304l Stainless Steel Powder
304L stainless steel powder is an austenitic chromium-nickel stainless steel powder with low carbon content. It offers excellent corrosion resistance, good formability and weldability, and widely used for powder metallurgy applications. The ‘L’ denotes lower carbon compared to 304 standard grade. The low carbon minimizes carbide precipitation and maximizes corrosion resistance. Powder metallurgy 304L provides a cost-effective alternative to 316L for non-critical applications not needing molybdenum alloying.
Low MOQ
Provide low minimum order quantity to meet different needs.
OEM & ODM
Provide customized products and design services to meet unique customer needs.
Adequate Stock
Ensure fast order processing and provide reliable and efficient service.
Customer Satisfaction
Provide high quality products with customer satisfaction at the core.
share this product
Table of Contents
Overview
304L stainless steel powder is an austenitic chromium-nickel stainless steel powder with low carbon content. It offers excellent corrosion resistance, good formability and weldability, and widely used for powder metallurgy applications.
The ‘L’ denotes lower carbon compared to 304 standard grade. The low carbon minimizes carbide precipitation and maximizes corrosion resistance. Powder metallurgy 304L provides a cost-effective alternative to 316L for non-critical applications not needing molybdenum alloying.
This article provides an in-depth look at 304L stainless steel powder covering composition, properties, processing, applications, specifications, suppliers, costs, and other technical details.
Composition
The nominal composition of 304L stainless steel powder is listed below:
Table: Typical composition of 304L stainless steel powder
Element | Weight % |
---|---|
Chromium (Cr) | 18-20 |
Nickel (Ni) | 8-10.5 |
Manganese (Mn) | <2 |
Silicon (Si) | <1 |
Carbon (C) | <0.03 |
Sulfur (S) | <0.03 |
Phosphorus (P) | <0.045 |
Nitrogen (N) | <0.1 |
Iron (Fe) | Balance |
Chromium and nickel are the main alloying elements. Chromium provides corrosion and oxidation resistance. Nickel enhances ductility, toughness, and weldability.
Manganese and silicon increase strength. Carbon is kept very low for optimum corrosion resistance. Sulfur, phosphorus, and nitrogen are impurities that are minimized.
Properties
Key properties of 304L stainless steel powder in the annealed condition are provided below:
Table: Properties of 304L stainless steel powder
Property | Value |
---|---|
Density | 7.9-8.1 g/cm3 |
Ultimate Tensile Strength | 505-620 MPa |
Yield Strength | 205-275 MPa |
Elongation | ≥40% |
Hardness | ≤92 HRB |
Modulus of Elasticity | 190-210 GPa |
Melting Point | 1400-1450°C |
Thermal Conductivity | 16 W/m-K |
Electrical Resistivity | 0.072 μΩ-cm |
The combination of properties make 304L highly useful for a wide range of applications. The austenitic microstructure provides ductility, toughness, and non-magnetic behavior. 304L has excellent corrosion resistance comparable to 316L stainless steel.
By selecting ultra-low carbon powder, carbide precipitation can be avoided to maximize corrosion resistance in critical applications. Strength and hardness can be increased through cold working.
Applications
Typical applications for 304L stainless steel powder include:
- Food processing equipment
- Pharmaceutical tooling
- Chemical plant components
- Architectural panels, railings
- Medical instruments and implants
- Marine hardware, fittings, fasteners
- Consumer products, appliances
- Powder metallurgy mechanical parts
- 3D printing powders
304L provides cost-effective corrosion resistance versus 316L when molybdenum alloying is not needed for highly corrosive environments. The excellent polishability and non-magnetic properties also suits 304L for architectural cladding and hardware components.
Powder metallurgy is commonly used to produce small precision parts from 304L at high volumes versus machining. Additive manufacturing utilizes 304L powder for prototypes, tooling, and end-use components across industries.
Powder Manufacturing
304L stainless steel powder is commercially manufactured via gas atomization or water atomization processes.
In gas atomization, a high pressure inert gas stream disintegrates the molten metal into fine droplets, producing spherical powders ideal for additive manufacturing and MIM. Particle size distribution is controlled through process parameters.
Water atomization uses high pressure water jets to break up the metal stream into fine particles. This generates irregular, satellite particle shapes. The powder requires post-treatment for additive manufacturing.
Plasma atomization is sometimes used to produce very spherical, clean powders from a metal plasma stream in a controlled inert atmosphere. This ensures high purity and flowability.
Powder Specifications
304L stainless steel powder is commercially available in various size ranges, morphologies, and quality levels. Some typical powder specifications are below:
Table: 304L stainless steel powder specifications
Attribute | Details |
---|---|
Particles sizes | 15-45 μm, 10-100 μm |
Morphology | Spherical, irregular |
Apparent density | 2.5-4.5 g/cm3 |
Tap density | 4-5 g/cm3 |
Hall flow rate | <30 s/50g |
Purity | >99.5% |
Oxygen content | <2000 ppm |
Moisture content | <0.2% |
Smaller particle sizes below 45 μm are preferred for capturing fine features in additive manufacturing. Spherical particles provide good flowability. Apparent density correlates with powder packing efficiency.
High purity, low oxygen, and controlled moisture levels ensure quality sintered properties. Gas atomized powder offers the best specifications for critical applications.
