Metal powders suitable for SLM technology
Table of Contents
Selective Laser Melting (SLM) has revolutionized manufacturing, enabling the creation of complex, high-performance metallic parts directly from digital models. But at the heart of this technology lies a crucial ingredient: metal powder. Just like the quality of flour impacts the final cake, the right metal powder plays a pivotal role in the success of an SLM project. So, buckle up as we delve into the fascinating world of SLM metal powders, exploring their types, properties, applications, and the nitty-gritty details that matter.
The Types of Metal Powders that can be used in SLM technology
Imagine a treasure chest overflowing with metallic grains, each one a tiny building block for creating intricate 3D objects. SLM metal powders come in a diverse range, each offering unique properties and functionalities. Here are some of the most common types:
Table: Common Types of Metal Powders for SLM
Metal/Alloy | Composition | Key Properties | Applications |
---|---|---|---|
Stainless Steel 316L | Fe (base), 16-18% Cr, 10-14% Ni, 2-3% Mo | Excellent corrosion resistance, good mechanical strength, biocompatible | Medical implants, chemical processing equipment, aerospace components |
Titanium Grade 2 (CP Ti) | 99.2% Ti (min) | High strength-to-weight ratio, excellent biocompatibility, good corrosion resistance | Aerospace parts, biomedical implants, sporting goods |
Inconel 625 (Nickel Superalloy) | Ni (base), 20-24% Cr, 9-13% Fe, ~5% Mo | Exceptional high-temperature strength, oxidation resistance | Gas turbine components, rocket engine parts, heat exchangers |
Aluminum AlSi10Mg | Al (base), 9-11% Si, 0.3-0.6% Mg | Lightweight, good strength, high corrosion resistance | Automotive parts, aerospace components, electronics enclosures |
Tool Steel (e.g., H13) | Fe (base), ~5% Cr, 1.3% Mo, ~4% V | High hardness, wear resistance, good thermal stability | Dies, molds, cutting tools |
Cobalt-Chrome (CoCr) | Co (base), 20-30% Cr | High wear resistance, biocompatible | Joint replacements, dental prosthetics |
Copper | Cu (min. 99.5%) | Excellent thermal and electrical conductivity | Heat sinks, electrical components, waveguides |
Tungsten | W | High melting point, good density | Electrodes, armor components (limited applications due to processing challenges) |
This table just scratches the surface! Researchers are constantly developing new metal powder alloys with tailored properties for specific applications.
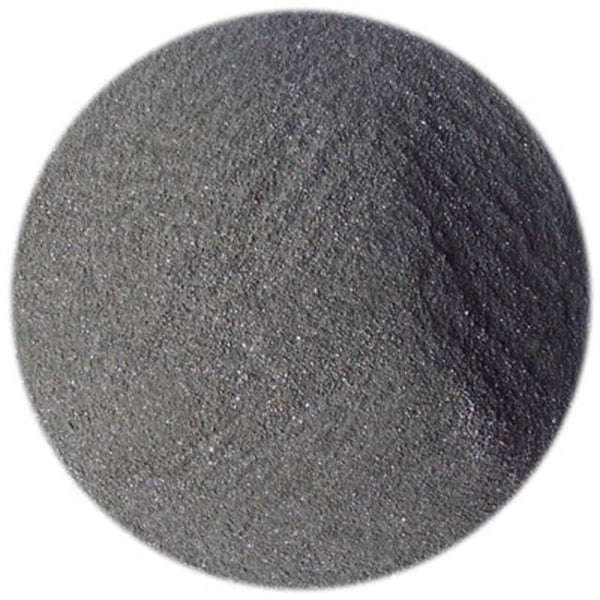
Factors to Consider When Selecting SLM Metal Powder
Choosing the right SLM metal powder is akin to selecting the perfect paintbrush for your masterpiece. Several factors influence this decision:
- Material Properties: Consider the desired properties of the final part, such as strength, weight, corrosion resistance, and operating temperature. Different metals offer unique combinations of these properties.
- Powder Characteristics: Particle size, flowability, and spherical shape are crucial. Consistent particle size ensures uniform melting, while good flowability allows for even powder bed deposition. Spherical particles promote better laser absorption and minimize spatter during the SLM process.
- Laser Compatibility: The powder’s absorption characteristics and melting point must be compatible with the SLM machine’s laser wavelength and power output.
- Cost: Metal powders can vary significantly in price. Consider the trade-off between material cost and the desired performance of the final part.
- Availability: Not all powders are readily available. Lead time and supplier reliability are essential factors.
