process for production of high-purity powders
Table of Contents
Imagine a world where materials are crafted with unparalleled precision, their structure so pure it unlocks groundbreaking applications. This is the realm of high-purity powders, microscopic marvels that push the boundaries of performance across diverse industries. But how do these tiny titans come to be? Buckle up, because we’re diving deep into the fascinating processes that transform raw materials into these incredible ingredients.
The Power of high-purity powders
High-purity powders are exactly what they sound like: finely divided materials boasting exceptionally low levels of impurities. These contaminants can significantly impact a material’s properties, hindering its strength, conductivity, or other crucial characteristics. By minimizing these unwanted guests, high-purity powders unlock a treasure trove of benefits:
- Enhanced Performance: Reduced impurities translate to superior strength, electrical conductivity, and other performance metrics.
- Tailored Properties: By meticulously controlling the powder’s composition and morphology (shape and size), engineers can create materials with properties precisely suited for specific applications.
- Unprecedented Applications: High-purity powders enable the development of cutting-edge technologies in fields like aerospace, electronics, and additive manufacturing.
Now, let’s delve into the nitty-gritty of how these wonder powders are born.
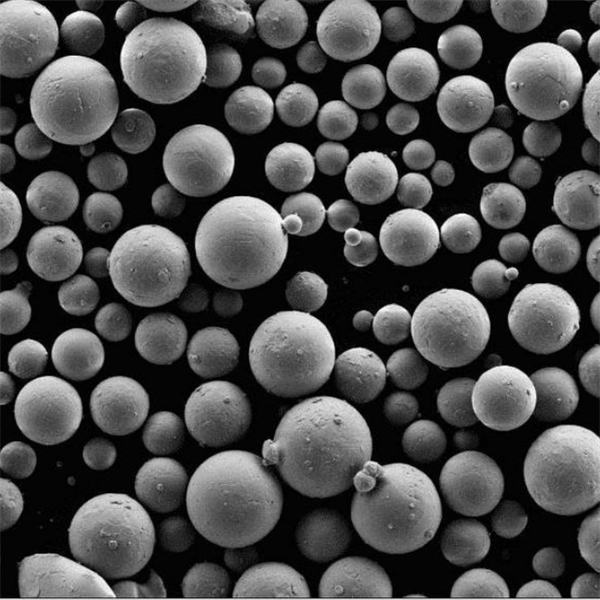
A Gallery of Techniques: Unveiling the Production Methods
The world of high-purity powder production boasts a diverse arsenal of techniques, each with its own strengths and applications. Here are some of the most prominent players:
1. Atomization: Picture molten metal being blasted into a fine mist using a high-pressure stream of gas, water, or even plasma. This rapid solidification creates a shower of spherical powder particles with a high degree of purity.
- Types: Gas atomization, water atomization, plasma atomization
- Applications: Aerospace components, medical implants, catalysts
2. Electrolysis: Imagine a metal acting as an electrode in a bath of a specific solution. By applying an electric current, the metal dissolves and deposits on the opposite electrode, forming a pure metal powder.
- Types: Mainly used for copper, but can be used for other metals like chromium and magnesium.
- Applications: High-conductivity electrical components, heat sinks
3. Chemical Precipitation: Think of this as a controlled magic show. Specific chemical reactions are used to create a precipitate – a solid that separates from a solution. This precipitate can then be processed into a high-purity powder.
- Types: Varies depending on the desired material. Common examples include precipitation of oxides, nitrides, and carbides.
- Applications: Pigments, ceramics, battery materials
4. Solid-State Reduction: For some metal oxides (compounds containing oxygen), a high-temperature, oxygen-deficient environment can be used to coax out the pure metal in the form of a powder.
- Types: Typically used for oxides of refractory metals like tungsten and molybdenum.
- Applications: High-temperature furnace components, cutting tools
5. Mechanical Milling: Imagine grinding a brittle material down to a fine powder. This brute force approach can be surprisingly effective for certain materials, though purity levels might be lower compared to other techniques.
- Types: Ball milling, attritor milling
- Applications: Powders for brazing and soldering, pyrotechnics
Beyond the Big Five: This list merely scratches the surface. Other techniques like hydrothermal synthesis and vapor deposition also play a role in the production of high-purity powders for specialized applications.
A Menagerie of Metal Marvels: Spotlight on Specific Powders
The world of high-purity powders is teeming with fascinating materials, each with unique properties and applications. Here are ten superstars to whet your appetite:
- Titanium Powder: The darling of the aerospace industry, prized for its exceptional strength-to-weight ratio and high-temperature performance.
