Metal Atomization Equipment Specifications
Table of Contents
Metal atomization is a manufacturing process that turns metal alloys into fine powder. It involves melting the metal and breaking it into droplets using gas or water atomization. The droplets rapidly solidify into powder particles with customized size ranges.
Metal atomization powder has unique properties and is used across industries like automotive, aerospace, biomedical, 3D printing, and more. This article provides a comprehensive overview of metal atomization equipment.
Overview of Metal Atomization Process
Metal atomization uses physical processes to produce fine metallic powders with precise control over particle size, morphology, and microstructure. Here are the key aspects of the metal atomization process:
Parameters | Details |
---|---|
Methods | Gas Atomization, Water Atomization |
Metal Inputs | Iron, Nickel, Cobalt, Copper, Aluminum alloys etc. |
Melting | Induction melting, Arc melting, Electron beam melting |
Atomization | High pressure gas or water breaks molten metal into droplets |
Solidification | Rapid cooling rates produce fine powders |
Particle Size | From 10 microns to 250 microns |
Particle Shape | Spherical, satellite, irregular shapes |
Applications | Metal injection molding, Additive manufacturing, Thermal spray powders |
The starting point is feeding metal alloys in wire or ingot form into a melting unit. The melt pool is then subjected to high velocity gas or water jets that break it into a spray of metal droplets. As the droplets cool rapidly, they solidify into fine spherical powder particles.
By controlling process parameters like gas pressure, melt flow rate and cooling rate, powders can be customized for flowability, density, size range, morphology and microstructure.
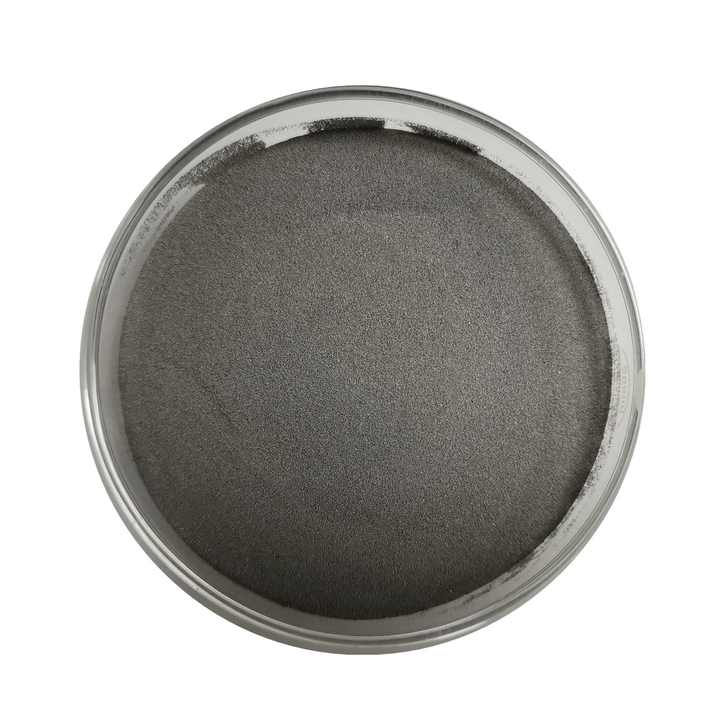
Types of Metal Atomization Equipment
There are two main types of atomization equipment – VIGA (Vacuum Induction Inert Gas Atomization) and EIGA (Electrode Induction Gas Atomization) Equipment.

VIGA (Vacuum Induction Inert Gas Atomization) Equipment
VIGA equipment has a wide range of applications, mainly for the production of high-performance iron-based, nickel-based, cobalt-based, aluminium-based, copper-based and other advanced alloy powder materials. It is widely used in aerospace, health, tooling, automobile, machinery, electronics, new energy and other fields and also suitable for additive manufacturing (3D printing), melting deposition, laser cladding, thermal spraying, powder metallurgy, hot isostatic pressing and other advanced manufacturing processes.