By carefully considering these factors, you can select the ideal SLM metal powder to bring your 3D printing vision to life.
the Applications OF SLM
Industry | Application Examples | Benefits of Using SLM |
---|---|---|
Aerospace | Lightweight aircraft components, rocket engine parts, satellite structures | Reduced weight for increased fuel efficiency, complex geometries for improved performance |
Medical | Custom-designed implants, surgical instruments, prosthetics | Biocompatible materials for improved patient outcomes, personalized implants for better fit and function |
Automotive | Lightweight wheels, customized gears | Weight reduction for better fuel economy, design freedom for optimized performance |
Tooling & Manufacturing | Complex molds and dies, customized cutting tools | Conformal cooling channels for improved efficiency, reduced lead times for tool production |
Consumer Goods | High-end jewelry, sporting goods components, customized bicycle frames | Unique designs and intricate details, lightweight and high-strength parts |
Energy | Heat exchangers, turbine blades | Optimized designs for improved efficiency, components resistant to high temperatures and harsh environments |
These are just a few examples, and the potential applications of SLM metal powders are constantly expanding. As the technology matures and powder costs decrease, we can expect to see even more innovative applications emerge across various industries.
Market Price of SLM Metal Powder
The cost of SLM metal powder can vary significantly depending on several factors:
- Material: Exotic or high-performance alloys like Inconel 625 typically command a premium price compared to common materials like stainless steel 316L.
- Powder Characteristics: Powders with tighter particle size distribution and higher sphericity often come at a higher cost due to the additional processing involved.
- Quantity: Bulk purchases typically offer lower prices per kilogram compared to smaller quantities.
- Supplier: Market competition and a supplier’s production capacity can influence pricing.
Table: Estimated Price Range of Common SLM Metal Powders (per Kg)
Metal/Alloy | Price Range (USD) |
---|---|
Stainless Steel 316L | $50 – $100 |
Titanium Grade 2 (CP Ti) | $100 – $200 |
Inconel 625 (Nickel Superalloy) | $200 – $400 |
Aluminum AlSi10Mg | $30 – $50 |
It’s important to remember that the cost of metal powder is just one piece of the puzzle. Factors like machine depreciation, labor costs, and post-processing expenses also contribute to the overall cost of producing an SLM part.
A Closer Look: Spotlight on Specific Metal Powders
Delving deeper, let’s explore some specific metal powders and their unique characteristics:
- Stainless Steel 316L: A versatile and widely used powder known for its excellent corrosion resistance, good mechanical strength, and biocompatibility. It’s a popular choice for applications in the medical, chemical processing, and aerospace industries. However, its laser reflectivity can be higher compared to some other metals, requiring adjustments in SLM machine parameters.
- Titanium Grade 2 (CP Ti): This biocompatible and lightweight powder is ideal for aerospace components and medical implants due to its high strength-to-weight ratio and excellent corrosion resistance. However, titanium has a higher melting point compared to steel, necessitating higher laser power for processing, which can lead to higher energy consumption during SLM.
- Inconel 625: A champion in high-temperature environments, Inconel 625 powder boasts exceptional resistance to oxidation and creep. This nickel-based superalloy is the go-to material for gas turbine components, rocket engine parts, and heat exchangers. The downside? Its high cost and challenging processing characteristics due to its high melting point and flowability issues.
- Aluminum AlSi10Mg: A lightweight and cost-effective option, Aluminum AlSi10Mg powder offers a good balance of strength and corrosion resistance. This makes it a popular choice for automotive parts, aerospace components, and electronic enclosures. However, aluminum can be reflective towards the SLM laser, requiring careful parameter optimization to achieve proper melting and minimize porosity in the final part.
These are just a few examples, and the choice of metal powder ultimately depends on the specific application requirements and desired part properties.
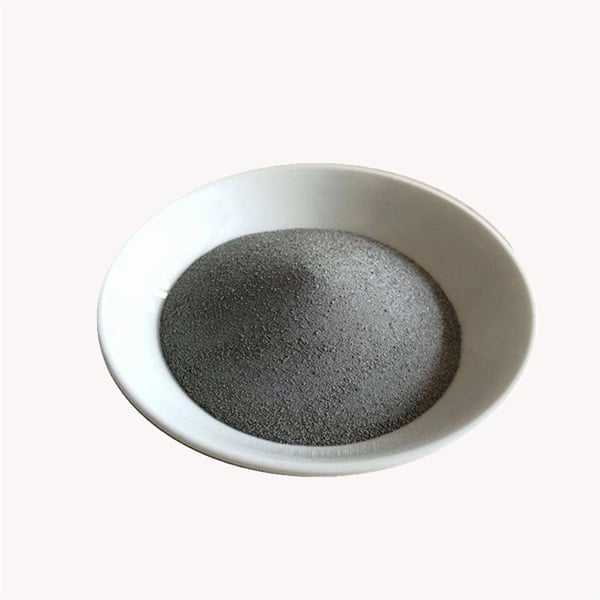
Advantages and Limitations of SLM Metal Powders
Advantages:
- Design Freedom: SLM allows for the creation of complex geometries that are impossible to achieve with traditional manufacturing techniques.
