CuCrZr Powder for metal 3d Printing
CuCrZr powder is an alloy powder composed of copper (Cu), chromium (Cr) and zirconium (Zr). It offers a unique combination of properties that make it suitable for high performance applications requiring high strength, good conductivity and resistance to softening at elevated temperatures.
Low MOQ
Provide low minimum order quantity to meet different needs.
OEM & ODM
Provide customized products and design services to meet unique customer needs.
Adequate Stock
Ensure fast order processing and provide reliable and efficient service.
Customer Satisfaction
Provide high quality products with customer satisfaction at the core.
share this product
Table of Contents
CuCrZr Powder Overview
CuCrZr powder is an alloy powder composed of copper (Cu), chromium (Cr) and zirconium (Zr). It offers a unique combination of properties that make it suitable for high performance applications requiring high strength, good conductivity and resistance to softening at elevated temperatures.
Composition of CuCrZr Powder
CuCrZr is a precipitation hardened alloy meaning its high strength comes from coherent precipitates formed in the metal matrix. The composition plays a key role in achieving optimal precipitation hardening response. Here are the typical composition ranges:
Element | Composition Range |
---|---|
Copper (Cu) | Remainder |
Chromium (Cr) | 0.5 – 1.2 wt% |
Zirconium (Zr) | 0.03 – 0.3 wt% |
- Copper forms the matrix and provides thermal and electrical conductivity.
- Chromium contributes to solid solution strengthening and forms precipitates to impede dislocation motion.
- Zirconium forms coherent precipitates with copper enabling precipitation hardening.
The chromium and zirconium content is optimized to maximize strength through precipitation hardening while still retaining decent conductivity.
Properties of CuCrZr Powder
CuCrZr powder offers an exceptional combination of strength, conductivity and heat resistance owing to its precipitation hardened nature. Here are some key properties:
Property | Value |
---|---|
Density | 8.8 g/cm3 |
Electrical Conductivity | 22 – 48% IACS |
Thermal Conductivity | 200 – 300 W/m-K |
Melting Point | 1065°C |
Coefficient of Thermal Expansion | 16.5 x 10<sup>-6</sup> /°C |
Elastic Modulus | 124 GPa |
Yield Strength | 350 – 650 MPa |
Elongation | 8-15% |
Oxidation Resistance | Good up to 900°C |
- It has high strength coming from precipitation hardening while still retaining moderate conductivity. Strength can be tailored via heat treatment.
- Excellent conductivity compared to precipitation hardened stainless steels due to higher copper content in matrix.
- Good heat resistance with strength and conductivity retention up to 400-500°C. Less prone to softening compared to other Cu alloys.
- Resistant to oxidation and corrosion due to the formation of protective Cr2O3 oxide scale.
This unique property profile makes CuCrZr suitable for applications like resistance welding electrodes, thermal management components and high temperature springs.
Applications and Uses of CuCrZr Powder
The balanced properties of CuCrZr powder make it suitable for the following applications:
Application | Reason for Use |
---|---|
Resistance Welding Electrodes | High strength, good conductivity, resistance to deformation at elevated temperatures |
Heat Sinks and Heat Pipes | High thermal conductivity combined with high temperature strength |
Electrical Contacts and Connectors | Good conductivity, high strength enables miniaturization |
High Temperature Springs | Strength retention at elevated temperatures |
Glass Sealing Alloys | Close match of CTE with borosilicate glass |
- Resistance welding electrodes – Its excellent conductivity generates less heat while welding allowing faster weld times. High strength resists mushrooming of electrode tips.
- Thermal management – Used in heat exchangers, heat sinks, heat pipes etc. where high thermal conductivity rapidly dissipates heat while maintaining mechanical integrity.
- Electrical contacts – Can replace beryllium copper contacts in many applications due to superior strength and similar conductivity.
- High temperature springs – Used for springs operating up to 500°C without losing load capacity unlike steel springs.
- Glass-to-metal seals – Its CTE matches borosilicate glass enabling low stress glass sealing applications.
The precipitation hardening ability of CuCrZr allows tailoring strength as per the specific application requirements simply by modifying heat treatment parameters.
CuCrZr Powder Specifications
CuCrZr powder is available in various size ranges, purities and can be customized as per application needs. Here are some common specifications:
Specification | Details |
---|---|
Size range | 10 – 150 microns |
Purity | Up to 99.9% |
Carbon content | <100 ppm |
Oxygen content | <500 ppm |
Particle shape | Spherical, irregular |
Apparent density | Up to 80% of theoretical density |
Flow rate | Up to 25 s/50 g |
- Powder size directly affects density and surface finish of finished parts. Finer powder produces higher density and better surface finish.