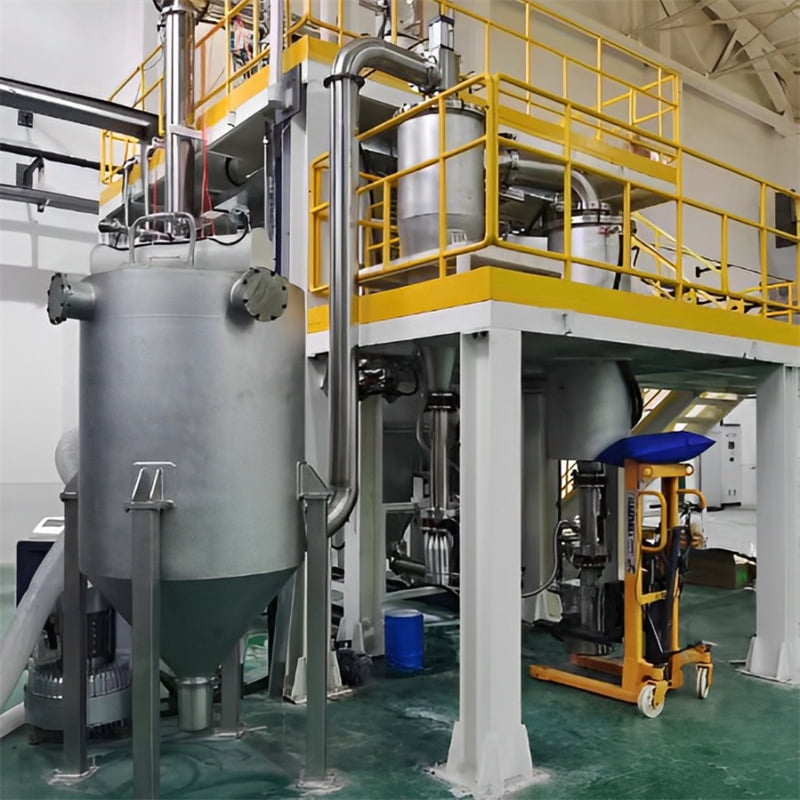
EIGA (Electrode Induction Gas Atomization) Equipment
EIGA equipment is mainly used for active and refractory metal or alloy powders, such as titanium and titanium alloys, superalloys, platinum-rhodium alloys, intermetallic compounds, etc. The powders are widely applied in selective laser melting, laser melting deposition, electron beam selected area melting, powder metallurgy, etc.
Metal powder produced by Metal Atomization Equipment
Aluminum Based Alloy Powder
Aluminum-based alloy powder refers to finely divided particles composed primarily of aluminum, along with other alloying elements mixed in powder form. These alloying elements are added to modify the properties of aluminum for specific applications. Aluminum-based alloy powders are commonly used in various industrial processes, including additive manufacturing, metal injection molding, powder metallurgy, and thermal spraying.
Here are some of the main types of aluminum-based alloy powders along with their primary alloying elements:
- Aluminum 6061: Contains magnesium and silicon as primary alloying elements. It offers good weldability, high strength, and excellent corrosion resistance.
- Aluminum 7075: Strengthened with zinc as the primary alloying element, along with copper, magnesium, and chromium. Known for its high strength-to-weight ratio, it’s often used in aerospace applications.
- Aluminum 2024: Contains copper as the primary alloying element, along with manganese and magnesium. Offers excellent fatigue resistance and is used in structural applications requiring high strength and machinability.
- Aluminum 5052: Contains magnesium as the primary alloying element, with chromium and manganese. Known for its excellent corrosion resistance in marine environments, it’s commonly used in sheet metal fabrication.
- Aluminum 5083: Primarily composed of magnesium, offering excellent corrosion resistance, particularly in seawater. Used in marine applications due to its high strength and weldability.
These are some of the main types of aluminum-based alloy powders, each with specific compositions tailored to meet different application requirements.
