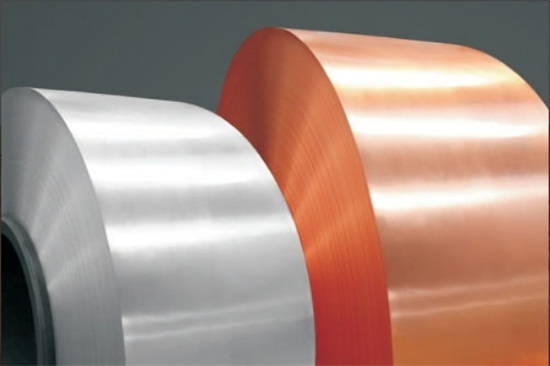
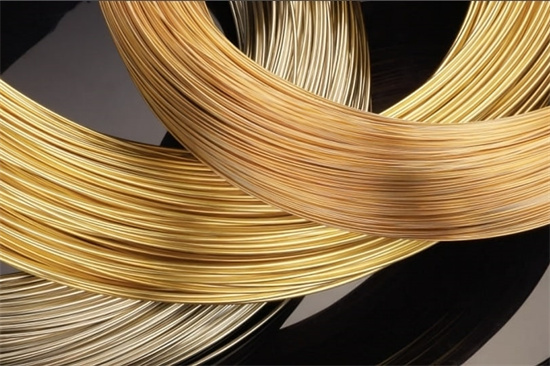
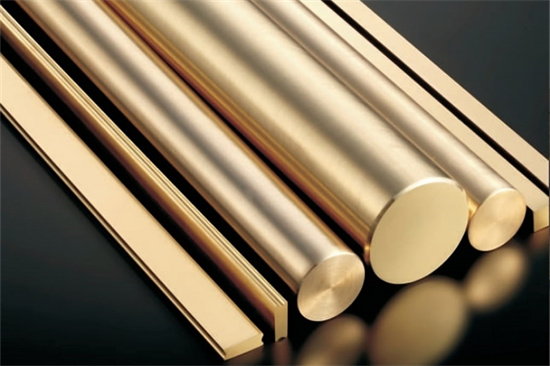
High Strength, High Wear Resistance Complex Copper Alloy: The Ultimate Guide for Engineers and Manufacturers
Low MOQ
Provide low minimum order quantity to meet different needs.
OEM & ODM
Provide customized products and design services to meet unique customer needs.
Adequate Stock
Ensure fast order processing and provide reliable and efficient service.
Customer Satisfaction
Provide high quality products with customer satisfaction at the core.
share this article
Table of Contents
When it comes to selecting materials for applications that demand both high strength and wear resistance, a complex copper alloy can be a game-changer. Copper, when alloyed with elements like nickel, aluminum, and silicon, can offer an impressive balance of ductility, conductivity, and durability. These alloys are designed to endure the wear and tear of high-performance machinery while maintaining their structural integrity over time.
In this comprehensive guide, we’ll explore everything you need to know about high strength, high wear resistance complex copper alloys, including their composition, properties, applications, specifications, and pricing. Whether you’re an engineer looking for the perfect material for a high-load bearing surface or a manufacturer seeking a reliable alloy for heavy-duty industrial equipment, this guide will help you make an informed decision.
Overview of High Strength, High Wear Resistance Complex Copper Alloys
So, what exactly is a high strength, high wear resistance complex copper alloy? This type of alloy typically includes a copper base with additional elements like nickel, aluminum, silicon, and sometimes iron or manganese. These elements are added to enhance properties such as tensile strength, hardness, and wear resistance, making the alloy suitable for heavy-duty applications where both strength and durability are critical.
Key Properties:
- High Strength: These alloys are designed to withstand high-stress environments, providing excellent mechanical strength even under heavy loads.
- Wear Resistance: Engineered to resist wear from friction, making them ideal for use in moving parts or components where durability is crucial.
- Thermal Conductivity: Retains some of copper’s excellent heat conductivity, making these alloys suitable for applications where thermal management is necessary.
- Corrosion Resistance: Many of these alloys exhibit good corrosion resistance, especially in marine environments or when exposed to chemicals.
- Machinability: Despite their strength, these alloys are often easy to machine, allowing for intricate designs and precision engineering.
Types, Composition, and Properties of High Strength, High Wear Resistance Complex Copper Alloys
There are several types of complex copper alloys that are specifically engineered for high strength and wear resistance. Each alloy has its unique composition, and the addition of different elements can significantly alter its properties.
