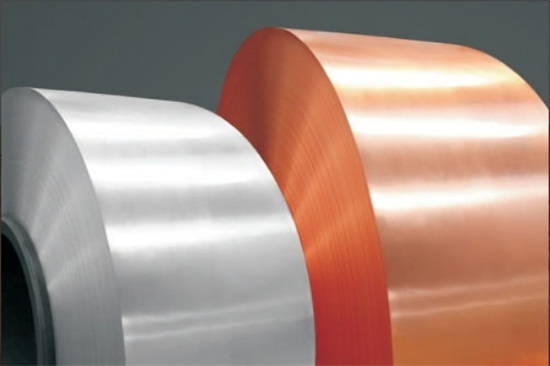
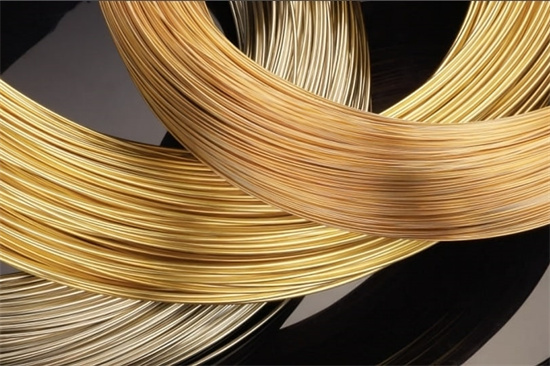
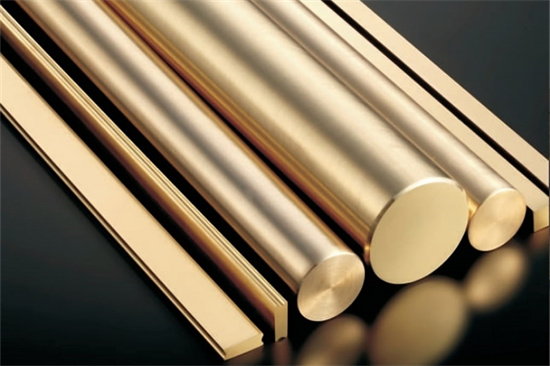
CuCr1: The Durable Copper Alloy You Need for Extreme Conditions
Low MOQ
Provide low minimum order quantity to meet different needs.
OEM & ODM
Provide customized products and design services to meet unique customer needs.
Adequate Stock
Ensure fast order processing and provide reliable and efficient service.
Customer Satisfaction
Provide high quality products with customer satisfaction at the core.
share this article
Table of Contents
Copper alloys are the backbone of many industries, from electronics to automotive and aerospace. But when you need the perfect balance between electrical conductivity, strength, and durability, CuCr1 (Copper-Chromium alloy) is a standout choice. Whether you’re designing high-stress components or working with high-temperature applications, CuCr1 offers a unique combination of properties that make it ideal for some of the most demanding engineering tasks.
In this comprehensive guide, we’ll explore everything you need to know about CuCr1—from its composition and properties to its applications, specifications, pricing, and more. We’ll break down the technical details in a way that’s engaging and easy to understand, so you can decide if CuCr1 is the right material for your next project.
Overview
Let’s start with the basics. CuCr1 is a copper alloy that primarily consists of copper (Cu) and a small amount of chromium (Cr). The addition of chromium greatly enhances the mechanical strength and wear resistance of the alloy without significantly sacrificing electrical conductivity. This makes CuCr1 an excellent choice for applications that require both good conductivity and high mechanical performance.
Key Features
- High Electrical Conductivity: CuCr1 retains a significant portion of copper’s natural conductivity, typically around 80-90% IACS (International Annealed Copper Standard).
- Increased Strength: Thanks to the presence of chromium, CuCr1 offers much higher tensile strength than pure copper, making it suitable for high-stress applications.
- Thermal Stability: CuCr1 performs well under elevated temperatures, making it an ideal choice for electrical contacts, switchgear, and welding electrodes.
- Corrosion and Wear Resistance: The alloy offers better corrosion resistance and wear resistance compared to pure copper, ensuring a longer service life in harsh environments.
- Good Formability: Despite its added strength, CuCr1 remains relatively easy to machine and form, making it versatile in manufacturing processes.
Composition and Properties
Understanding the composition and mechanical properties of CuCr1 is crucial for selecting the right material for your specific needs. Below, we’ll break down the typical chemical composition and physical properties of this alloy.
Composition
The composition of CuCr1 is carefully balanced to maintain a high level of electrical conductivity while improving the material’s strength and durability.
