Introduction to Titanium Alloys Powder
Table of Contents
Titanium alloys powder is a versatile engineered material with unique properties that make it suitable for advanced applications across industries. This article provides an overview of titanium alloys powder metallurgy, manufacturing methods, compositions, mechanical and physical properties, applications, specifications, pricing, pros and cons, and frequently asked questions.
Titanium Alloys Powder Manufacturing Methods
Titanium alloys powder can be produced through various methods that impact powder characteristics like particle size distribution, morphology, purity levels, and more. The main manufacturing routes include:
Method | Description | Typical Powder Characteristics |
---|---|---|
Gas Atomization | Liquid alloy stream disintegrated by high pressure gas jets into fine droplets that solidify into powder | Spherical morphology, medium to fine particle sizes (15-180 μm), tailored alloy compositions, high purity |
Plasma Rotating Electrode Process (PREP) | Electrode tip melted by plasma arc, centrifugal force forms microdroplets that solidify into powder | Spheroidal particles, very fine powder (25-75 μm), medium purity, wide alloy options |
Hydride-Dehydride (HDH) | Alloy hydride formation and decomposition process yields porous coarse powder | Irregular morphology, large particle size (75-250 μm), medium to high purity, limited alloys |
Each production method results in titanium alloys powder with distinct characteristics suited to different applications across industries.
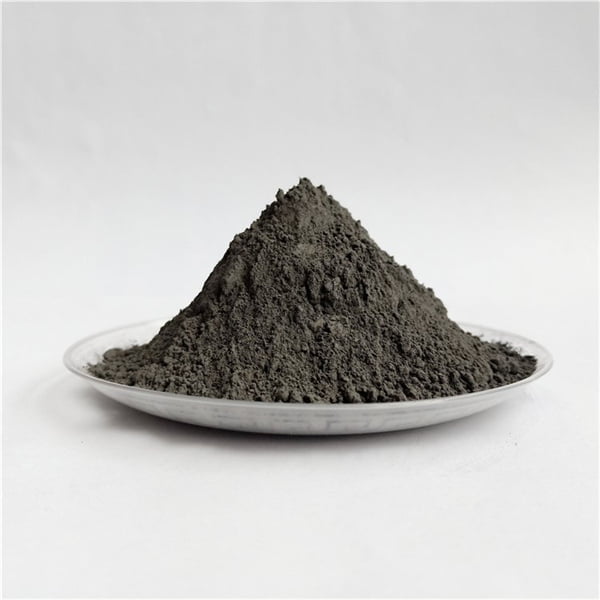
Titanium Alloys Powder Compositions
Titanium alloys powder for metallurgy consists of titanium blended principally with aluminum and vanadium, with trace additions of iron, oxygen, carbon and nitrogen. Common titanium alloys formulations by mass percentage include:
Alloy | Aluminum | Vanadium | Other Elements |
---|---|---|---|
Ti-6Al-4V (Grade 5) | 5.5-6.75% | 3.5-4.5% | Iron ≤ 0.3%, Oxygen ≤ 0.2%, Carbon ≤ 0.1%, Nitrogen ≤ 0.05% |
Ti-6Al-4V ELI (Extra Low Interstitial, Grade 23) | 5.5-6.5% | 3.5-4.5% | Iron ≤ 0.3%, Oxygen ≤ 0.13%, Carbon ≤ 0.08%, Nitrogen ≤ 0.05% |
Ti-10V-2Fe-3Al | 2.5-3.5% | 9-11% | Iron 1.8-2.2%, Oxygen ≤ 0.2%, Carbon ≤ 0.1%, Nitrogen ≤ 0.05% |
The titanium alloys powder chemistry can be tailored to optimize performance profiles from strength and hardness to corrosion resistance, bio-compatibility, high-temperature resistance, weight savings, and other priorities depending on end-use.
