S2 Powder
S2 powder is a high speed tool steel powder ideal for making cutting tools requiring high hardness, strength, and wear resistance at elevated temperatures. It contains tungsten, molybdenum, vanadium, and additional alloys providing excellent hot hardness and thermal fatigue resistance.
Low MOQ
Provide low minimum order quantity to meet different needs.
OEM & ODM
Provide customized products and design services to meet unique customer needs.
Adequate Stock
Ensure fast order processing and provide reliable and efficient service.
Customer Satisfaction
Provide high quality products with customer satisfaction at the core.
share this product
Table of Contents
Overview of S2 Powder
S2 powder is a high speed tool steel powder ideal for making cutting tools requiring high hardness, strength, and wear resistance at elevated temperatures. It contains tungsten, molybdenum, vanadium, and additional alloys providing excellent hot hardness and thermal fatigue resistance.
Key properties and advantages of S2 powder:
S2 Powder Properties and Characteristics
Properties | Details |
---|---|
Composition | Fe-1C-5Cr-2.35Mo-6.4W-1.4V-2Si alloy |
Density | 7.7 g/cc |
Particle shape | Irregular, angular |
Size range | 10-150 microns |
Apparent density | Up to 50% of true density |
Flowability | Low to moderate |
Hardness | 62-64 HRC when heat treated |
Toughness | Very good |
S2 powder produces cutting tools, dies, and machine components with extended service life under continuous high temperature and intermittent shock loading conditions.
S2 Powder Composition
Typical composition of S2 high speed steel powder:
S2 Powder Composition
Element | Weight % |
---|---|
Iron (Fe) | Balance |
Carbon (C) | 0.9-1.2% |
Chromium (Cr) | 3.8-4.5% |
Tungsten (W) | 6.4% |
Molybdenum (Mo) | 1.9-2.2% |
Vanadium (V) | 1.3-1.6% |
Manganese (Mn) | 0.2-0.5% |
Silicon (Si) | 0.9-1.4% |
- Iron provides the ferritic matrix
- Carbon, tungsten, and chromium form hard carbides
- Vanadium and molybdenum enhance wear resistance
- Manganese and silicon facilitate machining
The composition is optimized to achieve an exceptional combination of hot hardness, red hardness, and toughness necessary for high speed machining applications.
S2 Powder Physical Properties
S2 Powder Physical Properties
Property | Values |
---|---|
Density | 7.7 g/cc |
Melting point | 1320-1350°C |
Thermal conductivity | 37 W/mK |
Electrical resistivity | 0.6 μΩ-m |
Maximum service temperature | 600°C |
Curie temperature | 770°C |
- High density enables miniaturized components
- Retains hardness and strength at elevated temperatures
- Becomes paramagnetic above Curie point
- Can withstand prolonged service up to 600°C
- Good thermal conductivity reduces thermal expansion stresses
These properties provide a balanced combination of hot hardness and thermal shock resistance required in high speed machining applications.
S2 Powder Mechanical Properties
S2 Powder Mechanical Properties
Property | Values |
---|---|
Hardness | 62-64 HRC |
Transverse rupture strength | 4500-4800 MPa |
Compressive strength | 3800-4100 MPa |
Tensile strength | 2050-2250 MPa |
Yield strength | 1930-2050 MPa |
Elongation | 8-10% |
Impact toughness | 10-14 J/cm2 |
- Exceptional hardness when heat treated
- High strength with reasonable ductility
- Very good compressive and transverse rupture strength
- Excellent red hardness at elevated temperatures
- Strength depends on heat treatment process
S2 powder produces cutting tools and dies with hardness, strength, and thermal properties needed to machine challenging materials at high speeds and temperatures.
S2 Powder Applications
Typical applications of S2 high speed steel powder include:
S2 Powder Applications
Industry | Example Uses |
---|---|
Automotive | Cutting and milling tools |
Aerospace | Drills, end mills |
Manufacturing | Punches, forming dies |
Oil and gas | Downhole tools, drill bits |
General machining | Turning, boring, and planing tools |
Some specific product uses:
- Cutting inserts, indexable tooling
- Broaches, reamers, taps, threading dies
- Metal slitting saws and industrial knives
- Extrusion tooling and drawing dies
- Cold heading and forging dies
- Gauges, wear-resistant components
S2’s unique properties make it the top choice for reliable cutting tools and components used in demanding metalworking applications.
S2 Powder Specifications
Key specifications for S2 high speed steel powder:
S2 Powder Standards
Standard | Description |
---|---|
ASTM A600 | Specification for tool steels high speed steel |
JIS G4403 | High speed tool steels |
DIN 1.2363 | Equivalent to AISI S7 high speed steel |
UNS T11302 | Designation for AISI S2 grade |
ISO 4957 | Tool steels specification |
These define:
- Chemical composition limits of S2
- Required mechanical properties in heat treated condition
- Approved production methods like gas atomization
- Compliance testing protocols
- Quality assurance requirements
- Proper packaging and identification
Powder produced to these standards ensures suitability for high wear resistance tooling applications under thermal fatigue conditions.
S2 Powder Particle Sizes
S2 Powder Particle Size Distribution
Particle Size | Characteristics |
---|---|
10-22 microns | Ultrafine grade provides highest density |
22-53 microns | Most commonly used size range |
53-105 microns | Coarser size provides good flowability |
- Finer particles allow greater densification during sintering
- Coarser particles improve powder flow into die cavities
- Size is selected based on final part properties needed
- Both gas and water atomized particles used
Controlling size distribution optimizes pressing behavior, sintered density, and final component performance.