- High purity reduces contamination issues during consolidation and improves final properties.
- Gas atomized powder has smooth spherical morphology ideal for additive manufacturing. Water atomized powder has irregular shape useful for press and sinter applications.
- Apparent density indicates how tightly powder can be packed. Higher densities improve sintering.
- Flow rate affects ease of powder handling and uniform die filling in press and sinter process.
Powder attributes can be customized like particle size distribution, shape, apparent density etc. as per application requirements.
Consolidation Methods for CuCrZr Powder
CuCrZr powder can be consolidated into fully dense components using methods like:
Consolidation Method | Details |
---|---|
Additive Manufacturing | Selective laser melting, Electron beam melting |
Press and Sinter | Followed by infiltration or further heat treatment |
Hot Isostatic Pressing | Full densification of encapsulated powder |
Extrusion | Forging of powder blended with lubricants |
Spark Plasma Sintering | Rapid densification using pulsed current |
Additive manufacturing methods like selective laser melting and electron beam melting are commonly used to produce complex, net-shape CuCrZr parts with fine microstructure directly from powder.
Press and sinter method is economical for high volume production but involves multiple steps. Final properties depend on sintering temperature, time, atmosphere etc.
Hot isostatic pressing applies high pressure allowing full densification at lower temperatures. It reduces porosity in additively manufactured parts and improves fatigue life.
Extrusion and spark plasma sintering are alternate methods suitable for simpler geometries. The consolidation process influences final microstructure, properties and performance.
Heat Treatment of CuCrZr Alloy
A key benefit of CuCrZr alloy is its precipitation hardening response. Solutionizing and aging heat treatments can significantly alter its strength as per requirements:
Heat Treatment | Details |
---|---|
Solution Annealing | 850-980°C, water quench. Dissolves precipitates, softens alloy |
Aging | 350-500°C for 1-4 hours. Controls precipitation and hardening. |
Stress Relieving | 350°C for 1 hour. Removes residual stresses. |
Solution annealing dissolves chromium and zirconium in solid solution followed by rapid quenching to form a supersaturated solid solution. Subsequent aging treatment nucleates fine coherent precipitates resulting in precipitation hardening.
Aging time and temperature directly controls the hardening response. Lower aging temperature and shorter times preserve conductivity. Precipitation hardening can triple the strength compared to solutionized condition.
Stress relieving helps reduce residual stresses from prior cold or hot working to minimize distortion during machining.
Comparison of CuCrZr Powder with Alternatives
CuCrZr competes against alloys like precipitation hardened stainless steels, beryllium copper and nickel silver:
Alloy | CuCrZr | 17-4PH SS | Be-Cu | Ni-Ag |
---|---|---|---|---|
Strength | Excellent | Excellent | Fair | Good |
Conductivity | Good | Poor | Excellent | Good |
Workability | Fair | Good | Excellent | Excellent |
Weldability | Fair | Fair | Excellent | Good |
Cost | Moderate | High | Very High | Moderate |
- 17-4PH stainless has comparable strength but significantly lower conductivity due to higher Cr and Ni content.
- Beryllium copper has excellent conductivity but lower strength levels. Expensive and toxicity issues.
- Nickel silver has good strength but lower operating temperatures. Excellent formability.
- CuCrZr offers the best balance of strength, conductivity, workability and cost for many applications.
For strength plus conductivity combination, CuCrZr provides higher performance and lower cost compared to precipitation hardened stainless steels or beryllium copper alloys.
CuCrZr Powder Suppliers
CuCrZr powder is supplied by specialty metal powder producers. Here are some of the major suppliers:
Supplier | Powder Attributes |
---|---|
Sandvik | Size range 10-150 μm, Apparent density up to 65%, Irregular and spherical powder |
Hoganas | Size range 45-150 μm, Apparent density up to 80%, Spherical powder, High purity |
Pometon | Size range 10-63 μm, Apparent density up to 65%, Spherical and irregular powder |
CNPC Powder | Size range 10-150 μm, Apparent density up to 75%, High purity |
Various powder grades are available optimized for additive manufacturing, press and sinter applications, or tailored for specific customer requirements.
Reputable suppliers have extensive quality control in powder production and provide mill certificates with proof of batch composition.
