17-4PH Stainless Steel Metal Powder for MIM
17-4PH stainless steel is a precipitation hardening martensitic stainless steel that contains approximately 4% copper by composition. The powder metallurgy grade of 17-4PH stainless steel is an ideal choice for metal injection molding (MIM) applications due to its combination of high strength, good corrosion resistance, and excellent mechanical properties that can be further enhanced through precipitation hardening heat treatments.
Low MOQ
Provide low minimum order quantity to meet different needs.
OEM & ODM
Provide customized products and design services to meet unique customer needs.
Adequate Stock
Ensure fast order processing and provide reliable and efficient service.
Customer Satisfaction
Provide high quality products with customer satisfaction at the core.
share this product
Table of Contents
Overview
17-4PH stainless steel is a precipitation hardening martensitic stainless steel that contains approximately 4% copper by composition. The powder metallurgy grade of 17-4PH stainless steel is an ideal choice for metal injection molding (MIM) applications due to its combination of high strength, good corrosion resistance, and excellent mechanical properties that can be further enhanced through precipitation hardening heat treatments.
17-4PH powder provides an attractive option for MIM versus other competing alloys because of its dimensional stability during sintering and overall ease of processing. Parts made from 17-4PH metal powder feedstocks demonstrate high green strength for complex geometries, good moldability, and clean burnout with minimal residue.
In the following sections we will cover the composition, properties, applications, specifications, suppliers, and other technical details related to 17-4PH stainless steel powder for use in metal injection molding.
Composition
The nominal composition of 17-4PH stainless steel is shown below, with chromium, nickel, and copper as the main alloying elements:
Table: 17-4PH Stainless Steel Composition
Element | Weight % |
---|---|
Chromium (Cr) | 15.0 – 17.5 |
Nickel (Ni) | 3.0 – 5.0 |
Copper (Cu) | 3.0 – 5.0 |
Niobium (Nb) + Tantalum (Ta) | 0.15 – 0.45 |
Silicon (Si) | max 1.0 |
Manganese (Mn) | max 1.0 |
Carbon (C) | max 0.07 |
Sulfur (S) | max 0.03 |
Phosphorus (P) | max 0.04 |
Iron (Fe) | Balance |
The copper content is the distinguishing factor for 17-4PH stainless steel versus 17-4, which contains 4.0-6.0% copper. The lower copper in 17-4PH provides better ductility and impact properties while retaining high strength.
Silicon, manganese, carbon, sulfur, and phosphorus are kept to trace levels to maximize corrosion resistance and avoid carbide precipitation. The niobium and tantalum additions help refine the grain structure during sintering.
Properties
17-4PH stainless steel exhibits an excellent combination of high strength and good ductility in the precipitation hardened condition. Key properties in the H900 condition are provided below:
Table: Properties of 17-4PH Stainless Steel
Property | Value |
---|---|
Density | 7.8 g/cm3 |
Ultimate Tensile Strength | 1240-1300 MPa |
Yield Strength (0.2% offset) | 1100-1160 MPa |
Elastic Modulus | 190-210 GPa |
Elongation | 10-15% |
Hardness | 39-43 HRC |
Impact Toughness | 50-60 J |
Fatigue Strength | 550 MPa |
Shear Strength | 760 MPa |
Compressive Strength | 1275 MPa |
The precipitation hardening heat treatment used to achieve these high strength levels involves solution annealing at 900-950°C followed by aging at 450-500°C. This results in very fine copper-rich precipitates that hinder dislocation movement and strengthen the metal matrix while retaining ductility.
In the solution annealed condition without aging, 17-4PH stainless steel has lower but still respectable mechanical properties on par with 400 series stainless steels. It provides a good balance of moderate strength and ductility for cases where full hardening is not required.
The corrosion resistance of 17-4PH is comparable to martensitic 410 and 416 stainless steels, providing useful resistance to atmospheric corrosion and many mild chemicals. However, it has lower resistance compared to 300 series austenitic stainless steels.
Applications
The high strength after hardening and moderate corrosion resistance make 17-4PH stainless steel a popular choice for metal injection molded parts serving the following applications:
- Aerospace and aircraft components
- Orthopedic and dental implants
- Automotive, engines, valves
- Plastic injection molds
- Industrial tooling, punching/stamping tools
- Food processing and pharmaceutical equipment
- Petrochemical pumps, valves, instrumentation
- Consumer products like knives, marine hardware
- Watch cases, jewelry settings
MIM is advantageous to produce small, complex parts with good as-sintered mechanical properties. The excellent polishability of 17-4PH also suits it for decorative applications.
