Inconel 740 Powder
Inconel 740 is a nickel-based alloy powder used primarily in powder metallurgy applications. It has excellent high temperature strength, outstanding corrosion resistance, and good oxidation resistance.
Some key properties and characteristics of Inconel 740 powder include:
Low MOQ
Provide low minimum order quantity to meet different needs.
OEM & ODM
Provide customized products and design services to meet unique customer needs.
Adequate Stock
Ensure fast order processing and provide reliable and efficient service.
Customer Satisfaction
Provide high quality products with customer satisfaction at the core.
share this product
Table of Contents
Overview
Inconel 740 is a nickel-based alloy powder used primarily in powder metallurgy applications. It has excellent high temperature strength, outstanding corrosion resistance, and good oxidation resistance.
Some key properties and characteristics of Inconel 740 powder include:
Composition:
- Nickel: Balance
- Chromium: 22-25%
- Cobalt: 15-20%
- Tantalum: 1.5-2.5%
- Aluminum: 0.5-1.5%
- Titanium: 0.5-2%
- Carbon: 0.05-0.15%
Particle Size: 15-45 microns
Apparent Density: Typically 2.5-3.5 g/cm3
Flow Rate: 25-35 s/50g
Morphology: Spheroidal powder
Some of the key applications and uses of Inconel 740 powder include:
- Turbine blades
- Engine components
- Heat exchangers
- Valves and pumps
- Tooling
- Oil and gas extraction components
Composition
The composition of Inconel 740 powder can vary depending on the specification and requirements. Here is a typical composition:
Element | Weight % |
---|---|
Nickel | Balance |
Chromium | 22-25% |
Cobalt | 15-20% |
Tantalum | 1.5-2.5% |
Aluminum | 0.5-1.5% |
Titanium | 0.5-2% |
Carbon | 0.05-0.15% |
Nickel forms the base of the alloy, providing corrosion resistance. Chromium helps strengthen the alloy and enhances oxidation resistance. Cobalt also helps strengthen the alloy and provides hot hardness at high temperatures. Tantalum and titanium help with carbide precipitation strengthening.
The controlled additions of these alloying elements give Inconel 740 excellent high temperature mechanical properties and corrosion resistance.
Properties and Characteristics
Inconel 740 is valued for its combination of high strength, corrosion resistance, and ability to withstand extreme temperatures. Here are some of its key properties and characteristics:
Mechanical Properties:
- Excellent strength at high temperatures up to 1150°C
- Good weldability
- High hardness and wear resistance
Physical Properties:
- Melting point: 1350-1400°C
- Density: 8.1-8.3 g/cm3
Corrosion Resistance:
- Outstanding resistance to pitting and crevice corrosion
- Excellent resistance to oxidizing and carburizing atmospheres up to 1100°C
Oxidation Resistance:
- Can resist continuous operating temperatures up to 1100°C
- Forms protective oxide layer in oxidizing atmospheres
Other Characteristics:
- Resists thermal fatigue cracking
- Low coefficient of thermal expansion
- Easy to machine and grind
The unique combination of strength, hardness, and corrosion resistance make this alloy suitable for the most demanding applications. The high temperature capabilities allow components to operate safely in extreme environments.
Applications and Uses
Thanks to its well-balanced mechanical properties and corrosion resistance at elevated temperatures, Inconel 740 has found widespread use in industries like aerospace, power generation, and oil & gas.
Typical applications and uses include:
Aerospace: Combustors, turbine blades and vanes, rocket nozzles
Industrial Gas Turbines: Buckets, nozzles, combustion cans
Oil & Gas: Downhole tools, valves, wellhead components
Pollution Control: Gas turbine components exposed to hot corrosive gases
Automotive: Turbocharger turbines, exhaust valves
Chemical Processing: Reactor vessels, heat treating equipment
Power Generation: Heat exchanger tubing, coal gasification components
The excellent strength of Inconel 740 at extreme temperatures, combined with outstanding corrosion resistance, makes it well-suited for components exposed to hot gases under pressure. This allows it to outperform lower grade alloys in demanding environments.
Specifications
Inconel 740 powder is available in standard and custom specifications to suit different applications and processing methods.
