Inconel 718 Powder
Table of Contents
Overview
Inconel 718 powder is a nickel-chromium alloy powder used primarily in additive manufacturing and metal 3D printing applications. Some key features of Inconel 718 powder include:
- High strength and hardness, including at high temperatures
- Excellent corrosion and oxidation resistance
- Good weldability and machinability
- Ability to additively manufacture complex geometries
- Used in aerospace, oil and gas, automotive, and other demanding industries
Inconel 718 is a precipitation hardening nickel alloy with additions of chromium, iron, niobium, molybdenum, titanium and aluminum. It combines corrosion resistance, high strength at elevated temperatures up to 700°C, and ease of fabrication into complex parts using additive manufacturing.
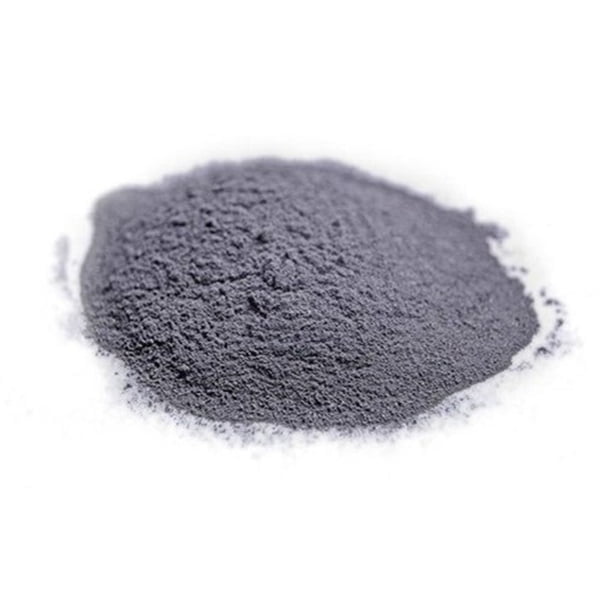
Inconel 718 Powder Composition
The nominal composition of Inconel 718 powder is given below:
Element | Weight % |
---|---|
Nickel (Ni) | 50-55% |
Chromium (Cr) | 17-21% |
Iron (Fe) | Balance |
Niobium (Nb) + Tantalum (Ta) | 4.75-5.5% |
Molybdenum (Mo) | 2.8-3.3% |
Titanium (Ti) | 0.65-1.15% |
Aluminum (Al) | 0.2-0.8% |
The iron content is balanced to 100% by weight. Other trace elements like carbon, manganese and silicon may be present in small quantities.
The key alloying elements in Inconel 718 powder are nickel, chromium, niobium, and molybdenum. Nickel forms the matrix of the alloy providing ductility. Chromium provides oxidation and corrosion resistance. Niobium in combination with nickel and chromium contributes to precipitation hardening. Molybdenum also enhances high temperature strength through solid solution strengthening.
Characteristics and Properties of Inconel 718 Powder
Inconel 718 powder exhibits the following characteristics:
Mechanical Properties:
- Tensile strength: 1,034 – 1,414 MPa
- Yield strength: 827- 1,103 MPa
- Elongation: Around 20%
- Hardness: 36-48 HRC
Physical Properties:
- Melting point: 1,300°C
- Density: 8.19 g/cm3
Thermal Properties:
- Coefficient of thermal expansion: 12.8 x 10<sup>-6</sup> /K
- Maximum service temperature: 700°C
- Thermal conductivity: 11.2 W/m.K
Corrosion Resistance:
- Excellent corrosion resistance in wide range of acids, alkalis and salts
- Resists sulphidation and oxidation up to 700°C
Particle Size Distribution of Inconel 718 Powder
Typical particle size distributions for Inconel 718 powder for AM processes are:
Particle Size (μm) | Percentage (%) |
---|---|
15 to 25 | 55% |
25 to 45 | 30% |
45 to 75 | 10% |
Above 75 | 5% |
Narrower particle size distributions like 15-45 μm can be used but generally wider distributions between 15-75 μm are common. Finer atomized powders below 15 μm are also available. Larger particles above 100 μm may need sieving out.
Production Methods of Inconel 718 Powder
The common production methods for Inconel 718 alloy powder include:
- Gas Atomization – High pressure inert gas (N2 or Ar) disintegrates molten alloy stream into fine droplets which solidify into powder. Provides spherical powder ideal for AM.
- Rotating Electrode Process – Molten material is spun at high speeds in an inert atmosphere to produce flakes or spherical powder. Lower cost than atomization.
- Plasma Rotating Electrode Process (PREP) – Electrodes of Inconel 718 are rotated and melted using a plasma heat source in an inert gas atmosphere. This produces spherical powder suitable for AM.
- Vacuum Induction Melting (VIM) followed by Gas Atomization – Alloy is first melted using VIM to refine composition and remove inclusions. Then atomized into powder.
