Inconel 600 Powder
Table of Contents
Inconel 600 is a standard engineering material for high temperature applications up to 1100°C. This guide covers Inconel 600 powder compositions, properties, manufacturing methods, applications, specifications, pricing, comparisons, and frequently asked questions when considering this nickel-chromium-iron alloy.
Typical Composition of Inconel 600 Powder
Element | Weight % |
---|---|
Nickel | 72% min |
Chromium | 14-17% |
Iron | 6-10% |
Carbon | 0.15% max |
Manganese | 1% max |
Sulfur | 0.015% max |
Silicon | 0.5% max |
Copper | 0.5% max |
The nickel-chromium balances high temperature strength with fabricability. Low carbon content minimizes harmful carbide precipitation during exposures above 550°C.
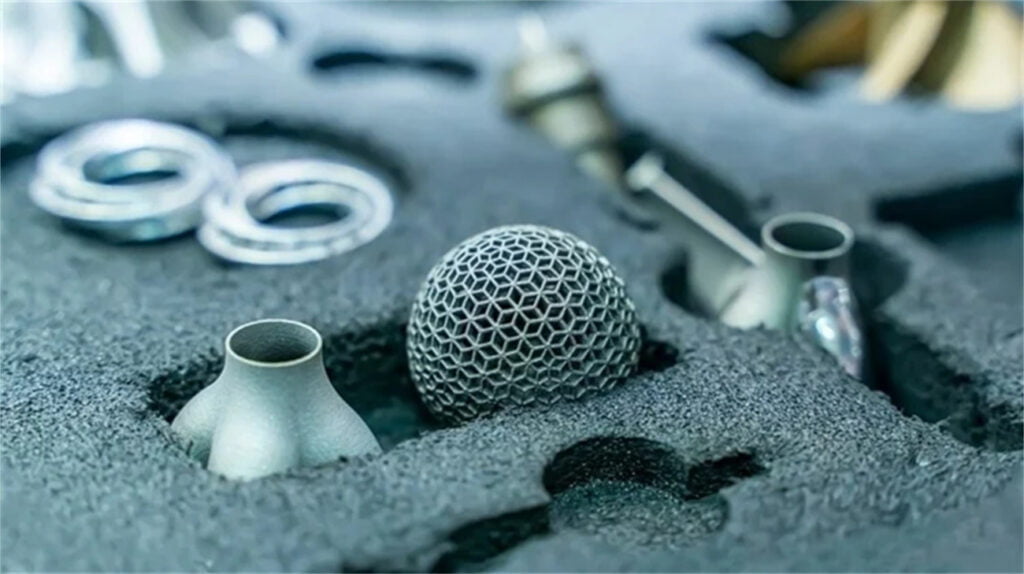
Key Properties and Characteristics
Property | Description | Benefit |
---|---|---|
High-Temperature Strength | Inconel 600 powder retains its impressive strength even at scorching temperatures reaching 2000°F (1093°C). This resilience makes it the perfect material for parts exposed to extreme heat, such as those found in gas turbine engines and combustors. | Inconel 600 powder enables the creation of components that can function flawlessly in environments where other materials would succumb to heat-induced weakness. |
Exceptional Corrosion Resistance | Inconel 600 powder boasts superior resistance to a variety of corrosive agents, including acids, alkalis, and chloride ions. It remains stable and untarnished in both oxidizing and reducing environments, making it ideal for use in chemical processing equipment, marine components, and nuclear power plants. | This property ensures that Inconel 600 powder can withstand harsh chemical attacks, safeguarding the structural integrity of components in demanding applications. |
Excellent Formability | Unlike some superalloys, Inconel 600 powder exhibits good ductility, allowing it to be shaped and formed using conventional metalworking techniques. This characteristic simplifies the manufacturing process for intricate parts. | The forgeability of Inconel 600 powder reduces the need for specialized fabrication methods, streamlining production and lowering overall costs. |
Weldability | Inconel 600 powder offers exceptional weldability, enabling the creation of strong and reliable joints between similar or dissimilar materials. This property is crucial for manufacturing complex structures from multiple components. | The ability to weld Inconel 600 powder seamlessly facilitates the construction of robust and dependable components for various applications. |
Good Fatigue Resistance | Inconel 600 powder demonstrates remarkable resistance to fatigue, which is the weakening of a material due to repeated stress cycles. This characteristic ensures that components can endure prolonged exposure to fluctuating loads without succumbing to failure. | The fatigue strength of Inconel 600 powder makes it suitable for applications involving constant vibration or cyclic stresses, such as turbine blades and jet engine parts. |
Oxidation Resistance | Inconel 600 powder exhibits exceptional resistance to oxidation, a process where a material reacts with oxygen at high temperatures. This property allows components to maintain their structural integrity and performance in environments with elevated temperatures and oxygen presence. | The oxidation resistance of Inconel 600 powder prevents components from degrading and becoming brittle in environments prone to high-temperature oxidation. |
Biocompatibility | Inconel 600 powder demonstrates good biocompatibility, meaning it poses minimal health risks when used in contact with human tissue. This characteristic makes it a viable material for certain medical implants and devices. | While not its primary function, the biocompatibility of Inconel 600 powder opens doors for its potential use in medical applications. |