Titanium Alloys Powder Properties
Key titanium alloys powder propertiesvalued across applications include:
Property | Ti-6Al-4V | Ti-6Al-4V ELI | Ti-10V-2Fe-3Al |
---|---|---|---|
Density (g/cm3) | 4.42 | 4.42 | 4.35 |
Melting Point (°C) | 1604-1660 | 1604-1660 | 1590-1650 |
Ultimate Tensile Strength (MPa) | 860-1200 | 860-1050 | 900-1150 |
Yield Strength (MPa) | 750-1100 | 760-960 | 800-1050 |
Elongation at Break (%) | 8-15 | 8-12 | 7-14 |
Elastic Modulus (GPa) | 100-115 | 95-115 | 90-110 |
Hardness (HRC) | 30-38 | 32-36 | 30-40 |
The titanium powder alloys offer an advanced property profile combining the light weight of titanium with high strength-to-weight ratio, fracture toughness, fatigue and corrosion resistance suited for critical applications.
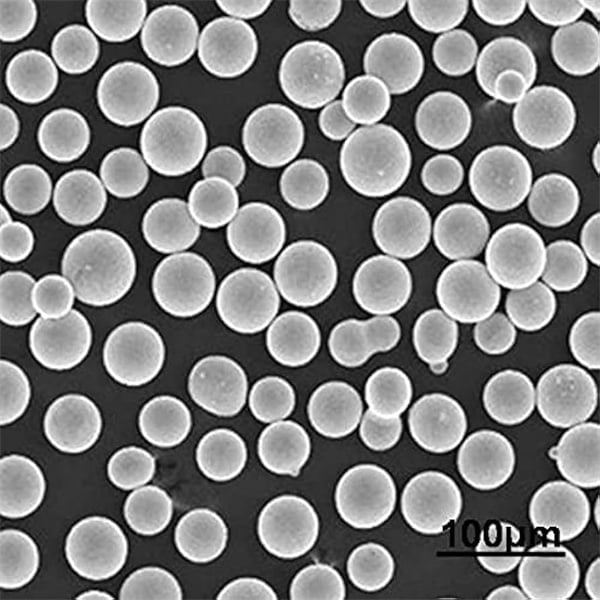
Titanium Alloys Powder Applications
The lightweight strength, biocompatibility and extreme environment resistance make titanium alloys a versatile choice across markets. Typical applications include:
Industry | Applications |
Aerospace | Aircraft engine and structural components, space vehicle structures, rockets |
Medical | Orthopedic and dental implants, surgical instruments, prosthetics |
Automotive | Valves, connecting rods, springs, fasteners, exhaust components |
Chemical | Pumps, valves, pipes, tanks, reaction vessels for corrosion resistance |
Power Generation | Steam and gas turbine blades, offshore platform components |
Sporting Goods | Golf clubs, tennis rackets, bicycles, other high-performance gear |
Oil & Gas | Downhole tubing, offshore rigs, wellhead components |
These demanding environments across sectors take advantage of titanium alloys properties like high strength-to-weight ratio, fatigue resistance, fracture toughness, corrosion resistance and biocompatibility.
Titanium Alloys Powder Specifications
Titanium alloys powders are produced in standardized specifications for chemistry, particle size distribution, morphology and other parameters tailored to additive manufacturing or press-and-sinter needs.
Parameter | Specification |
---|---|
Alloy Grade | Ti-6Al-4V, Ti-6Al-4V ELI, Ti-10V-2Fe-3Al, other grades |
Particle Shape | Spherical, irregular shapes |
Particle Size Range (μm) | 15-45, 45-100, 100-180 preferred for AM |
Hall Flow Rate (s/50g) | >32 seconds, indicating good powder flowability |
Apparent Density (g/cm3) | 2.7-3.2 for spherical, 2.2-2.8 for irregular powder |
Tap Density (g/cm3) | >4.0, improves packing efficiency |
Meeting chemistry assays within allowed limits for oxygen, nitrogen, carbon, iron and other trace elements is critical for high performance powder. These specifications enable processing suitability across AM or press-and-sinter techniques.