Gas atomized and plasma rotating electrode powders with controlled particle size distribution are preferred for additive manufacturing with Inconel 718.
Standards and Specifications
Inconel 718 powder manufactured for additive manufacturing applications complies with the following specifications:
Standard/Specification | Organization |
---|---|
AMS 5662 | SAE International |
ASTM B214 | ASTM International |
ISO 21432 | ISO |
Chemistry conforms to AMS 5662 and mechanical properties to AMS 5662 or ASTM B214 after built using AM and heat treatment.
Uses and Applications
The major uses and applications of Inconel 718 alloy powder include:
Aerospace: Critical aerospace components like turbines blades, casing, fasteners, gears, waveguides and airframes are additively manufactured using Inconel 718 powder due to its high strength and performance at elevated temperatures.
Oil and Gas: Used to print downhole tools, valves, wellhead components that must withstand hydrogen sulfide cracking and corrosion.
Automotive and Racing: Lightweight, high performance components like turbochargers, engine valves and exhaust manifolds are 3D printed in Inconel 718 instead of steel.
Medical and Dental: Surgical instruments, dental crowns and implants printed due to biocompatibility and ability to sterilize through autoclaving.
Tooling: Lightweight Inconel 718 tooling 3D printed using AM offers longer life than traditional tool steels.
Pumps, Valves and Marine Hardware: Components exposed to seawater corrosion and marine environments printed in Inconel 718.
Advantages of Inconel 718 Powder
The advantages of using Inconel 718 powder for additive manufacturing include:
- Parts printed in Inconel 718 can match or exceed the strength levels of forgings
- Ability to produce complex, lightweight geometries not possible with castings
- As-printed surface finish much smoother than machined surfaces
- Lower component weight reduces fuel consumption in aerospace applications
- Excellent corrosion resistance in harsh environments without coatings
- High hardness provides good wear and abrasion resistance
- Fully dense components compared to cast porosity defects
- Reduced lead times and costs compared to forgings or castings
Limitations of Inconel 718 Powder
Some limitations or disadvantages associated with Inconel 718 powder include:
- High material costs compared to tool steels or aluminum alloys
- Requires hot isostatic pressing (HIP) after AM to achieve best properties
- Difficult to print and process due to poor thermal conductivity
- Prone to cracking and porosity defects without optimized parameters
- Limited number of metal 3D printer models can process Inconel 718 powder
- Post-processing like supports removal, machining and finishing add to costs
- Qualification and certification requires expensive mechanical testing
Cost Analysis
Typical pricing for Inconel 718 alloy powder for additive manufacturing is summarized below:
Powder Grade | Cost Per Kg |
---|---|
Inconel 718 Pre-alloyed atomized powder | $220 – $350 per kg |
Inconel 718 plasma atomized powder | $245 – $425 per kg |
Inconel 718 gas atomized powder | $275 – $485 per kg |
Inconel 718 HIP powder | $300 – $450 per kg |
Cost depends on powder particle size distribution, morphology, manufacturing method and purchase quantity. Additional costs are incurred for heat treatment, HIP treatment, machining, testing and certification which can exceed the material cost. Buying fully certified aerospace quality powder will be costlier.
Suppliers
Some of the major global suppliers of Inconel 718 nickel alloy powder for AM include:
Company | Brand Names |
---|---|
Sandvik Osprey | Osprey 718 for AM |
Carpenter Additive | CarTech AL718V |
Praxair | 718 Atomized Powder |
Hoganas | 718Bond for AM |
LPW Technology | LP71S-F |
SLM Solutions | IN718 |
Selection Criteria
The main selection criteria for Inconel 718 powder includes:
Chemical composition – Must conform to AMS 5662 or ASTM B214 composition specifications
Particle size distribution – D50 and distribution depends on AM process and desired layer resolution
Powder shape – Highly spherical and smooth powder morphology ensures optimal powder flow and uniform layers
Manufacturing method – Gas atomized and plasma atomized powder preferred over PREP, rotary atomized methods
Impurities – Low oxygen and nitrogen levels to prevent defects and cracking issues
Apparent density and tap density – Higher density improves powder reuse rates and packing
Flow rate – Minimum Hall flow rate of 20 sec for 50 g ensures smooth powder spreading
Comparative Analysis
Comparison between Inconel 718 powder and alternatives:
Alloy | Inconel 718 | Inconel 625 | Haynes 282 |
---|---|---|---|
Density (g/cm3) | 8.19 | 8.44 | 8.36 |
Tensile Strength (MPa) | 1275 | 860 | 1035 |
Max Operating Temp (°C) | 700 | 980 | 730 |
Corrosion Resistance | Excellent | Excellent | Moderate |
Cost Per Kg | High | Moderate | High |
Inconel 718 vs Steel Powders
Parameter | Inconel 718 | Maraging Steel | Stainless Steel |
---|---|---|---|
Strength | Higher | Equivalent | Lower |
Hardness | Higher | Slightly Lower | Much Lower |
Cost | 3-4 times higher | – | Lower |
Advantages vs Stainless Steels
- Greater high temperature strength
- Higher hardness and wear resistance
- Improved corrosion resistance
Disadvantages vs Stainless Steels
- Higher material cost
- Lower ductility and fracture toughness
- More difficult to print and process
Print Parameters for Inconel 718 Powder
Typical range of print parameters for Inconel 718 powder on laser powder bed fusion (L-PBF) systems:
Parameter | Range |
---|---|
Layer thickness (μm) | 20 – 50 |
Laser power (W) | 195 – 400W |
Scan speed (mm/s) | 700 – 1300 |
Hatch spacing (mm) | 0.08 – 0.12 |
Powder bed temperature (°C) | 90 – 180 |
Parameters depend on factors like desired resolution, mechanical properties, build rates, OEM printer specifications and powder characteristics.