- High Performance: SLM parts can be incredibly strong, lightweight, and resistant to corrosion and high temperatures, making them ideal for demanding applications.
- Mass Customization: The ability to produce parts directly from digital models facilitates rapid prototyping and customization for individual needs.
- Material Efficiency: SLM offers minimal material waste compared to traditional subtractive manufacturing techniques.
Limitations (Continued):
- Cost: SLM machines and metal powders can be expensive, making this technology less suitable for high-volume production of simple parts.
- Surface Roughness: SLM parts can have a slightly rough surface finish compared to machined parts. Post-processing techniques like polishing or blasting may be required for certain applications.
- Residual Stress: The SLM process can introduce residual stress into the parts, potentially impacting their mechanical performance. Proper heat treatment strategies can help mitigate this issue.
- Limited Material Selection: While the range of SLM metal powders is expanding, it’s still not as vast as materials available in traditional manufacturing methods.
Despite these limitations, SLM technology offers significant advantages for creating high-performance, complex parts. As the technology matures and costs decrease, we can expect SLM to become even more widely adopted across various industries.
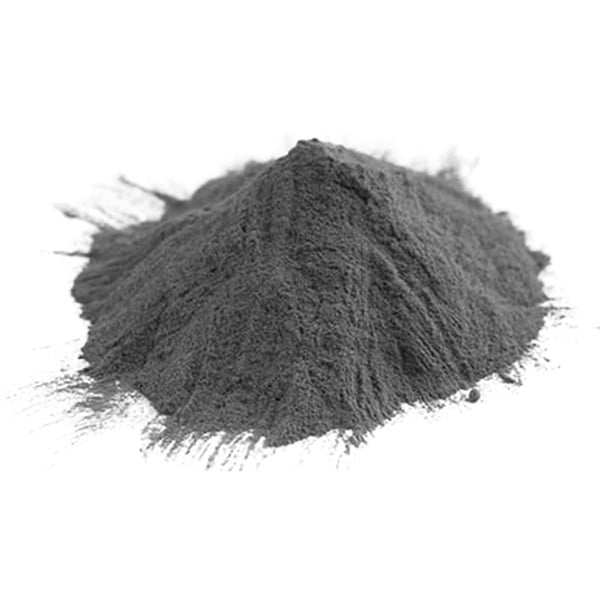
FAQ
Here are some frequently asked questions regarding metal powders for Selective Laser Melting (SLM):
Q: What are the different sizes of metal powder available for SLM?
A: The typical size range for SLM metal powders falls between 15 and 100 microns. The optimal particle size depends on the specific metal and the desired properties of the final part. Finer powders generally offer better surface finish but can be less flowable and more challenging to process.
Q: How are SLM metal powders manufactured?
A: Several methods are used to produce SLM metal powders, including gas atomization, water atomization, and plasma atomization. These processes involve melting the desired metal and then rapidly breaking it down into fine particles using a pressurized gas, water, or plasma stream.
Q: Can I recycle SLM metal powder?
A: Yes, in some cases, unused SLM metal powder can be recycled and reused. However, the recycling process needs to be carefully controlled to ensure the powder maintains its original properties and doesn’t introduce contamination into subsequent builds.
Q: Where can I buy SLM metal powder?
A: Several companies around the world specialize in supplying metal powders for SLM applications. It’s crucial to choose a reputable supplier that offers high-quality powders with proper certifications and material safety data sheets (MSDS).
Q: What are the safety considerations when handling SLM metal powders?
A: Metal powders can be flammable and pose health risks if inhaled. Proper handling procedures, including using a fume hood and personal protective equipment (PPE) like gloves and respirators, are essential when working with SLM metal powders.
By understanding these key aspects of metal powders, you can make informed decisions when venturing into the exciting world of Selective Laser Melting technology.
Share On
MET3DP Technology Co., LTD is a leading provider of additive manufacturing solutions headquartered in Qingdao, China. Our company specializes in 3D printing equipment and high-performance metal powders for industrial applications.
Inquiry to get best price and customized Solution for your business!
Related Articles
About Met3DP
Recent Update
Our Product
CONTACT US
Any questions? Send us message now! We’ll serve your request with a whole team after receiving your message.
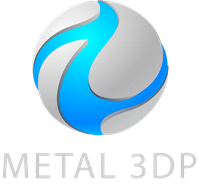
Metal Powders for 3D Printing and Additive Manufacturing