Titanium Alloys Powder Comparison
The most widely used titanium alloys powder variants – Ti-6Al-4V, Ti-6Al-4V ELI and Ti-10V-2Fe-3Al grades – have differing property advantages:
Ti-6Al-4V | Ti-6Al-4V ELI | Ti-10V-2Fe-3Al | |
---|---|---|---|
Strength | High strength | Slightly lower strength but better ductility | Strength comparable to Ti-6Al-4V |
Weldability | Moderate | Excellent | Better than Ti-6Al-4V |
Corrosion Resistance | Moderate | Better, for sensitive applications | Superior corrosion resistance |
Cost | Moderate price | Slight cost premium | Lower cost than Ti-6Al-4V alloys |
Biocompatibility | Excellent | Superior for body implants | Less preferred for medical devices |
Ti-6Al-4V ELI grade powder stands out for ductility, weldability, biocompatibility and corrosion resistance but costs more, while Ti-10V-2Fe-3Al excels in corrosion resistance at lower price but loses out in bio-medical suitability compared to the grade 5 and 23 alloys.
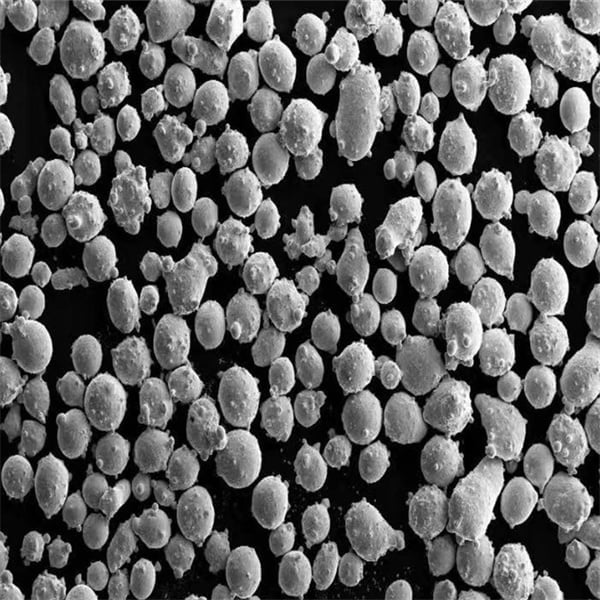
Titanium Alloys Powder Pricing
Titanium alloys powder commands a significant price premium over steel powders due to processing intensiveness and unique properties:
Powder Grade | Price Range (USD per kg) |
---|---|
Ti-6Al-4V | 120 – 160 |
Ti-6Al-4V ELI | 135 – 185 |
Ti-10V-2Fe-3Al | 100 – 165 |
Cost depends on manufacturing method, chemistry, size distribution, shape and order quantities. Irregular powder can be cheaper than spherical. Price premiums for argon or vacuum packaging also apply. Significant volume discounts also lower per-kilo rates.
Titanium Alloys Powder Pros and Cons
Pros | Cons | |
---|---|---|
Mechanical Properties | High strength-to-weight ratio, strong but lightweight | Lower strength than some steel alloys |
Physical Properties | Corrosion resistant, bio-compatible, non-magnetic, thermally conductive | High reactivity with elements like oxygen requiring inert handling |
Processing | Suitability for multiple AM techniques, heat treatment capability | Spherical powder more expensive to make vs. steels |
Performance | Superior fracture toughness, fatigue life, wear resistance | Can suffer hydrogen embrittlement, galling tendencies |
Economics | Big weight savings opportunity | Higher material cost than steel alternatives |
Titanium powder alloys enhance performance but at greater expense. They outpace steels on specific strength as well as environmental endurance but fall behind on absolute strength and cost metrics. Shorter fatigue life, hydrogen uptake and abrasion can also plague certain titanium alloys.