Additive Manufacturing Compatibility | Inconel 600 powder is particularly well-suited for additive manufacturing techniques like laser powder bed fusion. The spherical particle morphology of the powder optimizes flow and facilitates precise layer-by-layer construction during the printing process. | The compatibility of Inconel 600 powder with additive manufacturing allows for the creation of complex and intricate components with exceptional design freedom. |
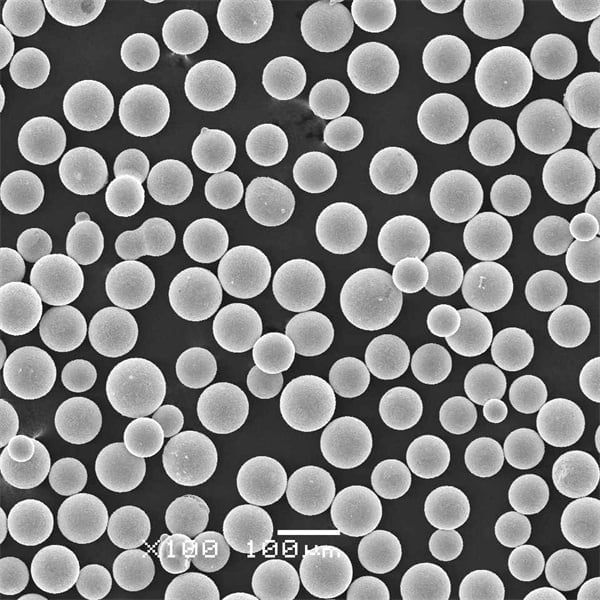
Applications of Inconel 600 Powder
Industry | Application | Key Properties Utilized | Additional Considerations |
---|---|---|---|
Aerospace | * Afterburner components * Exhaust ducts * Turbine shrouds | * High-temperature strength: Withstands extreme temperatures exceeding 1100°C, crucial for enduring the intense heat generated by jet engines. * Oxidation resistance: Maintains structural integrity in oxygen-rich environments encountered during flight. * Creep resistance: Resists deformation under prolonged high-temperature stress, ensuring component longevity. | * Strict tolerances and complex geometries: Inconel 600 powder’s good weldability allows for fabrication of intricate parts while meeting stringent aerospace standards. * Weight reduction: Additive manufacturing with Inconel 600 powder enables lightweight component design, improving fuel efficiency. |
Chemical Processing | * Heat exchangers * Reaction vessels * Processing equipment for harsh chemicals | * Corrosion resistance: Exhibits exceptional resistance to a wide range of corrosive chemicals, ensuring process media containment and component integrity. * High-temperature strength: Handles high operating temperatures encountered in chemical reactions. * Good fabricability: Inconel 600 powder allows for the creation of complex shapes required for specialized chemical processing equipment. | * Surface finish: The surface finish of 3D printed Inconel 600 components might require post-processing for optimal chemical compatibility depending on the specific application. |
Oil & Gas | * Downhole tools * Wellhead control lines * Subsea equipment | * High-temperature strength: Withstands the scorching temperatures encountered in deep well environments. * Pressure resistance: Maintains structural integrity under the immense pressure exerted by oil and gas at significant depths. * Corrosion resistance: Resists the corrosive effects of downhole fluids, including brines and sour gas. | * Residual stress: Minimizing residual stress after 3D printing is crucial for downhole components to ensure they can withstand the demanding service conditions. * Non-destructive testing: Rigorous non-destructive testing is essential to identify any potential defects in 3D printed Inconel 600 components for oil and gas applications. |
Power Generation | * Gas turbine components * Heat exchangers * High-temperature piping | * High-temperature strength and creep resistance: Ensures components can endure the extreme temperatures and constant stress present in gas turbine operations. * Oxidation resistance: Maintains structural integrity in high-temperature, oxygen-rich environments. * Weldability: Enables reliable joining of 3D printed Inconel 600 components with traditionally manufactured parts. | * Strict quality control: stringent quality control measures are necessary throughout the 3D printing process to guarantee components meet the demanding requirements of power generation applications. |