Types and Composition of Complex Copper Alloys
Alloy Type | Copper (Cu) | Nickel (Ni) | Aluminum (Al) | Silicon (Si) | Other Elements | Primary Properties |
---|---|---|---|---|---|---|
C95500 (Nickel Aluminum Bronze) | 77-80% | 9-11% | 9-10% | 0.5-1.5% | Iron (max 5%) | High strength, excellent wear resistance, superior corrosion resistance. |
C63000 (Aluminum Bronze) | 78-82% | 4.5-5.5% | 9-11% | – | Iron (max 2%) | High strength, good ductility, excellent resistance to wear and fatigue. |
C93700 (Leaded Bronze) | 78-82% | – | – | – | Lead (6-8%), Tin (7-9%) | Superior wear resistance, good machinability, used in bearing applications. |
C86200 (Manganese Bronze) | 60-65% | – | 0.5% | – | Zinc (20-25%), Iron (2-4%) | High tensile strength, good wear resistance, often used in heavy industrial machinery. |
C81400 (Iron-Silicon Bronze) | 83-87% | – | – | 2.5-4% | Iron (4-6%) | Extreme wear resistance, high tensile strength, good thermal conductivity. |
Mechanical and Physical Properties of Complex Copper Alloys
The mechanical properties of these alloys vary based on their composition, but they all share the same key features: high strength and wear resistance. Below are the general properties of some commonly used high-strength copper alloys.
Property | C95500 (Nickel Aluminum Bronze) | C63000 (Aluminum Bronze) | C93700 (Leaded Bronze) | C86200 (Manganese Bronze) | C81400 (Iron-Silicon Bronze) |
---|---|---|---|---|---|
Tensile Strength (MPa) | 690-800 | 620-750 | 270-350 | 550-690 | 620-800 |
Yield Strength (MPa) | 300-500 | 350-450 | 150-250 | 250-400 | 400-600 |
Hardness (HB) | 170-210 | 150-180 | 90-120 | 140-180 | 180-220 |
Elongation at Break (%) | 10-20% | 15-25% | 10-20% | 20-30% | 10-20% |
Density (g/cm³) | 7.5-8.0 | 7.6-8.2 | 8.9 | 7.3-8.4 | 7.7-8.1 |
Thermal Conductivity (W/m·K) | 50-60 | 60-80 | 30-40 | 40-50 | 45-55 |
Applications of High Strength, High Wear Resistance Complex Copper Alloys
Given their combination of high strength and wear resistance, these copper alloys are frequently used in industries where mechanical stress, friction, and corrosion are factors. Their ability to endure heavy loads while resisting wear makes them indispensable in marine environments, aerospace, automotive, and heavy machinery.
Common Applications of Complex Copper Alloys
Industry | Application |
---|---|
Marine Engineering | Propellers, valve seats, fasteners, and bearing bushings due to their corrosion resistance and durability. |
Aerospace | Landing gear components, pump impellers, and bushings in high-wear, high-stress environments. |
Automotive | Bearings, gearshift forks, and synchronizer rings that require both strength and wear resistance. |
Heavy Machinery | Hydraulic piston rings, worm gears, and guide bushings where durability under stress is critical. |
Power Generation | Turbine blades, heat exchanger parts, and components that must withstand both high temperatures and stress. |
Mining | Crusher liners, grinding mills, and wear plates that need to resist abrasion and erosion. |
Marine Engineering
One of the most significant uses for these alloys is in marine environments. Marine applications require materials that can withstand not just mechanical stress but also corrosion from saltwater. Complex copper alloys like C95500 (nickel aluminum bronze) are commonly used in propellers, valves, and pumps due to their superior corrosion resistance and strength.
Aerospace Applications
In aerospace, these alloys play a crucial role in components subjected to high stress and friction, such as landing gear bushings and pump impellers. The high wear resistance of these alloys ensures that parts last longer, reducing the need for frequent replacements and enhancing the safety of the aircraft.
Automotive Industry
In the automotive industry, complex copper alloys are used in bearings, gearshift forks, and synchronizer rings. These components need to be incredibly strong and wear-resistant to handle the constant motion and friction within a car’s engine and transmission system.
Specifications, Sizes, and Standards for Complex Copper Alloys
Complex copper alloys are available in a wide range of forms, sizes, and specifications. These materials are produced to meet specific industry standards, ensuring that they meet the necessary mechanical and physical properties. Below is a breakdown of the typical sizes, forms, and standards for some of the most commonly used high-strength copper alloys.
Available Forms, Sizes, and Industry Standards for Complex Copper Alloys
Form | Typical Sizes Available | Industry Standards |
---|---|---|
Bars/Rods | Diameter: 10 mm to 500 mm | ASTM B150, BS 2874, EN 12163 |
Plates/Sheets | Thickness: 0.5 mm to 100 mm | ASTM B171, DIN 17670, EN 1653 |
Wires | Diameter: 0.1 mm to 10 mm | ASTM B206, EN 12166 |
Tubes/Pipes | Outer Diameter: 10 mm to 300 mm | ASTM B466, BS 2871, EN 12449 |
Custom Castings | Cast to specifications per customer’s request | ASTM B505, DIN 1709, EN 1982 |
Most complex copper alloys adhere to ASTM standards, which govern everything from the alloy’s chemical composition to its mechanical properties. For example, ASTM B150 specifies the properties of aluminum bronze bars used in high-stress applications.