Element | Percentage (%) |
---|---|
Copper (Cu) | 98.85 – 99.25 |
Chromium (Cr) | 0.50 – 1.00 |
Other Elements | <0.15 (e.g., Fe, Si) |
This relatively small amount of chromium (typically between 0.5% and 1.0%) significantly boosts the alloy’s mechanical properties, while the copper base ensures excellent conductivity.
Mechanical and Physical Properties
Here’s a detailed look at the mechanical and physical properties of CuCr1, which make it an ideal choice for a wide range of applications:
Property | Typical Value |
---|---|
Tensile Strength | 350 – 550 MPa |
Yield Strength | 250 – 400 MPa |
Elongation | 10 – 25% |
Hardness | 100 – 150 HB |
Electrical Conductivity | 80 – 90% IACS |
Thermal Conductivity | 300 – 370 W/mK |
Density | 8.9 g/cm³ |
Melting Point | 1083°C |
Coefficient of Expansion | 16.9 x 10⁻⁶ /°C |
Why These Properties Matter
- Tensile and Yield Strength: The higher strength of CuCr1 allows it to handle mechanical stress better than pure copper, making it suitable for high-load electrical contacts and switchgear.
- Electrical Conductivity:it retains excellent electrical properties, making it ideal for uses where both strength and conductivity are required, like in power distribution systems.
- Thermal Conductivity: With a high thermal conductivity, CuCr1 efficiently dissipates heat, which is critical in electrical components that are exposed to high temperatures.
- Formability and Machinability: Despite its added strength, CuCr1 can be machined and formed relatively easily, allowing for complex shapes and precise components.
Applications: Where Is It Used?
The unique combination of high conductivity and strength makes it a go-to material in a variety of industries. Below, we’ll take a closer look at the most common applications of CuCr1.
Common Applications
Industry | Applications |
---|---|
Electrical | Switchgear, circuit breakers, electrical contacts |
Welding | Welding electrodes, resistance welding parts |
Automotive | Connectors, electrical terminals, heat exchangers |
Aerospace | High-temperature connectors, heat-resistant parts |
Power Generation | Turbine blades, generator components |
Industrial Equipment | Molds, tooling, high-temperature furnaces |
Why CuCr1 is Preferred in These Applications
- Electrical Components: It is widely used in switchgear and circuit breakers because it combines good conductivity with high strength, ensuring long-lasting performance even under high loads and frequent switching.
- Welding: In welding electrodes, it offers excellent thermal stability and wear resistance, making it ideal for resistance welding where high temperatures are common.
- Automotive: It is commonly used in automotive electrical systems for connectors and terminals that need to withstand vibration, heat, and corrosion.
- Aerospace: In aerospace applications, it is used in high-temperature connectors and components where thermal stability and strength are critical.
- Power Generation: it is ideal for generator components and turbine blades where the combination of strength and thermal conductivity is needed to handle high stresses and heat.
Specifications, Sizes, and Grades
Selecting the right form, size, and grade of CuCr1 is essential for ensuring optimal performance in your application. Below, we’ll outline the various specifications and grades available for it.
Specifications and Sizes
Specification | Details |
---|---|
Form | Rods, plates, wires, strips, bars |
Diameter Range (Rods) | 1 mm to 150 mm |
Thickness Range (Plates) | 0.5 mm to 50 mm |
Temper | Annealed, cold-worked, hardened |
Standards | ASTM B224, EN 13601, DIN 17666 |
Grades
Grade | Characteristics |
---|---|
CuCr1-Soft (Annealed) | High ductility, suitable for forming |
CuCr1-Hard (Cold-Worked) | Increased strength, suitable for high-load |
CuCr1-Extra Hard | Maximum strength, ideal for wear-intensive applications |
Choosing the Right Grade
The grade of CuCr1 you choose will depend on your application requirements. For example, CuCr1-Soft is easier to work with and form into complex shapes, while CuCr1-Hard or Extra Hard offers superior strength for high-stress components.
Suppliers and Pricing
When sourcing CuCr1, it’s important to consider both quality and cost. Below is a list of trusted suppliers along with estimated pricing to give you a ballpark figure of what to expect.
Suppliers and Pricing Details
Supplier | Location | Price Range (per kg) | Delivery Time |
---|---|---|---|
Metal Supermarkets | USA | $25 – $40 | 1-2 weeks |
EuroAlloys | Europe | €22 – €38 | 2-3 weeks |
AsiaMet | China | $20 – $35 | 2-4 weeks |
GlobalMetal Supply | India | $18 – $32 | 2-4 weeks |
CopperAlloy Solutions | UK | £20 – £36 | 1-2 weeks |
Factors Affecting CuCr1 Pricing
- Form: The price of CuCr1 can vary depending on whether you’re purchasing rods, plates, wires, or bars.
