Titanium Metal Powder
Table of Contents
titanium metal powder metallurgy enables fabricating advanced lightweight structural parts combining high specific strength, corrosion resistance and biocompatibility. This guide covers titanium powder production methods, characteristics, alloying strategies, applications, specifications, pricing, and comparisons against alternative metals. It also includes research directions and expert recommendations on processing titanium powder for optimized properties.
Overview
Key attributes make titanium metal powder useful across industries from aerospace to medical:
- Highest strength-to-weight ratio of any metallic element
- Fully biocompatible and non-toxic
- Resists saltwater, aquatic and physiological corrosion
- Thermally inert from cryogenic to 600°C temperatures
- More ductile than competing high-strength alloys
- Powder bed fusion 3D printing compatibility
- Allows lightweight composites and reinforced structures
Continued titanium powder metallurgy developments now enable larger printed parts for orthopedic implants, aerospace components, automobile systems and many general engineering applications leveraging titanium’s intrinsic benefits.
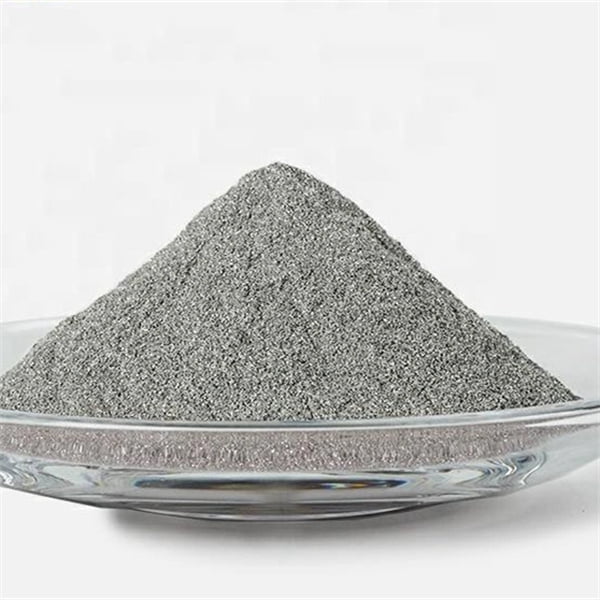
Titanium Metal Powder Composition
Commercially pure titanium comprises >99% titanium with low oxygen and iron impurities:
Element | Weight % | Role |
---|---|---|
Titanium (Ti) | 99.5%+ | Corrosion resistance, strength |
Oxygen (O) | <0.20% | Contaminant – reduces ductility |
Iron (Fe) | <0.30% | Contaminant – reduces corrosion resistance |
Nitrogen (N) | <0.03% | Contaminant – causes embrittlement |
Carbon (C) | <0.10% | Contaminant – reduces bonding |
The high reactivity of titanium means it is never found in pure form naturally. But once extracted and purified into powder, it demonstrates exceptional properties suitable for manufacturing high performance parts.
Characteristics and Properties
- High tensile strength – 490 MPa
- Density – 4.5 g/cm3
- Melting point – 1668°C
- Thermal expansion – 8.6 μm/(m.K)
- Electrical resistivity – 420 nΩ.m
- Thermal conductivity – 21.9 W/(m.K)
- Paramagnetic with no biotoxicity
- Excellent biocompatibility
These properties depend strongly on impurity controls during powder production stages as described next.
Titanium Powder Production Methods
Armstrong Process
- Reducing titanium tetrachloride with sodium/magnesium under inert atmosphere
- Facilitates low interstitial elemental powder suited for additive manufacturing
Hydride-Dehydride (HDH) Process
- Most common method converting titanium sponge into spherical powder
- Lower cost but higher oxygen pickup requiring optimization
Steps | Details |
---|---|
Feedstock | Titanium ingot or sponge |
Hydriding | Process reacting Ti with hydrogen to make brittle TiH2 |
Milling | Crushing hydride into fine powder particles |
De-hydriding | Carefully removing hydrogen from TiH2 |
Conditioning | Desiccation, blending, particle size distribution adjustment |
Final Testing | Chemical assays, particle size distribution, morphology checks |
Key characteristics:
- Particle sizes tuned between 15 microns to 150 microns
- Near spherical morphologies with some satellites
- Controlled low oxygen and nitrogen impurity levels
- Minimized surface oxidation using stabilization heat treatments
- Custom chemistry blending possible by mixing hydride powders
The next section highlights some approaches to consolidate titanium powder into end use parts and components.
