Inconel X750 Powder
Inconel X750 Powder is a nickel-chromium alloy powder used primarily in high-temperature applications requiring corrosion and oxidation resistance. It has excellent strength, toughness, and fatigue resistance up to 1300°F (704°C). Key features include:
- High temperature strength and corrosion resistance
- Excellent oxidation resistance up to 1800°F (982°C)
Low MOQ
Provide low minimum order quantity to meet different needs.
OEM & ODM
Provide customized products and design services to meet unique customer needs.
Adequate Stock
Ensure fast order processing and provide reliable and efficient service.
Customer Satisfaction
Provide high quality products with customer satisfaction at the core.
share this product
Table of Contents
Overview
Inconel X750 Powder is a nickel-chromium alloy powder used primarily in high-temperature applications requiring corrosion and oxidation resistance. It has excellent strength, toughness, and fatigue resistance up to 1300°F (704°C). Key features include:
- High temperature strength and corrosion resistance
- Excellent oxidation resistance up to 1800°F (982°C)
- Good weldability and formability
- Used in gas turbines, spacecraft, nuclear reactors, heat treating equipment
Inconel X750 powder can be used in various powder metallurgy techniques like hot isostatic pressing, metal injection molding, additive manufacturing, and laser/electron beam melting to fabricate complex parts.
Table 1: Inconel X750 powder types and characteristics
Type | Size range | Morphology | Apparent density | Flowability | Sintered density |
---|---|---|---|---|---|
Gas atomized | 15-45 μm | Spherical | High | Good | >98% |
Water atomized | 150-300 μm | Irregular | Medium | Fair | 96-98% |
Plasma atomized | 10-22 μm | Mostly spherical | Very high | Excellent | >99% |
Composition
The nominal composition of Inconel X750 powder is given below:
Table 2: Chemical composition of Inconel X750 powder
Element | Weight % |
---|---|
Nickel (Ni) | 72.0 min |
Chromium (Cr) | 14.0-17.0 |
Iron (Fe) | 5.0-9.0 |
Niobium (Nb) + Tantalum (Ta) | 0.7-1.2 |
Titanium (Ti) | 0.7-1.7 |
Aluminum (Al) | 0.5-1.2 |
Cobalt (Co) | 1.0 max |
Manganese (Mn) | 1.0 max |
Silicon (Si) | 1.0 max |
Carbon (C) | 0.1 max |
Boron (B) | 0.006-0.02 |
Zirconium (Zr) | 0.05 max |
The balance is nickel and incidental impurities. The mixture of niobium, tantalum, titanium, and aluminum content gives Inconel X750 excellent high temperature mechanical properties by precipitation strengthening.
Properties
Table 3: Physical and mechanical properties of Inconel X750
Property | Values |
---|---|
Density | 8.25 g/cm3 |
Melting point | 1315-1370°C |
Thermal conductivity | 11.2 W/m-K |
Modulus of elasticity | 205 GPa |
Poisson’s ratio | 0.29 |
Tensile strength | 1310 MPa (annealed) |
Yield strength | 1110 MPa (annealed) |
Elongation | 16% (annealed) |
Hardness | 390 HB |
Applications
Some major applications of Inconel X750 powder include:
Table 4: Applications of Inconel X750 powder
Industry | Components |
---|---|
Aerospace | Turbine blades, combustion chambers, nozzle guide vanes |
Oil & gas | Wellhead components, downhole tools |
Automotive | Turbocharger wheels, valve components |
Industrial gas turbines | Transition ducts, combustor baskets |
Nuclear | Heat exchangers, valve bodies |
Advantages of using Inconel X750 powder for these applications:
- Excellent high temperature mechanical properties up to 1300°F
- Retains strength and hardness at elevated operating temperatures
- Outstanding corrosion and oxidation resistance at high temperatures
- Parts maintain close dimensional tolerances during service
- Components have good surface finish and complex geometries
Table 5: Additive manufacturing processes for Inconel X750
Process | Properties | Applications |
---|---|---|
Laser powder bed fusion (L-PBF) | High density, moderate surface finish and accuracy | Aerospace components, tooling |
Electron beam melting (EBM) | Fully dense parts, anisotropic microstructure | Structural parts, engine components |