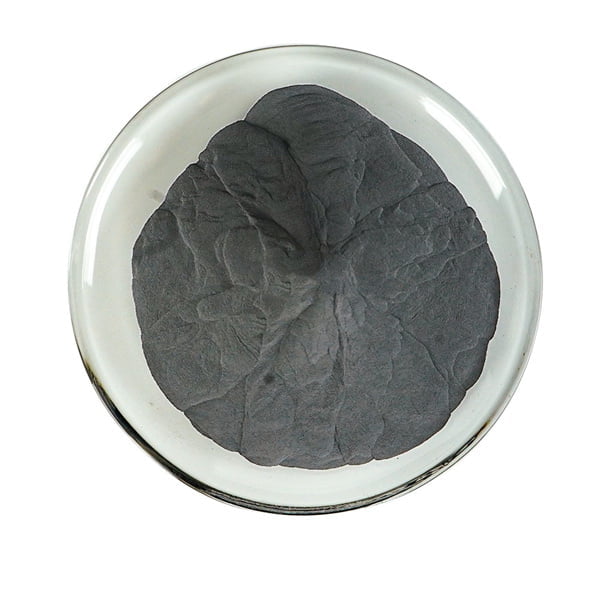
Post-Processing Operations
The common post-processing steps performed on Inconel 718 printed parts include:
- Powder removal: Excess powder is first blown or brushed off from internal cavities and surfaces
- Stress relieving: Heating below solutionizing temperature to remove residual stresses
- Hot isostatic pressing (HIP): Capsule HIP process helps close internal cavities and micropores
- Solution treatment and aging: Precipitation hardening heat treatments to achieve required properties
- Surface machining: CNC machining printed surfaces to lower roughness and bring to tighter tolerances
- Surface conditioning: Glass bead peening, laser polishing or other surface conditioning processes can lower roughness
FAQs
Why is Inconel 718 the most widely used superalloy for metal 3D printing?
Inconel 718 is popular for additive manufacturing due to its excellent strength at high temperatures, good corrosion resistance, ease of fabrication into complex geometries using 3D printing, ability to perform in extreme environments, and adoption in critical applications in aerospace, oil and gas, etc. where failure is not an option.
Does Inconel 718 require heat treatment after AM?
Yes, heat treatment involving solution annealing and multiple step aging are necessary after printing components in Inconel 718 via AM to adjust the microstructure for transforming into hardened precipitates which provide the excellent mechanical properties.
What is the difference between Inconel 625 vs 718 in additive manufacturing?
The main differences are that Inconel 625 has higher weldability while Inconel 718 offers greater yield and tensile strength. Inconel 718 also performs better under cryogenic conditions while Inconel 625 is preferred for resistance to fatigue, stress corrosion cracking and wear.
Should Inconel 718 parts be HIPed after 3D printing?
Hot isostatic pressing (HIP) helps to eliminate internal voids and microporosity in AM Inconel 718 components. HIP improves ductility, fatigue life and corrosion resistance while reducing potential failure points. Aerospace applications require HIP to ensure highest quality and reliability.
Share On
MET3DP Technology Co., LTD is a leading provider of additive manufacturing solutions headquartered in Qingdao, China. Our company specializes in 3D printing equipment and high-performance metal powders for industrial applications.
Inquiry to get best price and customized Solution for your business!
Related Articles
About Met3DP
Recent Update
Our Product
CONTACT US
Any questions? Send us message now! We’ll serve your request with a whole team after receiving your message.
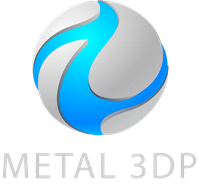
Metal Powders for 3D Printing and Additive Manufacturing