Here are some of the common sizes, grades, and standards for Inconel 740 powder:
Powder Sizes
Mesh Range | Micron Range |
---|---|
-325 mesh | <45 microns |
-270 + 325 mesh | 45-53 microns |
-230 + 270 mesh | 63-74 microns |
Grades
Grade | Description |
---|---|
Standard | Balance of mechanical properties and cost |
High Purity | Minimized impurities for performance critical applications |
Low Carbon | Improved ductility and impact resistance |
Standards
Standard | Description |
---|---|
AMS 5801 | General specification for nickel alloy powder |
ASTM B751 | Standard for general requirements for nickel and nickel alloys |
The powder can also be customized to meet application requirements in terms of particle size distribution, morphology, apparent density, flow characteristics, impurity levels, etc.
Suppliers and Pricing
As a widely used superalloy powder, Inconel 740 is supplied by leading metal powder manufacturers and distributors globally. Some of the major suppliers include:
Suppliers
- Carpenter Powder Products
- Praxair Surface Technologies
- Hoganas High Alloys
- CNPC Powder Group
- Sandvik Osprey
Pricing
Grade | Price Range |
---|---|
Standard | $50-70 per kg |
High Purity | $70-100 per kg |
Low Carbon | $60-80 per kg |
Pricing can vary based on order volume, precise composition, particle characteristics, etc. Custom grades tailored to application needs are also available at premium prices. The high performance of Inconel 740 powder justifies its higher cost versus simpler alloys.
Comparison With Alternatives
Inconel 740 delivers an optimized combination of temperature capability, corrosion resistance, strength, and cost. But several alternative alloys exist for high temperature applications, each with pros and cons:
Alloy | Pros | Cons |
---|---|---|
Inconel 740 | – Strength up to 1150°C
– Resists corrosion – Cost effective |
– Limited high temperature creep resistance |
Inconel X | – Higher strength than 740
– Better creep above 1000°C |
– Less corrosion resistance
– Higher alloy content raises cost |
Haynes 230 | – Oxidation resistance to 1200°C
– Most economical |
– Lower strength than Inconel
– More susceptible to thermal fatigue |
Inconel 740 offers the best balance by delivering 80-90% of the capabilities of more advanced alloys at lower cost. It significantly outperforms workhorse alloys like 316 stainless steel in high temperature environments.
For the ultimate in performance with less regard to cost, alloys like Inconel X or Inconel 783 may be chosen instead. But Inconel 740 covers a wide sweet spot between price and extreme temperature capacity.
Advantages and Limitations
Inconel 740 is designed to excel in hot corrosion environments, but there are some limitations in certain applications:
Advantages
- Retains over 50% of room temperature strength at 1100°C
- Better oxidation resistance than stainless steels
- Does not require special welding procedures
- Available at lower cost than Inconel X or 600 alloys
Limitations
- Less exceptional creep resistance than some Inconel grades
- Not suitable for continuous service above 1150°C
- Requires careful heat treatment to optimize properties
- Difficult to machine compared to lower alloys
For the majority of high temperature applications below 1100°C, Inconel 740 has clear advantages over more common materials. But pushing beyond this temperature threshold requires more advanced alloys or superalloys.
Proper processing and heat treatment of Inconel 740 can further improve properties. The alloy also benefits greatly from hot isostatic pressing to eliminate porosity in powder metallurgy parts.
Conclusion
With its balanced composition and processing versatility, Inconel 740 empowers engineers to design for hot corrosion resistance across a wide range of operating temperatures and environments.
This nickel-based superalloy powder combines strength, oxidation resistance, cost-efficiency, and compatibility with multiple manufacturing techniques for high performance components.
Turbines, combustion hardware, downhole tools, and other hot section parts rely on Inconel 740 to safely endure temperatures exceeding 1000°C even in corrosive conditions while retaining adequate ductility and fatigue life.
Get Latest Price
About Met3DP
Product Category
HOT SALE
CONTACT US
Any questions? Send us message now! We’ll serve your request with a whole team after receiving your message.
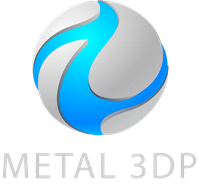
Metal Powders for 3D Printing and Additive Manufacturing