Titanium Based Alloy Powder
Titanium-based alloy powder refers to finely divided particles composed primarily of titanium, along with other alloying elements mixed in powder form. These alloying elements are added to modify the properties of titanium for specific applications. Titanium-based alloy powders are commonly used in various industrial processes, including additive manufacturing, powder metallurgy, and thermal spraying.
Here are some of the main types of titanium-based alloy powders along with their primary alloying elements:
- Ti-6Al-4V Powder (Titanium 6-4): This is one of the most widely used titanium alloys, containing 6% aluminum and 4% vanadium. It offers excellent strength, corrosion resistance, and biocompatibility, making it suitable for aerospace, medical, and automotive applications.
- Ti-6Al-2Sn-4Zr-2Mo (Ti-6242): This alloy contains aluminum, tin, zirconium, and molybdenum as the primary alloying elements. It provides high strength, toughness, and creep resistance, often used in aerospace components.
- Ti-6Al-2Sn-4Zr-6Mo (Ti-6246): Similar to Ti-6242 but with higher molybdenum content for improved strength and creep resistance, especially at elevated temperatures.
- Ti-6Al-2Sn-4Zr-2Mo-0.1Si (Ti-6242S): This alloy variant includes a small amount of silicon for enhanced weldability and improved mechanical properties, particularly in welded joints.
- Ti-3Al-2.5V (Ti-3-2.5): Contains 3% aluminum and 2.5% vanadium. It offers good weldability, high strength, and excellent corrosion resistance, commonly used in aerospace and marine applications.
- Ti-10V-2Fe-3Al (Ti-10-2-3): This alloy contains vanadium, iron, and aluminum, offering high strength and toughness at elevated temperatures. It’s often used in aerospace components subjected to high stress and temperature environments.
These are some of the main types of titanium-based alloy powders, each with specific compositions tailored to meet different application requirements.
-
Ti45Nb Powder for Additive Manufacturing
-
TiNb Alloy Powder
-
TiNbZrSn Alloy Powder
-
Ti6Al4V Powder Titanium Based Metal Powder for Additive Manufacturing
-
CPTi Powder
-
TC18 Powder : Unlocking the Power of Titanium Carbide
-
TC11 Powder : A Comprehensive Guide
-
TC4 ELI Powder
-
Best Ti-6Al-4V powder (TC4 Powder)for additive manufacturing
High Temperature Alloy Powder
High temperature alloy powder refers to a type of powdered material composed of various alloying elements, designed to withstand high temperatures and harsh environments while retaining their mechanical properties. These powders are commonly used in additive manufacturing processes like powder bed fusion (such as selective laser melting or electron beam melting) to produce parts for aerospace, automotive, and other industries where high temperatures and corrosion resistance are essential.
Some common types of high temperature alloy powders include:
- Nickel-Based Alloys:
- Cobalt-Based Alloys:
- Stellite
- Haynes 188
- Iron-Based Alloys:
- Stainless Steel 316L
- Tool Steel Powders
These powders are often chosen based on the specific application requirements such as temperature resistance, corrosion resistance, strength, and other mechanical properties needed for the final part.
Metal Atomization System Design
A complete metal atomization system consists of multiple sub-systems for material handling, melting, atomization, and powder processing.
Sub-Systems in a Metal Atomization Equipment
Sub-System | Role | Equipment Used |
---|---|---|
Material handling | Feedstock storage and supply | Hoppers, Conveyors, Feeders |
Melting | Melting metal alloy into uniform liquid | Induction furnace, Arc melting furnace, Electron beam melting |
Atomization | Breaking melt into fine droplets | Atomization chamber, Gas/water nozzles |
Powder handling | Separation, cooling, collection and storage | Cyclones, Screens, Conveyors, Bins |
Critical factors in designing a metal atomization system include:
- Controlling process parameters like temperature, gas/water pressure, flow rates
- Minimizing melt turbulence before atomization
- Nozzle design and uniform distribution of gas/water jets
- Cooling rate control for desired powder microstructure
- Efficient powder separation from atomizing medium
- Containment of fine powders and minimizing hazards
- Quality control through lab testing and sampling points
Metal Atomization Equipment Specifications
Technical specifications vary across different capacity systems from lab scale to high production models.