Pollution Control | * Coal gasification components * Exhaust recuperators * Flue gas treatment systems | * High-temperature strength and oxidation resistance: Crucial for withstanding the high temperatures and harsh environments encountered in coal gasification processes. * Corrosion resistance: Enables components to resist the corrosive effects of acidic flue gases and other pollutants. * Fabricability: Allows for the creation of complex geometries required for efficient pollution control equipment. | * Powder characteristics: The specific characteristics of Inconel 600 powder, such as particle size and distribution, can influence the printability and final properties of the manufactured components. |
Inconel 600 Powder Specifications
Property | Specification | Typical Value | Importance in Additive Manufacturing |
---|---|---|---|
Chemical Composition (wt%) | * Nickel (Ni) + Cobalt (Co) * Chromium (Cr) * Iron (Fe) * Niobium + Tantalum (Nb+Ta) * Carbon (C) * Silicon (Si) * Phosphorus (P) * Sulfur (S) * Aluminum (Al) * Manganese (Mn) * Copper (Cu) * Titanium (Ti) | * ≥ 72 * 14.0 – 17.0 * 6.0 – 10.0 * ≤ 1.00 * ≤ 0.15 * ≤ 0.50 * ≤ 0.040 * ≤ 0.015 * ≤ 0.35 * ≤ 1.00 * ≤ 0.50 * ≤ 0.50 | * The specific balance of elements dictates the mechanical properties, corrosion resistance, and high-temperature performance of the final product. * Strict adherence to these specifications ensures consistent and reliable performance in additive manufacturing. |
Particle Size Distribution | * D10 * D50 * D90 | * Varies depending on application * Typical range: 15-150 μm | * Particle size distribution significantly impacts powder flowability, packing density, and printability. * A narrower distribution with a median particle size (D50) optimized for the specific additive manufacturing process is preferred. |
Particle Morphology | * Sphericity * Surface Morphology * Satellite Particles | * High Sphericity * Smooth Surface * Minimal Satellite Particles | * Spherical particles enhance powder flowability, packing density, and laser absorption during the additive manufacturing process. * A smooth surface minimizes defects and improves surface finish of the final component. * Minimal satellite particles (small particles adhering to larger ones) ensure consistent material flow and prevent nozzle clogging. |
Apparent Density | 4.0 – 4.5 g/cm³ | * Apparent density influences powder handling, packing efficiency, and material usage in the additive manufacturing process. * A higher apparent density allows for better packing and reduces printing time. | |
Flowability | Measured by techniques like Hall Flow Rate | * Good flowability is essential for even powder deposition and consistent layer formation during additive manufacturing. * Powder characteristics like particle size distribution and morphology significantly influence flowability. | |
Moisture Content | ≤ 0.2 wt% | * Excessive moisture can lead to spattering, porosity, and weakened mechanical properties in the final component. * Low moisture content ensures smooth printing and high-quality parts. | |
Oxygen Content | ≤ 0.5 wt% | * High oxygen content can lead to oxide formation, negatively impacting the material’s mechanical properties and high-temperature performance. * Low oxygen content is crucial for maintaining the desired properties of Inconel 600 in the final product. | |
Chemical Analysis | Performed using techniques like X-ray fluorescence (XRF) or optical emission spectrometry (OES) | * Chemical analysis verifies adherence to the specified composition and ensures consistent material properties. * Regular analysis throughout the powder production process is essential for quality control. |
Global Suppliers and Price Range
Company | Lead Time | Price/kg |
---|---|---|
Sandvik Osprey | 10-14 weeks | $50-$150 |
TLS Technik | 16 weeks | $60-$180 |
Atlantic Equipment | 12 weeks | $45-$130 |
Prices for 100+ kg quantity. Significant cost reduction above 500 kg volumes possible through negotiations.
