm³ |
Melting Point | 1290-1350°C |
Tensile Strength | 827 MPa (120 ksi) |
Yield Strength | 414 MPa (60 ksi) |
Elongation | 30% |
Hardness (Rockwell B) | 85 |
Applications of Inconel 625 Powder in Industry
Given its superior properties, Inconel 625 powder is widely used in aerospace, marine, energy, and chemical processing industries.
Key Industrial Applications
Industry | Use Case | Reason for Use |
---|---|---|
Aerospace | Jet engines, exhaust systems, heat shields | Extreme heat resistance, oxidation resistance |
Marine | Submarine parts, offshore drilling components | Resistance to seawater corrosion |
Energy | Gas turbines, nuclear reactors | High-temperature strength, creep resistance |
Chemical Processing | Heat exchangers, piping systems | Corrosion resistance against acids and alkalis |
Medical | Implants, prosthetics | Biocompatibility, strength, corrosion resistance |
How Inconel 625 Powder Outperforms Other Nickel Alloys
Compared to other nickel-based superalloys like Inconel 718 and Hastelloy X, Inconel 625 offers:
- Better corrosion resistance than Inconel 718
- Higher temperature performance than Hastelloy X
- More flexibility in metal 3D printing applications
Production Methods for Inconel 625 Powder
The manufacturing method of Inconel 625 powder significantly impacts its quality, flowability, and performance. There are three primary production techniques:
Comparison of Production Methods
Production Method | Process Description | Advantages | Disadvantages |
---|---|---|---|
Gas Atomization | Metal is melted and atomized using inert gas jets | Spherical powder, good flowability | Higher cost |
Plasma Rotating Electrode Process (PREP) | Metal electrode is spun and melted using plasma | High purity, excellent sphericity | Expensive, lower yield |
Water Atomization | Molten metal is atomized with water jets | Cost-effective, large-scale production | Irregular particle shape, lower flowability |
For high-end applications like aerospace and 3D printing, gas atomized and PREP powders are preferred due to their high sphericity and purity.
Why Met3DP Uses Gas Atomization and PREP
At Met3DP, we employ state-of-the-art VIGA and PREP technologies to produce high-quality Inconel 625 powder with consistent particle size, excellent flowability, and minimal impurities.
Quality Standards for Inconel 625 Powder
When selecting Inconel 625 powder for industrial applications, meeting strict quality standards is crucial. Various international organizations have established guidelines to ensure consistency, safety, and performance. Here’s what you need to know.
Key Quality Standards for Inconel 625 Powder
Standard | Description | Applicable Industries |
---|---|---|
ASTM B443 | Specification for Inconel 625 sheet, strip, and plate | Aerospace, marine, chemical processing |
AMS 5666 | Aerospace Material Specification for forged Inconel 625 | Aerospace, defense |
ISO 9001 | Quality management system certification | General manufacturing |
ASTM F3055 | Standard for additive manufacturing of Ni-based alloys | 3D printing, medical implants |
AMS 5892 | Heat-resistant Inconel 625 for gas turbines | Energy, power generation |
Meeting these standards ensures that the material performs reliably under high-stress environments, extreme temperatures, and corrosive conditions.
Why Met3DP’s Inconel 625 Powder Meets the Highest Standards
At Met3DP, we adhere to ISO 9001-certified quality control systems, ensuring each batch of Inconel 625 powder meets or exceeds ASTM F3055 and AMS 5666 specifications. Our production process includes strict chemical composition analysis, particle morphology control, and flowability testing to deliver top-tier powders for industrial applications.
Cost Analysis of Inconel 625 Powder
The cost of Inconel 625 powder depends on various factors, including manufacturing method, particle size distribution, supplier reputation, and order volume.
Factors That Influence the Price of Inconel 625 Powder
Factor | Impact on Cost |
---|---|
Production Method | PREP and gas atomization lead to higher costs due to better quality |
Purity & Composition | Higher purity powders cost more but offer better performance |
Particle Size Distribution | Fine powders optimized for SLM and EBM are more expensive than coarser powders |
Order Volume | Bulk orders reduce costs due to economies of scale |
Supplier Reputation | Established suppliers with ISO-certified processes may charge more for quality assurance |
Price Comparison: Inconel 625 vs. Other Nickel-Based Powders
Material | Average Price per kg (2025) | Primary Application |
---|---|---|
Inconel 625 Powder | $80 – $150 | Aerospace, energy, 3D printing |
Inconel 718 Powder | $70 – $130 | Aerospace, automotive |
Hastelloy X Powder | $90 – $160 | High-temperature applications |
Stainless Steel 316L Powder | $20 – $50 | General manufacturing |
While Inconel 625 powder is more expensive than stainless steel, its superior heat and corrosion resistance make it a cost-effective choice for mission-critical applications.