Applications Using Titanium Metal Powder
Additive Manufacturing
- 3D printing complex geometries using laser powder bed fusion
- Aerospace and medical implants like orthopedic knee/hip joints
- Light weighting otherwise machined components
Powder Injection Molding
- High volume net shape small components like fasteners
- Cost effective consolidation into titanium hardware
Metal Injection Molding
- Small intricate titanium parts with thin walls
- Corrosion resistant valves and fittings
Powder Metallurgy Press and Sinter
- Hot Isostatic Pressing of encapsulated titanium
- Porous structures like bone in-growth surfaces
Thermal Spraying
- Wear and corrosion resistant titanium coatings
- Salvaging worn components via metallic coatings
Emerging: Binder jet 3D printing using polymer adhesives alongside ultrasonic consolidation and cold spray additive techniques now under development.
Next we outline general specification details used to order custom titanium powder.
-
Ti45Nb Powder for Additive Manufacturing
-
TiNb Alloy Powder
-
TiNbZrSn Alloy Powder
-
Ti6Al4V Powder Titanium Based Metal Powder for Additive Manufacturing
-
CPTi Powder
-
TC18 Powder : Unlocking the Power of Titanium Carbide
-
TC11 Powder : A Comprehensive Guide
-
TC4 ELI Powder
-
Best Ti-6Al-4V powder (TC4 Powder)for additive manufacturing
Titanium Powder Specifications
Commercially available titanium powder for industrial uses conforms to established quality metrics:
Parameter | Typical Values |
---|---|
Particle Size Distribution | 10 μm to 150 μm |
Particle Shape | Predominantly spherical |
tap density | 2.2 g/cc to 3.0 g/cc |
Apparent density | 1.5 g/cc to 2.0 g/cc |
Purity | 99.7% titanium content |
Oxygen Impurity | <2000 ppm |
Nitrogen Impurity | <150 ppm |
Hydrogen Impurity | <100 ppm |
Flowability | Improved via dry coatings |
Particle engineering – Smaller is difficult but better. Larger than 100 microns risks imperfections.
Purity – Vital to properties and depends on production route.
Powder characteristics – Matched to consolidation technique and desired material performance.
Significant customization possible but requires MOQ batch commitments. Supply partnerships facilitate application development.
Titanium Powder Processing Insights
Handling fine titanium powder poses combustion risks needing safety controls:
- Use inert gas glove boxes for storage and handling
- Avoid storing bulk quantities near ignition sources
- Electrically ground equipment to dissipate static buildup
- Employ dedicated vacuum and ventilation systems
- Thermally protect reactive intermediates like hydride
- Follow strict safety protocols given material reactivity
The next section examines the economics around titanium powder which remains costlier than traditional wrought metal forms.
Titanium Powder Price Analysis
Product | Price Range |
---|---|
R&D grade Ti powder | $800+ per kg |
Industrial grade | $100+ per kg |
Aerospace grade | $200+ per kg |
Medical grade | $500+ per kg |
Powder production economics dominate finished part costs relative to added material value. But lightweight potential justifies adoption for aviation, space and racing mobility applications.
Tight chemistry requirements for biocompatibility certification uplift medical pricing tiers. High nitrogen makes powder unsuitable for bone contact implant devices.
Supply partnerships and qualified LTA arrangements help secure best pricing stabilizing variable raw material volatility in export-controlled titanium sponge costs.