CuCrZr Powder Pricing
As a specialty alloy powder, CuCrZr is more expensive than standard material powders. Here are some typical pricing ranges:
Powder Grade | Particle Size | Price Range |
---|---|---|
CuCrZr for AM | 15-45 μm | $100-150 per kg |
CuCrZr for Press & Sinter | 45-150 μm | $50-100 per kg |
High Purity CuCrZr | 10-45 μm | $180-250 per kg |
- Fine powder below 45 microns is generally over $100/kg ideal for additive manufacturing.
- Coarser powder 45-150 microns costs $50-100/kg suitable for press and sinter route.
- High purity (>99.9%) powder intended for critical applications commands premium pricing over $180/kg.
- Reducing oxygen and carbon content improves consolidation and final properties.
- Prices vary with quantity, size range, quality level of powder.
Volume discounts from 1 kg to multiple tons may be negotiated with suppliers. High purity powder with controlled particle size distribution attracts higher pricing.
CuCrZr Powder: Health and Safety
Like most metal powders, CuCrZr powder requires careful handling to minimize health and safety risks:
Hazard | Precautions | PPE |
---|---|---|
Eye contact | Avoid direct contact. Do not rub eyes after exposure. Rinse with water if contacted. | Safety goggles |
Skin contact | Avoid direct contact. Wash affected areas thoroughly with soap and water. | Gloves |
Inhalation | Avoid breathing powder dust. Ensure adequate ventilation. | Approved respirators |
Ingestion | Avoid hand to mouth contact. Wash hands after handling. | – |
Fire | Use dry sand to extinguish metal powder fire. Do not use water. | Fire safety gear |
- Wear PPE – goggles, gloves, respirator when handling powder to minimize contact.
- Practice good hygiene after working with powder.
- Prevent accumulation of powder dust on surfaces.
- Store sealed containers in cool, dry area away from sources of ignition.
Refer to SDS for complete safety information. Get medical assistance if exposure causes irritation. Having proper safety protocols minimizes risks when handling CuCrZr powder.
Inspection and Testing of CuCrZr Powder
To ensure high quality and consistency, CuCrZr powder should be inspected and tested for:
Parameter | Method | Specification |
---|---|---|
Chemical composition | XRF, wet chemistry | Conformance to specified Cu, Cr and Zr content |
Particle size distribution | Laser diffraction, sieving | Median size, D10, D90 within specified range |
Powder morphology | SEM imaging | Spherical shape, minimal satellites for AM powder |
Apparent density | Hall flowmeter | As specified for application |
Flow rate | Hall flowmeter | As specified for application |
Impurities | ICP, LECO analysis | Low oxygen and nitrogen content |
Proper in-process QC testing and final inspection ensures the powder meets the chemical, physical and morphological attributes required for the intended application. Routine testing should be implemented by both powder producer and user.
FAQs
Q. What is CuCrZr alloy used for?
A. CuCrZr is used in applications requiring high strength combined with good electrical and thermal conductivity like resistance welding electrodes, heat sinks, and high temperature springs.
Q. How is CuCrZr powder made?
A. CuCrZr is produced via gas atomization or water atomization of the molten alloy to create fine spherical or irregular powder particles optimally sized for AM or press and sinter use.
Q. What affects the properties of CuCrZr parts?
A. Properties depend on composition, powder quality, consolidation method and parameters, heat treatment, and microstructure. The precipitation hardening ability of CuCrZr also allows customization of strength.
Q. What is the difference between gas atomized and water atomized CuCrZr powder?
A. Gas atomized powder has a spherical morphology ideal for AM processing whereas water atomized powder has an irregular shape suitable for press and sinter application.
Q. Does CuCrZr alloy need heat treatment?
A. Yes, solution annealing and aging heat treatments allow optimizing the strength and conductivity by controlling precipitation in the alloy microstructure.
Q. What is the typical price for CuCrZr powder?
A. CuCrZr powder ranges from $50/kg for press and sinter grade to $250/kg for high purity AM grade powder. Finer size fractions and higher purity increase cost.
Get Latest Price
About Met3DP
Product Category
HOT SALE
CONTACT US
Any questions? Send us message now! We’ll serve your request with a whole team after receiving your message.
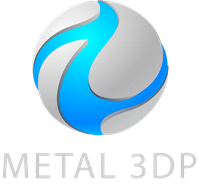
Metal Powders for 3D Printing and Additive Manufacturing