Comparative Analysis
Feature | Description | Benefit | Consideration |
---|---|---|---|
Chemical Composition | Inconel 600 powder boasts a primary composition of nickel (around 70%), chromium (around 15%), and iron (around 8%). Smaller quantities of elements like manganese, copper, and silicon are also present. | This composition offers a compelling combination of properties: excellent resistance to high-temperature oxidation and corrosion, good mechanical strength at elevated temperatures, and desirable fabricability. | The specific balance of elements can be adjusted by some manufacturers to achieve slight variations in properties for specialized applications. |
Powder Production Methods | Two main methods dominate Inconel 600 powder production: gas atomization and water atomization. Gas atomization involves molten metal being dispersed into a high-velocity inert gas stream, creating fine, spherical particles that solidify rapidly. Water atomization uses a similar principle, but with a water stream instead of gas. | Gas atomization generally yields powders with tighter particle size distribution, improved flowability, and lower oxygen content, leading to superior final product quality. Water atomized powders can be a more cost-effective option, but may require additional processing for some applications. | The choice between methods depends on the desired powder characteristics and the specific application requirements. |
Particle Size & Distribution | Inconel 600 powder is available in a range of particle sizes, typically between 15 and 150 microns. The distribution of these particle sizes within the powder bed is crucial for successful Additive Manufacturing (AM) processes like Laser Beam Melting (LBM) and Electron Beam Melting (EBM). | A well-distributed particle size range promotes optimal packing density, good flowability, and efficient laser or electron beam interaction during melting. This translates to high-quality builds with minimal defects. | Inconel 600 powder manufacturers provide detailed particle size distribution data to ensure compatibility with specific AM equipment and process parameters. |
Flowability | Flowability refers to the ease with which powder moves under its own weight. It’s a critical factor for consistent layer deposition in AM processes. | Good flowability allows for even powder spreading and minimizes the risk of layer density variations. This translates to improved dimensional accuracy and mechanical properties of the final printed part. | Powder manufacturers employ techniques like surface modification or the addition of flow agents to enhance flowability. Pre-heating the powder bed can also be used to improve flow characteristics. |
Sphericity & Morphology | Ideally, Inconel 600 powder particles should be spherical in shape with smooth surfaces. This morphology promotes good packing density and minimizes inter-particle voids, leading to denser and stronger printed parts. | Highly spherical particles also tend to flow better and improve laser coupling efficiency during melting. | Powders with irregular shapes or surface defects can lead to inconsistencies in packing density and potential weaknesses in the final product. |
Apparent & Tap Density | Apparent density is the ratio of a powder’s mass to its total volume, including inter-particle voids. Tap density is measured after a standardized tapping routine that compacts the powder bed. | Apparent density provides a basic measure of powder bulkiness, while tap density reflects the maximum achievable packing density. The difference between these values indicates the amount of porosity within the powder bed. | Higher tap density is generally preferred for AM applications, as it translates to denser and stronger final parts. |
FAQ
Why is Inconel 600 preferred for high temperature fasteners?
Easy forming and joining characteristics facilitate nut and bolt manufacturing unlike highly alloyed grades needing specialty processing. Good creep strength above 550°C suits turbocharger applications.
What particle size range works best for laser powder bed fusion?
Around 25 to 45 microns optimal for balancing surface finish, resolution, and build speed. Too coarse powders hurt density and accuracy. Verify size distribution for adequate flowability.
What process parameters matter most when printing Inconel 600 parts?
Energy density, preheat control, powder spread parameters that ensure dense melting without excess oxidation or residual stresses leading to cracking during build and heat treatment steps.
What heat treatments apply for additively manufactured Inconel 600?
Stress relief aging similar to wrought processing helps attain consistent properties – 1050-1120°F for 1-3 hours typically specified. Precipitation treatments less common.
How is used Inconel 600 powder recycled?
retrieval systems filter, sieve, blend about 20-30% reused powder with fresh material continuously. Monitor oxygen levels and re-use fraction limits to avoid contamination issues.
Conclusion
To summarize, Inconel 600 powder provides an optimal combination of formability, weldability and heat resistance essential for component fabrication across demanding industries via additive manufacturing or other powder metallurgy techniques.
Share On
MET3DP Technology Co., LTD is a leading provider of additive manufacturing solutions headquartered in Qingdao, China. Our company specializes in 3D printing equipment and high-performance metal powders for industrial applications.
Inquiry to get best price and customized Solution for your business!
Related Articles
About Met3DP
Recent Update
Our Product
CONTACT US
Any questions? Send us message now! We’ll serve your request with a whole team after receiving your message.
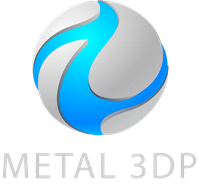
Metal Powders for 3D Printing and Additive Manufacturing