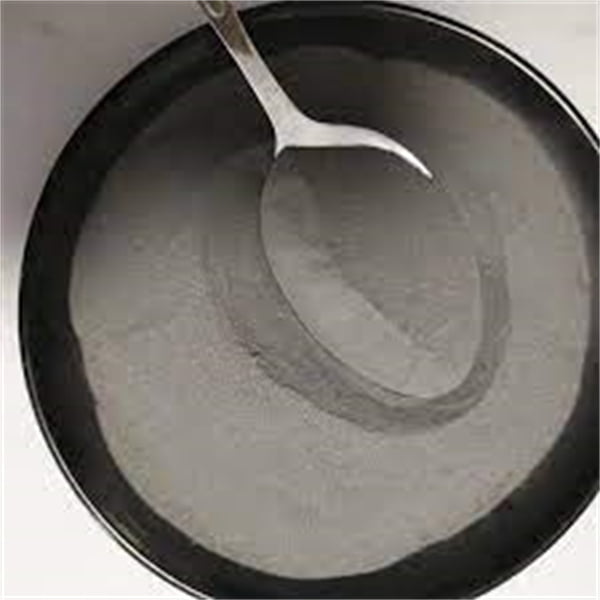
FAQ
Question | Answer |
---|---|
What are the main titanium alloys available in powder form? | The most used titanium alloys powders are Ti-6Al-4V, Ti-6Al-4V ELI and Ti-10V-2Fe-3Al which are manufactured in common AM-ready particle size distributions and compositions. Custom alloys are also possible. |
What particle size range works best for titanium alloys powder bed AM? | A particle size range of 15-100 microns with average size between 30-60 microns is optimal. Too fine leads to challenges in powder handling and spreading. Too coarse can cause less dense parts. |
How is titanium alloys powder stored and handled? | Inert gas purging and minimized exposure to air is critical to avoid picking up oxygen that can alter alloy chemistry. Vacuum sealed containers and argon-filled glove boxes enable effective powder storage and handling. |
What post-processing is used on AM titanium parts? | Heat treatments like hot isostatic pressing and annealing can help improve mechanicals. Surface finishing steps may involve CNC machining, drilling, grinding and polishing. Shot peening is also used to induce compressive stresses. |
Are titanium alloys recyclable after additive manufacturing? | Yes, used titanium powder can often be salvaged, sieved and blended with virgin powder for reuse. Recycling yield rates over 90% are achieved for some titanium alloys, bringing significant cost savings. |
Conclusions
With properties like high specific strength, fatigue and corrosion resistance, titanium alloys powders enable lighter, more durable parts across aerospace, medical, automotive, energy and other demanding applications. Advancements in titanium powder metallurgy are expanding adoption further through optimized powders tailored for AM techniques.
Leading titanium grades Ti-6Al-4V, Ti-6Al-4V ELI and Ti-10V-2Fe-3Al balance properties like strength, ductility, toughness, weldability, bio-compatibility and chemical resistance at attractive pricing. Continued titanium alloys development and progress in metal AM capabilities are set to accelerate utilization of titanium powder for mission-critical components.
Share On
MET3DP Technology Co., LTD is a leading provider of additive manufacturing solutions headquartered in Qingdao, China. Our company specializes in 3D printing equipment and high-performance metal powders for industrial applications.
Inquiry to get best price and customized Solution for your business!
Related Articles
About Met3DP
Recent Update
Our Product
CONTACT US
Any questions? Send us message now! We’ll serve your request with a whole team after receiving your message.
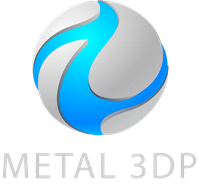
Metal Powders for 3D Printing and Additive Manufacturing
COMPANY
PRODUCT
cONTACT INFO
- Qingdao City, Shandong, China
- [email protected]
- [email protected]
- +86 19116340731