Versus other MIM alloys, 17-4PH offers higher strength than 316L stainless steel, similar or better strength than 420 and 17-4 stainless with better toughness, and corrosion resistance superior to tool steels.
Metal Powder Specifications
17-4PH stainless steel powder for MIM feedstock is commercially available in various size ranges, chemistries, and morphologies. Some common specifications are provided below:
Table: 17-4PH Stainless Steel Metal Powder Specifications
Attribute | Details |
---|---|
Particles sizes | 3-5 um, 5-9 um, 10-20 um |
Chemistry range | Per AMS 5643, ASTM A564, ASTM A705 |
Carbon content | <0.1%, ultra low carbon |
Oxygen content | <0.6%, low oxygen |
Morphologies | Spherical, partially spherical |
Apparent density | 3.0-4.5 g/cm3 |
Tap density | 4.5-5.5 g/cm3 |
Flow rate | 15-35 s/50g |
Powder quality is critical for high performance MIM parts. Key characteristics like powder morphology, particle size distribution, purity, and powder flow behavior determine the quality of the feedstock and the resulting component properties.
Spherical powder morphology provides the best flow and packing density for MIM. Small particle sizes (<20 um) are preferred for capturing fine features, while larger sizes improve flow and moldability.
Powder Manufacturing
17-4PH powder is manufactured using gas atomization or inert gas atomization processes. High pressure water atomization is also occasionally used.
In gas atomization, the alloy melt stream is disintegrated into fine droplets by high velocity inert gas jets. The droplets rapidly solidify into powder particles with a spherical shape. Particle size distribution is controlled via the gas flow rate, nozzle design, and other process parameters.
Water atomization uses water jets for disintegration of the metal stream. It produces irregular, satellite-type powder particles. For MIM use, the powder requires additional conditioning steps to make it spherical.
Vacuum inert gas processes produce the most clean and pure 17-4PH powder for high performance MIM feedstocks. The inert gas prevents oxidation of the melt and powder.
Standards and Grades
17-4PH stainless steel powder and MIM parts meet the following standards and specifications:
- ASTM A564 – Standard for precipitation hardening stainless steel wire and strip
- ASTM A705 – Standard for precipitation hardening cobalt-chromium-nickel-copper alloy (PH15-7Mo) powder
- AMS 5643 – Precipitation hardening stainless steel powder, grades PH13-8Mo, PH15-7Mo
- AMS 5646 – Stainless steel 17-4, precipitation hardening
- AMS 5803 – Stainless steel 15-5, powder metallurgy
Available product designations and equivalent grades are:
- 17-4PH – UNS S17400 (most common)
- 15-5PH – UNS S15500
- X5CrNiCu15-5 – DIN 1.4545
- 1RK91 – AFNOR Z6CNNbCu15-05
Compositional grades meet AMS 5643 Group 1 alloy ranges. Ultra-low carbon powder with <0.03% C is also available.
Suppliers
17-4PH stainless steel metal powder for MIM is commercially produced by the major specialty alloy and stainless steel powder suppliers:
Table: 17-4PH Stainless Steel Powder Manufacturers
Company | Brand Names |
---|---|
Sandvik | Osprey + Amperit |
Praxair | Printsalloy PH |
Carpenter | Hydramite PH |
Höganäs | Stellite 21 + Densimet PH |
CNPC | FSM-17-4PH |
The powder can be purchased through metal powder distributors, MIM service bureaus, toll processors, and feedstock suppliers.
Cost Analysis
The powder cost for 17-4PH stainless steel is moderately high, ranging from $25-$45 per kg in small quantities. Price is lower for larger orders above 1000 kg.
In comparison, 316L stainless steel powder costs $15-$30/kg while tool steel powders (H13, P20) run $12-25/kg.
For the finished MIM part, materials account for 50-70% of the unit cost depending on part size and complexity. Smaller parts in higher volumes will have a lower share of materials cost versus secondary operations.
Design Recommendations
To successfully apply 17-4PH stainless steel powder and achieve full properties, the following design guidelines for MIM should be followed:
- Use minimum wall thicknesses of 0.3-0.5 mm for adequate strength
- Maintain aspect ratios under 8:1 for complex shapes
- Include radii of 0.25 mm or greater to avoid stress concentrations
- Gate with >0.5 mm thickness and >35% cross-section of cavity opening
- Anisotropic shrinkage is ~17% on main axes, ~20% on thickness direction
- Achieve >92% density after sintering for required mechanicals
Processing Considerations
Key processing steps in using 17-4PH powder feedstocks for metal injection molding include:
- Mixing: High shear mixing of powder and binder components to form homogenous feedstock with uniform powder loading around 62-68% by volume.
