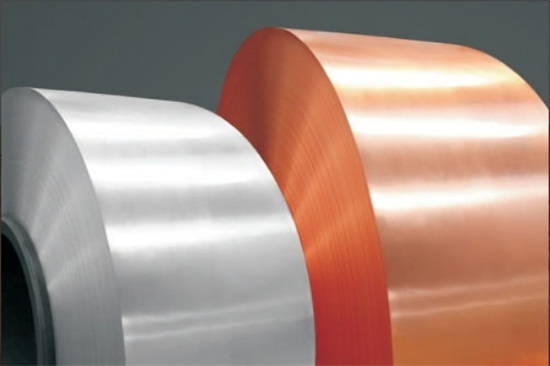
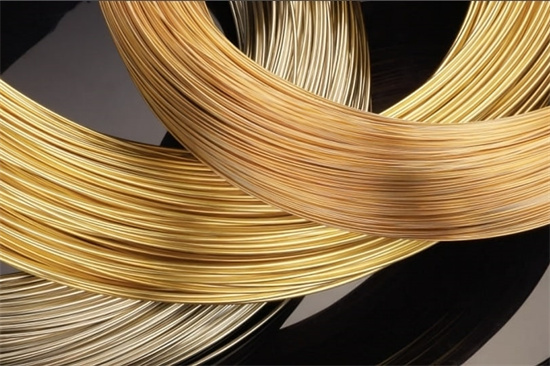
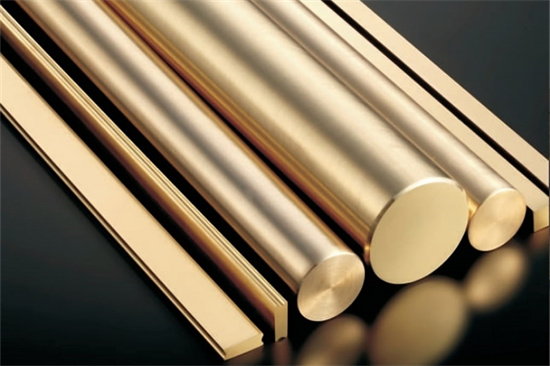
Revolutionary Copper Alloy for Precision Moulds: Unbeatable Properties
Low MOQ
Provide low minimum order quantity to meet different needs.
OEM & ODM
Provide customized products and design services to meet unique customer needs.
Adequate Stock
Ensure fast order processing and provide reliable and efficient service.
Customer Satisfaction
Provide high quality products with customer satisfaction at the core.
share this article
Table of Contents
Wen it comes to precision moulds, the choice of material can make or break the production process. If you’re in the manufacturing or tooling industry, you’ve probably come across copper alloys. Known for their high thermal conductivity, excellent machinability, and resistance to wear, copper alloys are a popular choice for precision moulds.
Whether you’re crafting moulds for plastic injection, die casting, or blow moulding, copper alloys offer a unique blend of properties that give them an edge over other materials like steel or aluminum. But what exactly makes them so effective? Why are industries increasingly turning to copper alloys for their moulding processes? Let’s dive deep into the world of copper alloy for precision moulds, exploring their composition, properties, applications, and more.
Overview of Copper Alloy for Precision Moulds
Copper alloys have gained significant popularity in the precision mould industry due to their ability to dissipate heat rapidly, reducing cycle times and improving overall production efficiency. Unlike steel moulds, which can trap heat and lead to warping or degradation of delicate parts, copper alloys help maintain dimensional accuracy and surface quality by minimizing thermal stress.
Key Characteristics of Copper Alloy for Precision Moulds
- High Thermal Conductivity: Copper alloys dissipate heat faster than steel, reducing cycle times and increasing production efficiency.
- Excellent Wear Resistance: Copper alloys are highly resistant to wear, extending the lifespan of moulds and reducing maintenance costs.
- Outstanding Machinability: Copper alloys are easier to machine than other materials, making complex mould designs more feasible.
- Corrosion Resistance: Copper alloys, especially those with additional elements like nickel or beryllium, are resistant to corrosion, making them suitable for high-humidity or chemically aggressive environments.
- Toughness and Strength: Despite being softer than steel, certain copper alloys, such as beryllium copper, offer exceptional strength and durability.
Types, Composition, and Properties of Copper Alloy for Precision Moulds
Copper alloys come in various forms, each offering distinct mechanical properties and thermal performance. Depending on the moulding process (e.g., injection moulding, die casting), different alloys may be more suitable. Let’s explore the most commonly used copper alloys in precision moulding.