Typical Specifications for Metal Atomization Equipment
Parameter | Typical Range |
---|---|
Capacity | 1 kg/hr to 5000 kg/hr |
Melting Unit Power | 10 kW to 1 MW |
Temperature | 500°C to 2000°C |
Pressure | 5 bar to 4000 bar |
Nozzle size | 0.5mm to 5mm |
Nozzle material | Tungsten carbide, Silicon carbide |
Powder size | 10 μm to 250 μm |
Enclosure | Stainless steel, Alloy steel |
Height | 2m to 10m |
Footprint | 2m x 2m to 10m x 4m |
Control system | PLC, SCADA |
The capacity, pressure rating, temperature range and footprint increase from lab models to industrial production systems. High precision controls are required to monitor and regulate critical process parameters.
Metal Atomization Equipment Design Standards
Equipment manufacturers follow design codes and standards for critical components to ensure safe and reliable operation.
Relevant Standards for Metal Atomization Equipment
Component | Applicable Standards |
---|---|
Pressure Vessels | ASME SEC VIII Div 1, EN 13445, PD 5500 |
Piping | ASME B31.3, ANSI B16.5 |
Powder handling | NFPA 654, EN 14460 |
Nozzles | ASME MFC-7M |
Controls | IEC 61131, NFPA 79 |
Structural | AISC 360, EN 1993 |
Material composition | ASTM, DIN, BS, UNS, EN |
Compliance with standards related to pressure equipment, combustible dust, controls, materials, and structural fabrication is mandatory. Vendors need to have quality systems and code stamps like ASME U or CE marking.
Applications of Metal Atomization Powders
The unique properties of metal atomization powders make them suitable for some key applications:
Major Applications of Metal Atomized Powders
Application | Alloys Used | Benefits |
---|---|---|
Metal injection molding | Stainless steel, tool steel, copper | High precision, complex parts |
Additive manufacturing | Titanium, aluminum, nickel alloys | Custom alloys, minimal waste |
Thermal spray coatings | Molybdenum, copper, iron alloys | Wear & corrosion protection |
Powder metallurgy | Iron, tungsten heavy alloys | Porous parts, magnets |
Aerospace | Nickel superalloys | High strength engine parts |
Biomedical | Titanium, cobalt chrome | Joint replacement implants |
The microstructure and particle shape influence compressibility, flowability, densification, and sintering response during part making. Gas atomized powders with spherical morphology offer the best performance.
Metal Atomization Equipment Manufacturers
Some leading global manufacturers of metal atomization equipment across small, medium and large scale capacities are:
Prominent Metal Atomization Equipment Manufacturers
Company | Location | Capacities |
---|---|---|
MET3DP | China | Lab, Pilot, Production scale |
EIG | USA | Small to high capacity |
ALD Vacuum Technologies | Germany | Small lab units |
TLS Technik GmbH | Germany | Medium capacity |
Sandvik Materials Technology | Sweden | Large production systems |
Reputable manufacturers have decades of experience in designing customized systems for different alloy groups and powder requirements. They also offer auxiliary equipment like sieves, mills, metallographic testers.
Price Range of Standard Metal Atomization Equipment Models
Capacity | Price Range |
---|---|
Lab scale (1-5 kg/hr) | $100,000 to $250,000 |
Pilot scale (10-50 kg/hr) | $500,000 to $1.5 million |
Production scale (200+ kg/hr) | $2 million to $5 million |
Larger production capacities with multiple atomization streams, bigger melting/heating units, high-end controls and powder handling systems are costlier. Location and site-specific requirements also impact pricing.