Comparison Against Alternatives
Titanium competes against steels, aluminum alloys, magnesum and advanced composites:
Material | Tensile Strength | Density | Corrosion Resistance | Bio-compatibility | Cost |
---|---|---|---|---|---|
Titanium Ti64 | High | Light | Excellent | Excellent | $$$ |
Stainless Steel 316L | Medium | Heavy | Good | Fair | $ |
Al 6061 | Medium | Light | Poor | Good | $ |
CoCr Alloys | High | Heavy | Excellent | Toxicity risks | $$ |
Mg AZ91 | Low | Lightest | Fair | Good | $ |
Peek Polymer | Medium | Low | Excellent | Bio-inert | $$$ |
Titanium Benefits
- Highest strength to weight ratio
- Full corrosion resistance
- Proven biocompatibility
- Available supply infrastructure
Titanium Limitations
- High sensitivity to design geometries
- Tricky burn-out and debinding
- Reactive powder handling needs controls
- Relatively expensive feedstock pricing
Understanding these technical and commercial trade-offs helps identify ideal applications benefitting most from titanium powder metallurgy.
Research and Development Outlook
Emerging efforts to improve titanium powder include:
Alloy Design
- Customized compositions for dermatological implants
- High entropy alloys with exotic elemental blends
Modeling
- Predicting microstructural evolution during heat treatments
- Characterizing powder reuse limits
AM Process
- Binder jet printing followed by microwave sintering
- Hybrid manufacturing combining cold spray densification
Powder Production
- Electrostatic spheroidization without hydriding
- Low cost titanium powder blends through reuse
Applications
- Qualifying aerospace turbine prototypes
- Electronics thermal management devices
- Continuously variable transmission gearbox
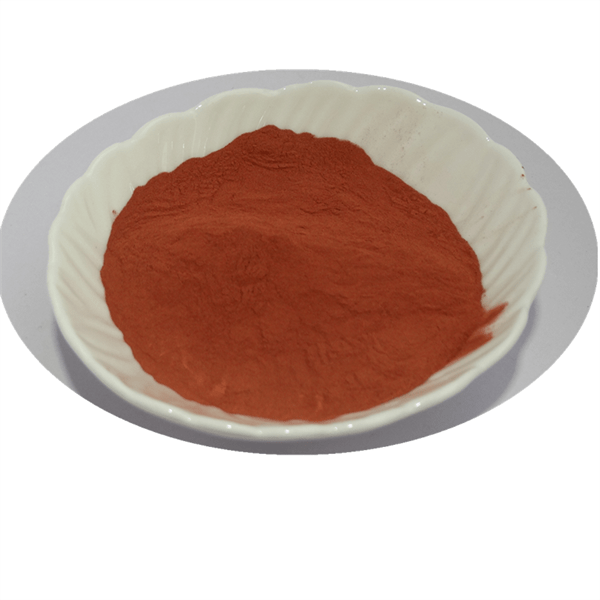
Summary
Titanium is the highest strength-to-weight ratio metallic element but has always been notoriously difficult to extract and fabricate using traditional casting and machining techniques. Recent powder metallurgy advances transform titanium’s potential to deliver lightweight, high strength printed parts combining corrosion resistance and biocompatibility. Tailoring chemistry compliance across medical, aerospace and automotive applications now unlocks innovative geometries previously impossible, technically or economically. However handling the pyrophoric reactivity risks of fine titanium powder remains an expertise barrier needing extreme vigilance when exploring adoption. Working closely with specialist materials partners allows harnessing titanium’s full potential while mitigating operational risks.
Share On
MET3DP Technology Co., LTD is a leading provider of additive manufacturing solutions headquartered in Qingdao, China. Our company specializes in 3D printing equipment and high-performance metal powders for industrial applications.
Inquiry to get best price and customized Solution for your business!
Related Articles
About Met3DP
Recent Update
Our Product
CONTACT US
Any questions? Send us message now! We’ll serve your request with a whole team after receiving your message.
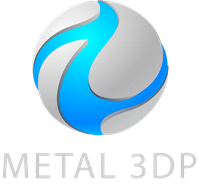
Metal Powders for 3D Printing and Additive Manufacturing
COMPANY
PRODUCT
cONTACT INFO
- Qingdao City, Shandong, China
- [email protected]
- [email protected]
- +86 19116340731