Suppliers and Pricing of High Strength, High Wear Resistance Complex Copper Alloys
The price of complex copper alloys can vary significantly depending on factors like grade, form, and order quantity. Additionally, the market prices of raw materials like copper and nickel heavily influence the overall cost.
Leading Suppliers and Pricing Estimates for Complex Copper Alloys
Supplier | Location | Price per kg | Minimum Order Quantity |
---|---|---|---|
Aviva Metals | USA | $30 – $70 | 50 kg |
Shanghai Metal Corporation | China | $25 – $65 | 100 kg |
MetalTek International | Global | $35 – $80 | Custom orders |
Copper Alloys Ltd. | UK | $40 – $85 | 100 kg |
Alro Metals | USA | $30 – $75 | Custom orders |
Prices generally range between $25 to $85 per kg, depending on the grade, form, and supplier. Large orders typically result in discounted pricing, especially for custom castings or long-term contracts. It’s worth noting that fluctuations in the prices of raw materials like copper and nickel can significantly affect the cost of these alloys.
Comparing the Pros and Cons of High Strength, High Wear Resistance Complex Copper Alloys
As with any material, complex copper alloys have their advantages and limitations. While they excel in strength and wear resistance, there are a few trade-offs to consider when selecting them for your project.
Advantages of Complex Copper Alloys
Advantage | Description |
---|---|
High Strength | These alloys excel in high-stress environments, providing superior mechanical strength. |
Excellent Wear Resistance | With the ability to resist friction and wear, they are ideal for moving parts and heavy-duty applications. |
Good Corrosion Resistance | Many complex copper alloys resist corrosion, especially in marine environments. |
Thermal Conductivity | Retains some of copper’s thermal conductivity, making them useful in heat exchangers and thermal management systems. |
Machinability | Despite their strength, these alloys are often easy to machine and shape. |
Disadvantages of Complex Copper Alloys
Disadvantage | Description |
---|---|
Higher Cost Compared to Standard Alloys | Complex copper alloys can be more expensive due to the addition of premium elements like nickel and aluminum. |
Heavier than Alternatives | These alloys are typically denser, which may be a disadvantage in applications where weight is a concern. |
Requires Specialized Welding | Welding these alloys requires specific techniques and expertise to avoid defects. |
Availability of Specialized Grades | Some lesser-known grades may have limited availability in certain regions. |
FAQs About High Strength, High Wear Resistance Complex Copper Alloys
Question | Answer |
---|---|
What are high strength, high wear resistance complex copper alloys used for? | They are used in high-stress, high-wear applications such as marine propellers, bearings, and aerospace components. |
Are these alloys corrosion-resistant? | Yes, many of these alloys offer excellent corrosion resistance, especially in marine environments. |
Can complex copper alloys be welded? | Yes, but they require specialized welding techniques such as TIG or MIG welding. |
How much do complex copper alloys cost? | Prices typically range between $25 to $85 per kg, depending on the grade and form. |
What is the most common application for these alloys? | Marine engineering and heavy machinery parts that require both strength and wear resistance. |
Do these alloys conduct heat well? | Yes, they retain some of copper’s natural thermal conductivity, making them suitable for heat exchangers. |
How do these alloys compare to steel in terms of strength? | While complex copper alloys are strong, steel generally offers higher tensile strength but lacks copper’s thermal and corrosion properties. |
Are these alloys heavier than aluminum? | Yes, complex copper alloys are denser and heavier than aluminum, but they offer superior wear resistance. |
Conclusion
High strength, high wear resistance complex copper alloys offer an exceptional combination of durability, strength, and wear resistance that makes them ideal for demanding industrial applications. Whether you’re building a marine propeller or designing parts for heavy machinery, these alloys provide the resilience and longevity needed to withstand the toughest conditions.
While they may be more expensive than standard materials, the long-term benefits of using complex copper alloys often outweigh the initial costs. Their ability to resist wear, corrosion, and mechanical stress ensures that components last longer and perform better under harsh conditions.
By understanding the different grades, properties, and applications of complex copper alloys, you can make an informed decision that will lead to improved performance, efficiency, and cost-effectiveness in your project.
Maybe you want to know more about our products, please contact us
Get Latest Price
About Met3DP
Product Category
HOT SALE
CONTACT US
Any questions? Send us message now! We’ll serve your request with a whole team after receiving your message.
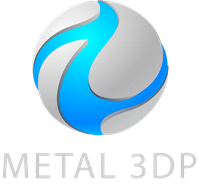
Metal Powders for 3D Printing and Additive Manufacturing