How to Choose a Metal Atomization Equipment Supplier
Important factors to consider when selecting a metal atomization equipment supplier:
Selection Criteria for Metal Atomization Equipment Supplier
Parameter | Details |
---|---|
Experience | Years in business, number of installations delivered |
Capabilities | Staff expertise, technology portfolio, R&D facilities |
Flexibility | Customization to meet product requirements |
Standards compliance | Certifications like ISO, industry standards |
After-sales service | Installation support, training, maintenance contracts |
Cost | Pricing models, total cost of ownership |
Delivery | Lead time, shipping, site readiness |
Location | Geographic proximity for support |
Look for an established player with proven expertise across different metals, scale, and powder specifications. Ensure they offer flexible solutions tailored to your needs. Review maintenance costs, spare parts availability, warranties before purchase.
Installing a Metal Atomization System
Metal atomization equipment requires careful site planning and installation. Below are some key guidelines:
Metal Atomization Equipment Installation Checklist
Activity | Details |
---|---|
Site planning | Ensure adequate space, utilities, secondary containment |
Civil works | Concrete foundation, walls, drainage works |
Assembly | Assemble sub-systems as per drawings |
Utilities | Electrical, process water, inert gas lines |
Ventilation | Fume extraction, HEPA filtration |
Commissioning | Dry & wet testing, trial powder runs |
Safety | Integrate safety interlocks, alarms |
Documentation | Operating manuals, P&ID drawings, inspection reports |
Operator training | Classroom and hands-on training |
Proper utilities, safety systems, containment structures and operator training help ensure smooth starting up and safe operation. Vendors provide technical support during installation and commissioning.
How to Operate a Metal Atomization System
Consistent quality powder depends on stable operation following standard procedures:
Metal Atomization Equipment Operation Guidelines
Activity | Instructions |
---|---|
Startup | Energize utilities, run purging cycles, preheat nozzles |
Melting | Charge feedstock, allow adequate melt soak time |
Atomization | Open gas/water valves to rated pressure |
Monitoring | Observe nozzle spray pattern, adjust parameters |
Shutdown | Stop atomization, allow melt to solidify before draining |
Powder handling | Handle hot powder carefully, avoid air ingress |
Maintenance | Inspect consumable parts, maintain spares inventory |
Safety | Ensure interlocks, ventilation are working |
Quality checks | Take samples for size analysis, morphology, chemistry |
Continuous monitoring of process variables like temperature, pressure, water/gas flow is required. Maintenance schedules and standard operation procedures need to be strictly followed.
Maintenance Requirements for Metal Atomization Equipment
Routine maintenance is vital for maximizing equipment life and performance.
Maintenance Checklist for Metal Atomization Equipment
Sub-system | Maintenance Activities | Frequency |
---|---|---|
Melting Unit | Inspect induction coils, charge materials, insulation | Monthly |
Nozzles | Inspect orifice condition, replace nozzles | 500 cycles |
Atomization chamber | Inspect refractory condition | 6 months |
Gas lines | Check for leaks, flow calibration | 3 months |
Water lines | Inspect seals, valves, pumps | Monthly |
Controls | Calibrate sensors, test interlocks | 3 months |
Fume extraction | Check filters, ducts | Weekly |
Powder handling | Inspect bins, seals, gaskets | Weekly |
Critical consumable spares like induction coils, nozzles, gaskets require inventory planning to avoid downtime. Annual maintenance contracts with vendors are advisable.