- Aluminum Powder: A lightweight champion, widely used in pyrotechnics, paints, and even 3D printing.
- Copper Powder: The undisputed king of conductivity, essential for electrical components and heat sinks.
- Nickel Powder: A versatile workhorse, used in everything from catalysts to battery electrodes.
- Iron Powder: The backbone of the metalworking world, forming the base for countless alloys and applications.
- Tungsten Carbide Powder: The ultimate tough guy, renowned for its extreme hardness and wear resistance, perfect for cutting tools and drill bits.
- Silicon Carbide Powder: Another champion of hardness, used as an abrasive and in high-performance ceramics.
- Yttria-Stabilized Zirconia (YSZ) Powder: A high-temperature ceramic with excellent thermal stability, ideal for fuel cells and oxygen sensors.
- Alumina (Aluminum Oxide) Powder: A ubiquitous material with a wide range of applications, from ceramics and abrasives to catalysts and refractory linings.
- Silver Powder: The high-society metal, prized for its exceptional electrical conductivity, thermal conductivity, and antibacterial properties, making it ideal for electronics, medical devices, and conductive coatings.
A Look Under the Microscope: Properties and Applications
Each high-purity powder boasts a unique set of properties that dictate its suitability for specific applications. Let’s explore some key characteristics:
Property | Description | Importance |
---|---|---|
Particle Size and Distribution | The size and uniformity of the powder particles significantly impact its behavior. Smaller particles tend to have a higher surface area, making them more reactive and ideal for applications like catalysts. A narrow particle size distribution ensures consistent performance. | Impacts: Sintering behavior, reactivity, flowability |
Morphology | The shape of the powder particles can influence packing density, flowability, and even mechanical properties. Spherical particles generally pack more efficiently and offer better flow characteristics. | Impacts: Powder handling, compaction behavior, final product properties |
Purity | The level of impurities directly affects the performance of the final product. High-purity powders are essential for applications demanding optimal electrical conductivity, strength, or other properties. | Impacts: Conductivity, strength, corrosion resistance, biocompatibility |
Flowability | The ease with which the powder flows is crucial for efficient processing and handling. Powders with good flowability enable smooth filling of molds and hoppers during manufacturing. | Impacts: Production efficiency, product consistency |
Matching the Powder to the Purpose: A Symphony of Applications
High-purity powders are the building blocks for a vast array of innovative products. Here’s a glimpse into the diverse applications they enable:
Application | Powders Used | Key Considerations |
---|---|---|
Aerospace Components | Titanium, Aluminum, Nickel alloys | High strength-to-weight ratio, high-temperature performance |
Medical Implants | Titanium, Tantalum | Biocompatibility, corrosion resistance, long-term stability |
Electronics | Copper, Silver, Nickel | High conductivity, solderability, thermal management |
Additive Manufacturing (3D Printing) | Titanium, Aluminum, Stainless steel | Powder flowability, laser compatibility, surface finish |
Catalysts | Nickel, Platinum, Palladium | High surface area, selectivity, activity |
Battery Materials | Lithium, Cobalt, Graphite | Electrochemical properties, stability, cyclability |
Pigments | Titanium dioxide, Iron oxide | Color intensity, dispersion, lightfastness |
Ceramics | Alumina, Silicon carbide, Yttria-stabilized zirconia | High-temperature performance, wear resistance, chemical stability |
Navigating the Maze: Choosing the Right Powder
Selecting the optimal high-purity powder for your application requires careful consideration of several factors:
- Desired Properties: Identify the crucial properties for your application, such as strength, conductivity, or biocompatibility.
- Processing Methods: Consider the compatibility of the powder with your chosen manufacturing techniques (e.g., 3D printing, sintering).
- Cost-Effectiveness: High-purity powders can be expensive. Evaluate the cost against the performance benefits and explore potential trade-offs.
- Supplier Reputation: Choose a reliable supplier with a proven track record of quality and consistency.
Beyond the Basics: A Deeper Dive
This exploration has merely scratched the surface of the fascinating world of high-purity powders. Here are some additional aspects to delve deeper:
- Advanced Characterization Techniques: Sophisticated tools like X-ray diffraction and electron microscopy are used to analyze the powder’s crystal structure, morphology, and composition with unparalleled detail.