- Grade: Higher-strength grades such as cold-worked or hardened it tend to be more expensive due to additional heat treatment or work hardening processes.
- Quantity: Bulk orders often result in lower per-unit costs, so consider buying in larger quantities if your project allows.
- Market Demand: Prices can fluctuate based on global demand, particularly from industries like automotive, aerospace, and power generation.
Pros and Cons
Like any material, it has its strengths and weaknesses. Below, we’ll compare the advantages and limitations of CuCr1 to help you determine if it’s the right choice for your application.
Advantages and Limitations
Advantages | Limitations |
---|---|
Excellent balance of strength and conductivity | More expensive than pure copper |
High thermal stability | Slightly lower conductivity than pure copper |
Good wear resistance | Requires precise heat treatment for best results |
Corrosion resistant | Limited availability in some regions |
Fatigue resistant | May require additional processing for specific forms |
Easy to machine and form | More difficult to source in custom sizes |
Key Takeaways
- It is an excellent choice when you need a material that offers both strength and conductivity—perfect for electrical components and welding applications.
- While it’s more expensive than pure copper, its increased durability and wear resistance often provide longer service life, reducing the need for frequent replacements.
- Keep in mind that availability can sometimes be an issue, especially if you’re looking for custom sizes or specific grades.
CuCr1 vs. Other Copper Alloys: A Comparison
To fully appreciate the benefits of CuCr1, it’s important to compare it to other common copper alloys like CuCr1Zr and pure copper. Below, we’ll break down how it stacks up against these materials.
CuCr1 vs. CuCr1Zr vs. Pure Copper
Property | CuCr1 | CuCr1Zr | Pure Copper |
---|---|---|---|
Tensile Strength | 350 – 550 MPa | 400 – 550 MPa | 200 – 250 MPa |
Yield Strength | 250 – 400 MPa | 300 – 450 MPa | 50 – 100 MPa |
Electrical Conductivity | 80 – 90% IACS | 70 – 85% IACS | 100% IACS |
Thermal Conductivity | 300 – 370 W/mK | 320 – 350 W/mK | 390 – 400 W/mK |
Wear Resistance | High | Moderate | Low |
Cost | Moderate | Moderate | Low |
Applications | Electrical contacts, welding | Aerospace, power generation | Electrical wiring, heat sinks |
Key Takeaways from the Comparison
- It offers a better balance of strength and conductivity compared to CuCr1Zr, making it ideal for welding and high-stress applications.
- It has slightly better thermal stability, which makes it a better choice for aerospace and power generation applications.
- Pure copper is the best option for electrical conductivity, but it lacks the strength and durability needed for mechanical applications.
Frequently Asked Questions (FAQ)
We’ve compiled a list of common questions about CuCr1 to help you quickly find the information you need.
Question | Answer |
---|---|
What is it used for? | It is commonly used in switchgear, welding electrodes, electrical contacts, and automotive connectors. |
How much does it cost? | It typically costs between $20 and $40 per kg, depending on the form and supplier. |
Is it corrosion resistant? | Yes, it offers good resistance to corrosion, particularly in high-temperature environments. |
Can it be used in high-temperature applications? | Yes, it maintains its properties at elevated temperatures, making it suitable for heat exchangers and power generation. |
What is the difference between CuCr1 and CuCr1Zr? | It contains chromium, while CuCr1Zr contains both chromium and zirconium, offering slightly better thermal stability. |
Is it easy to machine? | Yes, it is relatively easy to machine, though hardened grades may require specialized tools for optimal results. |
Conclusion
It is a high-performance copper alloy that offers an excellent balance of strength, conductivity, and thermal stability. Whether you’re working on electrical contacts, welding electrodes, or automotive components,it is a versatile and reliable material that can handle the demands of high-stress and high-temperature environments.
While it may be more expensive than pure copper, its durability and wear resistance make it a worthwhile investment for projects where performance and longevity are key. If you need a material that combines the conductivity of copper with the strength of an alloy, it is a top contender.
In summary, it is the ideal choice for applications requiring a high-performance copper alloy that can stand up to mechanical stress, heat, and corrosion—all while retaining excellent electrical properties.
Maybe you want to know more about our products, please contact us
Get Latest Price
About Met3DP
Product Category
HOT SALE
CONTACT US
Any questions? Send us message now! We’ll serve your request with a whole team after receiving your message.
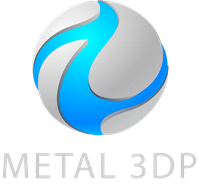
Metal Powders for 3D Printing and Additive Manufacturing