Common Types and Composition of Copper Alloy for Precision Moulds
Alloy Type | Primary Composition | Key Properties | Common Applications |
---|---|---|---|
Beryllium Copper (BeCu) | Copper (96-98%), Beryllium (1.5-2%) | High strength, excellent wear resistance, outstanding thermal conductivity, corrosion resistance. | Injection moulds, blow moulding, die casting. |
Copper-Nickel (CuNi) | Copper (70-90%), Nickel (10-30%) | Excellent corrosion resistance, good thermal and electrical conductivity, moderate strength. | Marine moulds, chemical environments, high wear. |
Brass (Cu-Zn Alloy) | Copper (60-70%), Zinc (30-40%) | Good machinability, moderate strength, lower corrosion resistance compared to other copper alloys. | Low-complexity moulds, low-cost applications. |
Aluminum Bronze | Copper (88-92%), Aluminum (6-12%) | Good wear resistance, high strength, moderate corrosion resistance, excellent thermal conductivity. | Heavy-duty moulds, die casting, marine applications. |
Phosphor Bronze | Copper (85-90%), Tin (5-10%), Phosphorus (<1%) | High fatigue resistance, good strength, excellent wear resistance, moderate thermal conductivity. | High-precision moulds, electrical connectors. |
Beryllium Copper (BeCu)
Beryllium copper is perhaps the most well-known copper alloy used in precision moulds. It offers a remarkable combination of strength, hardness, and thermal conductivity. The high thermal conductivity of beryllium copper allows for rapid heat transfer, making it an ideal choice for injection moulds where fast cooling times are essential.
Copper-Nickel Alloys (CuNi)
Copper-nickel alloys are valued for their excellent corrosion resistance, especially in marine or chemical environments. While they don’t match the strength of beryllium copper, the balance of thermal performance and corrosion resistance makes them a good choice for specialized moulding applications.
Applications of Copper Alloy for Precision Moulds
Copper alloys are used in a wide range of precision moulding applications, thanks to their thermal properties, wear resistance, and machinability. Different copper alloys are chosen depending on the specific moulding process, whether it’s plastic injection moulding, die casting, or blow moulding.
Common Applications of Copper Alloy in Precision Moulds
Application | Copper Alloy Used | Why It’s Used |
---|---|---|
Plastic Injection Moulding | Beryllium Copper | High thermal conductivity reduces cycle times, excellent wear resistance ensures longevity. |
Blow Moulding | Beryllium Copper, Aluminum Bronze | Fast cooling properties lead to high-quality finishes, high strength supports complex mould designs. |
Die Casting | Aluminum Bronze, BeCu | Withstands high temperatures and pressure, excellent wear resistance in high-friction environments. |
Compression Moulding | Phosphor Bronze, Copper-Nickel | Corrosion resistance and strength make these alloys ideal for demanding conditions like chemical exposure. |
Marine Moulds | Copper-Nickel Alloy | Outstanding resistance to saltwater corrosion, good thermal conductivity for moulding in marine environments. |
Automotive Moulds | BeCu, Aluminum Bronze | High strength and wear resistance, combined with fast heat dissipation, make these alloys perfect for automotive parts. |
Plastic Injection Moulding
In plastic injection moulding, the primary challenge is achieving fast cycle times while maintaining dimensional accuracy. Beryllium copper shines here due to its exceptional thermal conductivity, which allows the mould to cool quickly and evenly, preventing warping and distortion in the finished parts.
Die Casting
For die casting applications, moulds are subjected to high temperatures and intense wear. Aluminum bronze and beryllium copper are known for their ability to withstand these extreme conditions while maintaining structural integrity.
Specifications, Sizes, and Standards for Copper Alloy in Moulds
When selecting a copper alloy for precision moulds, it’s critical to adhere to industry standards and specifications. These standards ensure the material meets the necessary mechanical properties, thermal performance, and dimensional tolerances required for high-quality mould production.
Common Specifications, Sizes, and Industry Standards for Copper Alloys
Alloy Type | Standard Sizes Available | Industry Standards for Moulds |
---|---|---|
Beryllium Copper (BeCu) | Bars: Ø 10 mm to Ø 300 mm, Plates: 10 mm to 150 mm thick | ASTM B196, ASTM B194, DIN 17666, ISO 428 |
Aluminum Bronze | Bars: Ø 20 mm to Ø 200 mm, Sheets: 2 mm to 50 mm thick | ASTM B150, BS EN 12163, ISO 1338 |
Phosphor Bronze | Rods: Ø 8 mm to Ø 100 mm, Plates: 5 mm to 100 mm thick | ASTM B139, BS EN 1652, ISO 437 |
Copper-Nickel Alloys | Tubes: Ø 12 mm to Ø 500 mm, Plates: 5 mm to 100 mm thick | ASTM B466, BS EN 12449, ISO 6207 |
Brass (Cu-Zn Alloy) | Rods: Ø 5 mm to Ø 200 mm, Plates: 1 mm to 50 mm thick | ASTM B36, DIN 17660, BS 2870 |
These standards ensure dimensional accuracy, chemical composition, and mechanical performance are consistent across different suppliers. For example, ASTM B196 covers the specifications for beryllium copper bar and wire, ensuring the alloy meets the necessary hardness and strength requirements for precision moulds.