- Molding: Using injection molding parameters suited for high solids loading feedstocks – high shot size, fast injection speed, high holding pressure.
- Debinding: Solvent debinding followed by thermal debinding to completely remove binder components and leave brown part ready for sintering.
- Sintering: Sintering in vacuum or hydrogen atmosphere to ~1300°C to achieve full density. Sintering shrinkage should be compensated in mold tooling.
- Heat treatment: Solution annealing followed by aging/precipitation hardening as required to achieve strength requirements.
- Secondary operations: May include coining, drilling, tapping, surface treatments, plating, laser marking etc.
MIM service bureaus and toll processors have established best practices for 17-4PH MIM to ensure dimensional accuracy and repeatable mechanical properties part-to-part.
Inspection and Testing
Some of the inspection and testing methods used for quality control and validation of 17-4PH MIM parts are:
- Chemical analysis – ICP and OES to verify composition and gas levels
- Particle size analysis – Laser diffraction to check powder size distribution
- Density testing – Archimedes method and helium pycnometry
- Tensile testing – ASTM E8, to obtain UTS, yield strength, elongation
- Hardness testing – Rockwell and Vickers to check hardness
- Microstructure – Optical microscopy and SEM to examine phases
- Grain size – ASTM E112, comparison methods to determine grain size
- Defect analysis – Dye penetrant testing to identify surface defects
Well-equipped metallurgical labs have the capabilities to carry out these tests in accordance with international test standards for metal powders and industrial parts. This ensures compliance to specifications during alloy powder manufacture, MIM part production, and for final part qualification.
Health and Safety
17-4PH stainless steel powder and parts do not pose any significant health hazards in solid form. However, the following recommended practices should be observed when handling, processing, or machining this material:
- Wear PPE – gloves, respiratory protection, eye shields when handling powder
- Use dust extraction when cleaning powder spills or machining sintered parts
- Avoid breathing powder dusts and fumes from melting/sintering operations
- Prevent and treat cuts, abrasions to avoid exposure to metal particles
- Follow safe powder handling and transfer procedures if loading powder feedstock
- Use non-sparking tools and ground equipment if machining sintered parts
- Ensure adequate ventilation and wear PPE when welding or brazing 17-4PH components
- Dispose according to local environmental regulations and avoid powder releases to the environment
With sound procedures, 17-4PH powder and MIM parts do not pose any significant hazards. Main risks are potential irritation from dust exposure and cuts from handling. Proper ventilation, PPE use, and secure storage mitigate these risks.
FAQ
Q: What particle size 17-4PH powder is recommended for MIM?
A: 10-20 microns is commonly used, but sizes from 3-45 microns work depending on part geometry. Finer <10 um powder captures details better but can be challenging for molding.
Q: Does 17-4PH powder require handling in inert atmosphere?
A: Not necessarily, it can be handled in air, but an inert glovebox ensures oxygen and moisture levels are minimized for purity.
Q: What is the difference between 17-4 and 17-4PH stainless steel?
A: 17-4PH has lower copper content (3-5% vs. 4-6% in 17-4) giving better impact toughness and ductility for same strength level.
Q: Can you age harden 17-4PH stainless steel multiple times?
A: Yes, 17-4PH can be precipitation hardened repeatedly. Each cycle returns it to high strength, but ductility may decrease with repeated aging.
Q: What is the typical surface finish achieved with 17-4PH MIM parts?
A: As-sintered surface is around Ra 3-5 microns. Polishing and etching can achieve under 0.5 micron. Plating also produces smooth surfaces.
Q: Does 17-4PH work for metal 3D printing compared to MIM?
A: Yes it can be used for DMLS and binder jetting but requires adapted parameters versus MIM. Cooling rates are higher so properties differ.
Q: What types of post processing are commonly done on 17-4PH MIM parts?
A: Machining, drilling, tapping, grinding, EDM, shot peening, passivation, electropolishing, plating, heat treating, welding, and laser marking.
Q: What plating options work well over 17-4PH stainless steel?
A: Electroless nickel, hard chrome, zinc nickel, tin, copper, and precious metal plating like silver, gold, and rhodium work well for corrosion or wear resistance.
Get Latest Price
About Met3DP
Product Category
HOT SALE
CONTACT US
Any questions? Send us message now! We’ll serve your request with a whole team after receiving your message.
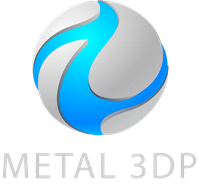
Metal Powders for 3D Printing and Additive Manufacturing