How to Get the Best Price for Inconel 625 Powder
- Buy in Bulk – Suppliers often provide discounts for large-volume purchases.
- Choose the Right Supplier – Trusted companies like Met3DP offer high-quality powders at competitive rates.
- Select the Right Particle Size – Avoid overpaying for ultra-fine powders if your process doesn’t require them.
Inconel 625 Powder for Powder Bed Fusion vs. Binder Jetting
Two major 3D printing technologies use Inconel 625 powder: Powder Bed Fusion (PBF) and Binder Jetting (BJ). Each has unique advantages and is suited for different applications.
Comparison: Inconel 625 Powder for PBF vs. Binder Jetting
Feature | Powder Bed Fusion (PBF) | Binder Jetting (BJ) |
---|---|---|
Printing Process | Uses a laser or electron beam to melt and fuse powder | Uses a binder to glue powder particles before sintering |
Ideal Particle Size | 15-45µm (SLM), 45-106µm (EBM) | 20-50µm |
Strength of Final Part | High-density, strong parts | Lower strength, requires post-processing |
Best for Complex Geometries? | Yes, supports intricate designs | Limited complexity |
Cost | Higher due to laser/electron beam technology | Lower due to faster printing and cheaper materials |
Application | Aerospace, medical implants, energy components | Prototyping, low-cost manufacturing |
If you need high-strength, precision parts, PBF is the best choice. But if you’re looking for cost-effective, high-speed production, Binder Jetting might be more suitable.
Met3DP’s Expertise in Powder Bed Fusion
At Met3DP, we specialize in high-quality spherical Inconel 625 powders optimized for SLM and EBM technologies. Our gas atomized powders provide excellent flowability, ensuring consistent and reliable 3D printing results.
Water Atomized vs. Gas Atomized vs. PREP Inconel 625 Powder: Which Is Better?
The powder production method directly impacts its morphology, purity, and suitability for different manufacturing processes.
Comparison of Inconel 625 Powder Production Methods
Method | Particle Shape | Purity | Best Application |
---|---|---|---|
Water Atomization | Irregular | Lower | Pressed & sintered parts |
Gas Atomization | Spherical | High | Laser-based 3D printing (SLM, EBM) |
Plasma Rotating Electrode Process (PREP) | Perfectly Spherical | Very High | High-end aerospace, medical |
Why Gas Atomized and PREP Powders Are Superior
- Better Flowability: Ensures smooth powder spreading for 3D printing.
- Higher Purity: PREP powders have minimal oxygen contamination.
- Consistent Particle Size Distribution: Critical for SLM and EBM applications.
At Met3DP, we use advanced gas atomization and PREP techniques to manufacture premium-quality Inconel 625 powder for the most demanding applications.
FAQ: Everything You Need to Know About Inconel 625 Powder
Question | Answer |
---|---|
What makes Inconel 625 powder unique? | Its high nickel content, combined with chromium and molybdenum, provides exceptional corrosion resistance and high-temperature strength. |
What industries use Inconel 625 powder? | Aerospace, marine, energy, chemical processing, and medical implants. |
What is the ideal particle size for SLM printing? | Between 15-45µm, ensuring smooth powder flow and optimal print quality. |
Is gas atomized powder better than water atomized powder? | Yes, gas atomized powders are more spherical, purer, and better suited for 3D printing. |
How much does Inconel 625 powder cost in 2025? | Prices range from $80 to $150 per kg, depending on purity, particle size, and supplier. |
Where can I buy high-quality Inconel 625 powder? | Met3DP offers top-tier gas atomized and PREP powders for 3D printing and industrial applications. |
Final Thoughts
Inconel 625 powder remains one of the most versatile and high-performance nickel-based powders available in 2025. Whether you need it for 3D printing, aerospace, energy, or corrosion-resistant environments, selecting the right supplier and ensuring quality standards are met is crucial.
At Met3DP, we provide industry-leading metal powders optimized for SLM, EBM, and other advanced manufacturing technologies. Contact us today to find the perfect powder for your application!
Get Latest Price
About Met3DP
Product Category
HOT SALE
CONTACT US
Any questions? Send us message now! We’ll serve your request with a whole team after receiving your message.
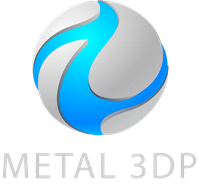
Metal Powders for 3D Printing and Additive Manufacturing