Standards and Grades
304L stainless steel powder complies with the following standards:
- ASTM A240 – Standard for chromium and chromium-nickel stainless steel plate, sheet, and strip
- ASTM A313 – Standard for stainless steel spring wire
- ASTM A314 – Standard for stainless steel bent wire
- AMS 5501 – Stainless steel bars, wire, forgings, tubing with low carbon
- AMS 5647 – Stainless steel powder, atomized, 304L
Equivalent grades include:
- UNS S30403
- Werkstoff No. 1.4306
- SUS 304L
- SS2348
Powder can be sourced per ASTM specifications or custom composition for specific applications. Ultra-low carbon and single pressed powders provide optimum properties.
Cost Analysis
304L stainless steel powder costs between $15-30 per kg for gas atomized material. Water atomized powder is cheaper at $8-15/kg but has less sphericity.
Prices vary based on order volume, particle size range, powder morphology, purity levels, and manufacturer/distributor margins.
For finished parts, 304L accounts for 30-60% of MIM component cost, depending on part size and complexity. Small parts in high volumes have a lower share of material cost.
Powder Storage and Handling
To prevent contamination and maintain powder properties, 304L stainless steel powder should be stored and handled as follows:
- Store in sealed containers in a cool, dry environment
- Use inert gas purging or vacuum to prevent moisture pickup
- Keep away from sparks, flames, and ignition sources
- Ground all powder handling and transfer equipment
- Avoid contact with contaminants like oil, grease, paints, etc.
- Use PPE – mask, gloves, eye protection when handling powder
Powder spills should be promptly cleaned using non-sparking tools and HEPA vacuuming. Powders are moderately sensitive to moisture and air exposure. Proper storage is key.
Metal Injection Molding
304L is widely used for metal injection molding of small, complex parts leveraging powder metallurgy. Key considerations include:
- Feedstock: 60-68% powder loading with multi-component binder system
- Molding: High shot size, fast injection speed, high holding pressure
- Debinding: Solvent debinding followed by thermal debinding
- Sintering: 1350-1400°C in hydrogen or vacuum atmosphere
- Secondary Operations: Machining, laser marking, passivation, electropolishing
MIM service bureaus have established best practices for high-performance 304L parts with as-sintered properties approaching wrought material.
Design for AM
For additive manufacturing using 304L stainless steel powder, key design guidelines include:
- Maintain wall thicknesses above 1 mm
- Use self-supporting geometries with angles above 45°
- Include drain holes to remove unfused powder
- Observe build orientation effects on properties
- Account for 20-25% shrinkage when designing mating parts
- Include machining allowances of 0.5-1 mm for critical fits
- Reduce overhangs, bridges, fine details that require supports
Quality Control
Quality control testing performed on 304L stainless steel powder includes:
- Chemical analysis – ICP and OES to verify composition
- Particle size analysis – Laser diffraction particle size analyzer
- Powder morphology – SEM imaging at high magnifications
- Apparent density and tap density – Hall flowmeter method
- Powder flow rate – Hall flowmeter funnel method
- Loss on ignition – ASTM E sin gravity furnace
- Moisture analysis – Karl Fischer titration, LECO analysis
For sintered MIM parts, testing includes:
- Dimensional tolerances – CMM inspection
- Density – Archimedes method
- Microstructure – Optical microscopy, image analysis
- Mechanical testing – Hardness, tensile, fatigue, Charpy impact
Health and Safety
Like most stainless steel powders and parts, 304L poses little health risk with proper handling:
- Wear PPE when handling powder – mask, gloves, goggles
- Avoid skin contact to prevent sensitization
- Use HEPA-filtered vacuum for clean-up of dust and powder
- Avoid breathing any welding or melting fumes
- Dispose according to local environmental regulations
- Ensure adequate ventilation and respiratory protection if grinding or machining sintered parts
No special disposal precautions are needed for 304L. With sound procedures, it poses minimal hazard for workers and the environment.
FAQ
-
What is the difference between 304 and 304L stainless steel powder?
304L has lower carbon content (<0.03%) than 304 (<0.08%) for better corrosion resistance, especially for welding. 304 is more common.
-
Does 304L powder require a controlled atmosphere?
Not necessarily, but storage in sealed containers with inert gas prevents oxidation and contamination.
-
What particle size is best for AM?
15-45 microns is typical for powder bed fusion AM to provide good flow and high resolution. Larger sizes from 45-100 microns are also used.
-
Is 304L used for metal 3D printing?
Yes, 304L is widely used for powder bed and directed energy deposition 3D printing to make prototypes, tooling, and end-use parts.
-
What causes powder to oxidize and lose reusability?
Exposure to air/moisture causes surface oxidation. Proper sealed storage with desiccant and oxygen absorbers prevents this.
-
Does 304L require solution annealing after laser sintering?
Yes, stress relieving at 1050-1150°C and rapid cooling helps restore ductility and toughness after the rapid solidification.
-
What finish can be expected on as-sintered MIM 304L parts?
Around Ra 3-6 microns initially. Polishing and etching can achieve under 0.5 micron. Plating also gives a smooth finish.
-
What tolerance can be achieved with 304L MIM parts?
±0.1-0.3% is typical but tolerances under ±0.1% are possible for high precision components.
-
Why is 304L preferred over 304 stainless steel?
The lower carbon gives 304L better corrosion resistance, especially for weldments, reducing sensitization. It has become the dominant grade.
-
What is the cost premium for 304L vs. 304 powder?
Typically 10-30% higher cost for 304L due to the lower carbon composition. Price also depends on quantities ordered.
Get Latest Price
About Met3DP
Product Category
HOT SALE
CONTACT US
Any questions? Send us message now! We’ll serve your request with a whole team after receiving your message.
Related products
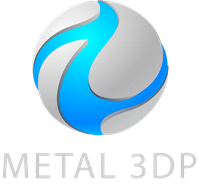
Metal Powders for 3D Printing and Additive Manufacturing