Directed energy deposition (DED) | Low porosity, good structural integrity | Repair and cladding of high value parts |
Specifications
Inconel X750 powder is available in various size distributions and morphologies to suit different additive manufacturing processes:
Table 6: Specifications of Inconel X750 powder
Description | Specification |
---|---|
Size range | 10-45 μm |
Chemistry | AMS 5667, AMS 5699 |
Particle shape | Spherical, irregular |
Manufacture | Gas atomized, water atomized, plasma atomized |
Apparent density | Up to 65% for loose powder |
Tap density | Up to 75% for packed powder |
Flow rate | >30 s/50 g |
Oxygen content | <100 ppm |
Nitrogen content | <40 ppm |
Suppliers
Table 7: Suppliers of Inconel X750 powder
Company | Location |
---|---|
Sandvik | Sweden |
AP&C | Canada |
Carpenter Technology | United States |
Erasteel | Sweden |
Powder Alloy Corporation | United States |
Typical pricing for Inconel X750 powder depending on size, shape, and quantity:
- Gas atomized spherical – $80-150 per kg
- Water atomized irregular – $30-60 per kg
- Research/prototype quantities – Smaller, could be double commercial
Table 8: Comparison of Inconel X750 versus Inconel 718
Parameter | Inconel X750 | Inconel 718 |
---|---|---|
Density | Higher | 8.19 g/cm3 |
Tensile strength | Higher | 1275 MPa |
Creep strength | Lower | Better by ~100°C |
Oxidation resistance | Higher | Up to 1800°F |
Cost | ~2X more expensive | Less expensive |
Machinability | More difficult to machine | Easier |
Weldability | Lower due to precipitation hardening | Better |
Limitations
Some drawbacks and challenges with using Inconel X750 powder include:
- Expensive alloy increases component costs significantly
- Difficult to fully dense without hot isostatic pressing
- Prone to cracking if not processed correctly
- Requires stress-relieving to avoid cracking during service
- Lower creep rupture strength than Inconel 718
- Subject to strain-age embrittlement at lower temperatures
Proper dispersion of strengthening particles requires solution heat treatment and aging to achieve optimal properties. Susceptible to oxidation above 1800°F requiring protective coatings.
FAQs
What is Inconel X750 used for?
Inconel X750 is used to fabricate components for high temperature applications requiring good mechanical strength, creep resistance, thermal fatigue strength, and corrosion resistance up to 1300°F. Typical uses include gas turbine blades, combustor components, spacecraft and nuclear reactor parts.
What additive manufacturing methods can use Inconel X750?
Inconel X750 powder can be processed using laser powder bed fusion (L-PBF), electron beam melting (EBM), and directed energy deposition (DED) methods. Each process produces parts with different microstructures and mechanical properties.
Does Inconel X750 require hot isostatic pressing?
For highest quality fully dense parts with optimum properties, Inconel X750 components fabricated by AM require HIP post-processing. However, parameters can be optimized to achieve >99% density directly after heat treatment for some applications.
Is Inconel X750 weldable?
Inconel X750 has lower weldability than the Inconel 600 series due to its precipitation hardening characteristics. Welding filler metals matching base composition along with proper solution annealing and aging is required to avoid weld cracking and weakened zones.
What is the typical surface finish of Inconel X750 AM parts?
For powder bed fusion processes like L-PBF and EBM, Inconel X750 parts typically have 8-12 μm surface roughness as-built. Additional finishing like grinding, milling, EDM can further improve finish. DED parts usually need extensive machining to final tolerances.
Get Latest Price
About Met3DP
Product Category
HOT SALE
CONTACT US
Any questions? Send us message now! We’ll serve your request with a whole team after receiving your message.
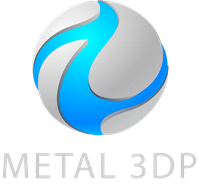
Metal Powders for 3D Printing and Additive Manufacturing