Suppliers and Pricing of Copper Alloy for Precision Moulds
The price of Copper Alloy for Precision Moulds used in moulds can vary significantly based on the type of alloy, form (bars, sheets, rods), and order quantity. Additionally, market fluctuations in the prices of copper, beryllium, aluminum, and other alloying elements can impact costs.
Leading Suppliers and Pricing Estimates for Copper Alloys
Supplier | Location | Alloy Types Available | Price per kg (estimate) | Minimum Order Quantity |
---|---|---|---|---|
Materion Corporation | USA, Global | Beryllium Copper, Phosphor Bronze | $25 – $50 | 10 kg |
Aviva Metals | USA | Beryllium Copper, Brass, Aluminum Bronze | $20 – $45 | 20 kg |
Shanghai Metal Corporation | China | Copper-Nickel, Brass | $10 – $25 | 50 kg |
KME Germany GmbH | Germany | Phosphor Bronze, Copper-Nickel | $15 – $40 | Varies by order |
Lebronze Alloys | France | Beryllium Copper, Aluminum Bronze | $30 – $55 | Custom orders |
Prices for beryllium copper can be notably higher due to the toxicity and special handling requirements of beryllium. On the lower end, brass and copper-nickel alloys are more affordable but may lack the thermal and mechanical properties necessary for high-performance moulds.
Comparing the Pros and Cons of Copper Alloy for Precision Moulds
Choosing the right Copper Alloy for Precision Moulds for your precision mould requires weighing the advantages and limitations of each option. Let’s break down the pros and cons of the most commonly used copper alloys.
Advantages and Limitations of Copper Alloy for Precision Moulds
Copper Alloy | Advantages | Limitations |
---|---|---|
Beryllium Copper (BeCu) | High strength, excellent wear resistance, superior thermal conductivity. | Expensive, requires special handling due to beryllium toxicity. |
Aluminum Bronze | Good wear resistance, high strength, excellent for high-temperature applications. | Lower thermal conductivity than beryllium copper, moderate cost. |
Phosphor Bronze | High fatigue resistance, good wear properties, excellent machinability. | Lower thermal conductivity, moderate strength compared to other alloys. |
Copper-Nickel Alloy | Excellent corrosion resistance, moderate strength, good machinability. | Lower thermal conductivity, higher cost compared to brass. |
Brass (Cu-Zn Alloy) | Affordable, good machinability, moderately strong. | Lower corrosion resistance, not suitable for high-temperature applications. |
Beryllium Copper vs. Aluminum Bronze
When comparing beryllium copper to aluminum bronze, the key difference is in thermal conductivity. Beryllium copper is the go-to choice if rapid heat dissipation is critical to the moulding process. However, aluminum bronze offers better wear resistance in high-temperature environments, making it ideal for die casting.
Phosphor Bronze vs. Copper-Nickel
For applications requiring high fatigue resistance and corrosion resistance, phosphor bronze and copper-nickel alloys are excellent options. However, phosphor bronze tends to excel in machinability, while copper-nickel shines in marine environments due to its superior corrosion resistance.
FAQs About Copper Alloy for Precision Moulds
Question | Answer |
---|---|
Why are copper alloys used in precision moulds? | Copper Alloy for Precision Moulds offer high thermal conductivity, wear resistance, and machinability, making them ideal for moulding applications. |
What is the best copper alloy for injection moulding? | Beryllium copper is widely considered the best for injection moulding due to its superior thermal properties. |
How much does copper alloy for moulds cost? | Prices range from $10 to $55 per kg, depending on the alloy type and supplier. |
Can Copper Alloy for Precision Moulds be used in high-temperature moulding? | Yes, Copper Alloy for Precision Moulds like aluminum bronze and beryllium copper can withstand high temperatures, making them suitable for die casting. |
Are Copper Alloy for Precision Moulds corrosion-resistant? | Many Copper Alloy for Precision Moulds, such as copper-nickel, offer excellent corrosion resistance, especially in marine or chemical environments. |
Conclusion
When it comes to precision moulds, copper alloys are an outstanding choice for a wide range of applications. From plastic injection moulding to die casting, copper alloys provide the perfect balance of thermal conductivity, strength, and wear resistance. Whether you’re looking to reduce cycle times, increase mould longevity, or simply improve the quality of your final products, copper alloys are a versatile and high-performance solution.
By understanding the types, properties, and applications of copper alloys, you can make informed decisions on the best material for your precision moulding processes. Whether it’s the superior thermal performance of beryllium copper or the corrosion resistance of copper-nickel alloys, there’s a copper alloy out there to meet your specific needs.
Maybe you want to know more about our products, please contact us
Get Latest Price
About Met3DP
Product Category
HOT SALE
CONTACT US
Any questions? Send us message now! We’ll serve your request with a whole team after receiving your message.