S2 Powder Apparent Density
S2 Powder Apparent Density
Apparent Density | Details |
---|---|
Up to 50% of true density | For irregular powder morphology |
4.0-5.0 g/cc | Higher for spherical, lower for irregular powder |
- Spherical powder shape provides high apparent density
- Irregular powder has lower density around 45-50%
- Higher apparent density improves die filling and part quality
- Allows complex tool geometry compaction
Higher apparent density leads to better component production rate and performance.
S2 Powder Production Method
S2 Powder Production
Method | Details |
---|---|
Gas atomization | High pressure inert gas breaks up molten alloy stream into fine droplets |
Vacuum induction melting | High purity input materials melted under vacuum |
Multiple remelting | Enhances chemical homogeneity |
Sieving | Classifies powder into different particle size fractions |
- Gas atomization provides spherical powder shape
- Vacuum melting eliminates gaseous impurities
- Multiple remelting improves uniformity
- Post-processing allows particle size customization
Fully automated processes combined with strict quality control ensures reliable and consistent S2 powder properties critical for tooling performance.
S2 Powder Pricing
S2 Powder Pricing
Factor | Impact on Price |
---|---|
Purity level | Higher purity grades cost more |
Particle size | Ultrafine powder more expensive |
Order quantity | Price decreases with larger volumes |
Additional services | Customization adds cost |
Indicative Pricing
- S2 spherical powder: $18-22 per kg
- S2 irregular powder: $12-16 per kg
- Large volume pricing up to 30% lower
Pricing depends on purity, particle characteristics, order quantity, and any additional customization requirements.
S2 Powder Suppliers
S2 Powder Suppliers
Company | Location |
---|---|
Höganäs | Sweden |
Carpenter Powder Products | USA |
Erasteel | USA, Europe |
Crucible Industries | USA |
voxco | Germany |
Jingdong New Materials | China |
Key supplier selection factors:
- Powder grades offered
- Production capacity
- Particle characteristics and consistency
- Testing capability and quality control
- Pricing and lead times
- Technical customer service
S2 Powder Handling and Storage
S2 Powder Handling
Recommendation | Reason |
---|---|
Ensure proper ventilation | Prevent exposure to fine metal particles |
Use appropriate PPE | Avoid ingestion through nose/mouth |
Ground equipment | Prevent static sparking |
Avoid ignition sources | Flammable dust hazard |
Use non-sparking tools | Prevent possibility of ignition |
Follow safe protocols | Reduce fire, explosion, health risks |
Storage Recommendations
- Store sealed containers away from moisture or contamination
- Maintain storage temperatures below 27°C
- Limit exposure to oxidizing acids and chlorine compounds
Proper precautions during handling and storage help preserve purity and prevent safety hazards.
S2 Powder Inspection and Testing
S2 Powder Testing
Test | Details |
---|---|
Chemical analysis | Verifies composition using optical/ICP spectroscopy |
Particle size analysis | Determines size distribution using laser diffraction or sieving |
Apparent density | Measured as per ASTM B212 using Hall flowmeter |
Powder morphology | SEM imaging to determine particle shape |
Flow rate test | Gravity flow rate through specified funnel |
Tap density test | Density measured after mechanically tapping powder sample |
Testing ensures the powder meets the required chemical composition, physical characteristics, particle size distribution, morphology, density, and flow rate specifications.
S2 Powder Pros and Cons
Advantages of S2 Powder
- Exceptional hot hardness and red hardness
- High strength and wear resistance at elevated temperatures
- Good toughness and thermal shock resistance
- Resists softening and shape changes up to 600°C
- Dimensional stability under thermal cycling
- Cost-effective compared to exotic PM tool steel grades
Limitations of S2 Powder
- Moderate corrosion resistance without surface treatment
- Limited cold formability and shear strength
- Requires careful heat treatment by experienced providers
- Not weldable using conventional fusion welding
- Large cross-sections can experience embrittlement
- Contains expensive alloying elements
Comparison With H13 Tool Steel Powder
S2 vs H13 Tool Steel Powder
Parameter | S2 | H13 |
---|---|---|
Hardness | 62-64 HRC | 54-57 HRC |
Hot hardness | Excellent | Good |
Toughness | Very good | Good |
Thermal shock resistance | Excellent | Moderate |
Cold strength | Good | Excellent |
Cost | High | Low |
- S2 has much greater hot hardness and thermal shock resistance
- H13 provides better cold strength and toughness
- S2 is more expensive due to higher alloy content
- S2 preferred for high speed machining applications
- H13 suited for cold and warm pressing tooling
S2 Powder FAQs
Q: What are the main applications of S2 tool steel powder?
A: Main applications include cutting tools like drills, mills, inserts, taps, dies, saws, planing tools, as well as extrusion tooling, forging dies, gauges, and components needing hot hardness and thermal shock resistance.
Q: What heat treatment is used for S2 tool steel powder?
A: S2 tool steel is typically heat treated by austenitizing between 1150-1200°C followed by air, oil, or polymer quenching, then tempering between 540-650°C to achieve hardness between 62-64 HRC.
Q: How does tungsten improve the properties of S2 steel?
A: Tungsten forms hard tungsten-iron-carbon complexes that provide exceptional hot hardness, strength and wear resistance at elevated temperatures needed for high speed machining applications.
Q: What safety precautions should be used when working with S2 powder?
A: Proper ventilation, protective gear, inert atmosphere, grounding, avoiding ignition sources, using non-sparking tools, and safe storage away from contamination or moisture.
Get Latest Price
About Met3DP
Product Category
HOT SALE
CONTACT US
Any questions? Send us message now! We’ll serve your request with a whole team after receiving your message.
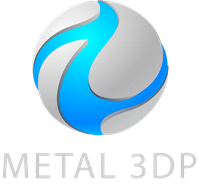
Metal Powders for 3D Printing and Additive Manufacturing