- Emerging Production Techniques: Researchers are constantly exploring novel methods for producing high-purity powders with even better properties and lower costs. Techniques like microwave-assisted processing and ultrasonic atomization are gaining traction.
- Sustainability Considerations: The production of high-purity powders can be energy-intensive. Sustainable practices like recycling and using renewable energy sources are becoming increasingly important.
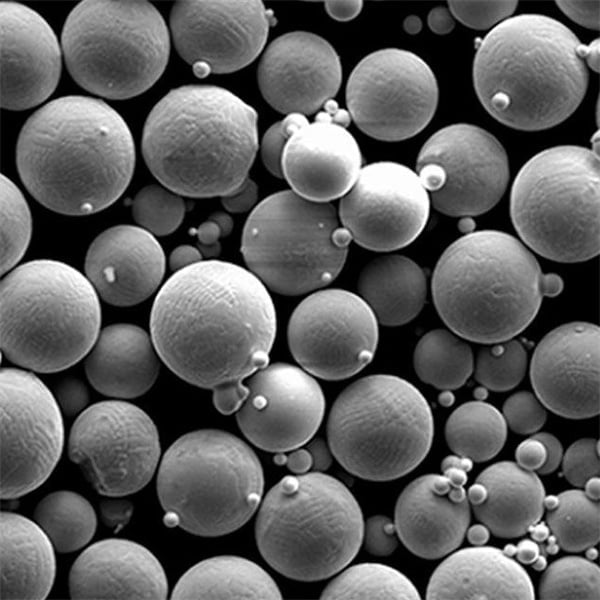
FAQ
Q: What are the advantages of using high-purity powders?
A: High-purity powders enable the development of cutting-edge technologies in various fields, including aerospace, electronics, and additive manufacturing.
Q: Are there any disadvantages to using high-purity powders?
A: While high-purity powders offer numerous advantages, there are a few potential drawbacks to consider:
- Cost: The production process for high-purity powders can be expensive, leading to higher material costs compared to lower-purity alternatives.
- Handling: Some high-purity powders can be reactive or pose health risks, requiring special handling procedures and safety precautions.
- Limited Availability: Depending on the specific material and desired purity level, certain high-purity powders might have limited availability or require longer lead times.
Q: How can I choose the right high-purity powder for my application?
A: Selecting the optimal high-purity powder involves careful consideration of several factors:
- Desired Properties: Identify the key properties critical for your application, such as strength, conductivity, thermal stability, or biocompatibility.
- Processing Methods: Ensure compatibility between the powder and your chosen manufacturing techniques (e.g., sintering, 3D printing). For instance, 3D printing might require powders with specific flow characteristics for optimal performance.
- Cost-Effectiveness: Evaluate the cost of the powder against the performance benefits it offers. Consider potential trade-offs between purity level and affordability.
- Supplier Reputation: Choose a reliable supplier with a proven track record of quality, consistency, and technical expertise. They can provide valuable guidance on selecting the most suitable powder for your needs.
The Future of High-Purity Powders: A Glimpse into Tomorrow’s Marvels
The future of high-purity powders is brimming with exciting possibilities. Here are some trends to watch:
- Nanoparticles: Powders with particle sizes in the nanometer range (billionths of a meter) are poised to revolutionize various fields. Their unique properties can lead to stronger, lighter materials and enable the development of next-generation electronics and catalysts.
- Composite Powders: Blending different high-purity powders can create materials with a unique combination of properties. Imagine a powder that is both strong and conductive, opening doors for innovative applications.
- In-Situ Processing: Researchers are exploring techniques to produce high-purity powders directly within the final product, eliminating the need for separate processing steps and potentially leading to more efficient manufacturing.
Share On
MET3DP Technology Co., LTD is a leading provider of additive manufacturing solutions headquartered in Qingdao, China. Our company specializes in 3D printing equipment and high-performance metal powders for industrial applications.
Inquiry to get best price and customized Solution for your business!
Related Articles
About Met3DP
Recent Update
Our Product
CONTACT US
Any questions? Send us message now! We’ll serve your request with a whole team after receiving your message.
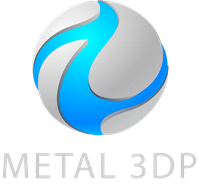
Metal Powders for 3D Printing and Additive Manufacturing
COMPANY
PRODUCT
cONTACT INFO
- Qingdao City, Shandong, China
- [email protected]
- [email protected]
- +86 19116340731