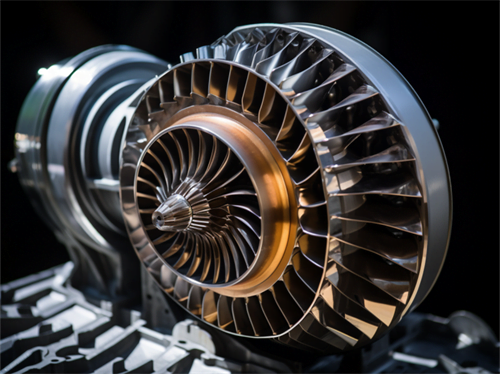
Advantages and Limitations of Metal Atomization
Advantages and Limitations of Metal Atomization Process
Advantages | Limitations |
---|---|
Precise control over particle size and morphology | Higher capital and operating costs |
Custom alloys and microstructures possible | Limited productivity for smaller units |
Minimal melt superheat required | Reactive alloys require inert gas |
Lower oxidation compared to gas atomization | Irregular powder shape with water atomization |
Suitable for reactive alloys using inert gas | Requires auxiliary powder handling equipment |
Near net shaped parts from powders | Safety hazards of fine pyrophoric powders require precautions |
The process is best suited for small batches of specialized powders despite higher costs. Safety procedures for handling reactive fine metal powders are essential. Larger production models offer better economies of scale for high volume applications.
FAQ
Q: What is the difference between gas atomization and water atomization?
A: Gas atomization uses inert gases at lower pressures to produce finer and more spherical powder particles compared to water atomization which uses water at ultra-high pressures for higher throughputs but irregular powder shapes.
Q: What particle size can be achieved with metal atomization?
A: Particle sizes ranging from around 10 microns to 250 microns can be produced depending on the method and operating parameters. Gas atomization can produce finer powders in the 10-100 micron range.
Q: What metals can be atomized into powders?
A: Most alloy systems including steels, aluminum, titanium, nickel, cobalt, copper alloys can be atomized. Refractory metals with very high melting points are difficult to atomize.
Q: How much does a metal atomization equipment system cost?
A: Costs range from around $100,000 for lab units up to several million dollars for large industrial systems, depending on capacity, automation, and customization requirements.
Q: What safety precautions are required for metal atomization?
A: Key requirements include ventilated enclosures, inert gas purging cycles, safety interlocks, adequate containment systems for fine pyrophoric metal powders, and personnel protective equipment.
Q: What determines the particle size distribution of atomized powder?
A: Particle size is influenced by factors like melt flow rate, atomizing gas/water pressure, nozzle design, melt temperature and cooling rate. Optimizing these parameters is key for desired size distribution.
Q: What are the major applications of metal atomization powder?
A: Key applications are metal injection molding, additive manufacturing including 3D printing, thermal spray coatings, powder metallurgy pressing and sintering, aerospace components, biomedical implants.
Q: How often is maintenance required for metal atomization equipment?
A: Routine preventive maintenance is recommended every few months on sub-systems like gas lines, water lines, nozzles, induction coils, and safety interlocks to maximize performance. Consumables may need replacement every few hundred cycles depending on usage.
Conclusion
Metal atomization converts alloys into fine spherical or irregular powders with unique properties tailored to demanding applications across industries. Gas atomization allows finer control over particle size and shape compared to higher volume water atomization.
Careful designing of sub-systems for material handling, melting, atomization and powder collection is required for optimal performance. Reputable vendors provide customizable equipment ranging from small R&D systems to large industrial capacities.
Proper installation, safety features, operator training and routine maintenance are essential to maximize production, efficiency and safety when operating metal atomization units. The atomized metal powders enable manufacturing of high performance components otherwise difficult to produce via conventional metallurgy routes.
Share On
MET3DP Technology Co., LTD is a leading provider of additive manufacturing solutions headquartered in Qingdao, China. Our company specializes in 3D printing equipment and high-performance metal powders for industrial applications.
Inquiry to get best price and customized Solution for your business!
Related Articles
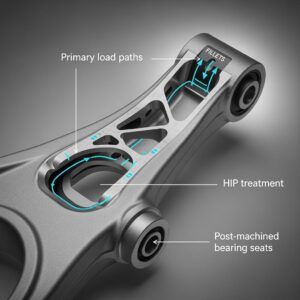
Metal 3D Printing for U.S. Automotive Lightweight Structural Brackets and Suspension Components
Read More »About Met3DP
Recent Update
Our Product
CONTACT US
Any questions? Send us message now! We’ll serve your request with a whole team after receiving your message.